Technology and Applications of cnc cutting machine wood
CNC cutting machines revolutionize wood processing by automating precise cuts and intricate designs.
These machines utilize computer-aided programming to guide cutting tools, eliminating manual labor and enhancing accuracy.
Applications:
* Furniture Manufacturing: Creating custom cabinets, doors, and intricate furniture pieces with complex shapes and joinery.
* Woodworking Crafts:
Enabling the production of detailed models, sculptures, and personalized gifts with high precision.
* Signage and Display: Cutting letters, logos, and intricate patterns for signs, billboards, and display materials.
* Construction and Architecture:
Producing custom moldings, stair components, and other architectural elements with precise dimensions.
Advantages:
* High Accuracy: CNC cutting ensures precise cuts and consistent results.
* Efficiency: Automation speeds up production and increases output.
* Versatility: Machines can handle a wide range of wood types and thicknesses.
* Complex Designs: Capable of producing intricate and customized designs.
CNC cutting machines empower businesses and individuals to create high-quality wood products with exceptional precision and efficiency.
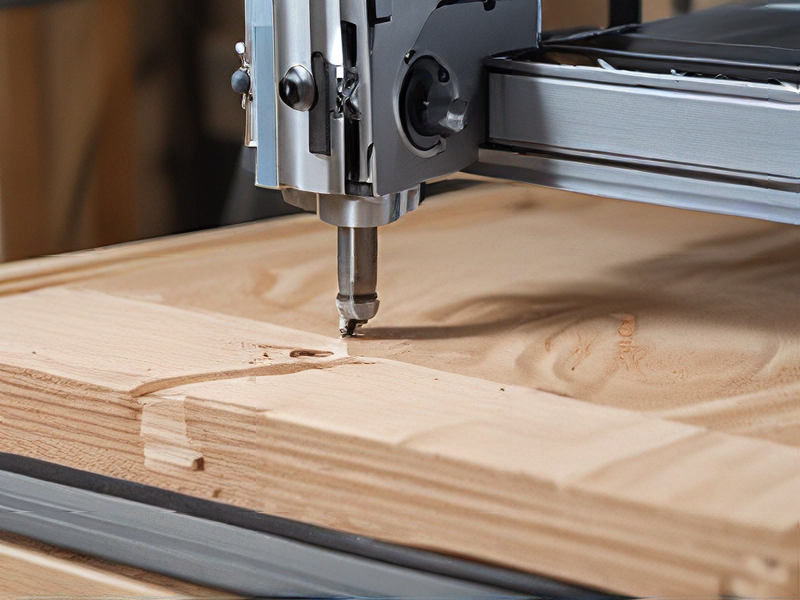
Quality Testing Methods for cnc cutting machine wood and how to control quality
Quality testing methods for CNC cutting machines used in wood processing typically include:
1. Dimensional Accuracy: Measure the dimensions of cut pieces using calipers or digital measuring tools to ensure they match specifications.
2. Surface Quality: Inspect the cut surfaces visually or using a surface roughness gauge to ensure smoothness and absence of defects.
3. Edge Straightness and Smoothness: Check edges for straightness and smoothness using straightedges and touch inspection for burrs.
4. Precision of Cuts: Verify the precision of cuts against design specifications using coordinate measuring machines (CMM) or laser alignment tools.
5. Material Inspection: Ensure the wood material used meets specified standards for moisture content, grain direction, and defects.
6. Tool Condition Monitoring: Regularly check tool condition (e.g., sharpness of cutting tools) to maintain consistent cutting quality.
7. Process Parameters: Monitor and control cutting parameters such as speed, feed rate, and depth of cut to optimize quality and efficiency.
To control quality effectively:
– Establish Standard Operating Procedures (SOPs): Document procedures for setup, operation, and maintenance to ensure consistency.
– Regular Maintenance: Schedule routine maintenance for CNC machines and cutting tools to prevent wear and ensure optimal performance.
– Employee Training: Train operators on machine operation, quality standards, and troubleshooting techniques.
– Quality Assurance Checks: Implement regular quality checks at different stages of production to detect deviations early.
– Feedback Loop: Establish a feedback mechanism to address issues promptly and improve processes continuously.
By employing these methods and controls, manufacturers can maintain high-quality standards in CNC wood cutting operations, ensuring precision, efficiency, and customer satisfaction.
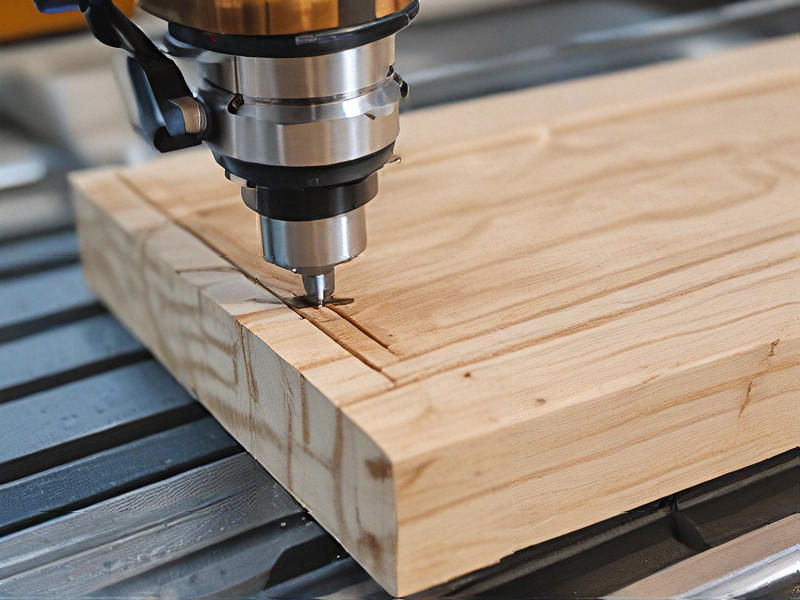
Tips for Procurement and Considerations when Purchasing from cnc cutting machine wood
When procuring a CNC cutting machine for wood, consider these essential tips and considerations:
1. Machine Specifications: Evaluate the machine’s cutting dimensions, speed, and accuracy. Ensure it meets your project requirements, including the types and thicknesses of wood it can handle.
2. Software Compatibility: Check if the machine’s software is user-friendly and compatible with your existing design programs. Ease of programming can significantly impact productivity.
3. Build Quality and Durability: Look for machines built with robust materials that can withstand continuous operation. Longevity and reliability are crucial for minimizing downtime.
4. Support and Training: Opt for suppliers that offer comprehensive training and ongoing technical support. This ensures your team can operate the machine proficiently and troubleshoot effectively.
5. Safety Features: Prioritize machines with built-in safety features like emergency stop buttons, protective barriers, and safety sensors. Compliance with safety standards is non-negotiable.
6. Cost Considerations: Compare upfront costs, maintenance expenses, and operational costs (e.g., electricity, tooling). Balance affordability with long-term value and ROI.
7. User Reviews and References: Research user reviews and seek references from other businesses using similar equipment. Real-world experiences can provide valuable insights.
8. Future Expansion: Anticipate future needs and consider scalability. Ensure the machine can accommodate potential upgrades or expansions in production capacity.
9. Warranty and Service Agreements: Review warranty coverage and service agreements. Understand what is included and for how long to avoid unexpected repair costs.
10. Environmental Impact: Evaluate energy efficiency and environmental impact. Choose machines that align with your sustainability goals and regulatory requirements.
By carefully considering these factors, you can make an informed decision when purchasing a CNC cutting machine for wood that aligns with your operational needs and long-term business goals.
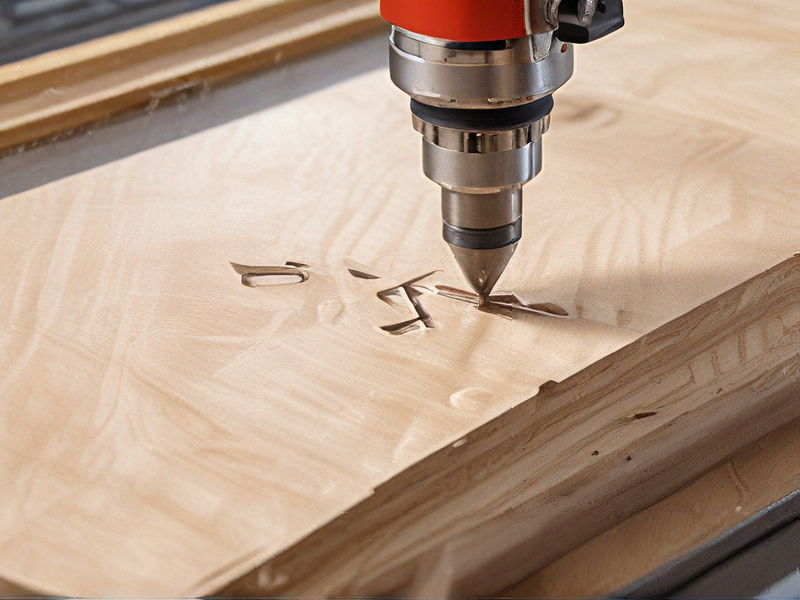
FAQs on Sourcing and Manufacturing from cnc cutting machine wood in China
When sourcing and manufacturing CNC cutting machines for wood from China, it’s essential to address several FAQs:
1. Quality Assurance: Ensure suppliers adhere to international quality standards (ISO certifications) and provide samples for verification.
2. Customization: Discuss customization options for machine specifications, software integration, and technical support.
3. Lead Times: Clarify production timelines, shipping schedules, and any potential delays due to manufacturing or global logistics issues.
4. Costs and Pricing: Obtain a detailed breakdown of costs including unit price, shipping, taxes, and import duties to avoid unexpected expenses.
5. After-Sales Support: Inquire about warranty terms, technical support availability, and spare parts accessibility to maintain machine longevity.
6. Communication: Establish clear communication channels and language proficiency to mitigate misunderstandings during the manufacturing and delivery process.
7. Compliance and Regulations: Ensure products comply with safety regulations and import requirements in your country to avoid legal issues.
8. Supplier Reputation: Research supplier reviews, request client references, and verify their reputation in the industry for reliability and product consistency.
9. Payment Terms: Negotiate favorable payment terms to balance financial security with supplier expectations.
10. Scalability: Discuss scalability options if future expansions or modifications to the CNC machines are necessary.
By addressing these FAQs thoroughly with potential suppliers in China, you can navigate sourcing and manufacturing CNC cutting machines for wood more effectively, ensuring quality, reliability, and compliance with your business needs.
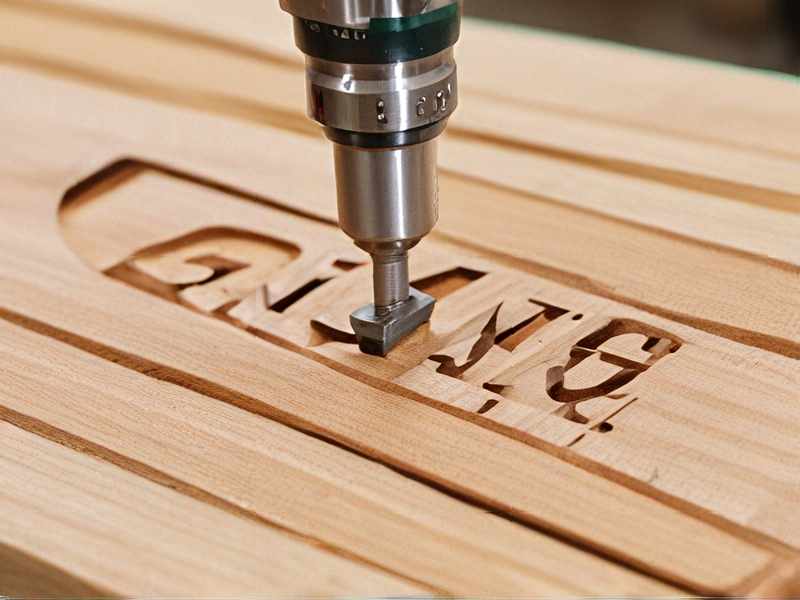