Technology and Applications of annealing metal definition
Annealing is a heat treatment process used to alter the physical and sometimes chemical properties of a metal to increase its ductility and reduce its hardness, making it more workable. The process involves heating the metal to a specific temperature, holding it at that temperature for a certain period, and then allowing it to cool slowly, usually in the furnace.
Technology
The technology of annealing varies depending on the type of metal and the desired properties. The main types include:
1. Full Annealing: The metal is heated to a temperature above its recrystallization point and then slowly cooled. This results in a soft, ductile material with uniform properties.
2. Process Annealing: Used primarily for low-carbon steels, the metal is heated below the recrystallization temperature to relieve internal stresses without changing the overall structure.
3. Stress Relief Annealing: Applied to reduce residual stresses in the metal without significantly altering its structure, typically done at lower temperatures.
4. Spheroidizing Annealing: Involves heating and cooling cycles to produce a globular form of carbide in steel, enhancing machinability.
Applications
Annealing is crucial in various industries due to its ability to improve material properties:
1. Manufacturing: Enhances the ductility of metals, making them easier to shape and form, which is essential for processes like stamping, forging, and rolling.
2. Automotive: Used in the production of car bodies and engine components to improve workability and reduce the risk of cracking during forming.
3. Aerospace: Ensures the durability and reliability of components exposed to extreme conditions by reducing brittleness and improving toughness.
4. Construction: Applied to structural steel to relieve stresses from welding and forming processes, ensuring the stability and safety of buildings and infrastructures.
5. Electronics: Utilized in the production of components like wires and connectors to enhance conductivity and flexibility.
Annealing is a fundamental process in metallurgy, pivotal for achieving desired mechanical properties and ensuring the quality and performance of metal products.
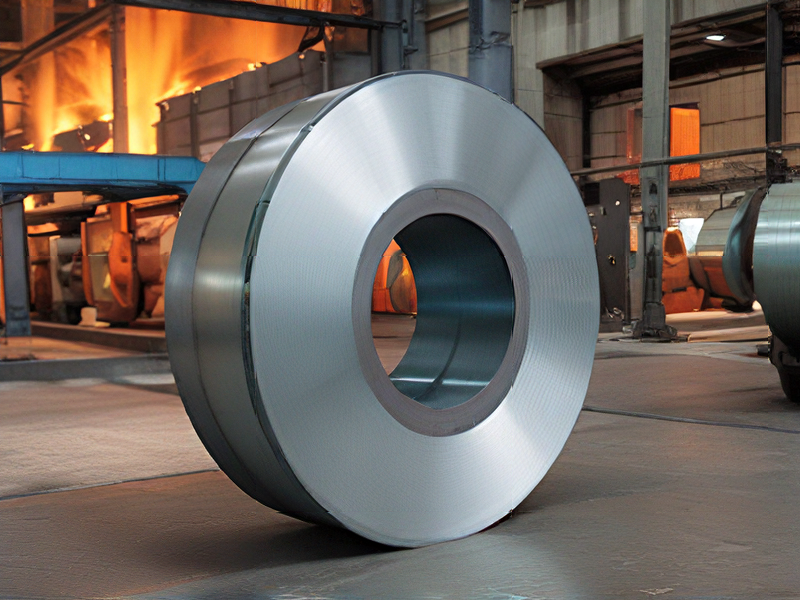
Quality Testing Methods for annealing metal definition and how to control quality
Annealing is a heat treatment process that alters the physical and chemical properties of metal to increase its ductility and reduce hardness, making it more workable. The process involves heating the metal to a specific temperature, holding it at that temperature for a certain period, and then allowing it to cool slowly.
Quality Testing Methods for Annealed Metals
1. Hardness Testing: This measures the metal’s resistance to deformation. Techniques like Rockwell, Brinell, and Vickers hardness tests are commonly used to ensure the metal has achieved the desired softness and workability.
2. Tensile Testing: This assesses the metal’s strength and ductility by pulling it apart until it breaks. The results help verify if the annealing process has provided the desired mechanical properties.
3. Microstructural Analysis: Using optical or electron microscopy, this examines the grain size and phase distribution within the metal. Proper annealing should produce a uniform, refined grain structure.
4. Non-Destructive Testing (NDT): Methods such as ultrasonic testing, X-ray diffraction, and eddy current testing detect internal flaws without damaging the metal. These tests ensure the annealing process has not introduced defects.
Controlling Quality During Annealing
1. Temperature Control: Precise control of the heating temperature is crucial. Using calibrated thermocouples and pyrometers ensures the metal reaches and maintains the correct temperature.
2. Soaking Time: The duration the metal is held at the annealing temperature must be controlled to allow complete recrystallization without grain growth. This is managed using accurate timing mechanisms.
3. Cooling Rate: Controlled cooling, often done in a furnace or using an insulating medium, prevents rapid temperature changes that could lead to thermal stresses and cracking.
4. Atmosphere Control: Maintaining a controlled atmosphere (e.g., inert gas or vacuum) during annealing prevents oxidation and contamination, ensuring the metal’s surface remains clean and the process is consistent.
By employing these quality testing methods and controls, the annealing process can produce metals with the desired mechanical properties and structural integrity.
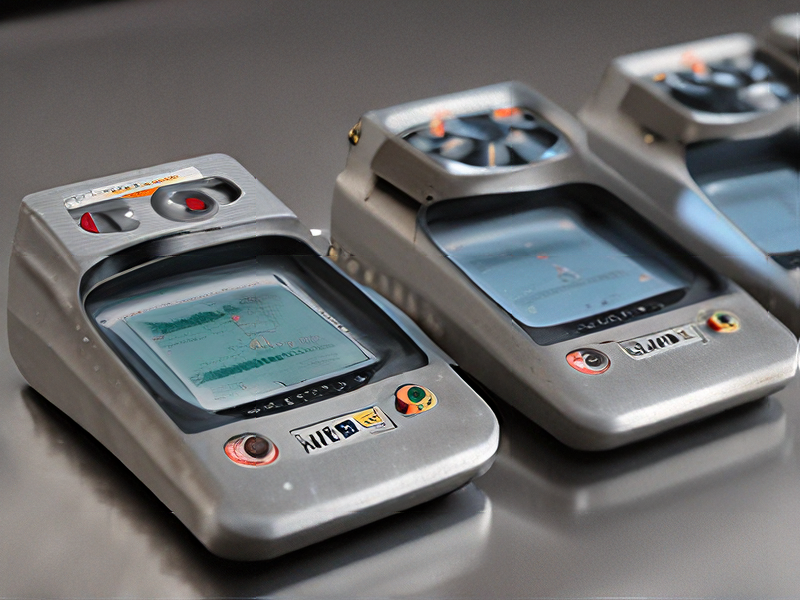
Tips for Procurement and Considerations when Purchasing from annealing metal definition
Tips for Procurement and Considerations when Purchasing from Annealing Metal Suppliers
Understanding Annealing:
Annealing is a heat treatment process that alters the physical and sometimes chemical properties of a metal to increase its ductility and reduce its hardness, making it more workable. This process involves heating the metal to a specific temperature, maintaining that temperature for a certain period, and then cooling it down slowly.
Procurement Tips:
1. Define Requirements Clearly:
– Specify the type of metal and the annealing process required.
– Determine the mechanical properties needed for your application, such as hardness, tensile strength, and ductility.
2. Supplier Evaluation:
– Assess the supplier’s expertise in annealing processes and their ability to meet your specifications.
– Check for certifications and quality control measures, such as ISO 9001.
3. Quality Assurance:
– Request material certifications and test reports to ensure compliance with standards.
– Consider performing independent tests to verify the material properties.
4. Cost Analysis:
– Compare prices from multiple suppliers but ensure that cost savings do not compromise quality.
– Factor in transportation, handling, and potential wastage costs.
5. Lead Time and Delivery:
– Confirm the supplier’s production capacity and lead times to ensure they can meet your schedule.
– Negotiate delivery terms and conditions to avoid delays.
6. Sustainability and Compliance:
– Ensure the supplier adheres to environmental and safety regulations.
– Consider the sustainability practices of the supplier, such as energy-efficient annealing processes.
Considerations When Purchasing:
1. Material Properties:
– Ensure the annealed metal has the desired characteristics suitable for your application, such as flexibility and reduced hardness.
2. Batch Consistency:
– Verify that the supplier can provide consistent quality across different batches to avoid variability in your end products.
3. Customization:
– Check if the supplier offers customization options for specific annealing requirements or special treatments.
4. Technical Support:
– Opt for suppliers who provide technical support and consultation to help you select the right material and process.
By focusing on these key aspects, you can ensure a successful procurement process and obtain high-quality annealed metals that meet your specific needs.
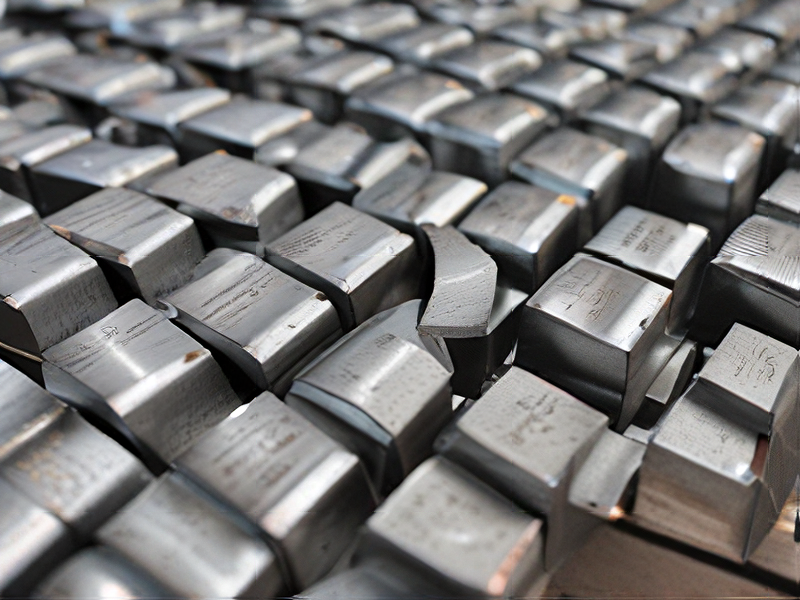
FAQs on Sourcing and Manufacturing from annealing metal definition in China
FAQs on Sourcing and Manufacturing from China
#### 1. What is annealing in metal manufacturing?
Annealing is a heat treatment process that alters the physical and chemical properties of a material, typically metal, to increase its ductility and reduce its hardness, making it more workable. The process involves heating the metal to a specific temperature, maintaining that temperature, and then allowing it to cool slowly.
#### 2. Why source from China?
China offers competitive pricing, a vast range of manufacturers, and a well-established supply chain infrastructure. The country’s expertise in manufacturing, coupled with large-scale production capabilities, allows for cost-effective solutions and quick turnaround times.
#### 3. How do I find reliable manufacturers in China?
Use platforms like Alibaba, Made-in-China, and Global Sources to identify potential suppliers. Vet suppliers by checking certifications, requesting samples, and visiting factories if possible. Third-party verification services can also ensure credibility and quality.
#### 4. What are common challenges in sourcing from China?
Language barriers, quality control issues, and logistics complexities are common challenges. Working with sourcing agents or companies specializing in Chinese manufacturing can help mitigate these issues.
#### 5. How do I ensure quality control?
Implement rigorous quality control measures, such as regular inspections, detailed specifications, and third-party audits. Request pre-production samples and conduct inspections at various stages of production.
#### 6. What are the logistics considerations?
Consider shipping methods (air, sea, or rail), customs regulations, tariffs, and incoterms (International Commercial Terms). Partnering with experienced freight forwarders and customs brokers can streamline the process.
#### 7. What is the typical lead time for manufacturing in China?
Lead times vary depending on the complexity of the product and the production schedule of the manufacturer. Generally, it ranges from a few weeks to several months. Clear communication and planning can help manage expectations and timelines.
#### 8. How do I handle intellectual property (IP) protection?
Register your IP in China, including patents, trademarks, and copyrights. Use non-disclosure agreements (NDAs) and choose manufacturers with a good track record of IP respect.
By understanding these key aspects, businesses can effectively navigate the complexities of sourcing and manufacturing from China.
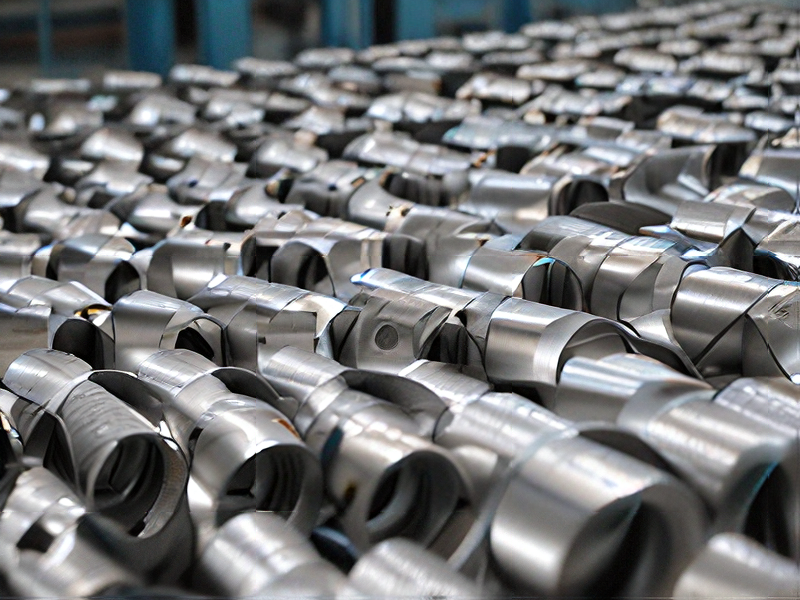