Technology and Applications of machine broaching
Technology and Applications of Machine Broaching
Technology:
Machine broaching is a precision machining process that removes material using a broach, a multi-toothed cutting tool. The broach’s teeth progressively increase in size, making shallow cuts that produce a smooth finish. This method can be categorized into two main types: linear and rotary broaching. Linear broaching involves moving the broach linearly against the workpiece, while rotary broaching rotates the broach as it cuts into the material. The process is highly automated and uses hydraulic or mechanical presses to drive the broach.
Applications:
Machine broaching is utilized in various industries for creating precise and complex shapes. Key applications include:
1. Automotive Industry: Broaching is used to produce engine components such as gears, splines, and transmission parts. It ensures high accuracy and consistency, which are crucial for the performance of automotive parts.
2. Aerospace Industry: The process is employed to manufacture high-precision components like turbine disks and landing gear parts. The ability to create intricate shapes with tight tolerances makes broaching ideal for aerospace applications.
3. Tool and Die Making: Broaching is used to create molds and dies with complex geometries. This application benefits from the process’s capability to produce accurate and repeatable shapes.
4. Manufacturing of Fasteners: Broaching produces various types of fasteners, such as bolts and screws, by cutting precise internal and external profiles.
5. Medical Device Manufacturing: Components for medical devices, such as surgical instruments and orthopedic implants, are often produced using broaching due to its precision and ability to handle small, detailed parts.
In conclusion, machine broaching is a versatile and precise machining process essential in producing high-quality, intricate components across multiple industries. Its ability to maintain tight tolerances and high repeatability makes it invaluable for applications requiring precision engineering.
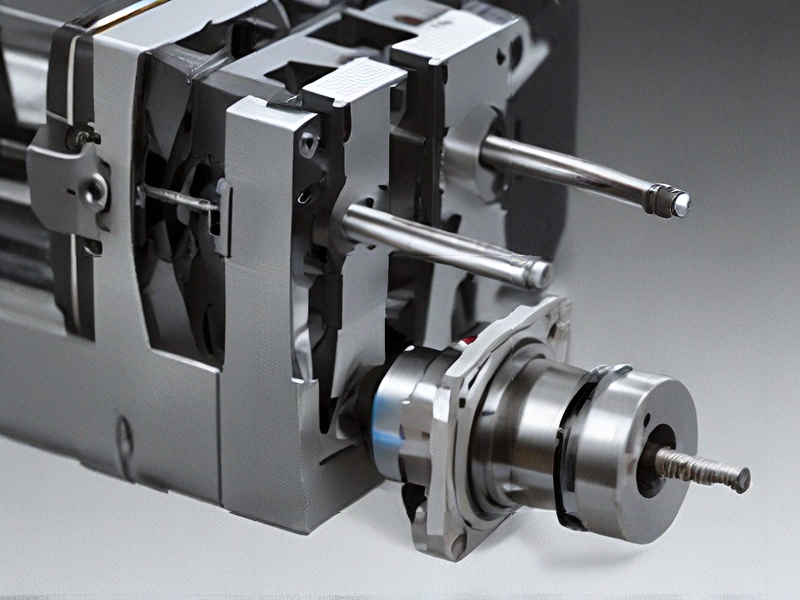
Quality Testing Methods for machine broaching and how to control quality
Quality testing methods for machine broaching ensure that the machined parts meet specified standards and are free of defects. Key methods and controls include:
1. Visual Inspection: Initial assessment to identify obvious defects such as surface roughness, burrs, or misalignments. This is often done using magnifying tools or microscopes.
2. Dimensional Inspection: Using precision measuring instruments such as calipers, micrometers, and coordinate measuring machines (CMM) to verify the dimensions of the broached parts against design specifications.
3. Surface Finish Measurement: Employing surface roughness testers to measure the texture of the machined surface. A profilometer can be used to ensure the surface finish is within the required Ra value.
4. Hardness Testing: Determining the hardness of the material to ensure it meets the specified range. Techniques like Rockwell, Vickers, or Brinell hardness tests are common.
5. Non-Destructive Testing (NDT): Methods such as ultrasonic testing, magnetic particle inspection, or dye penetrant inspection to detect subsurface defects without damaging the part.
6. Process Control: Implementing Statistical Process Control (SPC) to monitor the broaching process in real-time. Key parameters like tool wear, cutting speed, and feed rate are controlled to maintain consistent quality.
7. Tool Inspection and Maintenance: Regular inspection of broaching tools for wear and tear, ensuring they are sharp and in good condition. Replacing or reconditioning tools as necessary to maintain quality.
8. Material Testing: Ensuring the raw material used is of high quality and meets the required specifications through chemical and mechanical testing.
Quality Control Measures
– Standard Operating Procedures (SOPs): Establishing and following SOPs for each step of the broaching process.
– Training: Regular training for operators to ensure they understand quality requirements and best practices.
– Documentation and Traceability: Keeping detailed records of inspections and tests to trace any defects back to their source.
– Corrective Actions: Implementing a robust system to address any defects or non-conformities found during inspections.
By combining these methods and controls, the quality of machine broaching can be effectively managed and ensured.
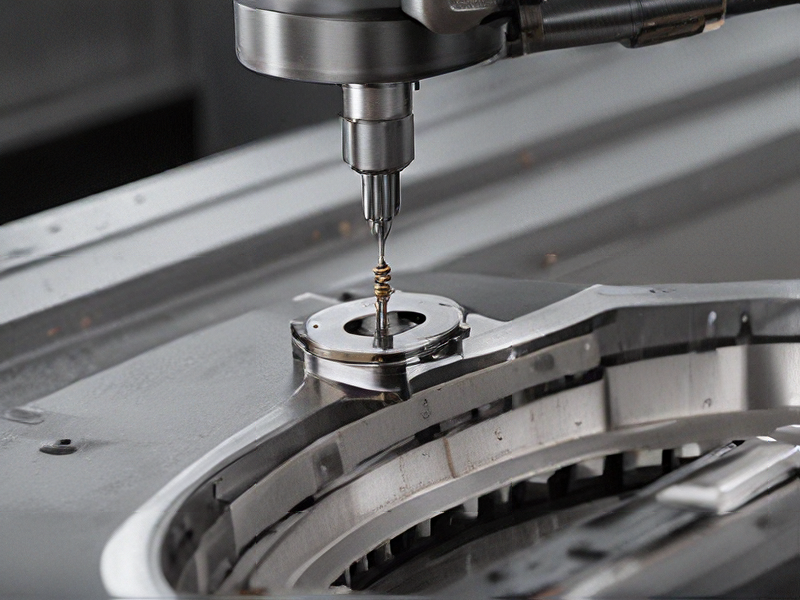
Tips for Procurement and Considerations when Purchasing from machine broaching
Tips for Procurement and Considerations when Purchasing from Machine Broaching
1. Understand Broaching Requirements:
– Determine the exact specifications and tolerances required for your parts. Different broaching machines and tools are optimized for specific materials and dimensions.
2. Quality and Reliability:
– Research manufacturers and suppliers with a reputation for producing high-quality, durable broaching machines. Look for reviews, certifications, and case studies to gauge reliability.
3. Technology and Innovation:
– Ensure the machine offers the latest technology and features that improve efficiency, accuracy, and ease of operation. Advanced machines may offer better automation, reducing manual intervention and error rates.
4. Cost Considerations:
– Compare prices from multiple suppliers, but also consider the total cost of ownership, including maintenance, spare parts, and energy consumption. Sometimes a higher initial investment can lead to long-term savings.
5. After-Sales Support:
– Evaluate the after-sales services, including warranty, technical support, and availability of spare parts. Good support can minimize downtime and extend the machine’s lifespan.
6. Customization and Flexibility:
– Check if the machine can be customized to fit specific production needs and if it can handle various broaching tasks. Versatile machines may offer better value.
7. Training and Ease of Use:
– Ensure that your team can operate the machine efficiently. Suppliers that provide comprehensive training and user-friendly interfaces can reduce the learning curve and increase productivity.
8. Compliance and Standards:
– Verify that the machine meets industry standards and compliance requirements, such as ISO certifications. This ensures safety and quality assurance in production.
9. Environmental Impact:
– Consider the environmental impact of the machine, including energy consumption and waste production. Machines with eco-friendly features can help reduce operational costs and support sustainability goals.
10. Trial and Evaluation:
– If possible, request a trial period or a demonstration of the machine in operation. This hands-on evaluation can provide valuable insights into its performance and suitability for your specific needs.
By following these tips and carefully evaluating each aspect, you can make a well-informed decision when procuring a broaching machine that meets your operational requirements and business objectives.
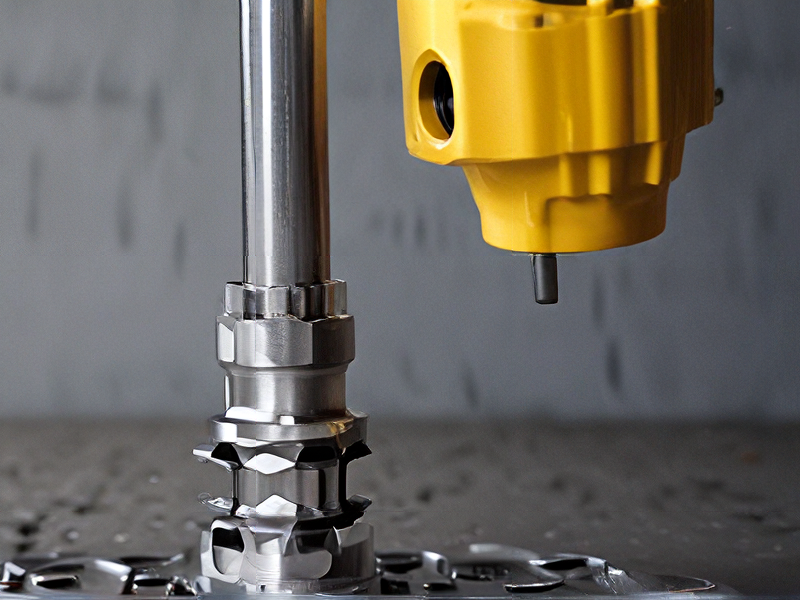
FAQs on Sourcing and Manufacturing from machine broaching in China
When considering sourcing and manufacturing machine broaching in China, several common questions arise:
1. Why choose China for machine broaching?
China offers competitive pricing due to lower labor and production costs. The country also has a vast network of suppliers specializing in precision machining, including broaching.
2. What are the key considerations when selecting a supplier?
Look for suppliers with experience in machine broaching and a proven track record in delivering quality products. Verify their certifications, such as ISO standards, and assess their capacity to meet your production volumes and timelines.
3. How can quality control be ensured?
Implement strict quality control measures throughout the manufacturing process. This includes supplier audits, prototype testing, and regular inspections during production. Clear communication and detailed specifications are crucial.
4. What are the potential challenges?
Language barriers and cultural differences can sometimes lead to misunderstandings. It’s essential to have clear contracts and specifications translated accurately. Shipping logistics and lead times should also be carefully planned.
5. How can intellectual property (IP) protection be addressed?
Protecting your designs and IP is critical. Work with suppliers who respect IP rights and consider legal protections such as patents or non-disclosure agreements (NDAs).
6. What are the steps for finding a reliable supplier?
Utilize online platforms, industry trade shows, and referrals to find reputable suppliers. Conduct thorough due diligence, including background checks and requesting samples before finalizing agreements.
Navigating machine broaching sourcing and manufacturing in China requires careful planning, clear communication, and diligent oversight to ensure quality and reliability throughout the production process.
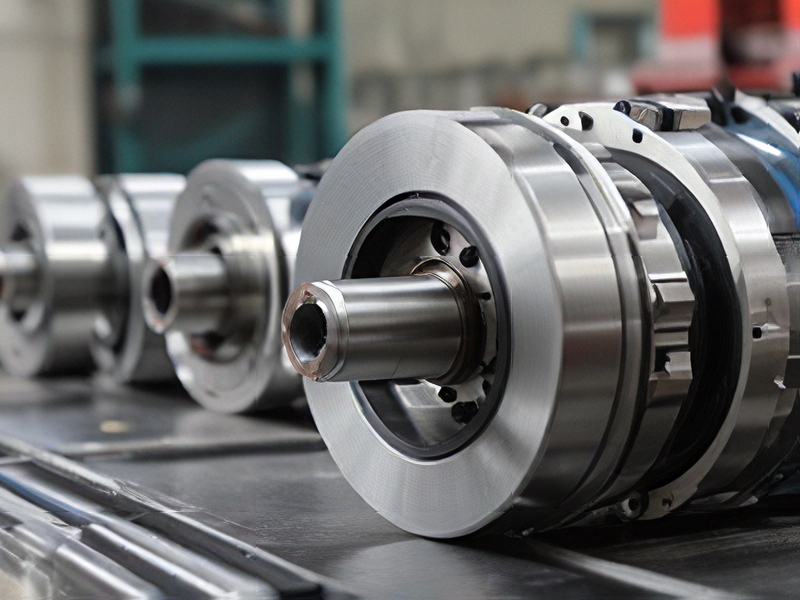