Technology and Applications of carving machine for wood
A carving machine for wood, often referred to as a CNC (Computer Numerical Control) wood carving machine, utilizes computer-controlled movements to precisely carve and sculpt wood. These machines have revolutionized woodworking by offering accuracy, speed, and the ability to replicate designs consistently.
Technology:
Modern CNC wood carving machines consist of several key components:
1. Computer Control: Operators use software to design patterns and specify carving parameters such as depth, speed, and tooling.
2. Mechanical System: This includes motors, gears, and drive systems that move the cutting tool (router or spindle) along predefined paths.
3. Tooling: Various cutting tools such as end mills, router bits, and drills are used based on the desired carving depth and detail.
Applications:
1. Furniture Manufacturing: CNC machines are extensively used to carve intricate designs on furniture components, from table legs to decorative panels.
2. Art and Sculpture: Artists and sculptors use these machines to create detailed sculptures and art pieces with precision that would be difficult to achieve manually.
3. Sign Making: CNC carving machines are used in sign-making industries to create custom signs with intricate lettering and designs.
4. Cabinetry: They are employed in making custom cabinets and cabinetry components, including detailed insets and moldings.
5. Prototyping and Production: CNC carving machines are valuable in prototyping new designs quickly and in the mass production of standardized components with consistent quality.
In conclusion, CNC wood carving machines combine advanced technology with traditional craftsmanship, offering versatility and efficiency in woodworking. They are indispensable tools in industries ranging from furniture manufacturing to artistic sculpture, enabling intricate designs and precise execution with minimal manual effort.
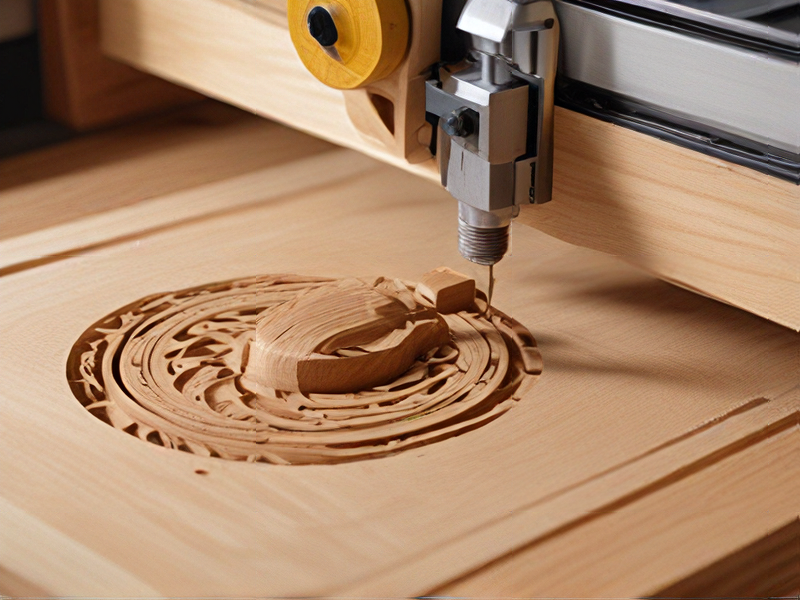
Quality Testing Methods for carving machine for wood and how to control quality
Quality Testing Methods for Wood Carving Machines
1. Dimensional Accuracy Testing:
– Method: Measure the carved dimensions against design specifications using calipers or laser measurement tools.
– Control: Regular calibration of the machine and tools ensures consistent precision.
2. Surface Finish Inspection:
– Method: Visual inspection and touch testing to detect rough surfaces, tool marks, and other imperfections.
– Control: Use standardized templates for comparison and ensure sharp, well-maintained tools.
3. Material Consistency Check:
– Method: Test different wood types to ensure the machine performs consistently across various materials.
– Control: Document machine settings for each material and regularly review performance data.
4. Repeatability Testing:
– Method: Perform multiple carvings of the same design and compare the results.
– Control: Implement automated software to track and compare outcomes, adjusting settings as necessary.
5. Vibration and Stability Analysis:
– Method: Monitor machine vibrations using accelerometers during operation.
– Control: Ensure the machine is on a stable surface and maintain tightness of all bolts and components.
6. Tool Wear Monitoring:
– Method: Regularly inspect tools for wear and tear.
– Control: Implement a scheduled tool replacement or sharpening program.
7. Software Integrity Check:
– Method: Verify the accuracy of the CAD/CAM software used for designing and executing carvings.
– Control: Regular software updates and validations against known standards.
8. Load Testing:
– Method: Run the machine at maximum capacity for extended periods to test durability.
– Control: Document performance under stress and perform preventive maintenance based on findings.
Controlling Quality
1. Standard Operating Procedures (SOPs): Develop and adhere to detailed SOPs for machine operation, maintenance, and quality checks.
2. Training: Regularly train operators on machine use, maintenance, and quality control techniques.
3. Data Logging: Implement a system to log all machine operations, maintenance activities, and inspection results for ongoing review and analysis.
4. Preventive Maintenance: Schedule regular maintenance to preemptively address wear and potential issues.
5. Continuous Improvement: Use feedback from inspections and operator input to continually refine processes and machine settings.
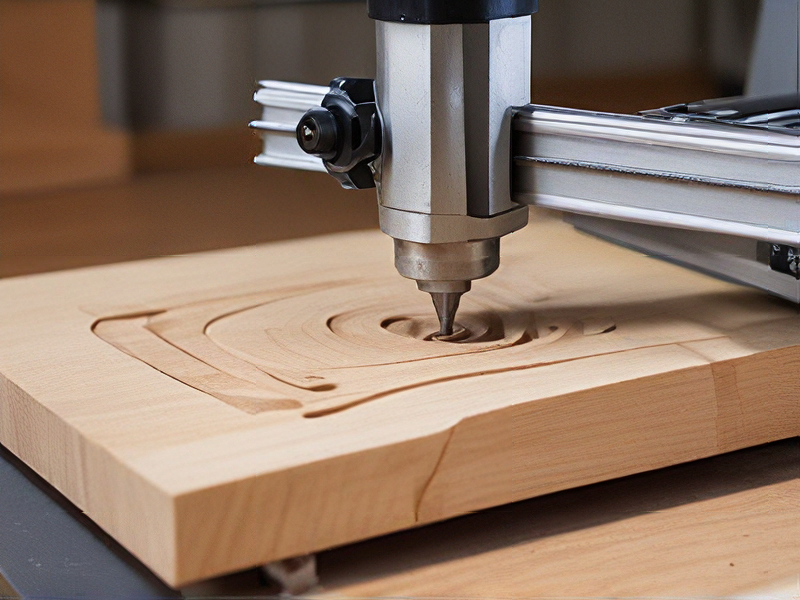
Tips for Procurement and Considerations when Purchasing from carving machine for wood
Tips for Procurement and Considerations when Purchasing a Wood Carving Machine
#### 1. Define Your Needs
– Project Scope: Determine the types of projects you’ll be undertaking. Different machines are suited for different levels of complexity and detail.
– Material Compatibility: Ensure the machine can handle the specific types of wood you plan to use.
#### 2. Budget Planning
– Initial Costs: Set a budget for the machine itself. Prices can range widely based on features and capabilities.
– Operational Costs: Consider ongoing expenses such as maintenance, power consumption, and tooling.
#### 3. Technical Specifications
– Cutting Area: The size of the workspace should match your project dimensions.
– Spindle Power: Higher power spindles can handle harder woods and provide smoother finishes.
– Speed and Precision: Look for machines with high RPM and precision for detailed work.
#### 4. Software Compatibility
– Design Software: Ensure the machine is compatible with your preferred CAD/CAM software for seamless operation.
– Updates and Support: Check if the manufacturer provides regular software updates and technical support.
#### 5. Build Quality and Durability
– Construction: Look for machines made from high-quality materials like steel or cast aluminum for longevity and stability.
– Brand Reputation: Research brands with a good reputation for reliability and customer service.
#### 6. Ease of Use
– User Interface: A user-friendly interface can significantly reduce the learning curve.
– Training and Tutorials: Availability of training resources or tutorials can be very helpful.
#### 7. Support and Warranty
– Customer Support: Opt for manufacturers that offer robust customer support.
– Warranty: A good warranty can protect your investment from manufacturing defects.
#### 8. Safety Features
– Emergency Stop: Ensure the machine has an easily accessible emergency stop button.
– Dust Collection: Consider machines with built-in dust collection to maintain a clean and safe working environment.
By carefully considering these factors, you can select a wood carving machine that meets your needs and provides long-term value for your woodworking projects.
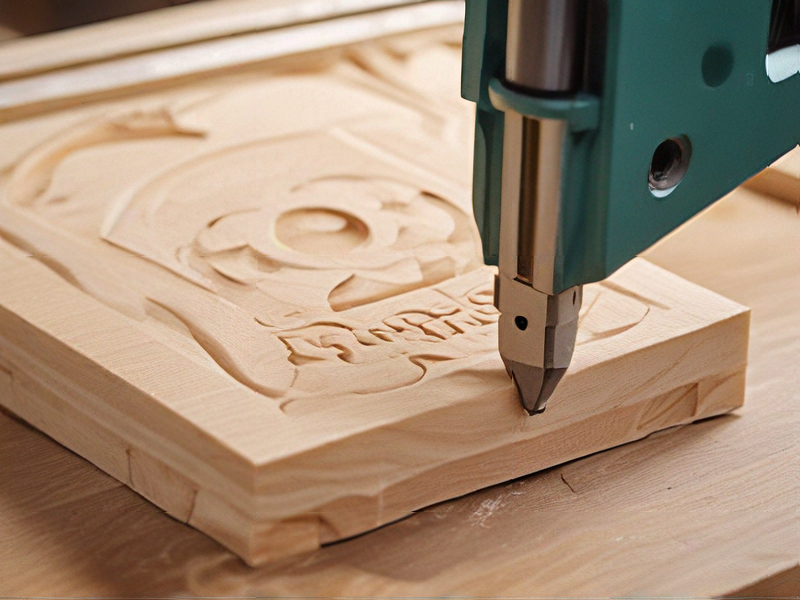
FAQs on Sourcing and Manufacturing from carving machine for wood in China
Certainly! Here are some FAQs regarding sourcing and manufacturing carving machines for wood in China:
1. What types of carving machines for wood are commonly manufactured in China?
China manufactures a wide range of carving machines for wood, including CNC routers, laser engravers, and traditional mechanical carving machines.
2. How do I find reliable suppliers of carving machines in China?
Utilize online marketplaces like Alibaba or Made-in-China.com to find suppliers. It’s crucial to vet suppliers carefully by checking their reviews, asking for samples, and verifying their manufacturing capabilities.
3. What are the typical manufacturing standards for carving machines in China?
Manufacturers in China adhere to various quality standards, such as ISO 9001. It’s advisable to discuss specific quality requirements with potential suppliers before making a purchase.
4. Can I customize carving machines according to my specifications?
Yes, many Chinese manufacturers offer customization options for carving machines. Be clear about your requirements regarding machine size, power, and specific functionalities.
5. What are the typical lead times for manufacturing and shipping carving machines from China?
Lead times can vary depending on the complexity of the machine and the supplier’s production capacity. It’s common to expect lead times ranging from a few weeks to several months.
6. How can I ensure product quality and reliability?
Conduct thorough inspections during production and before shipment. Consider hiring a third-party inspection service to ensure the machines meet your specifications and quality standards.
7. What are the payment terms typically used when sourcing carving machines from China?
Payment terms can vary, but common methods include T/T (Telegraphic Transfer) and L/C (Letter of Credit). Negotiate terms that provide security and align with your risk tolerance.
8. What are the challenges of sourcing carving machines from China?
Challenges may include language barriers, cultural differences, and logistical complexities. Building a strong relationship with your supplier and clear communication can mitigate these challenges.
9. Are there any import duties or regulations I need to be aware of?
Yes, research import duties, taxes, and any regulatory requirements that may apply in your country. Work closely with your supplier to ensure proper documentation and compliance.
10. What support can I expect from Chinese manufacturers after purchasing a carving machine?
Many manufacturers provide technical support, warranties, and spare parts. Clarify post-sale support details with your supplier before finalizing the purchase.
Navigating the sourcing and manufacturing process for carving machines in China requires careful planning, thorough research, and effective communication with potential suppliers to ensure a successful partnership.
