Technology and Applications of aluminium alloy metal
Aluminium alloys are widely utilized in various industries due to their exceptional properties, such as high strength-to-weight ratio, corrosion resistance, and excellent thermal and electrical conductivity. These alloys are primarily used in the aerospace, automotive, construction, and electronics sectors.
Technology:
1. Casting: Aluminium alloys are often produced through casting methods like sand casting, die casting, and permanent mold casting. These processes allow for the creation of complex shapes and are used extensively in the automotive industry for engine blocks and other components.
2. Extrusion: This process involves forcing aluminium alloy through a die to create objects with a fixed cross-sectional profile. It’s commonly used for manufacturing frames, pipes, and other structural components in construction and transportation.
3. Rolling: Rolling involves passing aluminium alloy between rollers to reduce its thickness and achieve desired mechanical properties. It’s used to produce sheets, foils, and plates, which are integral to the packaging and aerospace industries.
4. Forging: This process shapes aluminium alloy by compressive forces, enhancing its mechanical properties. Forged aluminium components are critical in high-stress applications like aircraft landing gears and automotive suspension parts.
5. Additive Manufacturing: Also known as 3D printing, this emerging technology allows for the production of complex aluminium alloy parts with minimal waste, offering significant advantages in prototyping and custom manufacturing.
Applications:
1. Aerospace: Aluminium alloys are essential for aircraft structures, including fuselage, wings, and landing gear, due to their lightweight and strength.
2. Automotive: Used in engine components, wheels, frames, and body panels, aluminium alloys help improve fuel efficiency and reduce emissions.
3. Construction: Aluminium alloys are used in building facades, roofing, window frames, and structural components, offering durability and design flexibility.
4. Electronics: Their excellent thermal conductivity makes aluminium alloys ideal for heat sinks and casings in electronic devices.
5. Marine: Aluminium alloys are used in shipbuilding for hulls and superstructures, providing corrosion resistance and reducing overall vessel weight.
Overall, aluminium alloys’ versatility and performance make them indispensable across various high-tech and industrial applications.
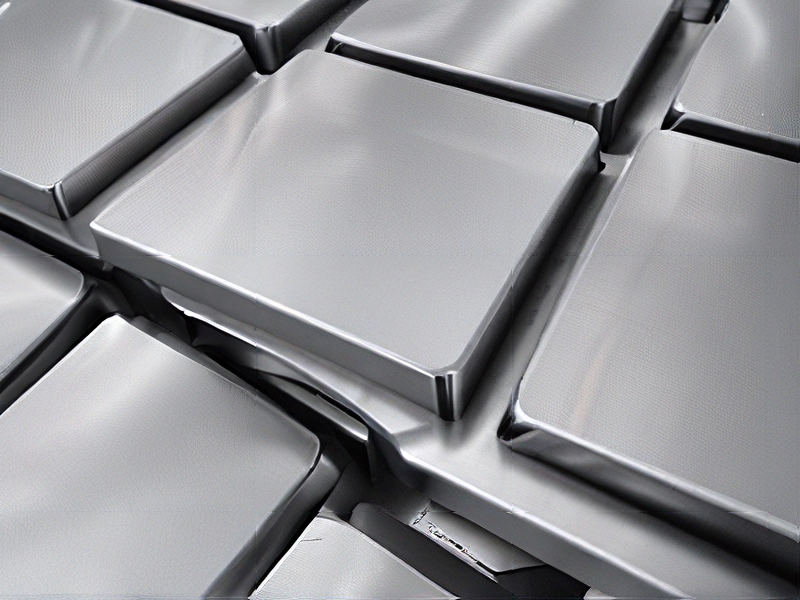
Quality Testing Methods for aluminium alloy metal and how to control quality
Quality testing for aluminum alloy metal involves several methods to ensure it meets required standards. Key methods include:
1. Visual Inspection:
– Purpose: Detect surface defects like cracks, dents, and discolorations.
– Control: Regular inspection routines and trained inspectors.
2. Dimensional Inspection:
– Purpose: Verify dimensions and tolerances using tools like calipers and micrometers.
– Control: Calibrated measurement instruments and adherence to design specifications.
3. Chemical Composition Analysis:
– Purpose: Ensure the alloy contains the correct proportions of elements.
– Methods: Spectroscopy (e.g., XRF, OES).
– Control: Regular sampling and comparison with alloy standards.
4. Mechanical Testing:
– Purpose: Assess properties like tensile strength, hardness, and ductility.
– Methods: Tensile tests, hardness tests (e.g., Brinell, Rockwell), and impact tests.
– Control: Standardized testing procedures and comparison against material specifications.
5. Non-Destructive Testing (NDT):
– Purpose: Detect internal defects without damaging the material.
– Methods: Ultrasonic testing, radiographic testing, and dye penetrant inspection.
– Control: Regular NDT schedules and qualified technicians.
6. Corrosion Resistance Testing:
– Purpose: Evaluate resistance to environmental degradation.
– Methods: Salt spray tests, humidity tests.
– Control: Consistent testing environments and compliance with industry standards.
Quality Control Measures:
– Standard Operating Procedures (SOPs): Detailed instructions for all processes.
– Statistical Process Control (SPC): Monitor production metrics to detect deviations.
– Regular Audits and Reviews: Internal and external audits to ensure adherence to quality standards.
– Training and Certification: Continuous training for employees on quality standards and testing techniques.
– Corrective and Preventive Actions (CAPA): System to address and prevent quality issues.
Implementing these testing methods and quality control measures ensures the reliability and performance of aluminum alloy products.
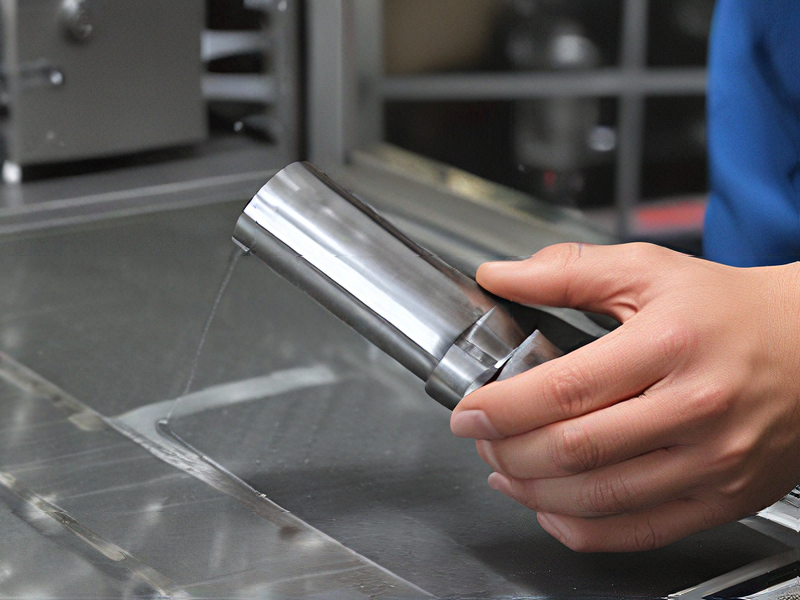
Tips for Procurement and Considerations when Purchasing from aluminium alloy metal
Tips for Procurement of Aluminium Alloy Metal
1. Define Requirements:
– Clearly specify the type and grade of aluminium alloy needed for your project. Different alloys offer various properties like strength, corrosion resistance, and machinability.
2. Supplier Selection:
– Choose reputable suppliers with a track record of providing high-quality aluminium alloys. Verify their certifications and compliance with industry standards.
3. Quality Assurance:
– Ensure the material meets required specifications and standards (e.g., ASTM, EN). Request certificates of conformity and material test reports.
4. Cost Considerations:
– Compare prices from multiple suppliers, but avoid compromising on quality. Consider total cost of ownership, including transportation, handling, and storage.
5. Lead Times:
– Confirm lead times and ensure they align with your project schedule. Factor in potential delays and plan for buffer stock if necessary.
6. Sustainability:
– Opt for suppliers who use recycled aluminium and adopt sustainable practices. This can reduce environmental impact and sometimes lower costs.
Considerations When Purchasing Aluminium Alloy Metal
1. Alloy Composition:
– Different alloys (e.g., 6061, 7075) have unique properties. Match the alloy composition with the application requirements, such as strength, weldability, and corrosion resistance.
2. Form and Size:
– Determine the required form (e.g., sheets, plates, bars, extrusions) and size. Ensure the supplier can provide the precise dimensions needed to minimize waste and machining costs.
3. Surface Finish:
– Specify the surface finish if relevant to the application. This can include mill finish, anodized, or coated surfaces, affecting both aesthetics and performance.
4. Mechanical Properties:
– Evaluate the mechanical properties like tensile strength, yield strength, and hardness to ensure the material can withstand operational demands.
5. Environmental Factors:
– Consider the operating environment (e.g., marine, industrial) and select an alloy with appropriate corrosion resistance.
6. Certification and Traceability:
– Ensure all materials are fully traceable and come with the necessary certifications. This is crucial for quality control and compliance with regulatory standards.

FAQs on Sourcing and Manufacturing from aluminium alloy metal in China
FAQs on Sourcing and Manufacturing from Aluminium Alloy Metal in China
1. Why source aluminium alloy from China?
– Cost Efficiency: China offers competitive pricing due to lower labor and production costs.
– Production Capacity: China has a large number of factories with advanced production capabilities and high output rates.
– Quality Standards: Many Chinese manufacturers adhere to international quality standards like ISO, ensuring high-quality products.
2. How do I ensure the quality of aluminium alloy products?
– Factory Audits: Conduct on-site inspections or hire third-party audit firms.
– Sample Testing: Request samples for testing before bulk production.
– Certifications: Ensure the manufacturer has relevant certifications (ISO, ASTM).
3. What are the common aluminium alloys available?
– Series 1000: Pure aluminium with excellent corrosion resistance and high thermal and electrical conductivity.
– Series 2000: High-strength alloys often used in aerospace applications.
– Series 3000: Manganese alloys with good formability, commonly used in beverage cans.
– Series 5000: Magnesium alloys with excellent corrosion resistance, used in marine environments.
– Series 6000: Silicon and magnesium alloys, versatile for construction and automotive industries.
– Series 7000: Zinc alloys with the highest strength, used in aerospace and high-stress applications.
4. What is the typical lead time for production?
– Lead times vary depending on the complexity and volume of the order but typically range from 4 to 12 weeks.
5. What shipping methods are available?
– Sea Freight: Cost-effective for large shipments, with transit times from 2 to 6 weeks.
– Air Freight: Faster but more expensive, suitable for urgent or smaller orders.
– Rail Freight: An intermediate option available for shipments to Europe.
6. How do I handle intellectual property (IP) concerns?
– NDA Agreements: Sign Non-Disclosure Agreements with manufacturers.
– Patents and Trademarks: Register your IP in China to protect your designs and brands.
7. What payment terms are common?
– Common terms include 30% deposit before production and 70% balance before shipment or upon receipt of the Bill of Lading.
These FAQs cover essential aspects of sourcing and manufacturing aluminium alloys in China, providing a foundation for informed decision-making.
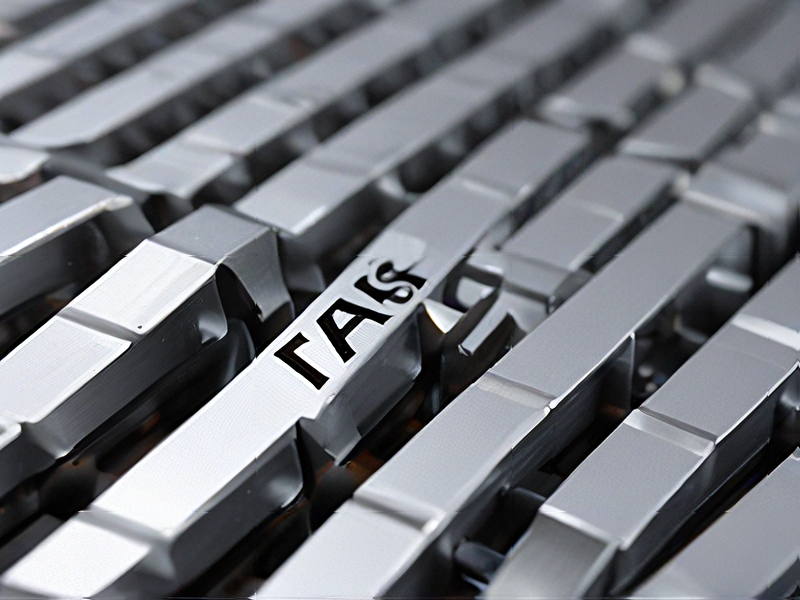