Technology and Applications of metal cnc machines
Metal CNC (Computer Numerical Control) machines are pivotal in modern manufacturing due to their precision and versatility. These machines use computer programs to control tool movements, enabling intricate and accurate metal cutting, shaping, and drilling processes. They find extensive application in various industries such as aerospace, automotive, electronics, and healthcare.
Technology:
Metal CNC machines operate on CAD (Computer-Aided Design) files that specify the dimensions and shapes of parts to be machined. The CNC controller interprets these instructions and directs the machine’s motors to move the cutting tools along multiple axes (typically 3 to 5 axes in advanced machines) with high precision. The cutting tools can be changed automatically, allowing for complex geometries and fine finishes. High-speed spindles, coolant systems, and rigid structures ensure efficient material removal and dimensional accuracy.
Applications:
1. Precision Machining: CNC machines produce parts with tight tolerances, crucial for components in aerospace engines and medical implants.
2. Prototyping and Customization: Rapid prototyping allows for quick iterations and customization of parts, benefiting industries like automotive for concept cars and bespoke components.
3. Mass Production: CNC machines automate production processes, enhancing productivity and consistency in manufacturing large volumes of metal parts such as gears, shafts, and housings.
4. Tool and Die Making: CNC machining is essential in creating molds, dies, and tools used in injection molding, stamping, and casting processes.
5. Repair and Maintenance: CNC machines refurbish worn-out parts, extending equipment lifespan in industrial sectors.
In conclusion, metal CNC machines play a crucial role in modern manufacturing by enabling precise, efficient, and versatile production of metal components across various industries, driving innovation and quality in product development and production processes.
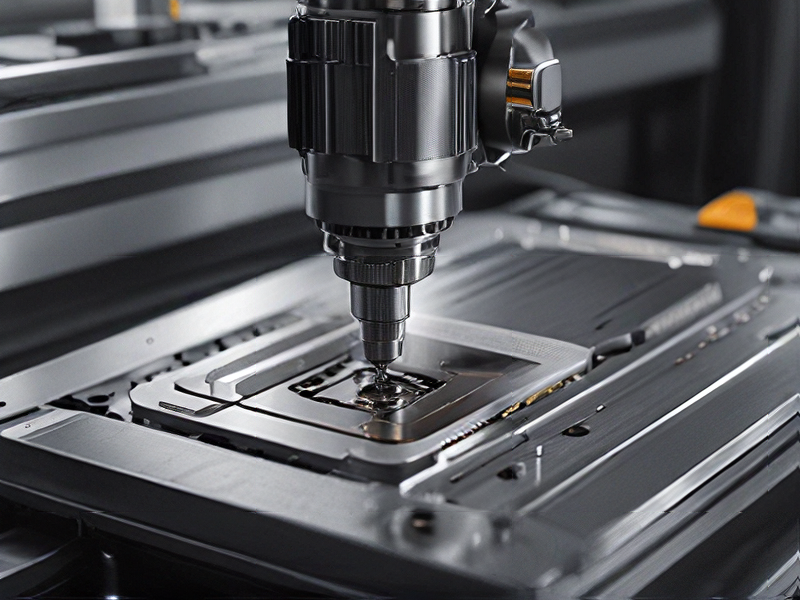
Quality Testing Methods for metal cnc machines and how to control quality
Quality testing methods for metal CNC machines typically include several key approaches:
1. Dimensional Accuracy: Using precision measuring tools like micrometers and calipers to verify the dimensions of machined parts against design specifications.
2. Surface Finish Inspection: Utilizing surface roughness testers to ensure the machined surfaces meet required smoothness and texture standards.
3. Material Testing: Performing material analysis to confirm the composition and properties (such as hardness and tensile strength) of the machined parts.
4. Functionality Testing: Assembling parts to check functionality, fit, and alignment within the final product assembly.
5. Durability Testing: Subjecting parts to stress tests (e.g., fatigue testing, impact testing) to evaluate durability and performance under various conditions.
To control quality effectively:
– Regular Calibration: Ensure CNC machines and measuring instruments are regularly calibrated to maintain accuracy.
– Standard Operating Procedures (SOPs): Implement detailed SOPs for machining processes to ensure consistency and repeatability.
– Quality Control Checks: Conduct inspections at each stage of production to detect defects early and prevent further processing of non-conforming parts.
– Training and Skill Development: Provide training to operators and inspectors on quality standards, inspection methods, and machine operation.
– Data Analysis: Use statistical process control (SPC) techniques to analyze production data and identify trends or deviations that may affect quality.
By integrating these methods and controls into the manufacturing process, companies can ensure that metal CNC machined parts meet high-quality standards consistently.
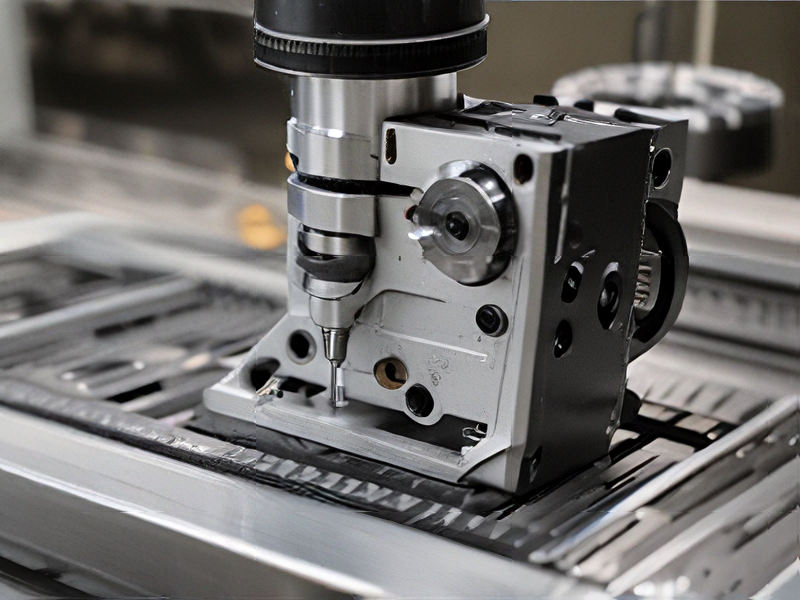
Tips for Procurement and Considerations when Purchasing from metal cnc machines
When procuring metal CNC machines, it’s crucial to consider several key factors to ensure you make a well-informed decision that meets your manufacturing needs. Here are some essential tips and considerations:
1. Machine Specifications:
– Accuracy and Precision: Evaluate the machine’s ability to produce parts with the required tolerance levels.
– Speed: Ensure the machine can operate at the speeds necessary for your production volume.
– Size and Capacity: Match the machine’s work envelope to the size of the parts you plan to produce.
2. Material Compatibility:
– Types of Metals: Verify that the CNC machine can handle the specific types of metals you work with, such as aluminum, steel, or titanium.
– Tooling Requirements: Check if the machine requires special tooling for different materials and whether these are readily available.
3. Software and Control Systems:
– User Interface: Ensure the control software is user-friendly and compatible with your current systems.
– CAD/CAM Compatibility: The machine should integrate seamlessly with your existing CAD/CAM software.
4. Manufacturer and Support:
– Reputation: Research the manufacturer’s reputation for reliability and customer service.
– Warranty and Support: Check the warranty terms and availability of technical support and spare parts.
5. Cost Considerations:
– Initial Investment: Balance your budget constraints with the need for a high-quality machine.
– Operating Costs: Factor in maintenance, power consumption, and tooling replacement costs.
6. Future-Proofing:
– Technology Upgrades: Consider the ease with which the machine can be upgraded with new technology.
– Scalability: Ensure the machine can accommodate future production increases.
7. Compliance and Safety:
– Regulations: Ensure the machine complies with local and international safety standards.
– Operator Safety: Check for features that enhance operator safety, such as emergency stop buttons and protective enclosures.
By meticulously evaluating these aspects, you can select a metal CNC machine that not only meets your current needs but also supports your future growth and operational efficiency.
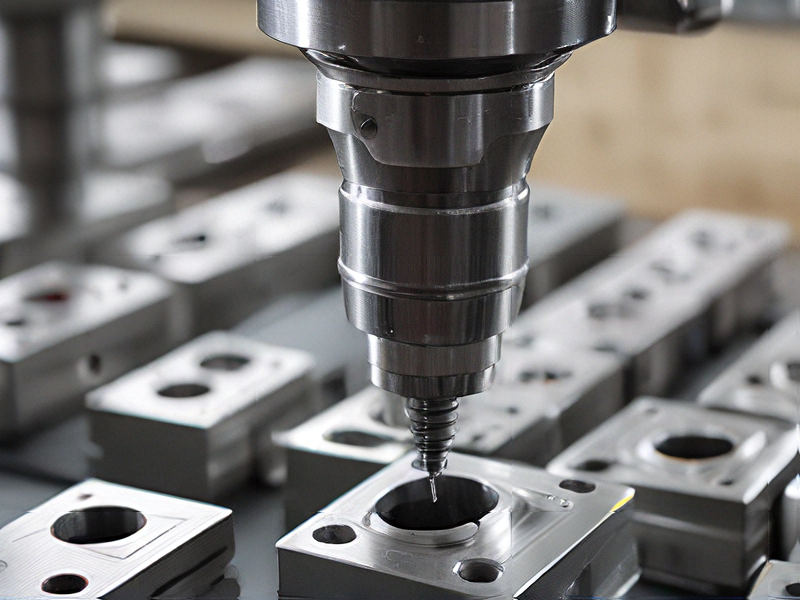
FAQs on Sourcing and Manufacturing from metal cnc machines in China
FAQs on Sourcing and Manufacturing from Metal CNC Machines in China
1. Why should I consider sourcing CNC machined parts from China?
China offers cost-effective solutions, advanced technology, skilled labor, and large production capacity, making it an attractive option for CNC machined parts.
2. How do I find reliable CNC machining suppliers in China?
Use platforms like Alibaba, Global Sources, and Made-in-China. Verify suppliers through third-party audits, customer reviews, and requesting sample parts.
3. What are the common materials used in CNC machining in China?
Common materials include aluminum, stainless steel, brass, copper, titanium, and various plastics.
4. How do I ensure the quality of CNC machined parts from China?
Specify detailed requirements, request samples, perform quality inspections, and consider using third-party inspection services.
5. What certifications should I look for in a Chinese CNC machining supplier?
Look for ISO 9001, ISO 14001, and IATF 16949 certifications, indicating quality management, environmental management, and automotive quality standards.
6. How can I communicate effectively with Chinese suppliers?
Use clear and concise English, employ translation tools if necessary, and maintain regular communication through emails, video calls, and instant messaging apps like WeChat.
7. What is the typical lead time for CNC machined parts from China?
Lead times vary but typically range from 2 to 6 weeks, depending on order complexity and volume.
8. How is intellectual property (IP) protected when sourcing from China?
Sign non-disclosure agreements (NDAs) and non-compete clauses, register your IP in China, and choose suppliers with good reputations for IP respect.
9. What are the payment terms for CNC machining services in China?
Common terms include 30% deposit upfront and 70% balance before shipment. Letters of credit and escrow services can provide additional security.
10. How do I handle shipping and logistics from China?
Work with experienced freight forwarders, understand Incoterms (FOB, CIF), and factor in customs duties and import regulations in your country.
Sourcing CNC machined parts from China can be highly beneficial if you ensure proper due diligence and clear communication throughout the process.
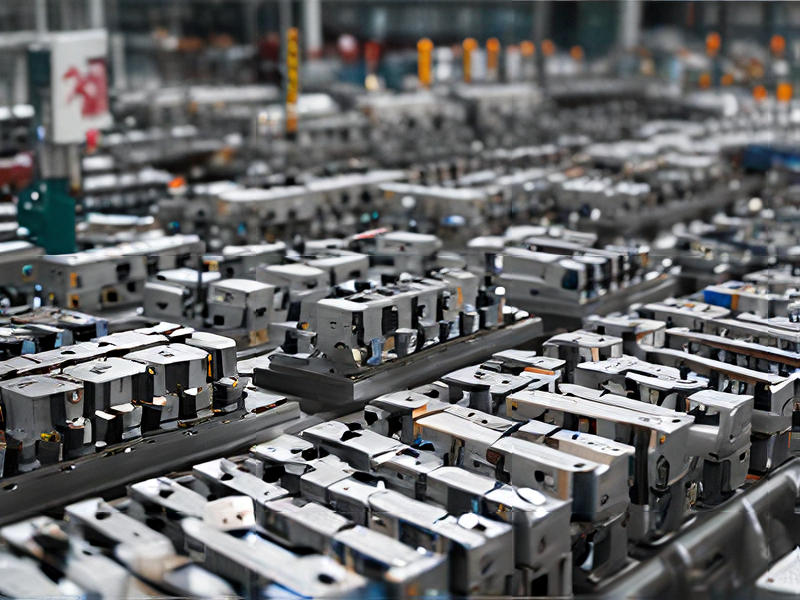