Technology and Applications of heating metal
Heating metals finds extensive applications across various industries, leveraging both traditional and modern technologies. Induction heating stands out as a prevalent method, utilizing electromagnetic induction to heat metals rapidly and efficiently. This technology is favored for its precise control over temperature and heating patterns, crucial in applications such as metal fabrication, forging, and heat treatment processes like annealing and hardening.
In industrial settings, resistance heating remains vital, employing electric current passing through the metal to generate heat. This method is widely used in electric furnaces and resistance welding, ensuring uniform heating across large metal components or sheets.
Flame heating, utilizing oxy-acetylene or other gases, offers versatility in portable and localized heating tasks, suitable for welding, cutting, and brazing operations. This method is valued for its mobility and ability to heat metals of varying thicknesses.
Furthermore, advancements in laser and electron beam technologies provide precise and localized heating for applications requiring high accuracy, such as in microelectronics and medical device manufacturing.
Overall, the choice of heating method depends on factors like the type of metal, required heating speed, temperature control needs, and the specific application’s scale. These technologies continue to evolve, driven by demands for efficiency, precision, and sustainability in metal heating processes across industries.
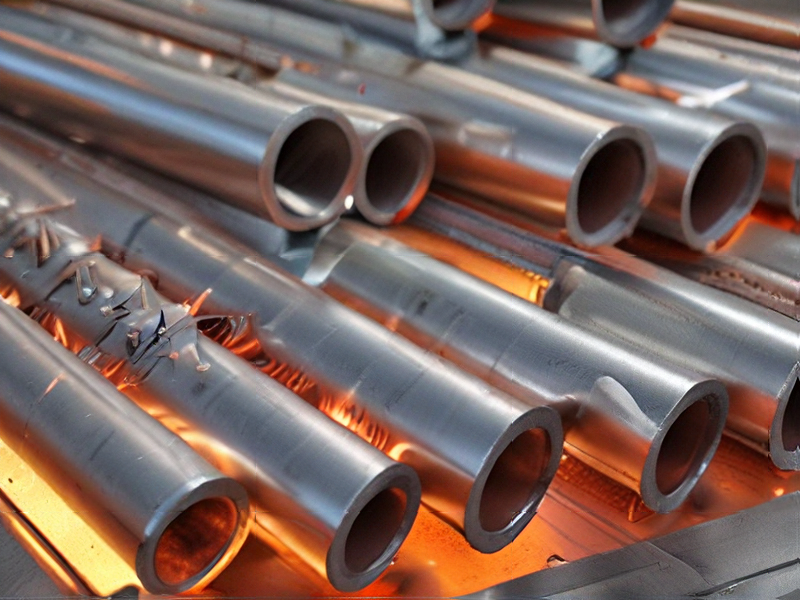
Quality Testing Methods for heating metal and how to control quality
Quality testing methods for heating metal typically involve both destructive and non-destructive techniques to ensure desired properties are achieved without compromising structural integrity.
1. Non-Destructive Testing (NDT):
– Visual Inspection: Surface checks for cracks, deformities, or discolorations.
– Ultrasonic Testing: Uses high-frequency sound waves to detect internal flaws like voids or cracks.
– Eddy Current Testing: Detects surface and near-surface flaws by inducing eddy currents and measuring resulting electromagnetic fields.
– Radiographic Testing: Uses X-rays or gamma rays to detect internal defects.
2. Destructive Testing:
– Tensile Testing: Measures material strength and ductility by applying tensile force until failure.
– Hardness Testing: Determines material hardness using methods like Rockwell or Brinell scales.
– Metallographic Examination: Analyzes microstructure to assess grain size, inclusion content, and phase distribution.
Quality Control Measures:
1. Process Control:
– Temperature Monitoring: Ensure heating processes adhere to specified temperature profiles to avoid overheating or underheating.
– Time Control: Maintain consistent heating durations to achieve desired metallurgical transformations.
– Atmosphere Control: Monitor and control the atmosphere to prevent oxidation or decarburization.
2. Statistical Process Control (SPC):
– Control Charts: Track key process variables like temperature or heating time to detect and correct deviations.
– Sampling and Testing: Regularly sample and test heated metals to verify adherence to quality standards.
3. Documentation and Traceability:
– Record Keeping: Document process parameters, testing results, and any deviations for traceability and analysis.
– Quality Assurance: Implement quality management systems (e.g., ISO standards) to ensure consistent quality.
By combining these testing methods and control measures, manufacturers can effectively ensure the quality of heated metals, meeting both regulatory requirements and customer expectations.
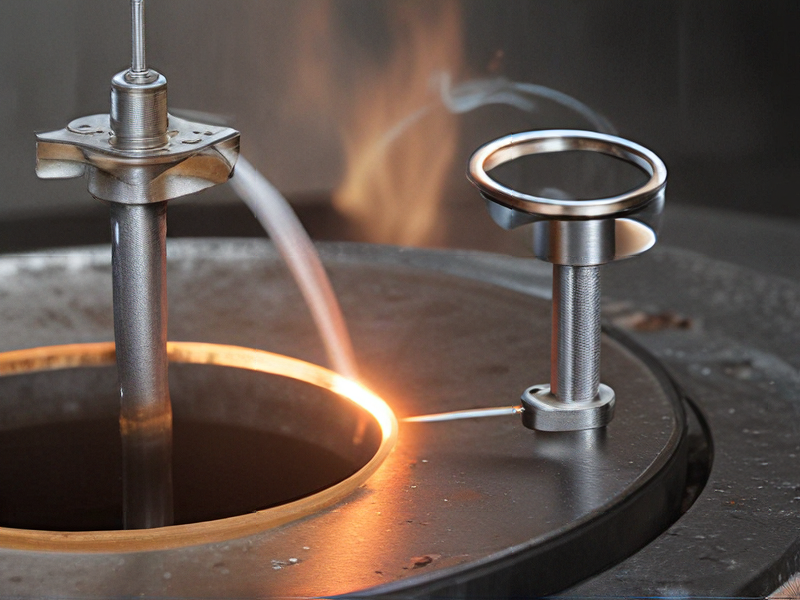
Tips for Procurement and Considerations when Purchasing from heating metal
When procuring heating metals, several considerations are crucial to ensure efficiency and effectiveness:
1. Material Specifications: Determine the exact material composition required for your heating application, considering factors like conductivity, durability, and resistance to corrosion.
2. Supplier Reliability: Choose suppliers with a proven track record for delivering high-quality materials on time. Check references and consider their ability to meet your volume and customization requirements.
3. Cost Efficiency: Balance cost with quality. Compare quotes from multiple suppliers to ensure competitive pricing without compromising on material standards.
4. Technical Support: Seek suppliers who offer technical assistance and guidance. They should be able to help you choose the right material and provide support during installation or integration.
5. Environmental Considerations: Assess the environmental impact of the materials you’re purchasing. Ensure compliance with regulations and consider materials that are recyclable or have a lower environmental footprint.
6. Logistics and Lead Times: Evaluate shipping logistics and lead times to avoid delays in your production schedule. Ensure the supplier can consistently meet your delivery timelines.
7. Quality Assurance: Implement quality control measures to verify material specifications upon delivery. This includes conducting tests to ensure the materials meet your performance requirements.
8. Long-Term Relationship: Consider building a long-term relationship with your supplier to secure stable pricing, consistent quality, and reliable service over time.
By focusing on these considerations, you can effectively procure heating metals that meet your operational needs while ensuring cost-efficiency and reliability in your supply chain.
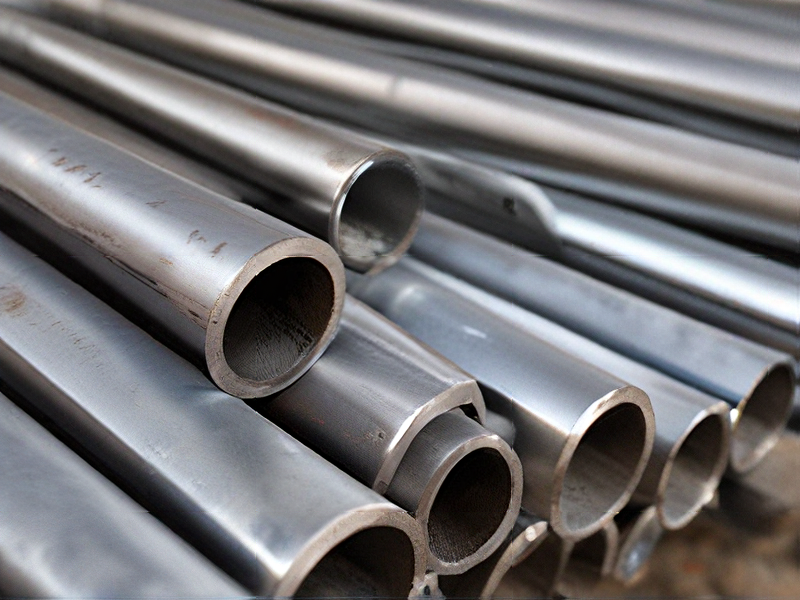
FAQs on Sourcing and Manufacturing from heating metal in China
When sourcing and manufacturing heating metal components in China, it’s crucial to address several FAQs:
1. Quality Assurance: How can quality be ensured? Engage with reputable manufacturers with ISO certifications and conduct regular inspections during production.
2. Cost Management: How can costs be controlled? Obtain detailed quotes, negotiate prices upfront, and clarify all cost inclusions to avoid unexpected expenses.
3. Communication: How to overcome language barriers? Utilize bilingual project managers or interpreters and maintain clear, written communication to minimize misunderstandings.
4. Lead Times: What are typical lead times? Plan for longer lead times due to manufacturing and shipping logistics; factor in buffer time for unexpected delays.
5. Intellectual Property: How to protect IP? Use non-disclosure agreements (NDAs) and consider registering patents or trademarks in China if applicable.
6. Logistics and Shipping: How to manage logistics? Partner with freight forwarders experienced in shipping from China to ensure timely delivery and minimize shipping costs.
7. Cultural Differences: How to navigate cultural differences? Understand cultural norms and business etiquette to build strong, respectful relationships with Chinese partners.
8. Payment Terms: What are common payment terms? Negotiate payment terms that balance risk and ensure compliance with international trade regulations.
9. Compliance and Regulations: What regulatory requirements apply? Stay updated on Chinese and international regulations for manufacturing and import/export to avoid legal issues.
10. After-Sales Support: How to handle after-sales support? Define expectations clearly in contracts and maintain open communication channels for swift issue resolution.
Navigating these aspects diligently can streamline sourcing and manufacturing processes in China while mitigating common challenges and risks.
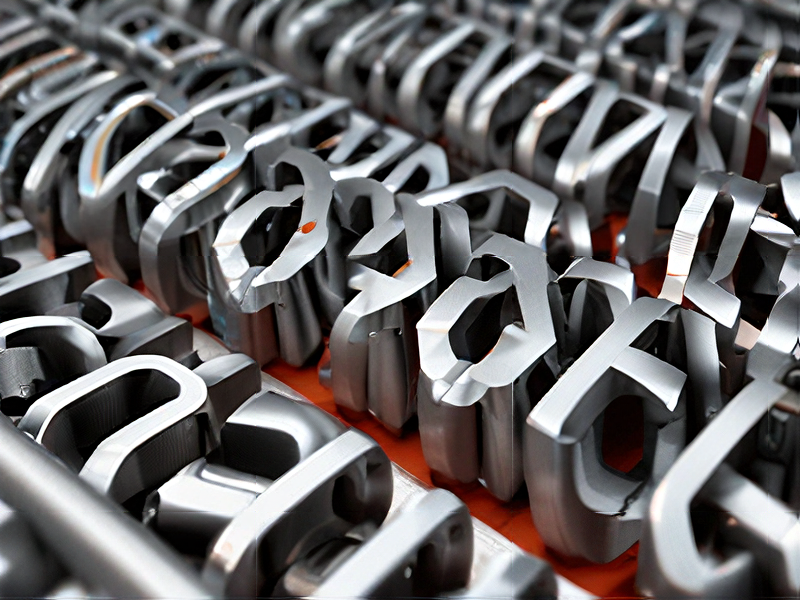