Technology and Applications of hot rolled steel vs cold formed
Hot rolled steel and cold formed steel are essential materials in construction and manufacturing, each with distinct technologies and applications.
Hot Rolled Steel
Technology: Hot rolled steel is produced by rolling steel at high temperatures, typically over 1,700°F, which is above steel’s recrystallization temperature. This process allows the steel to be easily shaped and formed. The high temperatures lead to a rougher surface finish and less precise dimensions compared to cold-formed steel.
Applications: Hot rolled steel is widely used in construction, such as in I-beams, channels, and other structural components due to its strength and durability. It’s also used in manufacturing heavy machinery, railroad tracks, and automotive frames.
Cold Formed Steel
Technology: Cold formed steel, also known as cold-rolled steel, is produced by rolling steel at room temperature. This method increases the steel’s strength through strain hardening and allows for more precise dimensions and a smoother finish. The process involves passing the steel through rollers to achieve the desired thickness and shape.
Applications: Cold formed steel is commonly used in applications requiring precision and surface quality, such as in the production of appliances, furniture, and automotive parts. It’s also utilized in the construction industry for light steel framing, purlins, and metal studs due to its high strength-to-weight ratio and dimensional accuracy.
Comparison
– Strength and Precision: Cold formed steel generally has higher strength and precision due to the strain hardening and controlled rolling process.
– Surface Finish: Cold formed steel has a smoother finish and more accurate dimensions, making it suitable for aesthetic and precision-required applications.
– Cost and Production: Hot rolled steel is typically less expensive to produce and is suited for larger structural components where precision is less critical.
In summary, hot rolled steel is preferred for large structural applications requiring durability, while cold formed steel is ideal for products requiring high strength, precision, and a smooth finish.
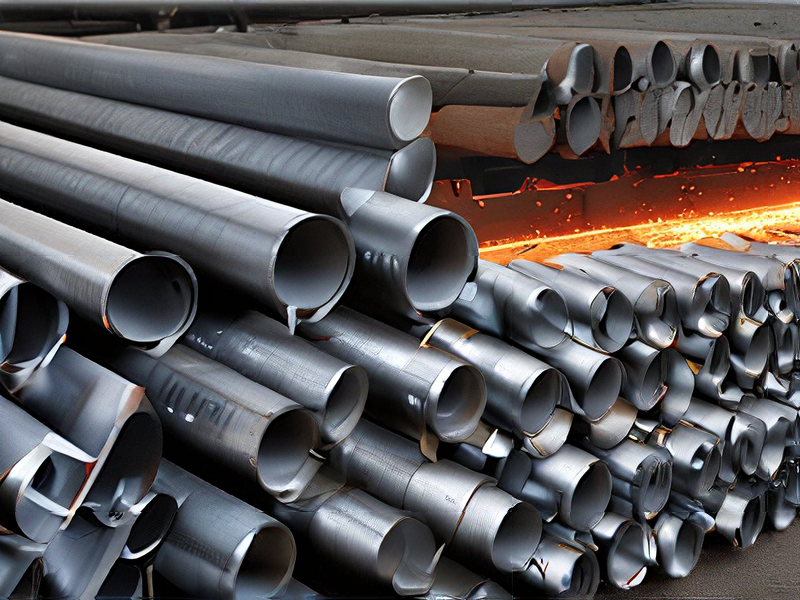
Quality Testing Methods for hot rolled steel vs cold formed and how to control quality
Quality testing methods for hot rolled steel and cold formed steel differ due to their distinct manufacturing processes and resultant properties.
For hot rolled steel, common quality control methods include:
1. Dimensional Inspection: Ensuring thickness, width, and length comply with specifications.
2. Surface Inspection: Checking for defects like scale, scratches, or surface discontinuities.
3. Mechanical Testing: Evaluating tensile strength, yield strength, elongation, and hardness.
4. Microstructural Analysis: Examining grain size and distribution to verify consistency.
5. Chemical Analysis: Verifying composition to meet required standards.
Cold formed steel undergoes different quality control measures, including:
1. Dimensional Accuracy: Ensuring profiles meet specified tolerances.
2. Surface Condition: Checking for cracks, folds, or surface defects.
3. Geometry Inspection: Verifying angles, straightness, and overall shape.
4. Mechanical Properties: Testing for strength, ductility, and toughness.
5. Weld Quality: Assessing weld integrity and adherence to specifications.
Quality control for both types involves:
– Process Monitoring: Regular checks during manufacturing to detect deviations early.
– Certification and Standards Compliance: Ensuring products meet industry standards (e.g., ASTM, EN).
– Traceability: Tracking materials from source to finished product to identify and address issues.
– Continuous Improvement: Using feedback to refine processes and enhance product quality.
Implementing these methods ensures that both hot rolled and cold formed steel meet stringent quality requirements, delivering reliable and consistent performance in various applications.
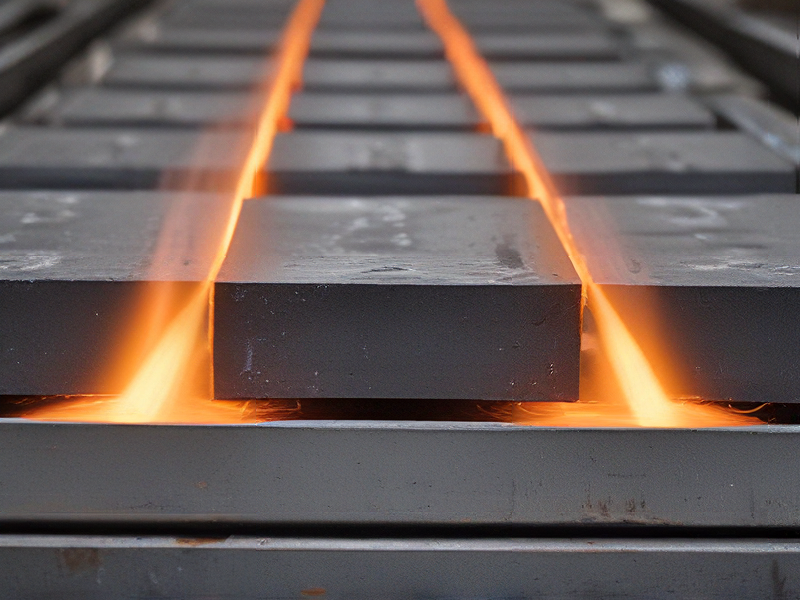
Tips for Procurement and Considerations when Purchasing from hot rolled steel vs cold formed
When deciding between hot rolled steel (HRS) and cold formed steel (CFS) for procurement, several factors should be considered:
1. Manufacturing Process and Properties:
– Hot Rolled Steel (HRS): Produced at high temperatures, resulting in a rough surface finish. HRS tends to be less precise in dimensions but is strong and ductile, suitable for structural applications like beams and columns.
– Cold Formed Steel (CFS): Formed at room temperature with precise dimensions and a smooth finish. CFS is stronger in terms of yield strength but less ductile than HRS. It’s ideal for applications requiring high strength-to-weight ratios, such as studs and joists.
2. Cost and Availability:
– Hot Rolled Steel: Generally cheaper due to less processing involved, readily available in a wide range of sizes and shapes.
– Cold Formed Steel: May be more expensive per ton due to higher processing costs, but savings can be achieved in transportation and installation due to lighter weight and dimensional accuracy.
3. Strength and Application Suitability:
– Hot Rolled Steel: Higher toughness and ductility make it suitable for heavy-duty applications like structural supports in buildings, bridges, and machinery.
– Cold Formed Steel: Offers higher yield strength and is lighter, making it advantageous for applications where weight reduction is critical, such as in automotive and aerospace industries.
4. Surface Finish and Aesthetics:
– Hot Rolled Steel: Characterized by a scaled surface finish due to the manufacturing process, which may or may not be desirable depending on the application.
– Cold Formed Steel: Has a smoother and more consistent surface finish, suitable for applications where aesthetics are important, such as architectural elements.
5. Environmental Impact:
– Both HRS and CFS can be recycled, but the energy-intensive nature of HRS production makes CFS potentially more environmentally friendly due to its lower energy consumption during manufacturing.
In summary, when choosing between hot rolled steel and cold formed steel, consider factors such as strength requirements, dimensional accuracy, cost-effectiveness, and the specific application’s needs. Each type has distinct advantages depending on the project’s scope, budget, and performance criteria.
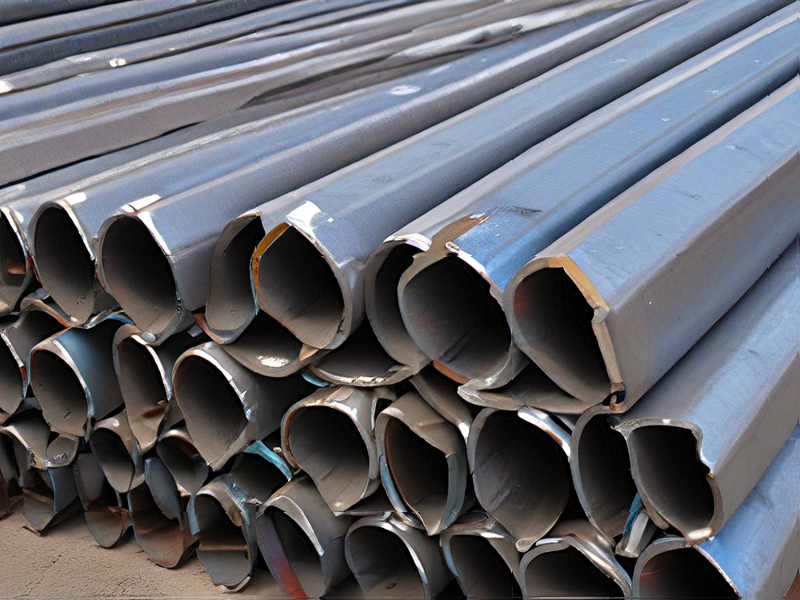
FAQs on Sourcing and Manufacturing from hot rolled steel vs cold formed in China
FAQs on Sourcing and Manufacturing from Hot Rolled Steel vs Cold Formed in China
1. What is the difference between hot rolled and cold formed steel?
– Hot Rolled Steel: Formed at high temperatures, it’s easier to shape and is typically used for structural components due to its durability.
– Cold Formed Steel: Shaped at room temperature, it offers a smooth finish and higher strength-to-weight ratio, making it suitable for precision applications.
2. What are the advantages of hot rolled steel?
– Cost-Effective: Generally cheaper due to the simpler manufacturing process.
– Versatile: Ideal for large structures where precision isn’t as critical.
– Durable: Suitable for heavy-duty applications and construction.
3. What are the benefits of cold formed steel?
– High Precision: Offers a superior surface finish and tighter tolerances.
– Increased Strength: Higher strength due to strain hardening.
– Lightweight: Ideal for lightweight structures and detailed work.
4. How does the choice of steel affect manufacturing costs in China?
– Hot Rolled Steel: Lower initial costs but may require more machining and finishing.
– Cold Formed Steel: Higher initial cost but less machining, leading to potential savings in the long run.
5. What are the common applications of hot rolled and cold formed steel?
– Hot Rolled Steel: Beams, railroad tracks, and frames for heavy equipment.
– Cold Formed Steel: Automotive parts, home appliances, and precision components.
6. How is the supply chain for steel in China?
– Abundant Supply: China has a vast network of steel manufacturers, ensuring a steady supply.
– Cost Efficiency: Competitive pricing due to large-scale production and low labor costs.
– Quality Standards: Many Chinese manufacturers adhere to international standards, but it’s crucial to verify certifications.
7. What should I consider when sourcing steel from China?
– Quality Control: Ensure the supplier meets international standards.
– Logistics: Consider shipping costs and lead times.
– Supplier Reliability: Verify the reputation and reliability of the supplier through references and audits.
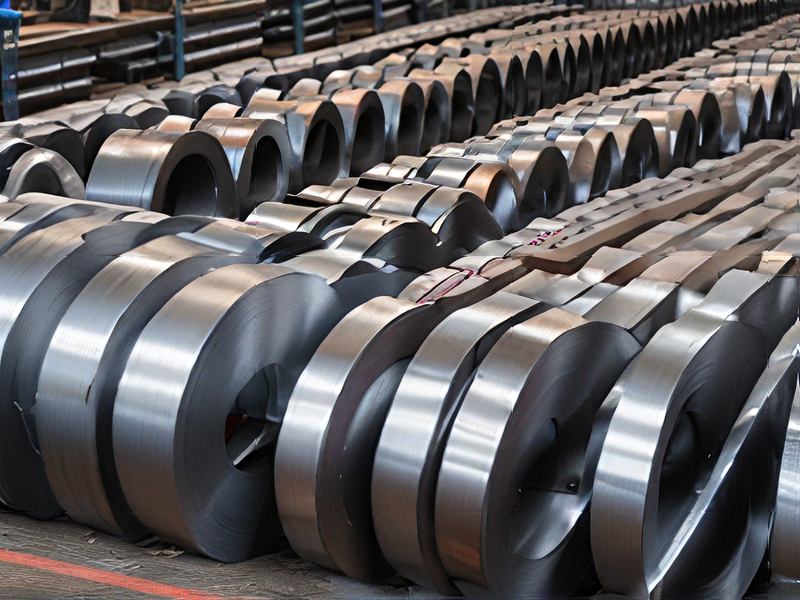