Technology and Applications of carving machine wood
Carving machines for woodwork encompass a variety of technologies tailored to enhance precision and efficiency in woodworking tasks. Computer Numerical Control (CNC) machines are prominent in this field, allowing intricate designs and patterns to be carved into wood based on digital templates. These machines operate with high accuracy, executing detailed cuts and engravings that manual methods may struggle to replicate consistently.
The technology behind carving machines involves robust mechanical structures equipped with motors and cutting tools, guided by computer programs. These programs translate design files, often created in CAD software, into precise movements of the cutting tool across the wood surface. This level of automation not only speeds up production but also reduces human error, ensuring uniformity in the finished products.
Applications of carving machines in woodworking are diverse. They are widely used in furniture manufacturing to create decorative elements such as intricate patterns on chair backs or tabletops. In architectural woodworking, these machines carve ornate details for doors, windows, and moldings, enhancing the aesthetic appeal of interiors and exteriors. Artists and craftspeople also utilize carving machines to produce custom pieces and sculptures with intricate designs that showcase creativity and technical precision.
Overall, carving machines have revolutionized woodworking by combining digital precision with traditional craftsmanship. They cater to both industrial-scale production and bespoke craftsmanship, offering versatility in design capabilities and improving overall efficiency in woodworking processes.
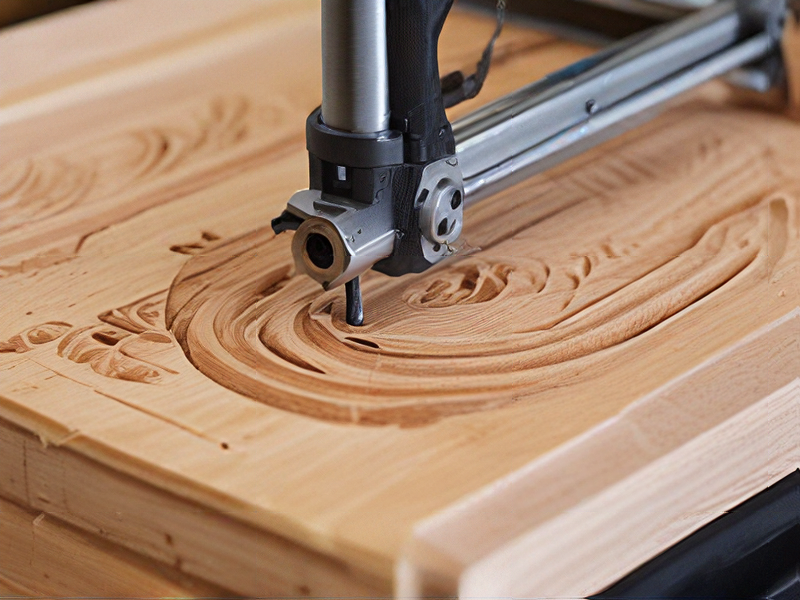
Quality Testing Methods for carving machine wood and how to control quality
Quality Testing Methods for Wood Carving Machines
1. Visual Inspection:
– Purpose: Detect surface defects such as rough edges, splinters, and inconsistencies in carvings.
– Process: Regularly examine carved pieces under good lighting to identify and rectify visible flaws.
2. Dimensional Accuracy:
– Purpose: Ensure carvings meet specified dimensions and tolerances.
– Process: Use calipers, micrometers, or laser measuring tools to check the dimensions of the finished pieces.
3. Surface Finish Testing:
– Purpose: Measure the smoothness of the wood surface.
– Process: Employ surface roughness testers to quantify the texture and smoothness of the carvings.
4. Load Testing:
– Purpose: Verify the structural integrity of the carved pieces.
– Process: Apply controlled forces to the carvings to ensure they can withstand expected loads without breaking.
5. Consistency Checks:
– Purpose: Ensure uniformity across multiple pieces.
– Process: Use templates or automated systems to compare multiple pieces for consistency in design and dimensions.
Quality Control Measures
1. Calibration:
– Regularly calibrate carving machines to maintain precision.
– Schedule routine maintenance to prevent deviations in machine performance.
2. Material Quality:
– Source high-quality wood with minimal defects.
– Conduct moisture content tests to ensure the wood is properly seasoned and less prone to warping.
3. Operator Training:
– Train operators thoroughly on machine use and maintenance.
– Implement standard operating procedures for consistent machine handling.
4. Automation and Software:
– Use CAD/CAM software for precise design and execution.
– Implement automated quality control systems to detect and correct errors in real-time.
5. Documentation:
– Maintain detailed records of quality checks and machine maintenance.
– Use these records to identify and address recurring issues.
By integrating these methods and controls, you can significantly enhance the quality and consistency of carvings produced by wood carving machines.
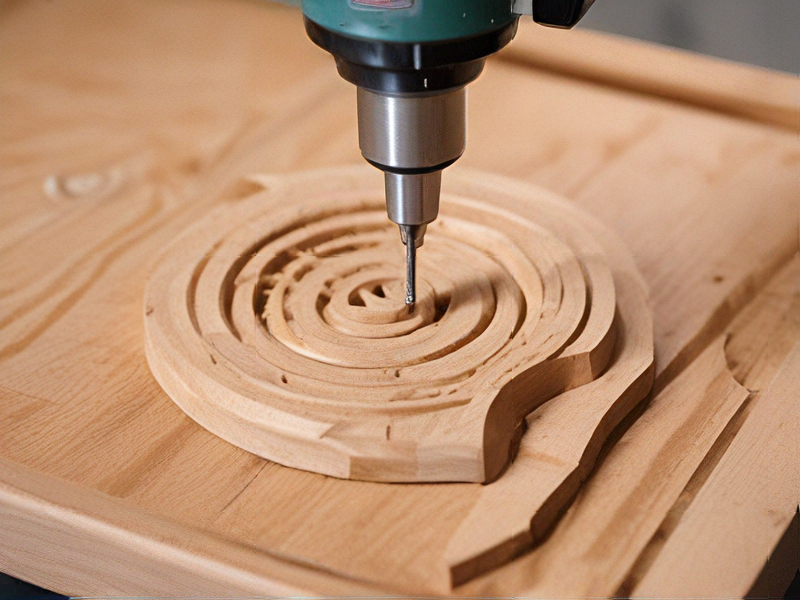
Tips for Procurement and Considerations when Purchasing from carving machine wood
When procuring a carving machine for woodwork, several considerations are crucial to ensure optimal performance and value:
1. Machine Type and Capability: Choose between CNC routers, laser cutters, or traditional carving machines based on your specific needs. CNC routers offer versatility, while laser cutters provide precision for intricate designs.
2. Performance Specifications: Evaluate factors like spindle power, cutting speed, and bed size. Higher spindle power and larger bed sizes accommodate larger and denser wood pieces, while cutting speed influences production efficiency.
3. Ease of Use and Software Compatibility: Opt for machines with user-friendly interfaces and compatible software. This ensures smoother operation and facilitates learning for operators.
4. Durability and Maintenance: Prioritize machines constructed from robust materials like cast iron or steel for durability. Check maintenance requirements and availability of spare parts to minimize downtime.
5. Safety Features: Ensure the machine complies with safety standards and features like emergency stop buttons, protective enclosures, and laser safety measures (if applicable).
6. Cost and Budget: Consider initial purchase costs, ongoing maintenance, and operational expenses. Balance these factors with the machine’s capabilities and expected return on investment.
7. Supplier Reputation and Support: Choose reputable suppliers offering warranties, technical support, and training. Research customer reviews and testimonials to gauge reliability.
8. Future Scalability: Anticipate future needs such as upgrading capabilities or expanding production capacity. Choose a machine that allows for future modifications or additions.
9. Environmental Impact: Consider energy efficiency ratings and environmental impact of the machine’s operation, especially if aiming for sustainable practices.
10. Training and Skill Requirements: Assess the level of expertise required for operation and consider training options to ensure staff competency.
By carefully evaluating these factors, you can make an informed decision when purchasing a carving machine for woodworking, ensuring it meets your production needs effectively and efficiently.
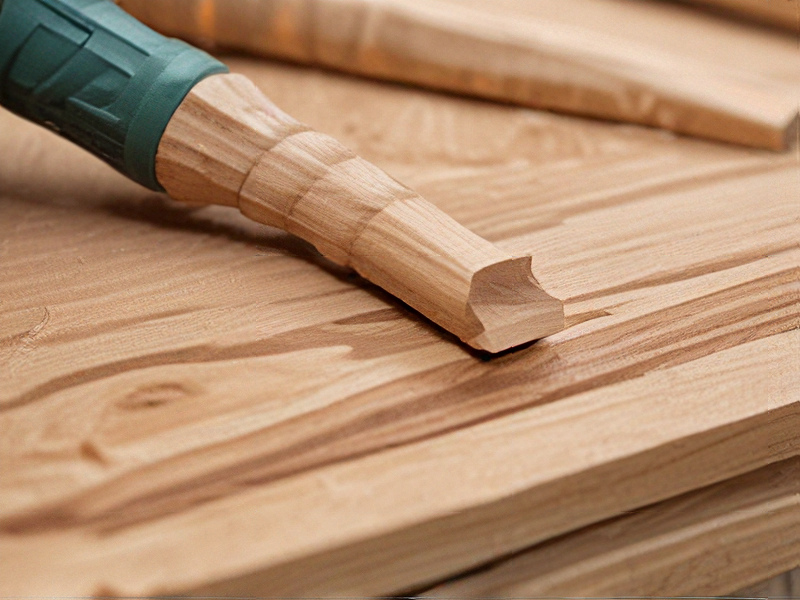
FAQs on Sourcing and Manufacturing from carving machine wood in China
FAQs on Sourcing and Manufacturing Wood Carving Machines in China
1. Why source wood carving machines from China?
China is a leading manufacturer of wood carving machines due to its advanced technology, skilled labor, and cost-effectiveness. The country offers a wide range of machines suitable for various scales of production.
2. How do I find reliable suppliers?
Utilize platforms like Alibaba, Made-in-China, and Global Sources to find suppliers. Look for suppliers with high ratings, positive reviews, and verified certifications. Attending trade fairs like Canton Fair can also help in meeting suppliers in person.
3. What certifications should I look for?
Ensure the machines comply with international standards such as CE, ISO, and RoHS. These certifications guarantee the machine’s safety, quality, and environmental compliance.
4. How can I verify the quality of the machines?
Request samples or visit the supplier’s factory if possible. Third-party inspection companies can also conduct pre-shipment inspections to ensure the machines meet your specifications.
5. What are the payment terms?
Common payment methods include T/T (Telegraphic Transfer), L/C (Letter of Credit), and Western Union. It’s advisable to negotiate a small deposit (30%) with the balance paid after shipment or upon inspection.
6. How do I handle shipping and logistics?
Suppliers usually offer FOB (Free On Board) terms, but you can also negotiate for CIF (Cost, Insurance, and Freight). Hiring a freight forwarder can simplify the logistics process, including customs clearance and delivery.
7. Are there any potential risks?
Risks include receiving substandard machines, delays in delivery, and communication barriers. Mitigate these risks by doing thorough research, maintaining clear communication, and using contracts that specify terms and conditions clearly.
8. Can I get after-sales support?
Most reputable suppliers provide after-sales support, including installation guidance, technical support, and spare parts. Ensure that this is included in your contract.
9. How long is the typical lead time?
The lead time can vary from a few weeks to several months, depending on the customization level and order quantity. Confirm the timeline with your supplier in advance.
10. What should I include in the contract?
A detailed contract should include product specifications, quantities, prices, payment terms, delivery schedule, warranty, and after-sales service terms.
By following these guidelines, you can effectively source and manufacture wood carving machines from China, ensuring quality and reliability.
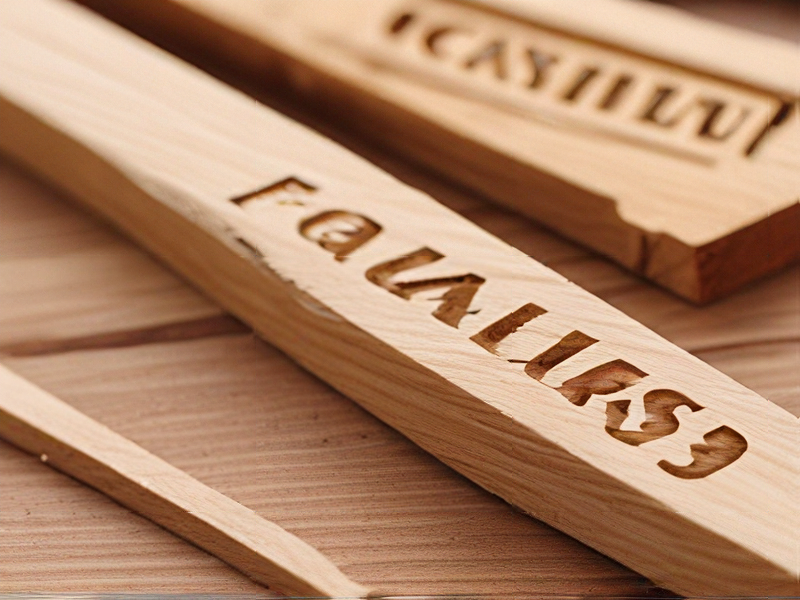