Technology and Applications of laser engraver and cutting machine
Laser engravers and cutting machines utilize focused laser beams to engrave, cut, or mark materials. These machines offer precision, speed, and versatility, making them essential in various industries.
Technology:
1. Laser Source: Common types include CO2, fiber, and diode lasers. CO2 lasers are versatile for non-metal materials, fiber lasers excel in metal marking and cutting, and diode lasers are used for engraving.
2. Control Systems: Advanced software controls the laser’s movement and intensity, ensuring precise and intricate designs.
3. Cooling Systems: Prevent overheating and maintain optimal performance.
4. Motion Control: High-precision motors and sensors ensure accurate positioning and movement of the laser head.
Applications:
1. Manufacturing: Used for cutting and engraving metals, plastics, and composites, enhancing product design and functionality.
2. Signage: Ideal for creating detailed signs, logos, and decorative items from wood, acrylic, and metal.
3. Jewelry: Engraves intricate designs and personalizes jewelry items.
4. Textiles: Cuts and engraves fabrics with precision, used in fashion and upholstery industries.
5. Prototyping: Rapidly creates prototypes from various materials, aiding in product development.
6. Electronics: Marks circuit boards and electronic components with high precision.
7. Medical Devices: Engraves markings on surgical instruments and medical devices for identification and compliance.
Advantages:
– Precision: Capable of intricate designs with minimal material wastage.
– Speed: Faster than traditional methods, increasing productivity.
– Versatility: Works on a wide range of materials, including metals, wood, plastics, glass, and textiles.
– Automation: Integrates with CAD/CAM software for automated production processes.
In summary, laser engravers and cutting machines are pivotal in modern manufacturing and design, offering unparalleled precision, versatility, and efficiency across numerous applications.
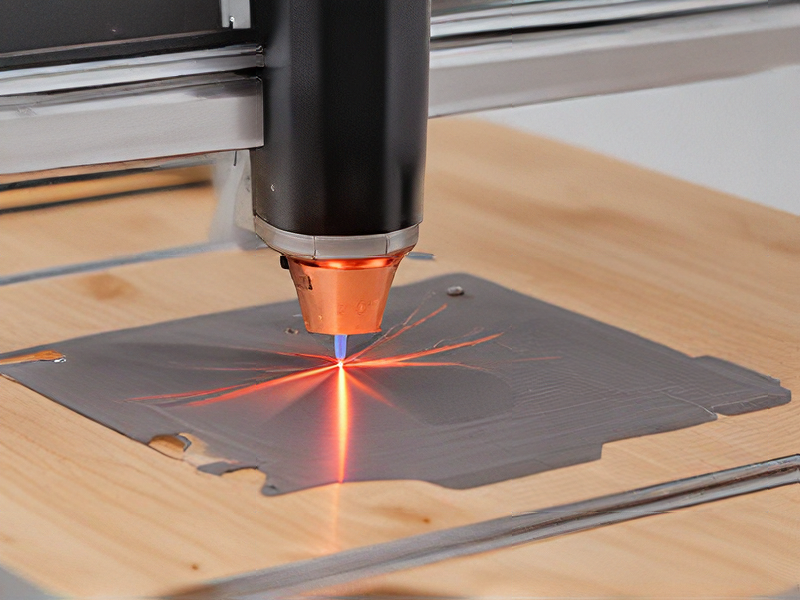
Quality Testing Methods for laser engraver and cutting machine and how to control quality
Quality Testing Methods for Laser Engraver and Cutting Machines
1. Calibration Testing: Regular calibration ensures the machine operates at the correct settings. Use calibration materials to check for precise cutting and engraving depths.
2. Material Compatibility Tests: Test a variety of materials to ensure the machine can handle different substrates effectively. This includes wood, acrylic, metal, and leather, ensuring the machine’s versatility.
3. Resolution and Precision Tests: Use high-detail test patterns to evaluate the machine’s resolution and precision. Fine patterns should be tested to check for clarity and accuracy.
4. Consistency Tests: Run repetitive cuts and engravings on the same material to check for consistency in performance. This helps in identifying any drifts or inconsistencies in the machine’s output.
5. Speed and Power Settings Tests: Test various speed and power settings to ensure the machine can handle different levels of detail and material thickness without compromising quality.
6. Edge Quality Tests: Inspect the edges of cut materials for smoothness and cleanliness. Any burn marks or rough edges indicate issues with settings or laser alignment.
Quality Control Methods
1. Routine Maintenance: Regular cleaning and maintenance of the machine’s components, such as lenses and mirrors, prevent degradation in performance.
2. Software Updates: Keep the machine’s software up to date to ensure it operates with the latest enhancements and bug fixes.
3. Training and Skill Development: Ensure operators are well-trained in using the machine and understanding its settings to maximize its potential and avoid errors.
4. Standardized Operating Procedures: Develop and follow standardized procedures for operating the machine, including specific settings for different materials and tasks.
5. Feedback and Adjustment Loop: Implement a system for collecting feedback from each job to identify areas for improvement and make necessary adjustments.
By incorporating these testing and quality control methods, the performance and output quality of laser engravers and cutting machines can be consistently maintained at high standards.
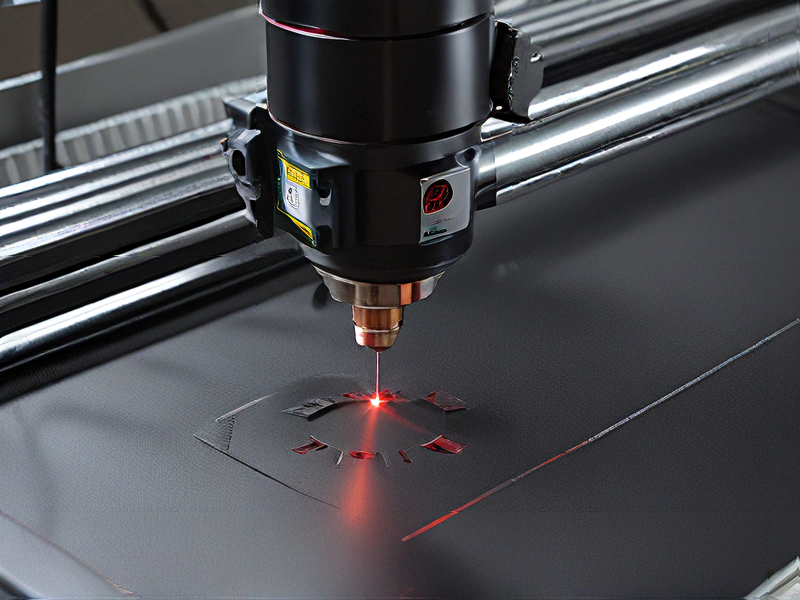
Tips for Procurement and Considerations when Purchasing from laser engraver and cutting machine
Purchasing a laser engraver and cutting machine involves careful consideration. Here are some tips:
1. Define Your Needs:
Determine the materials you’ll engrave/cut (wood, acrylic, leather, etc.), desired precision, engraving/cutting area, and project volume.
2. Budget:
Set a realistic budget, as prices vary significantly based on features and capabilities.
3. Types:
Research different laser types (CO2, fiber, diode) and their suitability for your materials. CO2 lasers are versatile but less precise, while fiber lasers offer higher precision but may be more expensive.
4. Power and Speed:
Higher power lasers cut thicker materials faster but generate more heat. Consider your material thickness and desired engraving/cutting speed.
5. Software and Compatibility:
Ensure the machine’s software is user-friendly and compatible with your design files (e.g., SVG, DXF).
6. Safety Features:
Prioritize safety features like emergency stop buttons, interlocks, and ventilation systems to protect yourself and your workspace.
7. Brand Reputation and Support:
Choose a reputable brand with good customer support and readily available spare parts.
8. Read Reviews:
Consult online reviews and comparisons to gain insights from other users.
Don’t rush the process. Thorough research and careful consideration will lead to a laser engraver/cutter that meets your specific needs and budget.
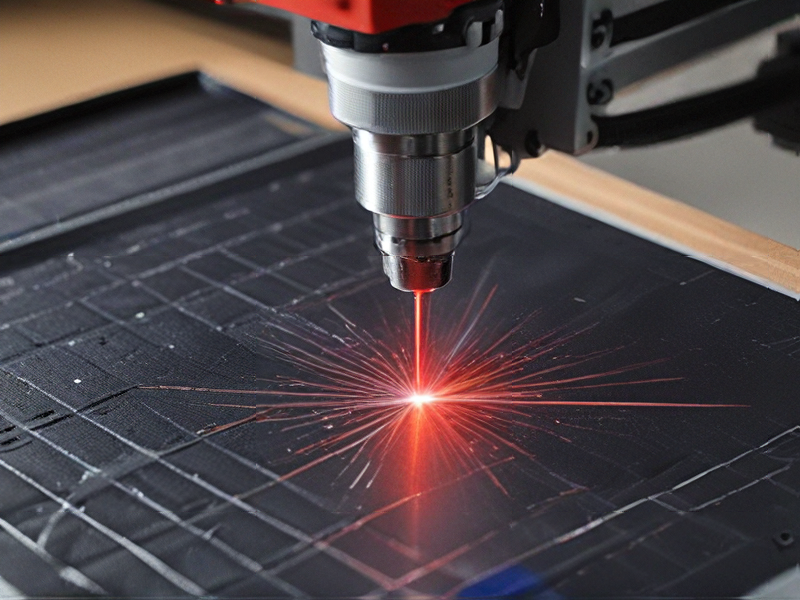
FAQs on Sourcing and Manufacturing from laser engraver and cutting machine in China
FAQs on Sourcing and Manufacturing Laser Engravers and Cutting Machines in China
1. Why source laser engravers and cutting machines from China?
– China is a global manufacturing hub offering a wide range of laser engravers and cutting machines at competitive prices. The country boasts advanced technology, a skilled workforce, and a robust supply chain, making it an attractive option for businesses.
2. How do I find reliable manufacturers?
– Utilize online platforms like Alibaba, Made-in-China, and Global Sources. Attend trade shows such as the Canton Fair. Verify manufacturers through customer reviews, factory visits, and third-party inspection services.
3. What should I consider when choosing a manufacturer?
– Evaluate the manufacturer’s experience, production capacity, quality control processes, and certifications (like ISO, CE). Assess their ability to provide customization and after-sales support.
4. What are the common types of laser engravers and cutting machines?
– CO2 lasers (for non-metal materials), fiber lasers (for metals), and diode lasers (for small-scale and detailed work) are popular types, each serving different material and application needs.
5. What is the typical lead time for production?
– Lead times can vary from 30 to 60 days, depending on the complexity of the order and the manufacturer’s schedule. Custom orders may take longer.
6. How can I ensure product quality?
– Request samples before placing a bulk order. Employ third-party quality inspections and factory audits. Ensure clear communication of specifications and quality standards.
7. What are the payment terms?
– Common terms include a 30% deposit upfront and the balance before shipment. Letter of Credit (L/C) and Trade Assurance on Alibaba offer additional security.
8. How do I handle shipping and logistics?
– Choose between air freight (faster but more expensive) and sea freight (cost-effective but slower). Partner with reputable freight forwarders and understand customs regulations in your country.
9. What after-sales support should I expect?
– Ensure the manufacturer offers technical support, spare parts, and a warranty. Training for operating the machines can also be beneficial.
10. Are there any risks involved?
– Risks include quality inconsistencies, delays, and communication barriers. Mitigate these by thorough research, clear contracts, and regular updates from the manufacturer.
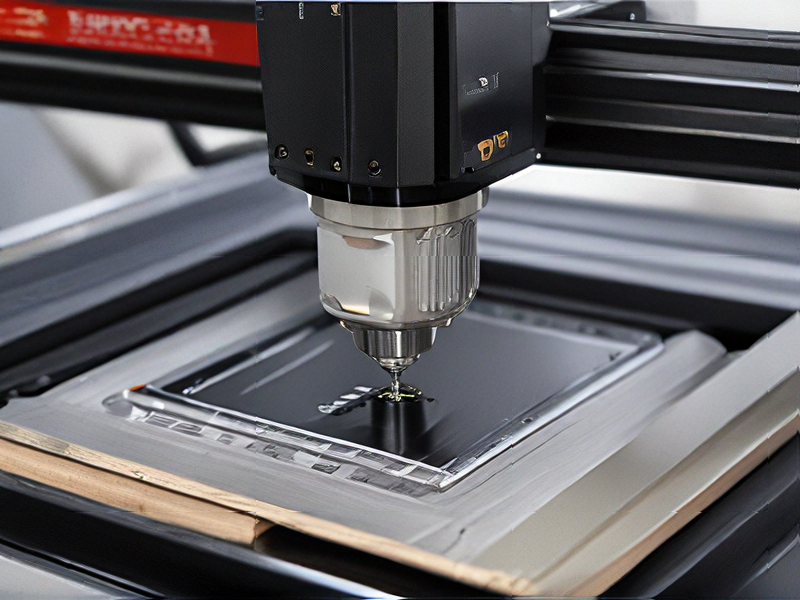