Technology and Applications of aluminum alloy metal
Aluminum alloy metal, composed primarily of aluminum combined with other elements like copper, magnesium, silicon, and zinc, offers a versatile range of properties that make it indispensable in various applications.
Technology
1. Alloying: The process of mixing aluminum with other metals to enhance its properties. For example, adding copper increases strength and hardness, while magnesium improves corrosion resistance and weldability.
2. Heat Treatment: Techniques like solution heat treatment and aging are used to alter the physical and mechanical properties of aluminum alloys, enhancing their strength and durability.
3. Manufacturing Processes: Advanced methods such as casting, extrusion, and rolling are employed to shape aluminum alloys into desired forms. Additive manufacturing (3D printing) with aluminum alloys is also emerging, allowing for complex geometries and reduced waste.
Applications
1. Aerospace: Aluminum alloys are critical in the aerospace industry due to their high strength-to-weight ratio, which improves fuel efficiency. They are used in aircraft frames, wings, and engine components.
2. Automotive: The automotive industry utilizes aluminum alloys to reduce vehicle weight, enhancing fuel efficiency and performance. Common applications include engine blocks, wheels, and body panels.
3. Construction: In construction, aluminum alloys are used for their durability, corrosion resistance, and aesthetic appeal. They are found in window frames, roofing, and structural components.
4. Marine: Aluminum alloys resist corrosion in marine environments, making them ideal for boat hulls and other components exposed to seawater.
5. Consumer Electronics: Lightweight and durable, aluminum alloys are used in the manufacturing of smartphones, laptops, and other electronic devices.
6. Packaging: Aluminum alloys are widely used in packaging, especially for food and beverages, due to their non-toxic nature and recyclability.
Conclusion
The technological advancements in processing and treating aluminum alloys, combined with their versatile properties, drive their widespread application across industries, making them essential to modern manufacturing and design.
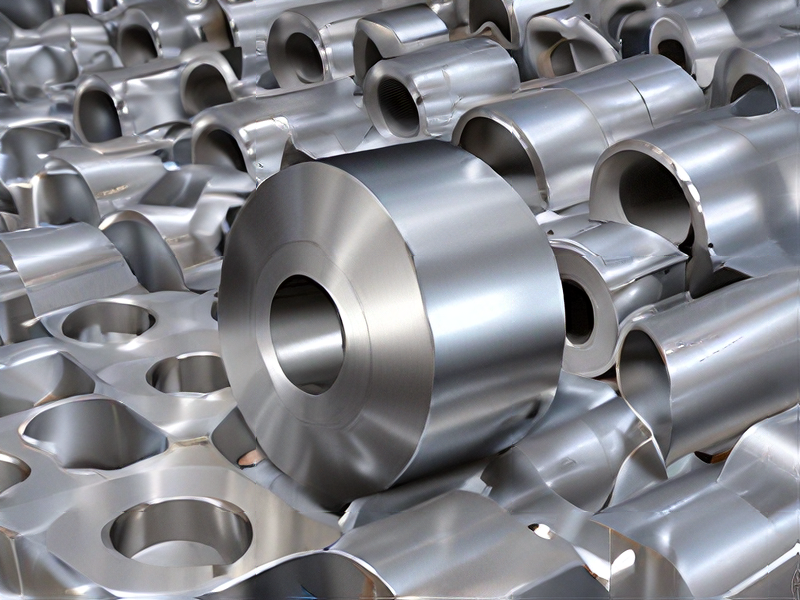
Quality Testing Methods for aluminum alloy metal and how to control quality
Quality Testing Methods for Aluminum Alloy Metal:
1. Visual Inspection:
– Detects surface defects like cracks, scratches, and discoloration.
– Uses tools like magnifying glasses and microscopes.
2. Chemical Analysis:
– Determines alloy composition.
– Methods: Optical Emission Spectroscopy (OES) and X-Ray Fluorescence (XRF).
3. Mechanical Testing:
– Tensile Test: Measures strength and ductility by stretching the alloy.
– Hardness Test: Assesses resistance to indentation (e.g., Brinell, Rockwell).
– Fatigue Test: Evaluates durability under cyclic loading.
4. Non-Destructive Testing (NDT):
– Ultrasonic Testing (UT): Uses sound waves to detect internal flaws.
– Radiographic Testing (RT): X-rays or gamma rays reveal internal defects.
– Eddy Current Testing (ECT): Detects surface and subsurface defects using electromagnetic fields.
5. Metallographic Examination:
– Analyzes microstructure using optical or electron microscopes.
– Prepares samples through sectioning, mounting, polishing, and etching.
Quality Control Measures:
1. Standardized Procedures:
– Implementing ASTM, ISO, or other relevant standards for consistent testing and quality.
2. Process Control:
– Monitoring and controlling manufacturing processes using Statistical Process Control (SPC) to detect variations early.
3. Supplier Quality Management:
– Ensuring raw material quality through supplier audits, certifications, and incoming material inspections.
4. Training and Certification:
– Regular training for personnel on quality standards and testing techniques.
5. Documentation and Traceability:
– Maintaining detailed records of test results and process parameters for traceability and continuous improvement.
6. Continuous Improvement:
– Applying methodologies like Six Sigma and Lean Manufacturing to reduce defects and improve quality continuously.
By combining rigorous testing with stringent quality control measures, manufacturers can ensure the reliability and performance of aluminum alloy products.
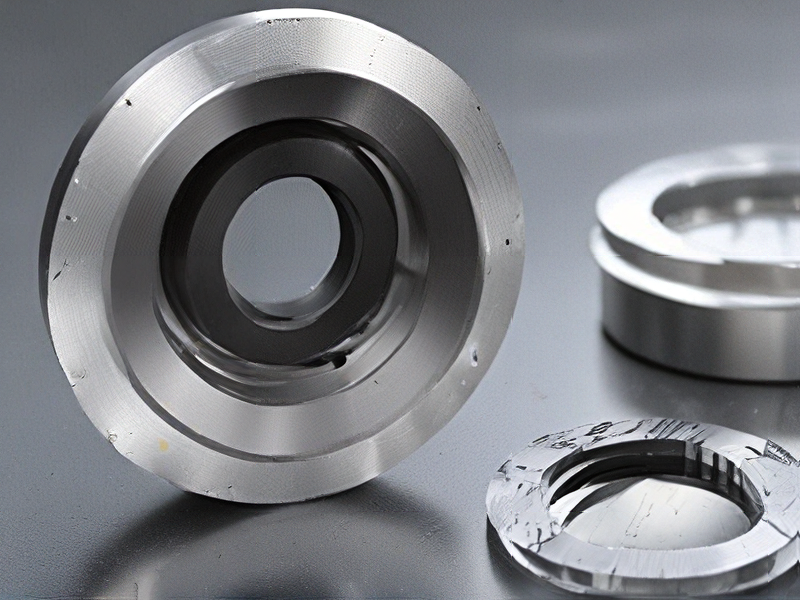
Tips for Procurement and Considerations when Purchasing from aluminum alloy metal
Tips for Procurement and Considerations When Purchasing Aluminum Alloy Metal
1. Understand Alloy Grades: Different grades of aluminum alloys, such as 6061, 7075, and 2024, offer varying levels of strength, corrosion resistance, and machinability. Choose the grade that best fits your project’s requirements.
2. Supplier Reliability: Vet suppliers carefully. Look for those with a strong track record, quality certifications (like ISO 9001), and positive customer reviews. Reliable suppliers ensure consistent material quality and delivery times.
3. Material Specifications: Define precise material specifications, including temper (e.g., T6, T5) and dimensions. Clear specifications help prevent misunderstandings and ensure you get the exact material needed.
4. Cost Considerations: While cost is important, don’t compromise on quality. Cheaper options might have hidden flaws or inconsistencies. Compare prices from multiple suppliers to find a fair balance between cost and quality.
5. Lead Times: Consider the lead times for delivery, especially if working on a tight schedule. Ensure the supplier can meet your project timeline without compromising quality.
6. Certification and Compliance: Ensure the material complies with relevant standards and regulations, such as ASTM or ISO standards. Request material certificates to verify compliance.
7. Sustainability: Opt for suppliers that practice sustainable sourcing and recycling. Aluminum is highly recyclable, and choosing recycled content can reduce environmental impact.
8. Technical Support: Select suppliers who offer technical support and consultation. This is especially useful for complex projects where specific alloy properties are critical.
9. Inspection and Testing: Implement a robust inspection and testing process. Non-destructive testing (NDT) methods like ultrasonic or X-ray inspections can detect internal flaws without damaging the material.
10. Future Supply Chain Security: Develop a relationship with your supplier to ensure a reliable supply chain. Long-term partnerships can offer benefits like priority in supply and better pricing.
By following these tips, you can ensure a successful procurement process, leading to high-quality aluminum alloy components for your projects.
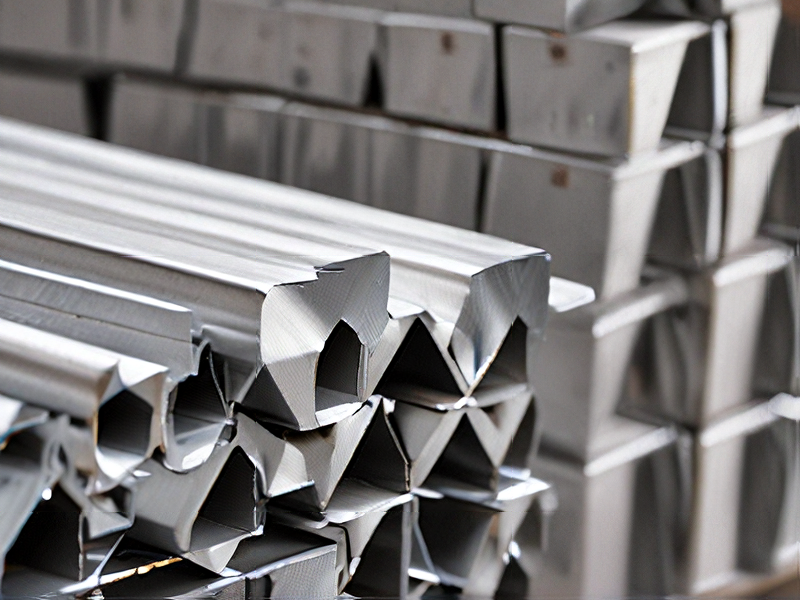
FAQs on Sourcing and Manufacturing from aluminum alloy metal in China
FAQs on Sourcing and Manufacturing from Aluminum Alloy Metal in China
1. Why source aluminum alloy metal from China?
China is a global leader in aluminum production, offering competitive prices and a wide variety of aluminum alloys. The country has a well-established supply chain and extensive manufacturing capabilities, ensuring high-quality products.
2. What are the key aluminum alloys available in China?
Common aluminum alloys include 6061, 6063, 7075, and 2024. Each alloy has specific properties suitable for various applications, from structural components to aerospace parts.
3. How can I find reliable suppliers in China?
Use platforms like Alibaba, Made-in-China, and Global Sources to identify suppliers. Verify their credentials through trade references, site visits, and by requesting sample products.
4. What should I consider when selecting a manufacturer?
Look for manufacturers with ISO certifications, a robust quality control system, and experience in your specific industry. Check their production capacity, lead times, and ability to meet custom specifications.
5. What are the common manufacturing processes for aluminum alloys in China?
Processes include extrusion, casting, forging, and CNC machining. Each process has different cost implications and is suitable for different types of products.
6. How can I ensure the quality of aluminum alloy products?
Conduct third-party inspections, request material test reports, and implement quality assurance protocols. Working with manufacturers who follow international standards can also help ensure quality.
7. What are the typical lead times for manufacturing?
Lead times vary depending on the complexity and quantity of the order. Generally, expect 4-8 weeks for production, plus additional time for shipping and customs clearance.
8. What are the cost factors involved?
Costs include raw material prices, manufacturing process, tooling, labor, quality control, and logistics. It’s essential to get detailed quotes and understand all cost components.
9. How do I handle logistics and shipping?
Choose experienced freight forwarders familiar with shipping aluminum products. Understand the import regulations of your country, including duties and tariffs.
10. What are the risks and how can they be mitigated?
Risks include quality issues, delays, and communication barriers. Mitigate these by working with reputable suppliers, maintaining clear communication, and having contingency plans.
By addressing these FAQs, you can better navigate the process of sourcing and manufacturing aluminum alloy metal in China.
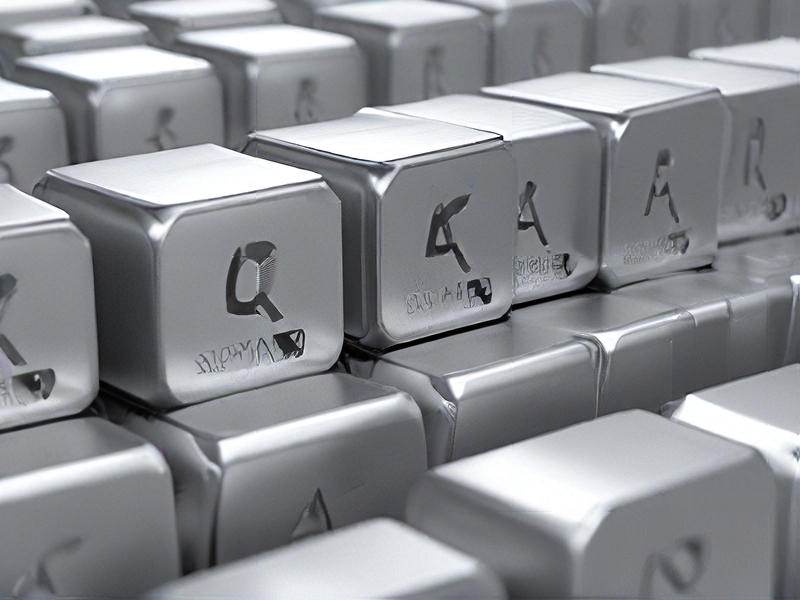