Technology and Applications of laser co2 cutting machine
CO2 laser cutting machines utilize a gas laser, primarily carbon dioxide, to cut and engrave materials. They operate by emitting a concentrated laser beam that heats and vaporizes material at the focal point. This technology is renowned for its precision, speed, and versatility in cutting a wide range of materials, including metals, plastics, wood, glass, and fabrics.
Technology:
1. Laser Source: The CO2 laser tube is filled with a mixture of carbon dioxide, nitrogen, hydrogen, and helium. When electricity passes through, it excites the gas molecules, producing a laser beam.
2. Beam Delivery: Mirrors and lenses direct and focus the laser beam onto the material.
3. Control System: CNC (Computer Numerical Control) or other automated systems control the movement of the laser head, ensuring precise cutting paths as programmed.
4. Cooling System: CO2 lasers generate heat, so water or air cooling systems are used to maintain optimal operating temperatures.
5. Assist Gas: Gases like oxygen or nitrogen are often used to blow away melted material, improving cutting efficiency and quality.
Applications:
1. Industrial Manufacturing: Cutting and engraving metals, such as steel and aluminum, for automotive, aerospace, and machinery parts.
2. Signage and Advertising: Creating detailed and custom signs from acrylic and other plastics.
3. Textiles and Fashion: Cutting patterns in fabrics with high precision and speed.
4. Electronics: Cutting and engraving circuit boards and other components with intricate designs.
5. Woodworking: Engraving and cutting wood for furniture, decorative items, and art pieces.
6. Medical Devices: Producing precise components for medical instruments and implants.
7. Prototyping and Customization: Rapidly creating prototypes and customized products in various materials.
CO2 laser cutting machines are highly valued for their ability to produce clean, precise cuts with minimal material waste. Their adaptability across numerous industries makes them a crucial tool in modern manufacturing and design.
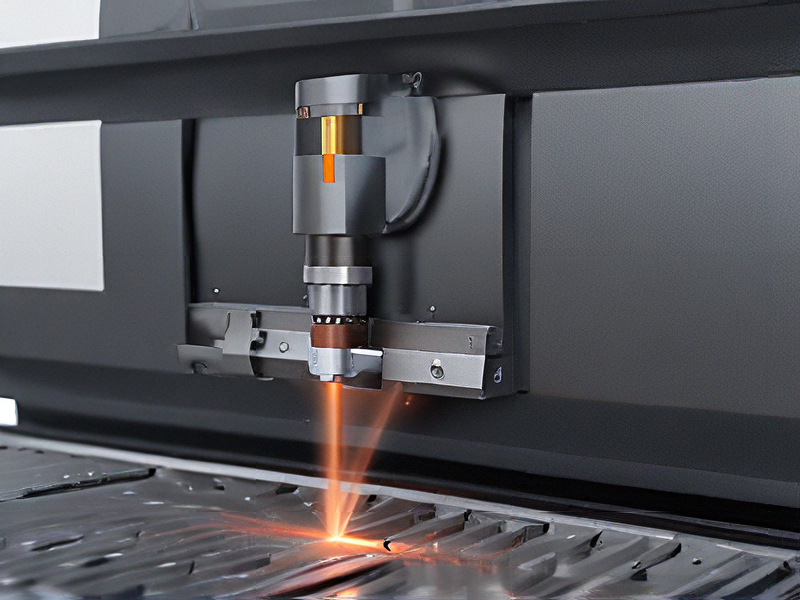
Quality Testing Methods for laser co2 cutting machine and how to control quality
Quality testing for a CO2 laser cutting machine involves several key methods to ensure precision, reliability, and performance:
1. Cut Quality Assessment:
– Visual Inspection: Evaluate the edges of cuts for smoothness, dross (residual material), and kerf width (cut width).
– Microscopic Analysis: Use microscopes to inspect the cut surface for any micro-cracks or heat-affected zones.
2. Dimensional Accuracy:
– Calipers and Micrometers: Measure the dimensions of cut parts to ensure they meet specified tolerances.
– Coordinate Measuring Machine (CMM): For complex shapes, use a CMM to verify all dimensions and geometric tolerances.
3. Material Consistency:
– Material Identification: Ensure the material being cut matches specifications using material identification tools (e.g., XRF analyzers).
– Thickness Verification: Measure material thickness before cutting to ensure consistency.
4. Laser Performance Testing:
– Power and Stability: Regularly test the laser output power and stability using a laser power meter.
– Beam Alignment and Focus: Check the alignment and focus of the laser beam to ensure consistent cutting quality.
5. Process Parameter Optimization:
– Cut Trials: Perform test cuts on sample materials to optimize parameters such as speed, power, and gas flow.
– Edge Quality Testing: Adjust parameters to minimize defects and achieve the desired edge quality.
Quality Control Methods:
1. Standard Operating Procedures (SOPs):
– Develop and follow SOPs for machine setup, operation, and maintenance to ensure consistent quality.
2. Regular Maintenance:
– Schedule and perform regular maintenance on the laser cutter to prevent malfunctions and ensure optimal performance.
3. Training and Certification:
– Ensure operators are properly trained and certified in the use of the CO2 laser cutter.
4. Statistical Process Control (SPC):
– Implement SPC to monitor and control the cutting process. Use control charts to track key variables and identify any deviations from the standard.
5. Inspection and Testing Protocols:
– Establish rigorous inspection and testing protocols for all cut parts, including first article inspection (FAI) and routine sampling.
By integrating these methods and controls, the quality of cuts produced by a CO2 laser cutting machine can be consistently monitored and maintained.
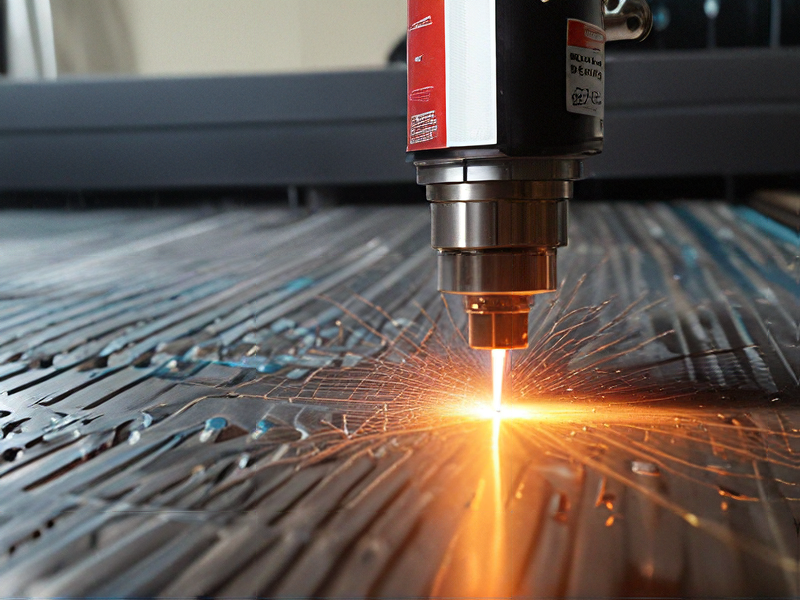
Tips for Procurement and Considerations when Purchasing from laser co2 cutting machine
When procuring a CO2 laser cutting machine, several key factors and tips can help ensure a successful purchase:
1. Understand Your Requirements:
– Material Compatibility: Ensure the machine can handle the materials you intend to cut, such as wood, acrylic, leather, or metals.
– Cutting Thickness: Verify the maximum thickness the laser can cut for each material.
2. Evaluate Technical Specifications:
– Laser Power: Higher wattage lasers can cut through thicker materials but may be more expensive.
– Cutting Speed and Precision: Balance speed with precision to meet your production needs efficiently.
– Bed Size: Match the bed size to the dimensions of the materials you’ll be working with.
3. Quality and Reliability:
– Brand Reputation: Research the manufacturer’s reputation for quality and reliability.
– Machine Build: Look for a sturdy frame and high-quality components that can withstand heavy use.
4. Cost Considerations:
– Initial Purchase Price: Include the cost of the machine and any necessary accessories.
– Operating Costs: Consider power consumption, maintenance, and consumables (like laser tubes and lenses).
5. Support and Service:
– Warranty: Ensure the machine comes with a comprehensive warranty.
– Technical Support: Check the availability and quality of technical support, including remote support and on-site service.
– Training: Look for suppliers that offer training to help you get the most out of your machine.
6. Software Compatibility:
– Control Software: Ensure the machine’s software is user-friendly and compatible with your existing design tools.
– Updates and Upgrades: Check for software update policies and potential upgrade paths.
7. Safety Features:
– Safety Interlocks: Ensure the machine has safety interlocks to prevent accidents.
– Ventilation and Fume Extraction: Proper ventilation is essential to remove harmful fumes produced during cutting.
By carefully considering these factors, you can choose a CO2 laser cutting machine that meets your operational needs, ensuring efficiency and reliability in your production processes.
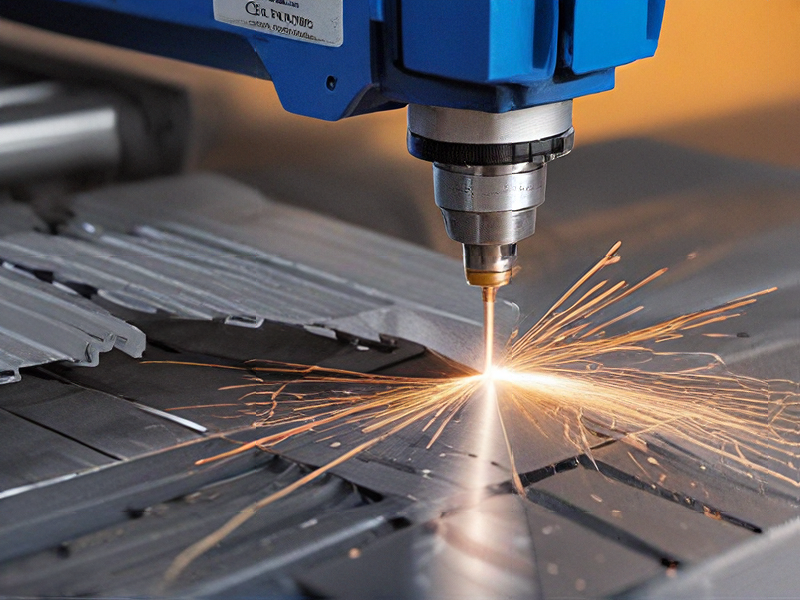
FAQs on Sourcing and Manufacturing from laser co2 cutting machine in China
FAQs on Sourcing and Manufacturing from Laser CO2 Cutting Machine in China
1. Why source laser CO2 cutting machines from China?
– Cost-Effective: China offers competitive prices due to lower manufacturing costs.
– Advanced Technology: Many Chinese manufacturers provide cutting-edge technology and customizable options.
– High Production Capacity: Chinese factories can handle large orders efficiently.
2. How do I find reliable manufacturers?
– Online Platforms: Websites like Alibaba and Made-in-China list numerous suppliers with reviews and ratings.
– Trade Shows: Attending exhibitions such as the Canton Fair allows direct interaction with manufacturers.
– Third-Party Agencies: Hiring sourcing agents can help identify and vet potential suppliers.
3. What should I look for in a manufacturer?
– Experience: Check the manufacturer’s history and expertise in laser CO2 technology.
– Certifications: Ensure they have necessary certifications like ISO9001, CE, and FDA.
– Customer Feedback: Look for testimonials or reviews from previous clients.
4. How can I ensure product quality?
– Quality Control: Insist on quality checks at various stages of production.
– Prototypes: Request samples or prototypes before finalizing the order.
– Third-Party Inspections: Hire independent inspection services to verify quality before shipment.
5. What about shipping and logistics?
– Shipping Terms: Discuss Incoterms (FOB, CIF) to clarify shipping responsibilities.
– Customs Clearance: Ensure your supplier assists with customs documentation.
– Lead Time: Confirm production and delivery timelines to avoid delays.
6. Are there any risks involved?
– Intellectual Property: Protect your designs and technology with patents or trademarks.
– Communication Barriers: Language and cultural differences can lead to misunderstandings; use clear, written agreements.
– Payment Risks: Use secure payment methods like letters of credit or escrow services.
By addressing these key points, you can streamline the process of sourcing and manufacturing laser CO2 cutting machines from China, ensuring quality and reliability.
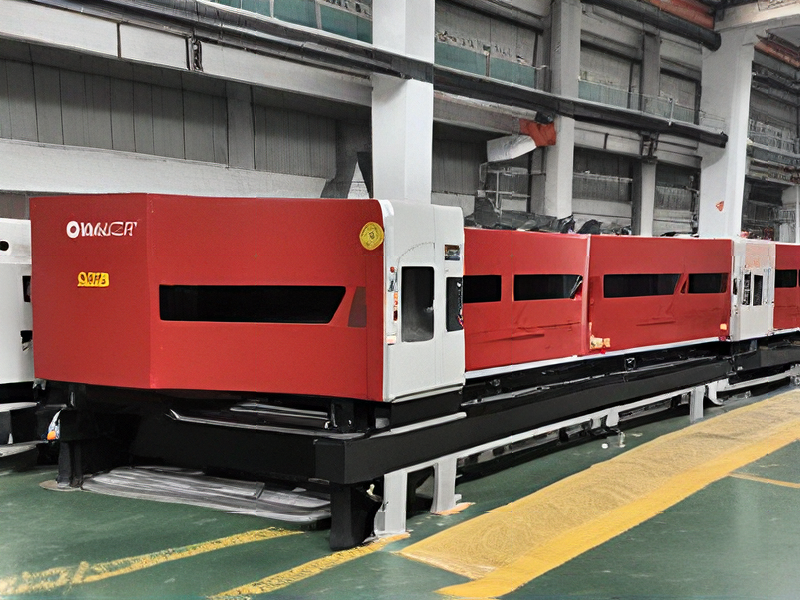