Technology and Applications of metals alloys
Metal alloys, combinations of two or more metals or a metal with another element, are fundamental in modern technology due to their enhanced properties compared to pure metals. These materials exhibit improved strength, durability, corrosion resistance, and versatility, making them indispensable across various industries.
Technology of Metal Alloys:
1. Production Techniques:
– Casting: Molten alloys are poured into molds to form desired shapes.
– Forging: Alloys are shaped under high pressure, enhancing their mechanical properties.
– Additive Manufacturing (3D Printing): Complex alloy structures are created layer by layer, allowing for customized and lightweight designs.
2. Heat Treatment:
– Annealing: Alloys are heated and then slowly cooled to improve ductility.
– Quenching and Tempering: Rapid cooling followed by reheating adjusts hardness and toughness.
Applications of Metal Alloys:
1. Construction:
– Steel (iron and carbon): Essential for buildings, bridges, and infrastructure due to its high strength and flexibility.
– Aluminum Alloys: Used in construction for their light weight and resistance to corrosion.
2. Automotive and Aerospace:
– Titanium Alloys: Offer high strength-to-weight ratios, critical for aircraft and spacecraft components.
– Magnesium Alloys: Used in car parts to reduce weight and improve fuel efficiency.
3. Electronics:
– Copper Alloys: Utilized in electrical wiring and components for their excellent conductivity.
– Solder (tin and lead alloys): Essential for joining electronic components.
4. Medical:
– Stainless Steel and Titanium Alloys: Used in implants and surgical instruments due to their biocompatibility and resistance to corrosion.
5. Energy Sector:
– Nickel Alloys: Crucial for gas turbines and nuclear reactors due to their ability to withstand high temperatures and corrosive environments.
Metal alloys continue to evolve, driven by technological advancements and the demand for materials with superior performance in specialized applications. Their development and utilization remain pivotal in shaping the future of various industries.
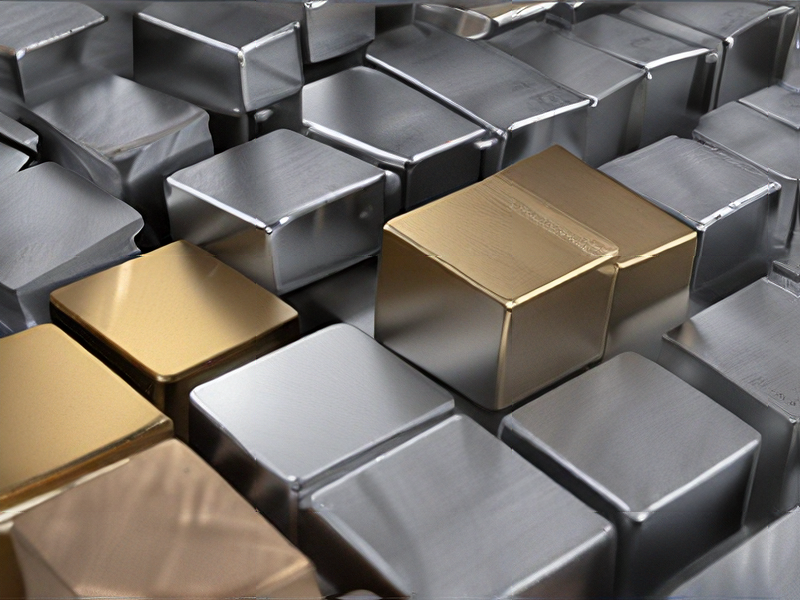
Quality Testing Methods for metals alloys and how to control quality
Quality testing methods for metal alloys typically include a combination of destructive and non-destructive techniques. Destructive testing involves methods like tensile testing, where a sample is pulled to determine its strength and ductility. Hardness testing measures a material’s resistance to indentation, often using methods like Brinell, Rockwell, or Vickers scales. Additionally, impact testing assesses a material’s toughness by subjecting it to sudden force.
Non-destructive testing methods include ultrasonic testing to detect internal flaws, magnetic particle inspection for surface and subsurface defects, and radiographic testing using X-rays or gamma rays to reveal internal structures. Visual inspection is crucial throughout the manufacturing process to detect surface imperfections.
Quality control in metal alloy production involves stringent process monitoring and adherence to specifications. Key aspects include raw material inspection, precise alloying, controlled heat treatment, and thorough testing at various production stages. Statistical process control (SPC) helps in monitoring parameters like composition, dimensions, and mechanical properties to ensure consistency and reliability.
Documentation and traceability of materials and processes are essential for quality assurance. Continuous improvement through feedback loops from testing results and customer feedback ensures ongoing quality enhancement. Adherence to international standards like ASTM, ISO, or ASME further guarantees product reliability and compatibility with industry requirements.
In conclusion, effective quality testing and control in metal alloy production rely on a comprehensive approach integrating both destructive and non-destructive methods, rigorous process monitoring, adherence to standards, and continuous improvement practices.
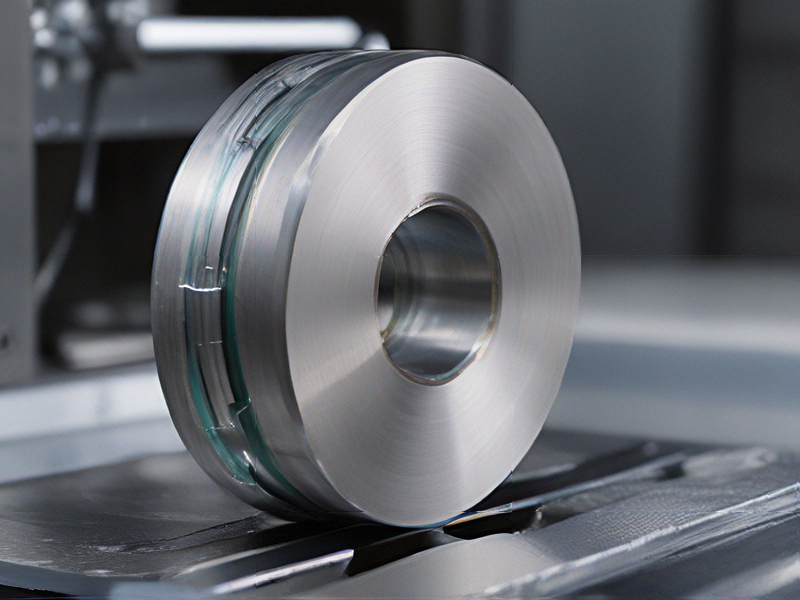
Tips for Procurement and Considerations when Purchasing from metals alloys
When procuring metals and alloys, several considerations are crucial to ensure quality, cost-effectiveness, and reliability:
1. Material Specifications: Clearly define the required specifications such as type of metal/alloy, grade (e.g., stainless steel 316), dimensions, and any specific performance requirements (e.g., tensile strength, corrosion resistance).
2. Supplier Selection: Choose reputable suppliers with a proven track record in delivering quality materials. Consider their certifications (ISO, ASME, etc.), industry reputation, and ability to meet delivery schedules.
3. Quality Assurance: Implement stringent quality checks and inspections. Request material certificates, test reports (e.g., chemical composition, mechanical properties), and ensure compliance with relevant standards (ASTM, EN, etc.).
4. Cost and Value: Balance cost considerations with material quality. Evaluate total cost of ownership, including maintenance and lifecycle costs, rather than opting solely for the lowest price.
5. Supply Chain Reliability: Assess suppliers’ supply chain resilience, especially regarding raw material sourcing and potential disruptions (e.g., geopolitical factors, market fluctuations).
6. Environmental and Regulatory Compliance: Ensure suppliers adhere to environmental standards and regulatory requirements (RoHS, REACH, etc.) to mitigate risks associated with non-compliance.
7. Packaging and Transportation: Evaluate packaging methods to prevent material damage during transportation and storage. Consider logistics efficiency and environmental impact.
8. Long-term Relationships: Foster partnerships with suppliers who demonstrate commitment to customer service, responsiveness to inquiries, and willingness to collaborate on continuous improvement initiatives.
By carefully considering these factors, procurement professionals can mitigate risks, optimize costs, and ensure the reliability of metals and alloys procured for various industrial applications.
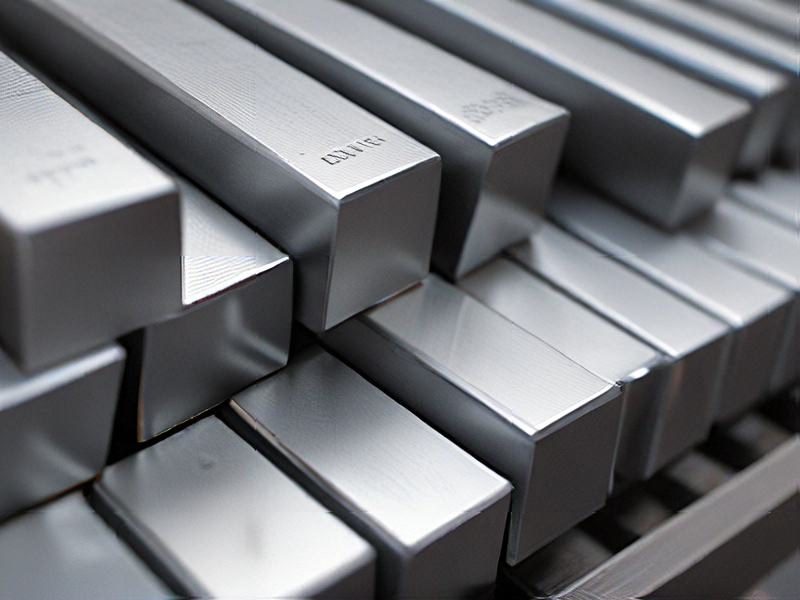
FAQs on Sourcing and Manufacturing from metals alloys in China
FAQs on Sourcing and Manufacturing from Metal Alloys in China
1. Why source metal alloys from China?
China offers competitive pricing, a vast selection of materials, advanced manufacturing technologies, and an extensive supply chain network. These factors contribute to reduced production costs and faster turnaround times.
2. What types of metal alloys are commonly sourced from China?
Common metal alloys include stainless steel, aluminum, copper, titanium, and various specialty alloys such as Inconel and Monel. These are used in industries ranging from automotive to aerospace.
3. How can I ensure the quality of metal alloys from Chinese suppliers?
Quality assurance can be managed by:
– Choosing reputable suppliers with certifications such as ISO 9001.
– Requesting material test reports (MTRs).
– Conducting third-party inspections and audits.
– Implementing rigorous supplier vetting processes.
4. What are the typical lead times for manufacturing metal alloys in China?
Lead times vary based on the complexity and quantity of the order but typically range from 4 to 12 weeks, including production and shipping.
5. How do I handle logistics and shipping for metal alloys from China?
Engage with reliable freight forwarders and logistics partners experienced in handling metal goods. Consider factors like shipping methods, customs clearance, and tariffs.
6. Are there any risks associated with sourcing metal alloys from China?
Potential risks include quality control issues, intellectual property concerns, and geopolitical factors. Mitigation strategies involve detailed contracts, IP protection measures, and maintaining diversified supply chains.
7. How can I ensure compliance with international standards?
Ensure your supplier adheres to international standards such as ASTM, ANSI, DIN, and JIS. Regular audits and third-party certifications can help maintain compliance.
8. What are the payment terms typically like?
Payment terms can vary but often include options like Letter of Credit (LC), Telegraphic Transfer (TT), and sometimes payment upon delivery, depending on the relationship with the supplier.
9. How do I find reliable metal alloy suppliers in China?
Use platforms like Alibaba, Global Sources, and Made-in-China. Attend trade shows such as the Canton Fair, and seek referrals from industry contacts.
By understanding these key aspects, businesses can effectively manage their sourcing and manufacturing operations in China, leveraging its strengths while mitigating potential risks.
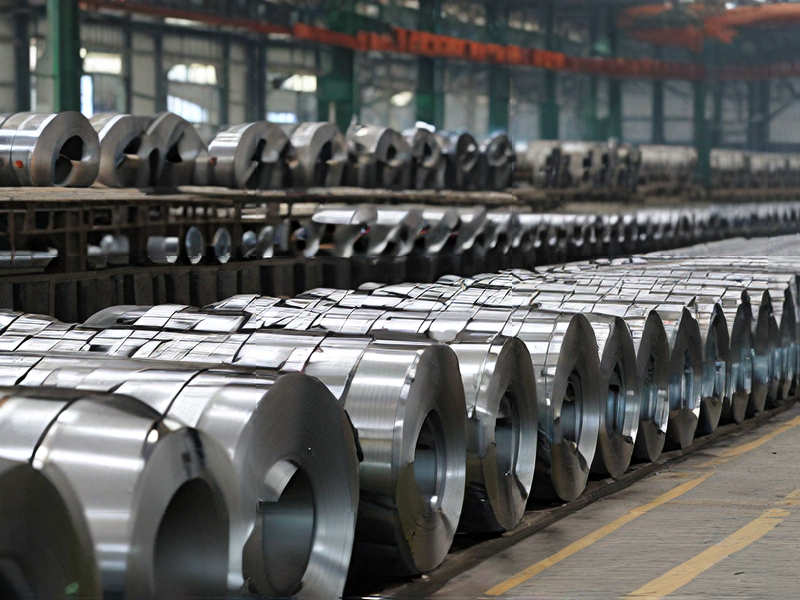