Technology and Applications of shimming metal
Shimming metal involves using thin layers of material, typically metals like aluminum, stainless steel, or brass, to adjust and align components within various applications. This technique is crucial in engineering and manufacturing for achieving precise tolerances and alignments where small gaps or adjustments are necessary.
Applications:
1. Precision Machinery: In machinery, shims are used to fill gaps between components such as gears, bearings, or shafts to ensure proper alignment and reduce vibration.
2. Automotive Industry: Shims are employed in automotive manufacturing to align parts like suspension components, brakes, and engine parts, ensuring optimal performance and durability.
3. Aerospace and Defense: Critical in aerospace applications to align aircraft components, control surfaces, and instrumentation precisely. Shims are also used in defense equipment for alignment and structural integrity.
4. Construction: Used in construction to level and align structures, including steel frames, concrete forms, and precast elements, ensuring stability and load-bearing capacity.
Technology:
1. Material Selection: Shims are typically made from metals due to their strength, durability, and ability to withstand high pressure and temperature variations.
2. Manufacturing Techniques: Shims can be manufactured through stamping, laser cutting, or water jet cutting to achieve precise dimensions and thicknesses required for specific applications.
3. Customization: Shims can be customized in shape, size, and material composition to meet the exact requirements of the application, ensuring compatibility and effectiveness.
4. Advancements: Modern techniques include computer-aided design (CAD) for precise shim dimensions and 3D printing for rapid prototyping of custom shims.
In conclusion, shimming metal plays a vital role across industries where precision, alignment, and durability are paramount. Advances in material science and manufacturing techniques continue to enhance the effectiveness and versatility of shimming technology in various applications.
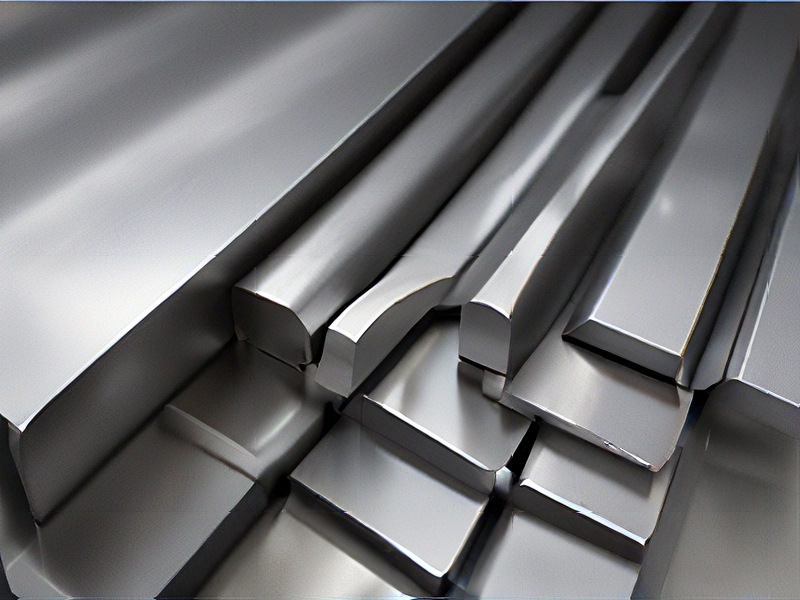
Quality Testing Methods for shimming metal and how to control quality
Quality testing methods for shimming metal are essential to ensure proper fit, performance, and durability in applications like machinery and structural components. Here are key methods and control techniques:
1. Dimensional Inspection: Utilizing tools like calipers, micrometers, and gauges to verify the shim’s thickness, length, and width against specified tolerances. This ensures that the shim fits correctly within its intended assembly.
2. Surface Roughness Measurement: Employing profilometers to assess surface finish, which can impact friction and wear in assembly. A consistent surface finish can enhance the shim’s performance and longevity.
3. Material Analysis: Conducting metallurgical testing, such as hardness and tensile strength tests, to confirm the shim’s material properties. This can involve techniques like Rockwell or Brinell hardness tests and ensures that the material meets engineering specifications.
4. Visual Inspection: Regular visual checks can identify defects such as cracks, warping, or improper machining. This simple yet effective method helps in early detection of quality issues.
5. Non-Destructive Testing (NDT): Methods like ultrasonic testing and dye penetrant inspection can assess material integrity without damaging the shim. These tests are useful for identifying subsurface defects.
6. Controlled Manufacturing Environment: Implementing strict quality control protocols during production, including training personnel and regular equipment calibration, helps maintain consistent quality.
To control quality, companies should establish clear specifications, maintain documentation for traceability, and perform periodic audits. Continuous improvement practices, such as collecting feedback from users, can further refine the manufacturing process and enhance quality assurance. By integrating these quality testing methods and control techniques, organizations can ensure the reliability and effectiveness of shimming metals in their applications.
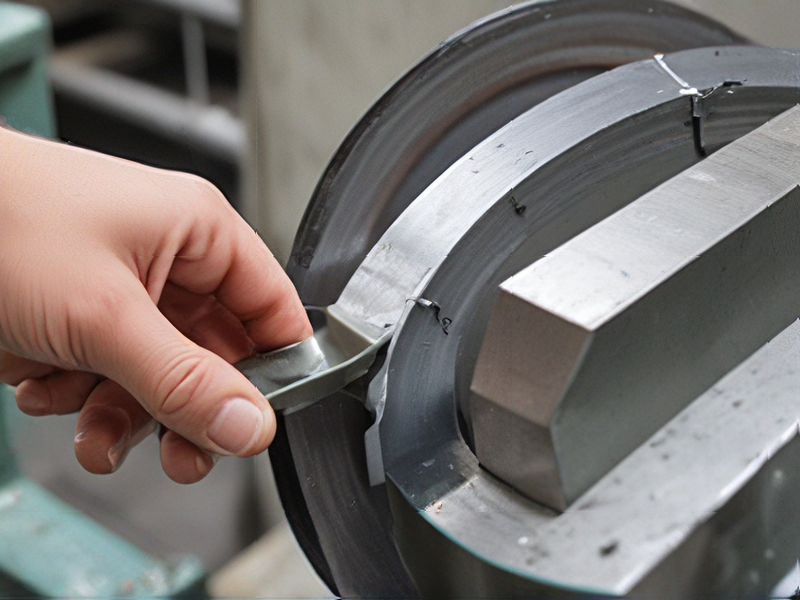
Tips for Procurement and Considerations when Purchasing from shimming metal
When procuring shimming metal, careful consideration is essential to ensure quality and suitability for your application. Here are key tips to guide your purchasing decision:
1. Material Specifications: Understand the specific type of shimming metal required for your project. Common materials include stainless steel, aluminum, brass, and composite metals. Each has unique properties—like corrosion resistance, strength, and thermal conductivity—that impact performance.
2. Thickness and Tolerance: Determine the required thickness and tolerances for the shims. Precise measurements are crucial to achieving the desired fit and function. Consult engineering drawings or specifications to avoid errors.
3. Supplier Verification: Research potential suppliers for reliability, quality certifications (e.g., ISO standards), and customer reviews. Selecting a reputable supplier can ensure consistent material quality and service.
4. Testing and Quality Assurance: Inquire about testing procedures for the shimming metal. Suppliers should provide documentation of material properties, including tensile strength and corrosion resistance.
5. Quantity and Lead Times: Assess your project’s volume requirements and expected lead times. Confirm with suppliers their ability to meet your timelines, especially if the order is large or requires custom specifications.
6. Costs: Compare prices from multiple suppliers, but consider the total cost of ownership, which includes shipping, taxes, and any potential waste due to poor quality.
7. Custom Solutions: If standard shims do not meet your needs, explore suppliers that offer custom machining or fabrication services for tailored solutions.
By keeping these considerations in mind during your procurement process, you can ensure that you select the right shimming metal that meets your project needs effectively and reliably.
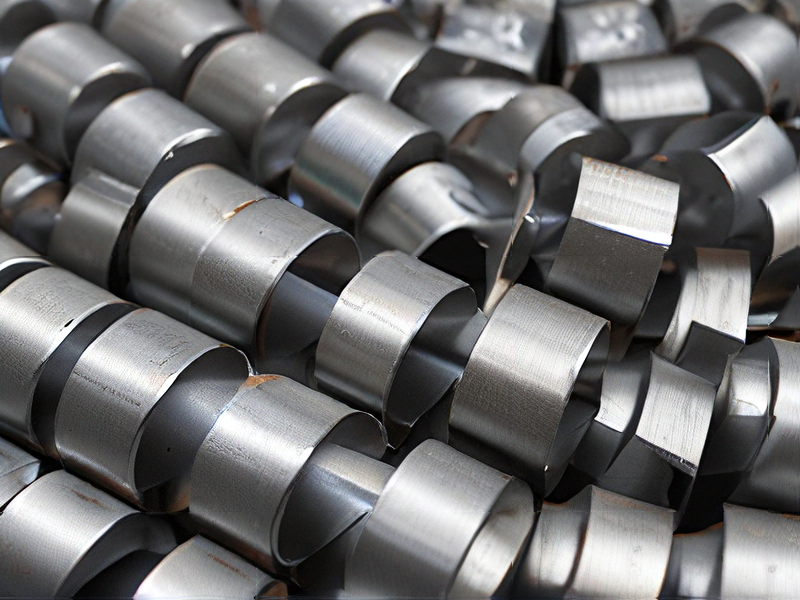
FAQs on Sourcing and Manufacturing from shimming metal in China
Sourcing and manufacturing shimming metal in China involves several key considerations:
1. Finding Suppliers: Utilize online platforms like Alibaba or Made-in-China to find potential suppliers. Ensure they specialize in shimming metals and have a track record of exporting to your region.
2. Quality Control: Implement stringent quality control measures. Conduct factory audits, request samples, and consider hiring a third-party inspection service to ensure product quality meets your standards.
3. Communication: Effective communication is crucial. Clarify specifications, production timelines, and expectations clearly to avoid misunderstandings.
4. Intellectual Property: Safeguard your designs and intellectual property. Use non-disclosure agreements (NDAs) and consider registering trademarks or patents if applicable.
5. Logistics and Shipping: Plan logistics carefully. Evaluate shipping options (air vs. sea freight), customs duties, and import regulations to optimize costs and delivery times.
6. Negotiation and Contracts: Negotiate pricing, payment terms, and production volumes. Draft comprehensive contracts that outline all terms and conditions to mitigate risks.
7. Cultural Understanding: Understand Chinese business culture. Building relationships and demonstrating respect can facilitate smoother transactions.
8. Environmental and Ethical Standards: Ensure suppliers comply with environmental and ethical standards. Conduct due diligence on their manufacturing practices.
By focusing on these aspects, you can navigate the complexities of sourcing and manufacturing shimming metal in China effectively while minimizing risks and maximizing product quality and reliability.
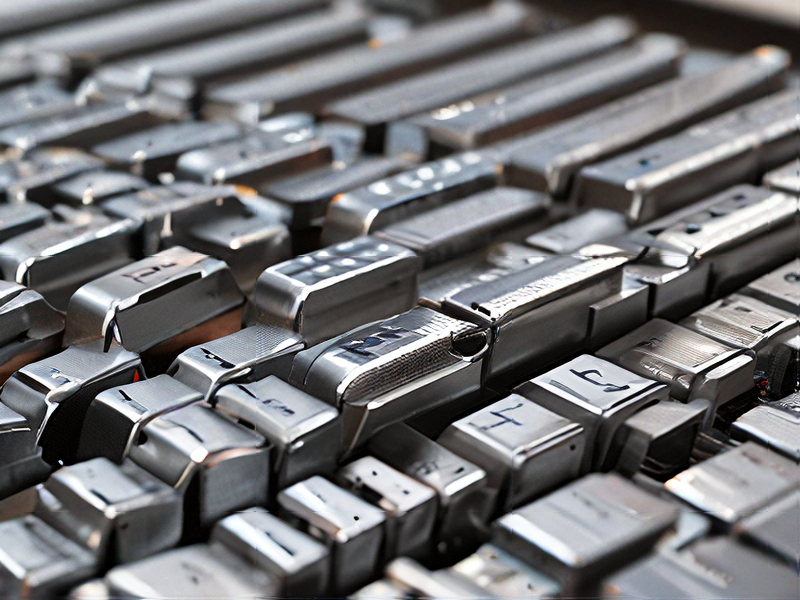