Technology and Applications of laser marking machine metal
Laser marking machines are crucial in metalworking industries for their precision and versatility. They utilize laser beams to mark or engrave surfaces with high accuracy and durability. This technology finds extensive applications in various sectors such as automotive, aerospace, electronics, and medical devices.
The process involves focusing a laser beam onto the metal surface, causing localized heating and oxidation, which changes the surface properties without compromising the material integrity. This results in permanent marks that are resistant to wear, corrosion, and fading.
Key applications include:
1. Product Identification: Laser marking is used for serial numbers, barcodes, and QR codes, facilitating traceability and inventory management in manufacturing.
2. Branding and Aesthetics: Manufacturers use laser marking to add logos, brand names, and decorative designs, enhancing product aesthetics.
3. Quality Control: It allows for precise marking of inspection symbols and quality marks, ensuring compliance with industry standards.
4. Anti-Counterfeiting: Laser markings can include intricate patterns and hidden identifiers that are difficult to replicate, aiding in anti-counterfeiting efforts.
5. Medical Devices: Laser marking ensures medical device traceability, compliance with regulatory standards, and patient safety.
6. Automotive and Aerospace Components: Critical components require durable identification and tracking throughout their lifecycle, which laser marking provides effectively.
Technological advancements have led to the development of fiber lasers, which are highly efficient and reliable for metal marking applications. These lasers offer high beam quality, enabling fine details and complex patterns to be marked accurately on various metals including steel, aluminum, titanium, and alloys.
In conclusion, laser marking machines play a pivotal role in modern metalworking industries by providing permanent, high-contrast marks essential for product identification, branding, and compliance purposes across diverse sectors.
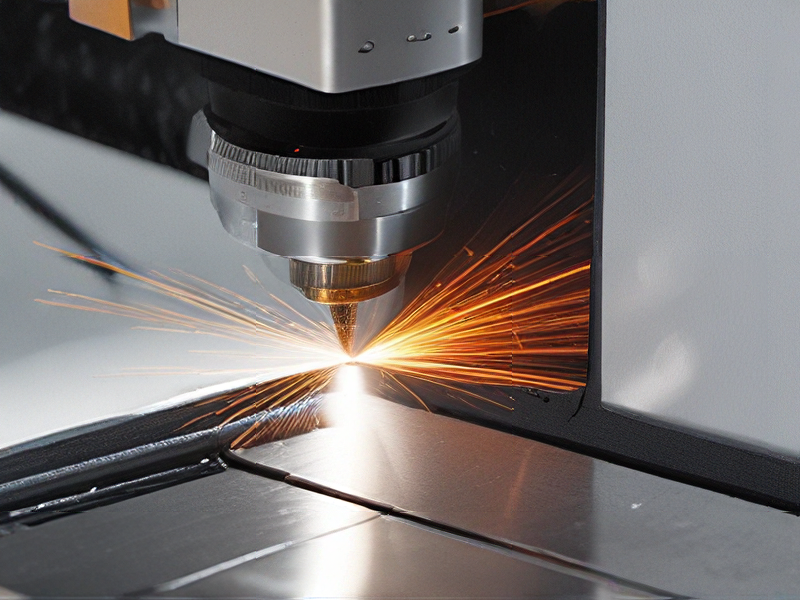
Quality Testing Methods for laser marking machine metal and how to control quality
Quality testing methods for laser marking on metal typically include:
1. Visual Inspection: Ensure the mark is clear, without smudges or inconsistencies.
2. Dimensional Accuracy: Measure the mark’s dimensions against specifications.
3. Contrast Measurement: Use tools to verify sufficient color contrast for readability.
4. Durability Testing: Assess mark resistance to abrasion, corrosion, and other environmental factors.
5. Barcode Scanning: Validate readability of barcodes using appropriate scanners.
To control quality:
– Calibration: Regularly calibrate the laser machine for consistent marking.
– Operator Training: Ensure operators are trained in proper machine use and quality standards.
– Process Documentation: Maintain detailed records of parameters used for each marking job.
– Feedback Loop: Implement a feedback system to address issues promptly.
By combining these methods with effective quality control measures, manufacturers can ensure reliable and high-quality laser marking on metal products.
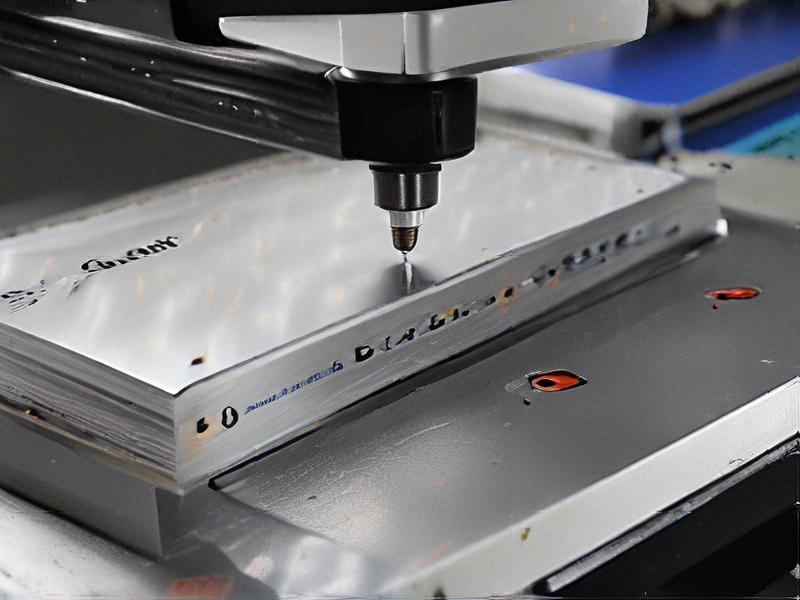
Tips for Procurement and Considerations when Purchasing from laser marking machine metal
When purchasing a laser marking machine for metal, consider the following key tips and factors:
1. Laser Type and Power: Choose a machine with the appropriate laser type (fiber, CO2, or UV) depending on your application needs. Ensure the laser power is sufficient for marking metals effectively.
2. Marking Speed and Precision: Evaluate the machine’s marking speed and precision capabilities. Higher wattage lasers generally offer faster marking speeds and finer resolution.
3. Ease of Use and Software Compatibility: Opt for a machine with user-friendly controls and software that supports your file formats (like DXF, AI). Look for intuitive interfaces and compatibility with your existing workflow.
4. Maintenance Requirements: Consider the maintenance needs of the machine. Look for systems with easy access to critical components for cleaning and servicing.
5. Material Compatibility: Ensure the machine is designed to handle a variety of metals you plan to mark, including stainless steel, aluminum, titanium, etc. Verify the machine’s compatibility with other materials if needed.
6. Safety Features: Laser machines should adhere to safety standards (like FDA regulations) and include features such as enclosures, interlocks, and safety sensors to protect operators.
7. Support and Training: Check the availability of training resources and technical support from the manufacturer or supplier. Proper training ensures efficient operation and maintenance.
8. Budget and ROI: Determine your budget constraints and assess the machine’s return on investment (ROI) based on its capabilities and expected productivity gains.
9. Reviews and Reputation: Research user reviews and the reputation of the manufacturer or supplier. Look for testimonials and case studies demonstrating successful applications in metal marking.
10. Future Scalability: Consider your future needs for scalability and expansion. Choose a machine that can accommodate potential increases in production volume or changes in marking requirements.
By considering these factors, you can make a well-informed decision when purchasing a laser marking machine for metal, ensuring it meets your operational needs and delivers reliable performance over time.
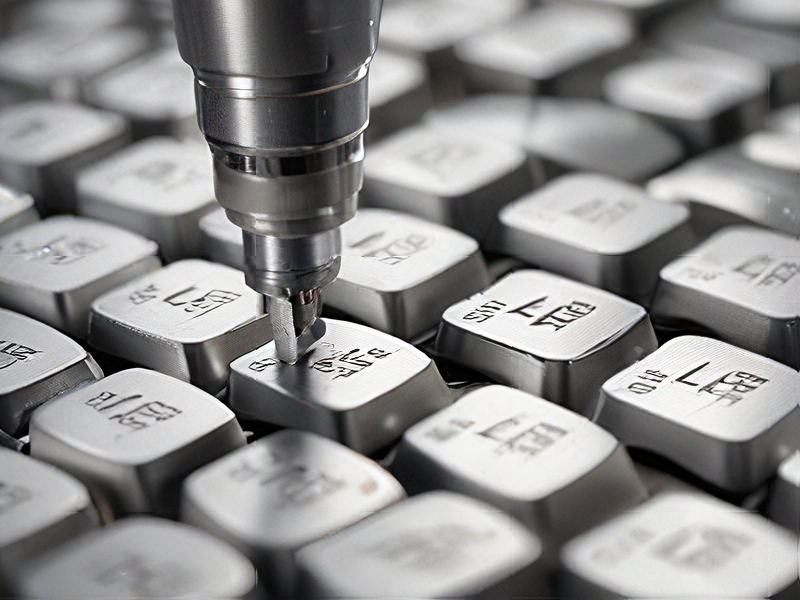
FAQs on Sourcing and Manufacturing from laser marking machine metal in China
When sourcing and manufacturing laser marking machines for metal in China, consider the following FAQs:
1. What are the key considerations when sourcing from China?
– Ensure the supplier has experience in laser marking technology and a proven track record in metalworking equipment.
– Verify their certifications for quality standards like ISO 9001 and CE compliance.
2. How do I ensure quality control?
– Conduct factory audits or request samples to assess product quality firsthand.
– Implement clear quality specifications and conduct regular inspections during production.
3. What are the typical lead times and shipping options?
– Lead times can vary but typically range from 4-8 weeks depending on customization and order volume.
– Shipping options include sea freight, which is economical but slower, or air freight for faster delivery.
4. Are there intellectual property concerns?
– Ensure contracts include clauses protecting your intellectual property (IP) rights.
– Consider registering patents or trademarks in China to bolster legal protection.
5. How do I manage communication and language barriers?
– Use clear and detailed technical specifications and drawings.
– Engage with suppliers who have English-speaking staff or employ translators to facilitate communication.
6. What support can I expect post-purchase?
– Clarify warranty terms and after-sales support, including training and technical assistance.
– Establish communication channels for ongoing support and troubleshooting.
7. What are the payment terms typically used?
– Negotiate payment terms that balance risk and cost-effectiveness, such as a deposit followed by final payment upon inspection or delivery.
Navigating these FAQs will help streamline the sourcing and manufacturing process for laser marking machines from China, ensuring quality, efficiency, and effective communication throughout.
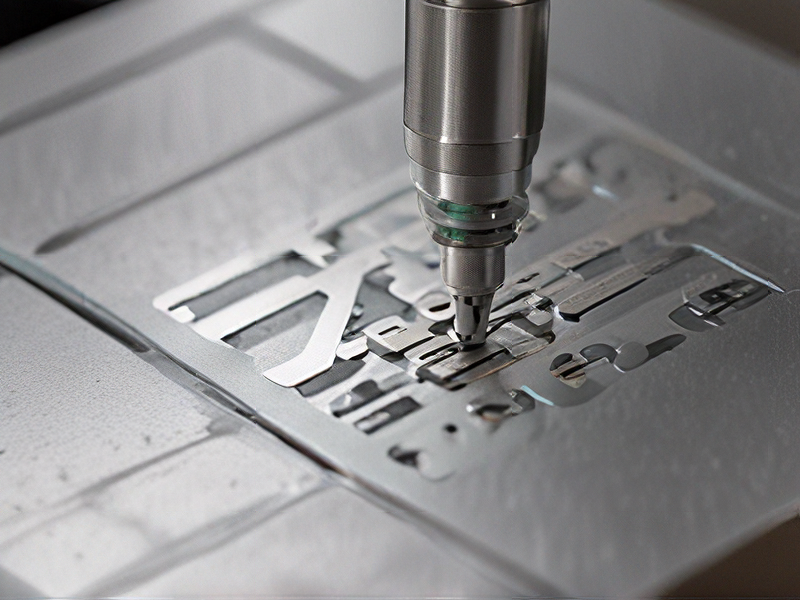