Technology and Applications of cutter for metal
Technology and Applications of Metal Cutters
Metal cutting is a fundamental process in manufacturing, involving the removal of material from a metal workpiece to shape it into the desired form. The technology and applications of metal cutters are diverse, catering to various industries such as automotive, aerospace, construction, and electronics.
#### Technologies of Metal Cutting
1. Mechanical Cutting:
– Sawing: Uses blades to cut through metal. Bandsaws and hacksaws are common types.
– Milling: Employs rotary cutters to remove material from the workpiece. CNC (Computer Numerical Control) milling machines offer high precision.
– Turning: Conducted on a lathe, this process rotates the workpiece against a cutting tool.
2. Thermal Cutting:
– Laser Cutting: Utilizes a high-powered laser beam to melt and vaporize metal, offering precision and speed.
– Plasma Cutting: Employs a jet of ionized gas (plasma) to cut through electrically conductive metals.
– Oxy-Fuel Cutting: Burns metal using a mixture of oxygen and fuel gases, suitable for cutting thick steel.
3. Electrical Cutting:
– Electrical Discharge Machining (EDM): Uses electrical discharges (sparks) to erode metal. It’s highly precise and used for intricate shapes.
#### Applications of Metal Cutters
1. Automotive Industry: Cutting components like gears, engine parts, and body frames.
2. Aerospace Industry: Precision cutting of high-strength alloys for aircraft parts.
3. Construction: Cutting steel beams, pipes, and reinforcing bars.
4. Electronics: Precision cutting for circuit boards and electronic components.
5. Fabrication Shops: General purpose cutting for various custom metal products.
Modern metal cutting technologies, particularly CNC machines and laser cutters, offer enhanced precision, efficiency, and versatility, meeting the high standards required in advanced manufacturing industries.
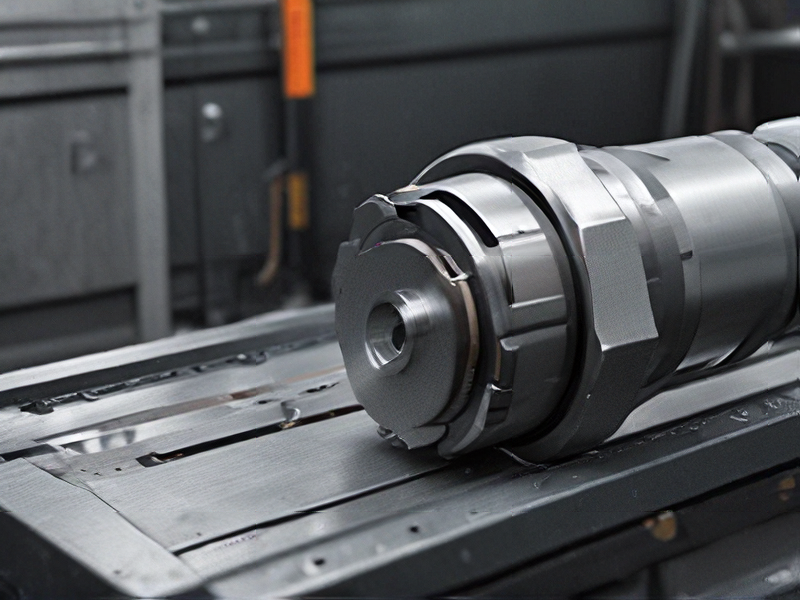
Quality Testing Methods for cutter for metal and how to control quality
Quality testing methods for metal cutters typically involve a combination of non-destructive and destructive techniques to ensure performance and durability. Non-destructive methods include visual inspection for surface defects, dimensional checks using calipers or micrometers, and ultrasonic testing to detect internal flaws without damaging the cutter.
Destructive testing methods involve taking samples for analysis, such as tensile testing to evaluate material strength, hardness testing using Rockwell or Vickers scales, and metallographic examination to assess microstructure integrity and grain size.
To control quality effectively:
1. Establish Specifications: Define precise requirements for dimensions, material composition, hardness, and surface finish.
2. Process Control: Monitor manufacturing processes closely to ensure consistency, including cutting parameters, heat treatment, and surface treatment.
3. Inspection Protocols: Implement regular inspections at critical stages of production and final inspection before shipment.
4. Documentation: Maintain detailed records of testing results and production parameters to trace quality issues and ensure compliance with standards.
5. Continuous Improvement: Analyze defects and customer feedback to refine processes and enhance product reliability.
By integrating these methods and controls, manufacturers can optimize the quality of metal cutters, ensuring they meet performance expectations and withstand operational demands effectively.
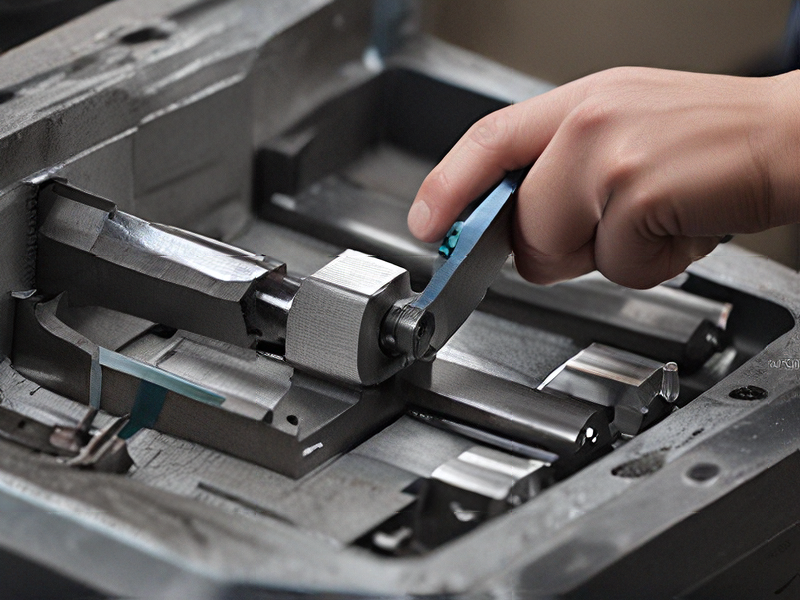
Tips for Procurement and Considerations when Purchasing from cutter for metal
When purchasing a metal cutter, consider these key procurement tips:
1. Define Requirements Clearly: Specify the type of metal you’ll be cutting (e.g., stainless steel, aluminum) and the thicknesses involved. This ensures you select a cutter suited to your needs.
2. Research Types of Cutters: Evaluate different types such as plasma cutters, laser cutters, or abrasive water jets. Each has unique capabilities and cost considerations based on precision, speed, and operating costs.
3. Evaluate Performance Metrics: Look at factors like cutting speed, accuracy, reliability, and ease of maintenance. These metrics impact productivity and operational efficiency.
4. Consider Operational Costs: Assess not only the initial purchase price but also ongoing costs such as energy consumption, maintenance requirements, and consumables (e.g., gas, electrodes).
5. Supplier Reputation and Support: Choose a reputable supplier known for quality products and reliable customer support. Check reviews and seek recommendations from industry peers.
6. Safety Features and Compliance: Ensure the cutter meets safety standards and consider additional safety features like automated shut-off mechanisms and protective guards.
7. Integration with Existing Systems: If integrating into an existing workflow, compatibility with other machinery and software systems is crucial for seamless operations.
8. Training and Support: Factor in training requirements for your team to operate and maintain the cutter effectively. Supplier-provided training can reduce downtime and improve safety.
9. Warranty and Service Agreements: Review warranty terms and service agreements to understand coverage and response times for repairs and maintenance.
10. Future Expansion: Consider future business growth and whether the cutter can accommodate increased production volumes or expanded capabilities.
By carefully considering these factors, you can make an informed decision that aligns with your operational needs and budgetary constraints when purchasing a metal cutter.
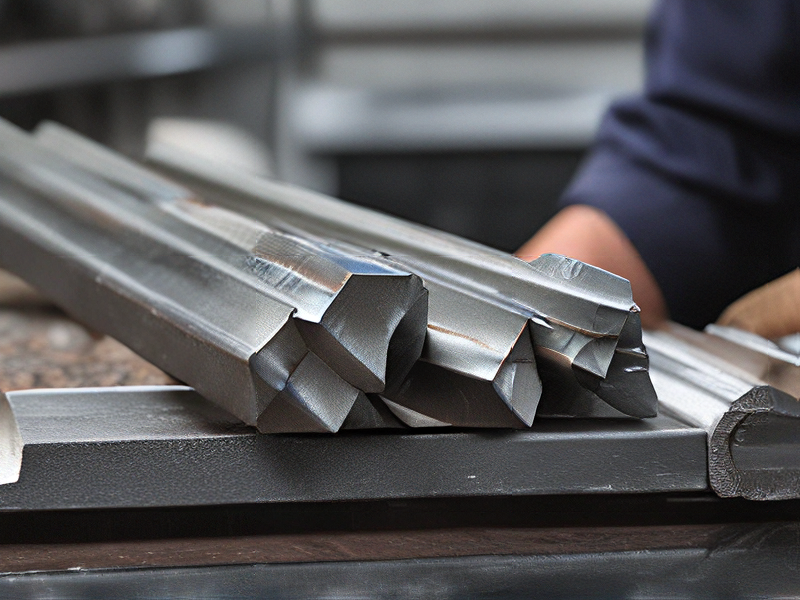
FAQs on Sourcing and Manufacturing from cutter for metal in China
FAQs on Sourcing and Manufacturing Metal Cutters in China
1. Why source metal cutters from China?
China is known for its cost-effective manufacturing, high production capacity, and technological advancements. This makes it a popular destination for sourcing metal cutters.
2. How to find reliable suppliers?
Use platforms like Alibaba, Global Sources, and Made-in-China. Verify suppliers through customer reviews, request samples, and conduct factory audits.
3. What certifications should I look for?
Look for ISO 9001 for quality management, ISO 14001 for environmental management, and specific certifications like CE for safety standards.
4. How to ensure product quality?
Request detailed product specifications, visit factories if possible, and hire third-party inspection services to verify quality before shipment.
5. What are the common payment terms?
Common terms include 30% deposit upfront and 70% before shipment (T/T), Letters of Credit (L/C), and sometimes PayPal for small orders.
6. What is the usual production lead time?
Lead times vary but typically range from 30 to 60 days, depending on order complexity and quantity.
7. How to handle shipping and logistics?
Suppliers often handle shipping. Ensure you discuss Incoterms (FOB, CIF, etc.), and consider hiring a freight forwarder for smooth logistics.
8. Are there any import duties or taxes?
Yes, import duties and taxes vary by country. Check your local customs regulations or consult with a customs broker.
9. How to deal with communication barriers?
Use clear, concise language, confirm details in writing, and consider hiring a local agent or translator if needed.
10. What should I do if there are quality issues?
Address issues immediately with the supplier, referencing the agreed-upon specifications. Use dispute resolution services on platforms like Alibaba if necessary.
11. What are the benefits of long-term relationships with suppliers?
Long-term relationships can lead to better pricing, priority service, improved product quality, and more reliable delivery times.
12. How to keep costs down?
Negotiate bulk order discounts, reduce customization where possible, and streamline your logistics to cut costs.
By following these guidelines, you can effectively source and manufacture metal cutters in China, ensuring quality and efficiency in your supply chain.
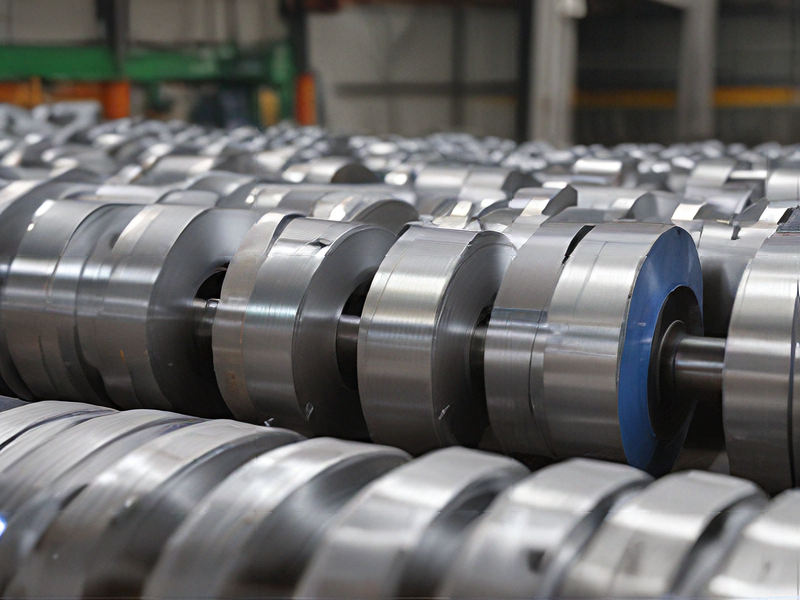