Technology and Applications of machining precision
Precision machining refers to the process of cutting metal parts to very tight tolerances using specialized tools and machinery. It plays a crucial role in various industries such as aerospace, automotive, medical devices, and electronics, where accuracy and quality are paramount.
Technology: Precision machining utilizes advanced CNC (Computer Numerical Control) machines that can interpret CAD (Computer-Aided Design) drawings with high precision. These machines include CNC milling machines, lathes, grinding machines, and electrical discharge machining (EDM) tools. They operate with incredible accuracy, often achieving tolerances within microns (millionths of a meter).
Applications: Precision machining finds applications in:
1. Aerospace: Manufacturing components for aircraft and spacecraft engines, structures, and control systems.
2. Automotive: Producing engine components, transmission parts, and intricate fuel injection systems.
3. Medical: Creating surgical instruments, implants, and devices requiring precise dimensions and surface finishes.
4. Electronics: Fabricating connectors, housings, and components for electronic devices where tight tolerances are crucial for performance and reliability.
5. Tool and Die Making: Crafting molds, dies, and tools used in manufacturing processes.
Precision machining ensures parts meet exact specifications, enhancing performance, reliability, and safety in critical applications. Advanced materials such as titanium alloys and composites can also be machined precisely, expanding the scope of industries benefiting from this technology.
In conclusion, precision machining is indispensable across high-tech industries, driven by continual advancements in CNC technology and materials science. Its ability to deliver complex parts with tight tolerances enables innovation and reliability in modern manufacturing.
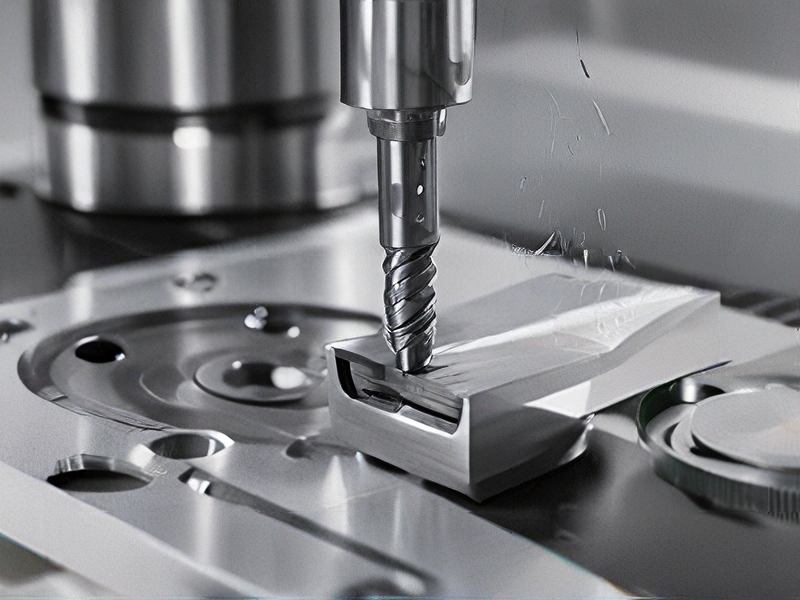
Quality Testing Methods for machining precision and how to control quality
Ensuring precision in machining involves rigorous quality testing methods to maintain standards. Key approaches include:
1. Dimensional Inspection: Utilizing coordinate measuring machines (CMMs) and gauges to verify part dimensions against engineering drawings.
2. Surface Roughness Measurement: Assessing the quality of machined surfaces using profilometers to ensure they meet specified roughness parameters.
3. Visual Inspection: Examining parts for defects such as burrs, scratches, or tool marks that could affect functionality or aesthetics.
4. Statistical Process Control (SPC): Monitoring machining processes using control charts to detect variations and ensure consistency.
5. First Article Inspection (FAI): Performing comprehensive checks on the first produced part to validate machining setup and processes.
6. Material Analysis: Verifying material composition and properties to ensure they meet required specifications.
To control quality effectively:
– Establish Clear Specifications: Define precise tolerances and quality criteria upfront.
– Implement Robust Process Controls: Regularly calibrate equipment, maintain stable machining conditions, and train operators thoroughly.
– Use Automated Inspection Technologies: Employ automated systems for faster and more accurate inspections.
– Continuous Improvement: Implement feedback loops to address issues promptly and improve processes iteratively.
By combining these methods, manufacturers can achieve high machining precision and consistent quality, crucial for meeting customer expectations and regulatory requirements.
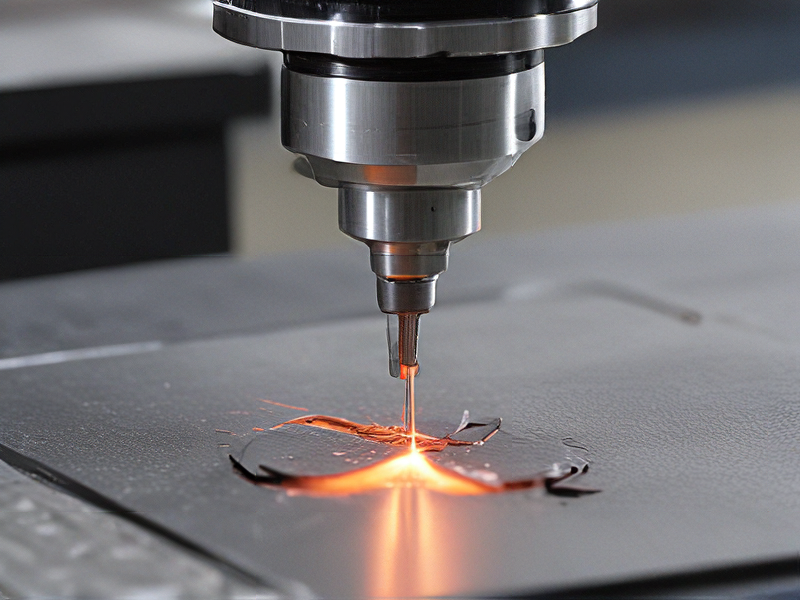
Tips for Procurement and Considerations when Purchasing from machining precision
When procuring precision machining services, several key considerations can ensure successful outcomes:
1. Supplier Capability: Assess the supplier’s expertise, equipment, and past projects in precision machining. Look for certifications like ISO standards that ensure quality and reliability.
2. Technical Specifications: Clearly define your requirements regarding tolerances, surface finish, materials, and any specific standards or certifications needed for your industry.
3. Quality Assurance: Ensure the supplier has robust quality control processes in place, such as inspection protocols and traceability of materials, to guarantee precision and consistency.
4. Cost and Value: Balance cost considerations with the quality of work and supplier reliability. Cheaper options may compromise on quality, leading to rework costs or delays.
5. Communication and Collaboration: Establish clear communication channels and expectations regarding project updates, timelines, and any potential issues that may arise during production.
6. Lead Times and Capacity: Understand the supplier’s production capacity and lead times to align with your project timeline and avoid delays.
7. Feedback and References: Seek references or reviews from other clients to gauge the supplier’s reputation and reliability in delivering precision machining services.
8. Contractual Agreements: Clearly outline deliverables, timelines, payment terms, and dispute resolution mechanisms in a formal contract to protect both parties.
By addressing these considerations, you can effectively navigate the procurement process for precision machining services and ensure the quality and reliability of your purchased components.
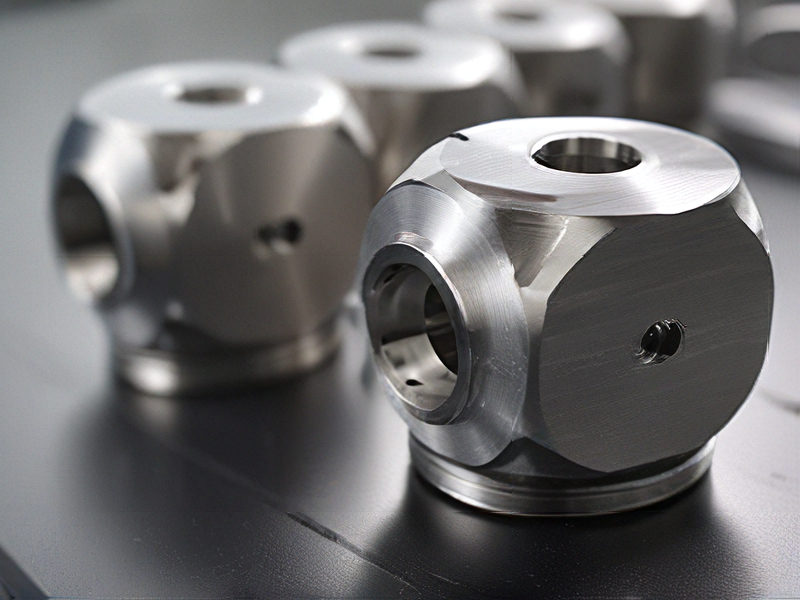
FAQs on Sourcing and Manufacturing from machining precision in China
Certainly! Here are some FAQs on sourcing and manufacturing precision machining in China:
1. Why should I consider sourcing precision machining from China?
China offers competitive pricing due to lower labor costs and established manufacturing infrastructure. It also provides access to a wide range of suppliers with varying capabilities.
2. How do I ensure quality when sourcing from China?
Quality assurance can be managed through rigorous supplier vetting, conducting factory audits, specifying clear quality standards, and implementing inspection protocols.
3. What are the typical lead times for precision machining in China?
Lead times vary depending on complexity and volume but are generally competitive, ranging from a few weeks to a couple of months.
4. What are the main challenges of manufacturing in China?
Challenges include language barriers, intellectual property protection, cultural differences, and logistics management.
5. How can I find reliable suppliers in China?
Utilize sourcing platforms, attend trade shows, seek recommendations, conduct thorough background checks, and request samples and references.
6. What are the advantages of outsourcing precision machining to China?
Advantages include cost savings, access to advanced technology and skilled labor, scalability, and flexibility in production volumes.
7. How can I protect my intellectual property when manufacturing in China?
Use legal contracts, non-disclosure agreements, trademarks, and patents. Work with reputable suppliers and consider compartmentalizing production processes.
8. What are the payment terms typically used with Chinese suppliers?
Common payment terms include T/T (Telegraphic Transfer), L/C (Letter of Credit), and sometimes PayPal for smaller transactions.
9. How can I manage communication effectively with Chinese suppliers?
Use clear and detailed specifications, employ translators or bilingual staff, establish regular communication channels, and build strong relationships.
10. What should I consider when negotiating pricing with Chinese suppliers?
Factors influencing pricing include order volume, material costs, production complexity, and market demand fluctuations.
These FAQs provide a foundational understanding of sourcing and manufacturing precision machining in China, addressing key considerations and strategies for successful collaboration.
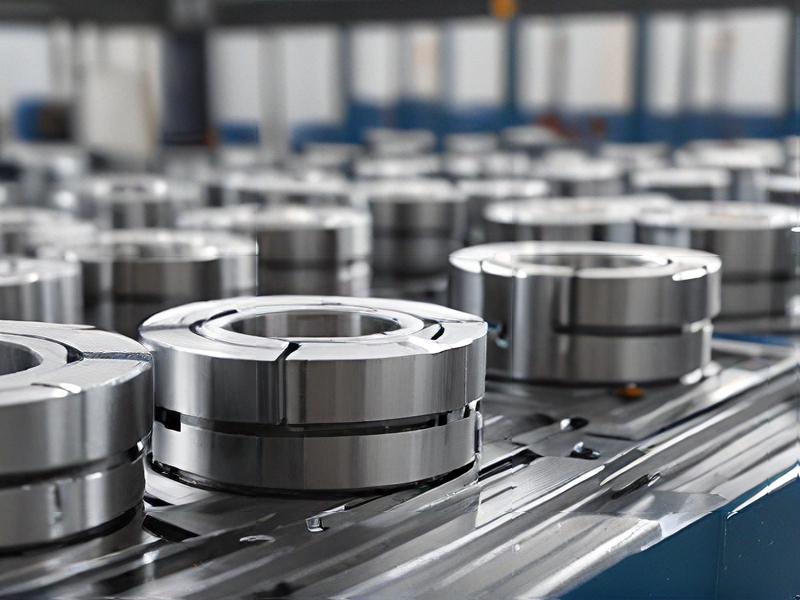