Technology and Applications of toughest metal in the world
The toughest metal in the world is tungsten, known for its remarkable properties. With the highest tensile strength of any natural metal, tungsten is incredibly resistant to heat, wear, and corrosion. Its melting point is the highest among all metals, at 3,422°C (6,192°F).
Technology and Applications:
1. Aerospace and Military:
– Tungsten’s heat resistance makes it ideal for aerospace applications, including rocket engine nozzles and high-temperature shielding.
– Military uses include armor-piercing ammunition and kinetic energy penetrators due to its density and hardness.
2. Electronics:
– Tungsten is essential in electronics for its use in integrated circuits, electrical contacts, and X-ray tubes.
– Its stability at high temperatures ensures reliable performance in extreme conditions.
3. Lighting and Filament:
– Tungsten’s high melting point makes it perfect for light bulb filaments and vacuum tube filaments.
– It emits a bright white light when heated, improving the efficiency and lifespan of lighting solutions.
4. Manufacturing and Industrial Applications:
– Tungsten carbide, a compound of tungsten and carbon, is used extensively in cutting tools, drilling equipment, and abrasives.
– Its durability ensures longer tool life and efficiency in industrial machining and mining operations.
5. Medical Applications:
– Tungsten’s radiopacity and biocompatibility make it suitable for medical imaging and radiation shielding.
– It is also used in cancer treatments through radiation therapy, providing precise targeting of tumors.
6. Jewelry and Fashion:
– Tungsten’s scratch resistance and luster have led to its use in jewelry, particularly in rings and watches.
– It offers a durable, attractive alternative to traditional metals.
Tungsten’s unique properties ensure its continued importance across various high-tech and industrial fields, driving advancements and efficiencies.
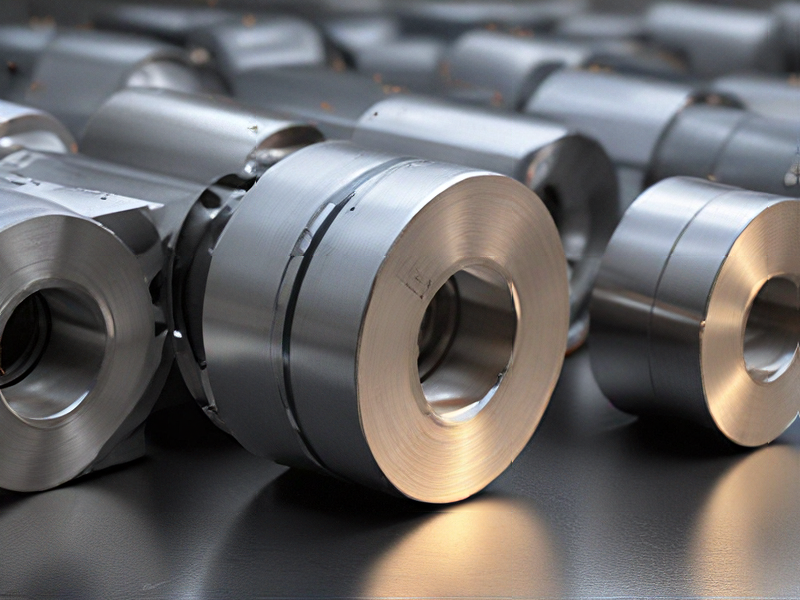
Quality Testing Methods for toughest metal in the world and how to control quality
Quality testing methods for the toughest metals typically involve rigorous mechanical and chemical analyses to ensure strength, durability, and reliability. Here are key methods and quality control measures:
1. Tensile Testing: Determines the maximum stress a material can withstand while being stretched or pulled. This helps assess its ultimate tensile strength and yield strength.
2. Hardness Testing: Measures the resistance of a material to indentation or scratching. Common methods include Rockwell, Brinell, and Vickers hardness tests.
3. Impact Testing: Evaluates the ability of a material to absorb energy during fracture, important for assessing toughness and resilience.
4. Microstructure Analysis: Involves examining the metal’s internal structure under a microscope to check for defects, grain size, and phase distribution.
5. Chemical Composition Analysis: Verifies the elemental composition of the metal, ensuring it meets specifications and standards.
6. Non-Destructive Testing (NDT): Techniques such as ultrasonic testing, radiography, and magnetic particle inspection detect internal defects without damaging the metal.
To control quality effectively:
– Establish Specifications: Define clear quality standards and performance criteria based on application requirements.
– Process Control: Monitor manufacturing processes closely to ensure consistency and adherence to specifications.
– Quality Assurance Testing: Implement regular testing throughout production to identify deviations early and take corrective actions.
– Supplier Quality Management: Ensure suppliers meet quality standards for raw materials and components.
– Continuous Improvement: Use feedback from testing and production data to refine processes and enhance product quality over time.
By employing these methods and controls, manufacturers can ensure that the toughest metals meet stringent quality standards and perform reliably in demanding applications.
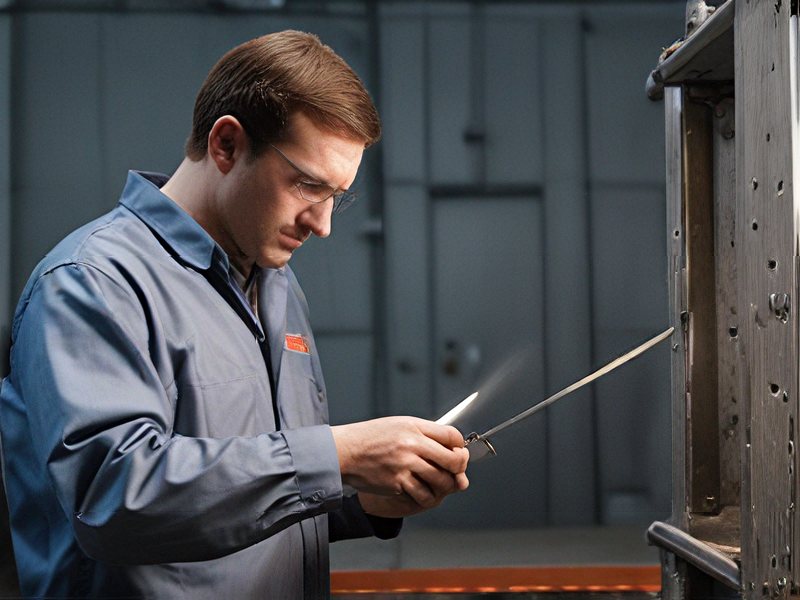
Tips for Procurement and Considerations when Purchasing from toughest metal in the world
When procuring and purchasing items made from the world’s toughest metals, several critical tips and considerations can ensure optimal performance and value.
Tips for Procurement
1. Define Requirements:
Clearly specify the performance requirements, such as hardness, tensile strength, and corrosion resistance, tailored to your application’s needs.
2. Supplier Research:
Identify and evaluate suppliers with proven expertise in dealing with tough metals like tungsten, titanium alloys, or certain high-strength steels. Check their certifications, reputation, and customer feedback.
3. Quality Assurance:
Ensure the supplier has stringent quality control processes. Look for ISO certifications and request material testing reports and certifications to verify metal properties.
4. Technical Support:
Choose suppliers offering robust technical support. Expert advice on metal selection, machining, and application can be invaluable.
5. Cost Analysis:
Consider the total cost of ownership, not just the purchase price. Tough metals can have higher upfront costs but may offer longer lifespans and reduced maintenance costs.
Considerations
1. Material Properties:
Understand the specific properties of the metal. For instance, tungsten is extremely hard and dense, making it ideal for high-wear applications but challenging to machine.
2. Machinability:
Assess the machinability of the metal. Some tough metals can be difficult to machine and may require specialized equipment and techniques, impacting manufacturing costs and lead times.
3. Application Environment:
Consider the operating environment. Metals like titanium offer excellent corrosion resistance, making them suitable for harsh environments, including marine and chemical processing applications.
4. Supplier Reliability:
Ensure the supplier can consistently meet your quantity and delivery time requirements. Evaluate their production capacity and supply chain stability.
5. Regulatory Compliance:
Verify that the material and supplier comply with relevant industry standards and regulations, ensuring safety and performance.
By meticulously planning and considering these factors, you can effectively procure the toughest metals, ensuring they meet your project’s demands and provide long-term value.
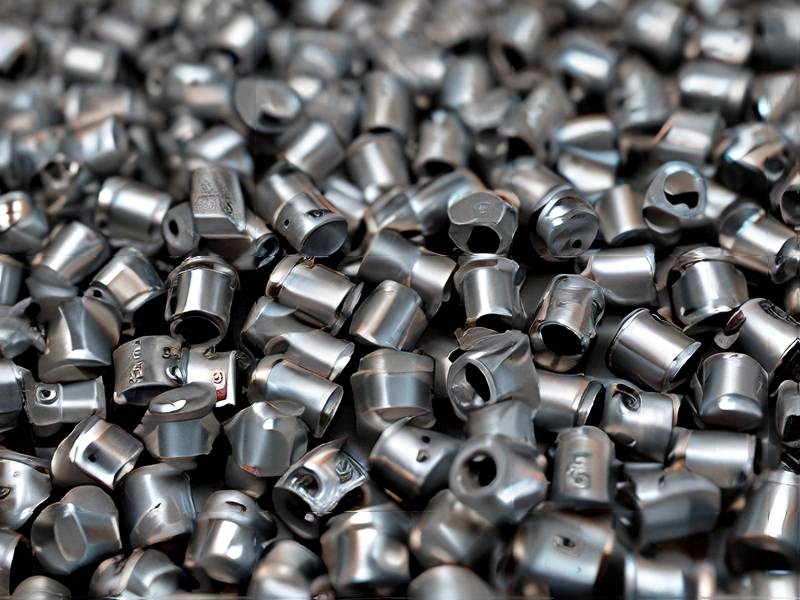
FAQs on Sourcing and Manufacturing from toughest metal in the world in China
FAQs on Sourcing and Manufacturing from the Toughest Metal in the World in China
1. What is the toughest metal in the world?
The toughest metal in the world is tungsten. It has the highest tensile strength and the highest melting point of all metals, making it extremely durable and resistant to heat and wear.
2. Why source tungsten from China?
China is the world’s largest producer of tungsten, accounting for over 80% of global production. The country offers competitive pricing, advanced manufacturing capabilities, and a well-established supply chain.
3. How to find reliable suppliers in China?
Utilize platforms like Alibaba, Made-in-China, and Global Sources to identify potential suppliers. Verify their credentials, request samples, and consider conducting on-site visits or audits to ensure quality and reliability.
4. What are the key considerations for manufacturing with tungsten?
Tungsten is challenging to machine due to its hardness and brittleness. Advanced techniques like powder metallurgy and specialized machining processes are required. Ensure your manufacturer has the necessary expertise and equipment.
5. Are there any regulatory concerns when importing tungsten products?
Yes, ensure compliance with international trade regulations and standards, such as REACH, RoHS, and ISO certifications. Verify that your supplier adheres to environmental and safety regulations.
6. How can I ensure the quality of tungsten products?
Implement rigorous quality control measures, including material testing, certification verification, and regular inspections. Third-party quality assurance services can provide additional verification.
7. What are the cost factors to consider?
Costs include raw material prices, manufacturing processes, transportation, tariffs, and any additional quality assurance measures. Negotiating long-term contracts can help stabilize costs.
8. What is the typical lead time for tungsten products from China?
Lead times vary depending on the complexity of the product and order size, typically ranging from a few weeks to several months. Clear communication and planning with your supplier can help manage timelines.
9. Can tungsten be customized for specific applications?
Yes, tungsten can be alloyed with other metals and fabricated into various shapes and sizes to meet specific industrial requirements. Work closely with your supplier to achieve the desired specifications.
By addressing these key questions, businesses can effectively navigate the complexities of sourcing and manufacturing tungsten in China.
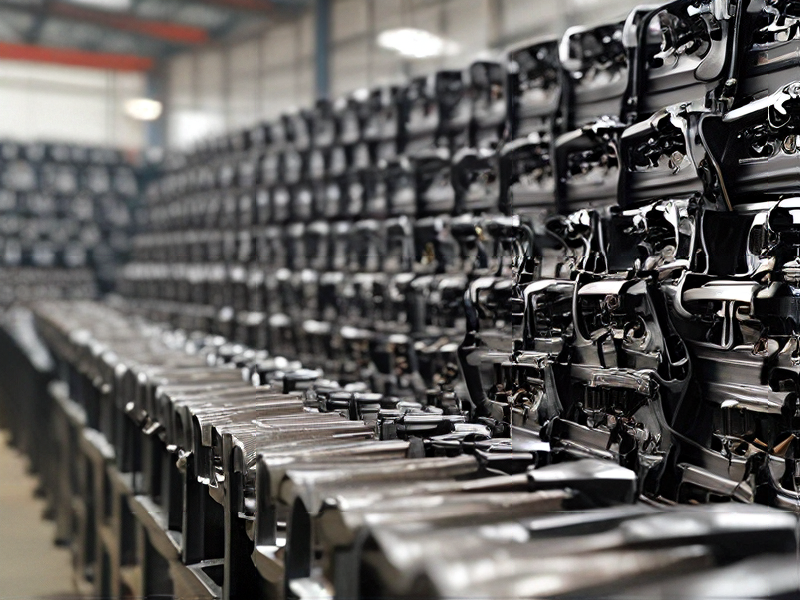