Technology and Applications of composition of stainless steels
Stainless steels are iron-based alloys known for their corrosion resistance, which is primarily due to their chromium content, usually at least 10.5% by mass. The composition of stainless steel can vary, including elements like nickel, molybdenum, and nitrogen to enhance specific properties.
Technology of Composition:
1. Chromium (Cr): Provides corrosion resistance by forming a passive oxide layer.
2. Nickel (Ni): Adds toughness and improves corrosion resistance, especially in acidic environments.
3. Molybdenum (Mo): Increases resistance to pitting and crevice corrosion.
4. Carbon (C): In small amounts, increases hardness and strength but too much can reduce corrosion resistance.
5. Nitrogen (N): Enhances strength and improves pitting resistance.
6. Manganese (Mn): Often used to replace nickel to reduce costs while maintaining austenitic structure.
Applications:
1. Construction: Stainless steel is used in building facades, bridges, and structural components due to its strength, durability, and resistance to weathering.
2. Medical Devices: Its biocompatibility and resistance to corrosion make it ideal for surgical instruments, implants, and medical tools.
3. Automotive and Aerospace: Used in exhaust systems, aircraft components, and structural parts for its high strength-to-weight ratio and corrosion resistance.
4. Food and Beverage Industry: Commonly used in equipment like tanks, pipes, and tools due to its ease of cleaning, non-reactivity, and resistance to contamination.
5. Chemical Processing: In equipment handling corrosive substances, stainless steel resists oxidation and chemical attack, ensuring longevity and reliability.
By adjusting the composition, stainless steels can be tailored for specific applications, enhancing properties like corrosion resistance, strength, and toughness to meet diverse industrial needs.
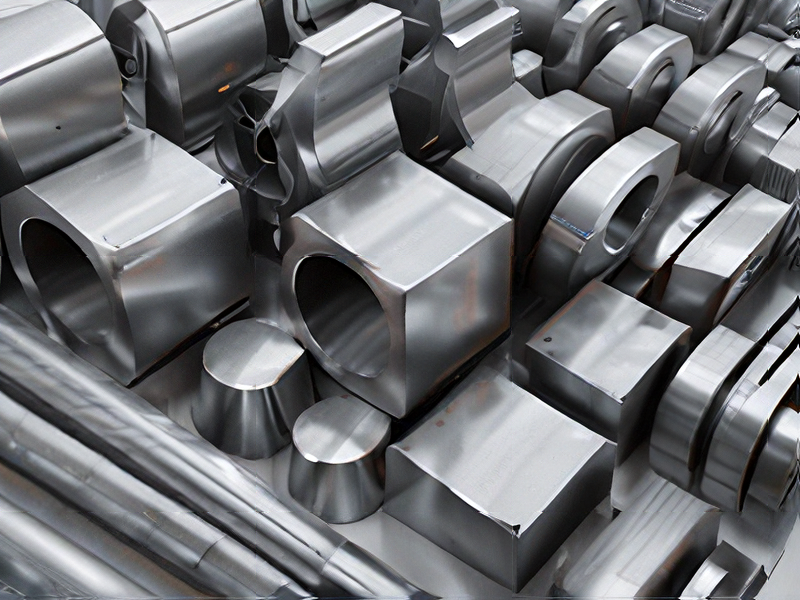
Quality Testing Methods for composition of stainless steels and how to control quality
Quality testing methods for stainless steels typically include a range of physical, chemical, and sometimes mechanical tests to ensure the composition meets specified standards. Here are key methods:
1. Chemical Composition Analysis: Utilizes techniques like X-ray fluorescence (XRF) or optical emission spectroscopy (OES) to determine the elemental composition of stainless steel. This ensures the correct proportions of chromium, nickel, molybdenum, etc.
2. Microstructure Examination: Involves metallographic techniques such as optical microscopy or scanning electron microscopy (SEM) to assess grain size, phases present, and overall microstructural integrity.
3. Mechanical Properties Testing: Involves tensile testing, hardness testing (e.g., Rockwell or Vickers), and impact testing to verify mechanical strength and resilience of the stainless steel.
4. Corrosion Resistance Testing: Conducted through methods like salt spray testing or exposure in corrosive environments to evaluate resistance to rust, oxidation, and other forms of corrosion.
5. Non-Destructive Testing (NDT): Techniques such as ultrasonic testing (UT) or magnetic particle inspection (MPI) are used to detect surface and internal defects without damaging the material.
To control quality, manufacturers implement rigorous procedures:
– Quality Management Systems (QMS): Establish standards and protocols for testing and inspection throughout production.
– Supplier Quality Assurance: Ensures raw materials meet required specifications before use.
– Process Control: Monitoring and adjusting parameters during manufacturing to maintain consistency.
– Traceability: Tracking materials and processes to identify and rectify any deviations or issues.
– Certifications and Standards Compliance: Adhering to international standards (e.g., ASTM, ISO) ensures product reliability and customer satisfaction.
By employing these methods and controls, manufacturers can consistently produce stainless steels that meet stringent quality requirements for various applications.
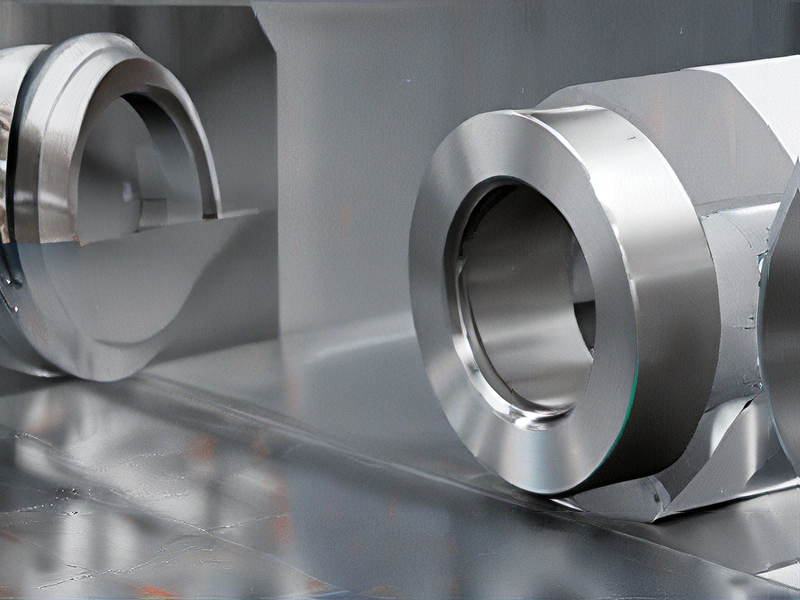
Tips for Procurement and Considerations when Purchasing from composition of stainless steels
Tips for Procurement and Considerations When Purchasing Stainless Steels
#### Understand the Application
Before procuring stainless steel, identify the specific application requirements. Different grades of stainless steel offer varying properties such as corrosion resistance, strength, and machinability. For instance, 304 stainless steel is excellent for general purposes, while 316 stainless steel is better suited for environments with high corrosion, such as marine applications.
#### Material Specifications
Verify the material specifications according to industry standards like ASTM, ISO, or EN. Ensure the chemical composition and mechanical properties meet the desired requirements. Key elements to check include chromium (for corrosion resistance), nickel (for toughness), and molybdenum (for additional corrosion resistance in chloride environments).
#### Supplier Credentials
Choose reputable suppliers with certifications like ISO 9001 for quality management. Review their track record, customer feedback, and ensure they provide material test reports (MTRs) to confirm compliance with specified standards.
#### Cost vs. Performance
Balance cost with performance needs. While higher-grade stainless steels like duplex or super-austenitic may offer superior properties, they come at a higher price. Evaluate if the added performance benefits justify the cost for your specific application.
#### Fabrication Considerations
Consider the ease of fabrication, including welding, machining, and forming. Some stainless steels, like 303, are specifically designed for improved machinability. Ensure that the chosen grade can be easily processed with available equipment and expertise.
#### Environmental Factors
Take into account the operating environment. Factors such as temperature extremes, exposure to chemicals, and humidity can impact the performance and longevity of stainless steel. Choose a grade that can withstand these conditions to avoid premature failure and additional costs.
#### Long-term Maintenance
Evaluate the long-term maintenance requirements and lifecycle costs. While some stainless steels may have a higher upfront cost, their durability and lower maintenance needs can offer cost savings over time.
By thoroughly considering these factors, you can make informed decisions when procuring stainless steel, ensuring optimal performance, cost-efficiency, and reliability for your applications.
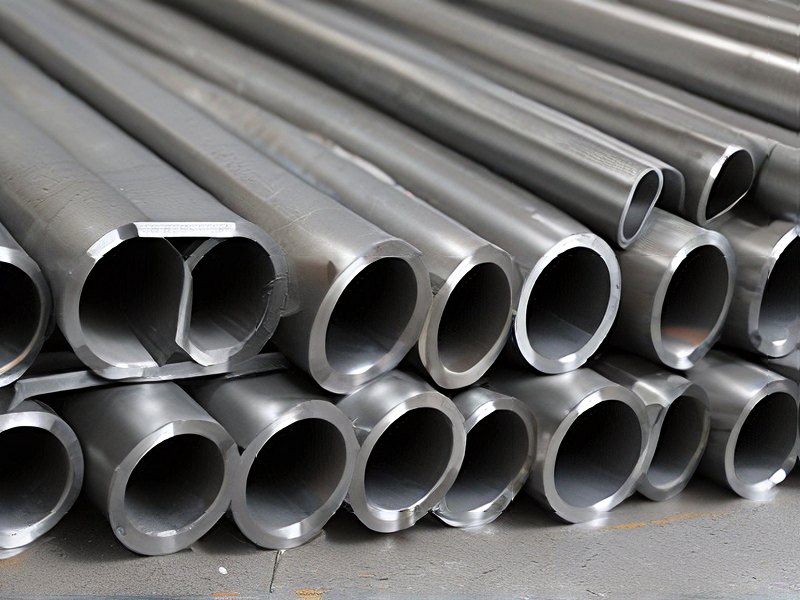
FAQs on Sourcing and Manufacturing from composition of stainless steels in China
When sourcing stainless steels from China, understanding composition and manufacturing processes is crucial. Here are some FAQs:
1. What are the common grades of stainless steel manufactured in China?
China produces a wide range of stainless steel grades, including austenitic (such as 304, 316), ferritic (such as 430), and duplex (such as 2205).
2. How can I ensure the quality of stainless steel sourced from China?
Verify that manufacturers adhere to international standards like ASTM or EN. Request material test reports (MTRs) to confirm chemical composition and mechanical properties.
3. Are there specific concerns with sourcing stainless steel from China?
Quality consistency and adherence to specifications can vary. It’s crucial to conduct thorough due diligence on suppliers and possibly perform independent quality inspections.
4. What manufacturing processes are commonly used for stainless steel in China?
Processes include hot rolling, cold rolling, and various surface treatments like pickling and passivation. For specialized applications, additional processes like heat treatment may be employed.
5. What certifications should I look for when sourcing stainless steel from China?
ISO 9001 certification ensures quality management systems are in place. For specific industries, additional certifications like ISO 14001 (environmental management) or product-specific certifications may be necessary.
Understanding these points will help navigate sourcing stainless steels from China effectively, ensuring quality and meeting your project requirements.
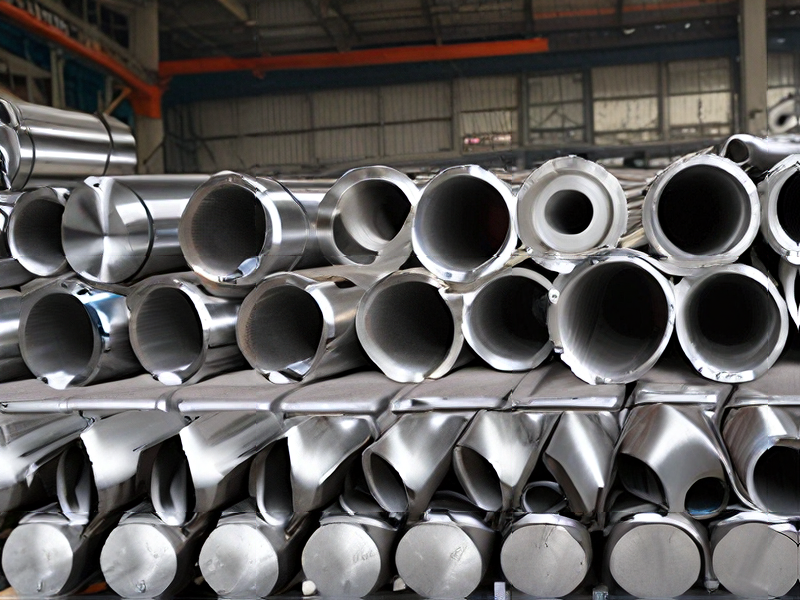