Technology and Applications of centerless grinder
Centerless grinding is a precision machining process used to create tight tolerances on cylindrical parts without the need for centering the workpiece. This method employs two wheels: the grinding wheel, which performs the grinding, and the regulating wheel, which controls the workpiece’s feed and rotation. It is particularly advantageous for high-volume production due to its efficiency and speed.
Technology: Modern centerless grinders are equipped with advanced CNC (Computer Numerical Control) systems, enabling precise adjustments and automation. They utilize sensors and feedback mechanisms for real-time monitoring and correction, ensuring consistent quality. Additionally, innovations in materials for grinding wheels, such as diamond and CBN (Cubic Boron Nitride), enhance longevity and performance, allowing the grinding of harder materials.
Applications: Centerless grinders are widely used across various industries, including automotive, aerospace, and medical device manufacturing. They are ideal for producing components like shafts, rods, and pins with high geometrical accuracy and surface finish. Specific applications include grinding fuel injectors, bearing races, and precision dowel pins.
Moreover, the centerless grinding process is versatile, accommodating different materials, such as metals, plastics, and composites. Its efficiency in producing long, slender parts makes it a preferred choice for manufacturers seeking to optimize productivity while minimizing waste.
In summary, the technology behind centerless grinders combines precision engineering with advanced automation, making it a vital tool in modern manufacturing processes, especially where high-volume and high-precision components are required.
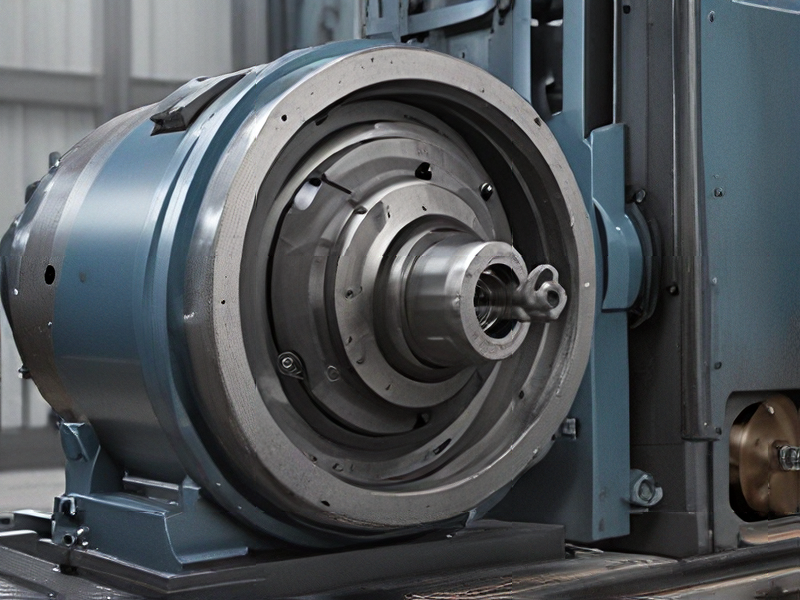
Quality Testing Methods for centerless grinder and how to control quality
Quality testing methods for centerless grinders typically include:
1. Dimensional Accuracy: Use calibrated measurement tools like micrometers and gauges to verify dimensions of ground components against specified tolerances.
2. Surface Finish: Employ surface roughness testers to ensure the surface finish meets required specifications, crucial for functional performance and aesthetics.
3. Roundness: Use roundness testers to check the circularity of the ground parts, ensuring they conform to design requirements.
4. Tolerance Control: Implement statistical process control (SPC) techniques to monitor key parameters such as grinding wheel speed, feed rate, and stock removal to maintain consistency and adherence to tolerances.
5. Visual Inspection: Conduct visual inspections to detect surface defects, such as scratches, burns, or irregularities that could affect part performance or aesthetics.
To control quality effectively:
– Calibration: Regularly calibrate measuring instruments to ensure accuracy in dimensional and surface finish measurements.
– Operator Training: Provide comprehensive training to operators on machine settings, tooling adjustments, and quality standards to minimize variability in production.
– Maintenance: Implement a proactive maintenance schedule for the grinder to prevent downtime and ensure consistent performance.
– Documentation: Maintain detailed records of quality inspections and adjustments made during the grinding process to facilitate traceability and continuous improvement.
By integrating these methods and controls, manufacturers can achieve consistent quality in centerless grinding operations, meeting customer specifications and enhancing overall product reliability.
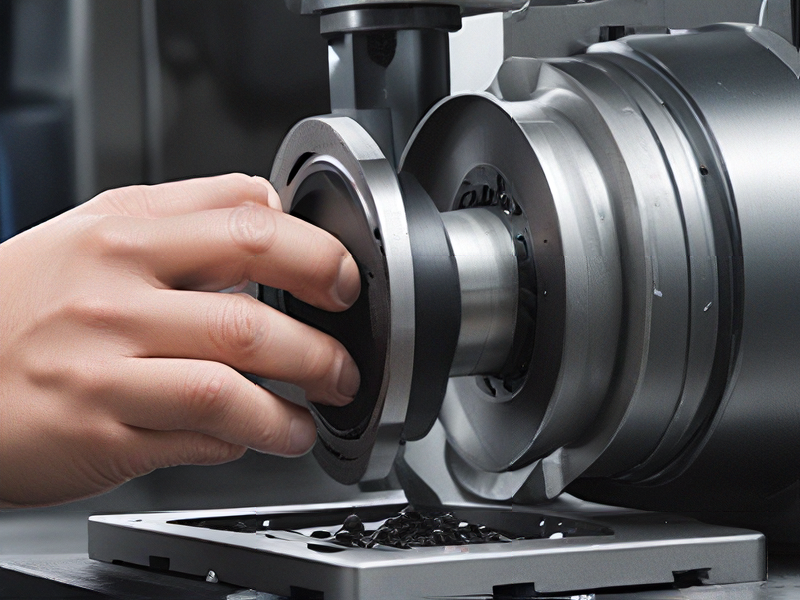
Tips for Procurement and Considerations when Purchasing from centerless grinder
When procuring a centerless grinder, careful consideration and strategic planning are crucial to ensure the best investment. Here are some key tips and considerations:
Tips for Procurement:
1. Define Requirements: Clearly outline the specifications needed for your applications, including the materials to be processed, tolerance levels, and production volume.
2. Research Suppliers: Identify reputable manufacturers and suppliers with a track record of reliability, quality, and customer support.
3. Budgeting: Establish a realistic budget that encompasses not only the purchase price but also installation, maintenance, and potential upgrades.
4. Request Quotes: Obtain detailed quotes from multiple suppliers, ensuring that all costs, including shipping and installation, are transparent.
5. Evaluate Features: Compare the technical features of different models, such as grinding speed, precision, automation capabilities, and ease of maintenance.
6. Check References: Seek feedback from other customers who have purchased the same or similar equipment to gauge performance and reliability.
7. Negotiate Terms: Negotiate the terms of sale, including warranties, service agreements, and training for your operators.
Considerations when Purchasing:
1. Machine Compatibility: Ensure the grinder is compatible with your existing production setup and future needs.
2. Quality and Precision: Look for machines that offer high precision and consistent quality to meet your production standards.
3. Ease of Use: Consider the ease of operation and maintenance, as well as the availability of user-friendly interfaces and controls.
4. Support and Service: Evaluate the supplier’s after-sales support, including the availability of spare parts, technical assistance, and response time for repairs.
5. Training: Ensure that the supplier provides comprehensive training for your staff to maximize the efficiency and safety of the machine.
6. Energy Efficiency: Consider the energy consumption of the grinder, as more efficient models can lead to significant cost savings over time.
7. Future Scalability: Choose a machine that can be easily upgraded or expanded to meet future production demands without requiring a complete overhaul of your equipment.
By carefully considering these factors, you can make an informed decision that will enhance your production capabilities and provide long-term value.
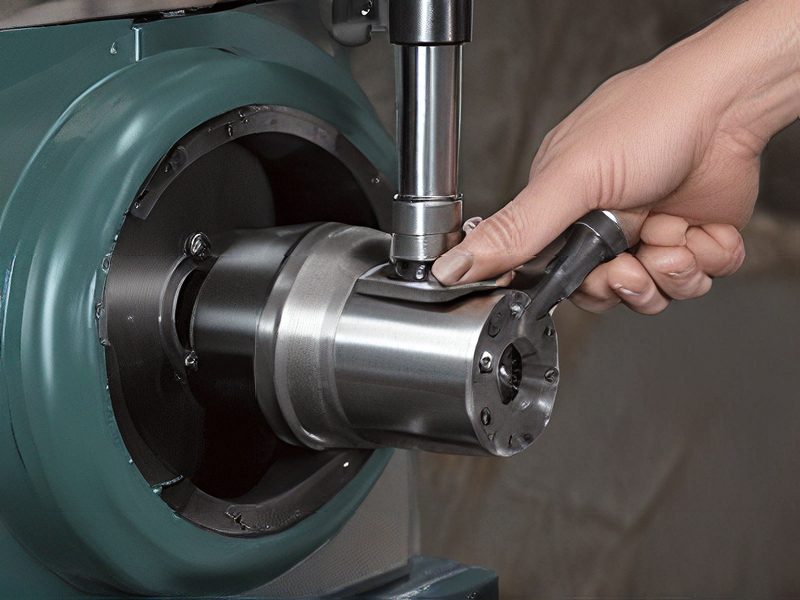
FAQs on Sourcing and Manufacturing from centerless grinder in China
FAQs on Sourcing and Manufacturing Centerless Grinders from China
1. Why source centerless grinders from China?
China offers cost-effective manufacturing, a wide variety of suppliers, and advanced technology. Many Chinese manufacturers specialize in precision machinery, making it a hub for high-quality centerless grinders.
2. How to find reliable suppliers?
Use platforms like Alibaba, Made-in-China, and Global Sources. Look for suppliers with verified profiles, positive reviews, and a history of exporting. Attending trade shows like the Canton Fair can also help identify reliable manufacturers.
3. What should I consider when evaluating suppliers?
Consider the supplier’s experience, certifications (ISO, CE), production capacity, and quality control processes. Request samples to assess quality firsthand. Conduct factory audits if possible.
4. What are the common payment terms?
Typical terms include a 30% deposit upfront and the remaining 70% upon shipment. Letter of Credit (L/C) and escrow services are also common to protect both parties.
5. How to ensure product quality?
Implement strict quality control measures, such as pre-shipment inspections by third-party companies. Establish clear specifications and standards in your contract.
6. What are the lead times for manufacturing?
Lead times vary but generally range from 30 to 60 days, depending on the complexity and quantity of the order. Confirm lead times with your supplier and include them in your contract.
7. What about logistics and shipping?
Choose reputable freight forwarders experienced in international shipping. Decide on shipping terms (FOB, CIF, DDP) that best suit your needs. Factor in customs clearance and import duties in your planning.
8. Are there any risks?
Risks include quality issues, communication barriers, and shipping delays. Mitigate these by choosing reputable suppliers, using clear contracts, and maintaining regular communication.
9. How to handle after-sales service and warranties?
Clarify warranty terms and after-sales support in your contract. Ensure the supplier provides technical support and spare parts availability. Consider a local service partner for maintenance and repairs.
By following these guidelines, you can effectively source and manufacture centerless grinders from China while minimizing risks and ensuring product quality.
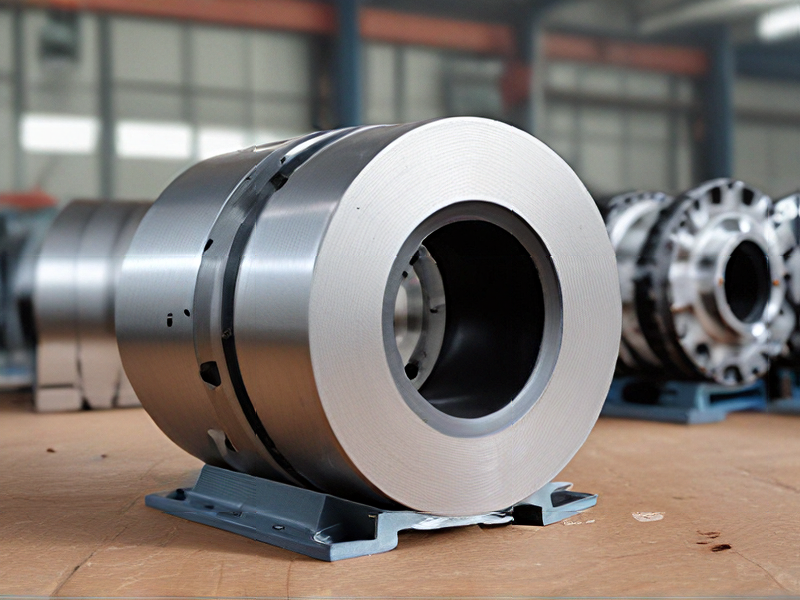