Technology and Applications of cnc for metal
Computer Numerical Control (CNC) technology revolutionizes metalworking by automating machining processes with precision and efficiency. CNC machines interpret digital instructions to manipulate tools and workpieces, ensuring consistent and accurate production. This technology finds extensive applications across various metalworking disciplines:
1. Milling: CNC milling machines utilize rotary cutters to remove material from a workpiece, creating intricate shapes and profiles. They excel in producing components for aerospace, automotive, and mold-making industries.
2. Turning: CNC turning centers rotate a workpiece while cutting tools remove material. This process is ideal for cylindrical parts such as shafts, bolts, and fittings, offering high-speed, high-accuracy production.
3. Drilling and Tapping: CNC machines automate drilling and tapping operations with precise control over depth, speed, and positioning. This capability is crucial in manufacturing holes for fasteners and fittings in metal structures.
4. Grinding: CNC grinding machines achieve fine surface finishes and dimensional accuracy by removing material through abrasion. They are vital in producing tools, dies, and precision components requiring tight tolerances.
5. Laser Cutting: CNC laser cutting machines use focused laser beams to cut through metal sheets and plates with exceptional speed and precision. This technology is widely used in sheet metal fabrication for industries ranging from electronics to construction.
6. Waterjet Cutting: CNC waterjet machines cut metal using a high-pressure jet of water mixed with abrasive particles. They offer versatility in cutting various metals, including stainless steel and aluminum, without thermal distortion.
7. Wire EDM: CNC Wire Electrical Discharge Machining (EDM) precisely cuts conductive materials using electrical discharges. It is indispensable in manufacturing intricate molds, dies, and tooling components with tight tolerances.
CNC technology enhances productivity, reduces waste, and enables the production of complex geometries that are challenging to achieve manually. Its applications continue to expand, driven by advancements in machine capabilities and software integration, catering to diverse demands in the metalworking industry.
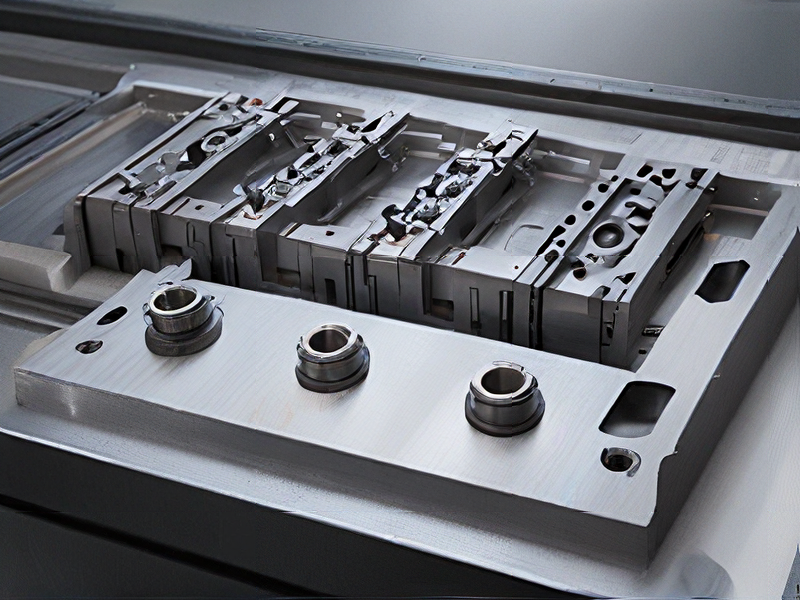
Quality Testing Methods for cnc for metal and how to control quality
Quality testing methods for CNC (Computer Numerical Control) machining of metal typically involve several key approaches:
1. Dimensional Inspection: Utilizing precision measurement tools such as micrometers, calipers, and CMM (Coordinate Measuring Machine) to verify part dimensions against CAD specifications.
2. Surface Roughness Measurement: Assessing the surface finish using profilometers or surface roughness testers to ensure it meets required standards.
3. Visual Inspection: Examining parts for defects like burrs, cracks, or surface irregularities that can affect functionality or aesthetics.
4. Material Testing: Verifying material properties through methods like hardness testing (Rockwell, Brinell) and material composition analysis (spectroscopy).
5. Functional Testing: Testing parts under simulated operating conditions to ensure they perform as intended.
To control quality:
1. Implementing Quality Management Systems: Establishing procedures and documentation to ensure consistency and traceability throughout the manufacturing process.
2. Regular Calibration of Equipment: Ensuring measurement tools and CNC machines are calibrated regularly to maintain accuracy.
3. Training and Skill Development: Providing ongoing training to operators and inspectors on quality standards, inspection techniques, and CNC machine operation.
4. Statistical Process Control (SPC): Monitoring production processes using statistical methods to detect and address variations before they affect product quality.
5. Feedback Loops and Continuous Improvement: Using data from inspections and testing to identify areas for improvement in processes and product quality.
By employing these methods and controls, manufacturers can ensure CNC machined metal parts meet stringent quality requirements, minimizing defects and ensuring customer satisfaction.
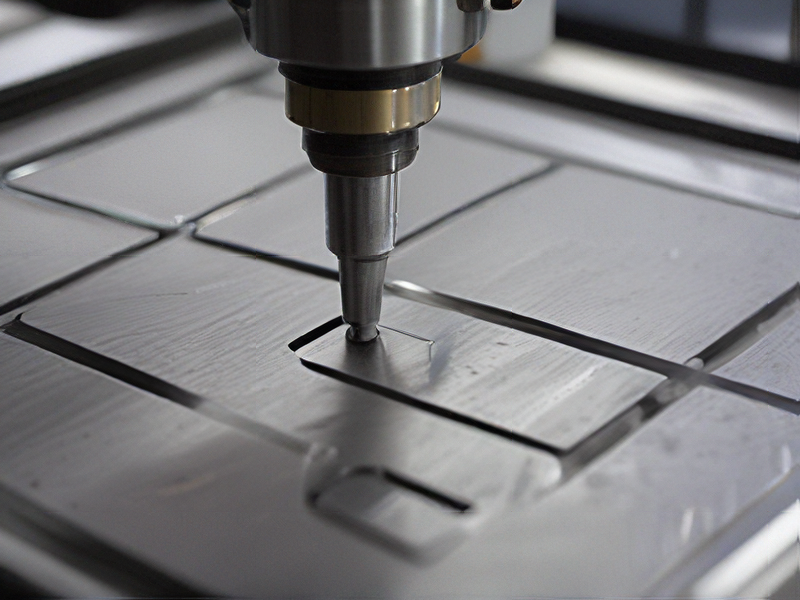
Tips for Procurement and Considerations when Purchasing from cnc for metal
Tips for Procurement and Considerations when Purchasing from CNC for Metal
1. Define Requirements Clearly: Specify the type of metal, tolerances, dimensions, and finishes needed. Include any certifications or standards the metal must meet.
2. Supplier Research: Evaluate potential CNC suppliers based on their reputation, experience, and capacity to handle your specific requirements. Look for reviews, case studies, and testimonials.
3. Quality Assurance: Ensure the supplier has robust quality control processes. Request samples or prototypes to verify their workmanship and adherence to specifications.
4. Technology and Capabilities: Confirm that the supplier’s CNC machines are capable of handling the materials and complexities of your design. Advanced machinery can offer better precision and faster turnaround times.
5. Cost and Budgeting: Obtain detailed quotes from multiple suppliers, including costs for setup, production, and finishing. Consider the total cost of ownership, including potential savings from improved quality and efficiency.
6. Lead Times and Delivery: Clarify the supplier’s lead times and their ability to meet your deadlines. Reliable delivery schedules are crucial to avoid production delays.
7. Communication and Support: Opt for suppliers who offer excellent customer service and are easy to communicate with. This ensures smooth project management and quick resolution of any issues.
8. Intellectual Property (IP) Protection: Ensure that your designs and proprietary information are protected. Review the supplier’s confidentiality agreements and IP policies.
9. Logistics and Location: Consider the supplier’s location in relation to your business. Local suppliers may offer advantages in terms of shipping costs and lead times, while overseas suppliers might offer cost benefits but longer delivery times.
10. Sustainability and Compliance: Check that the supplier adheres to environmental regulations and ethical standards. Sustainable practices can be a key differentiator and align with corporate social responsibility goals.
By following these tips, you can make informed decisions, ensuring that your procurement process is efficient, cost-effective, and aligned with your quality standards.
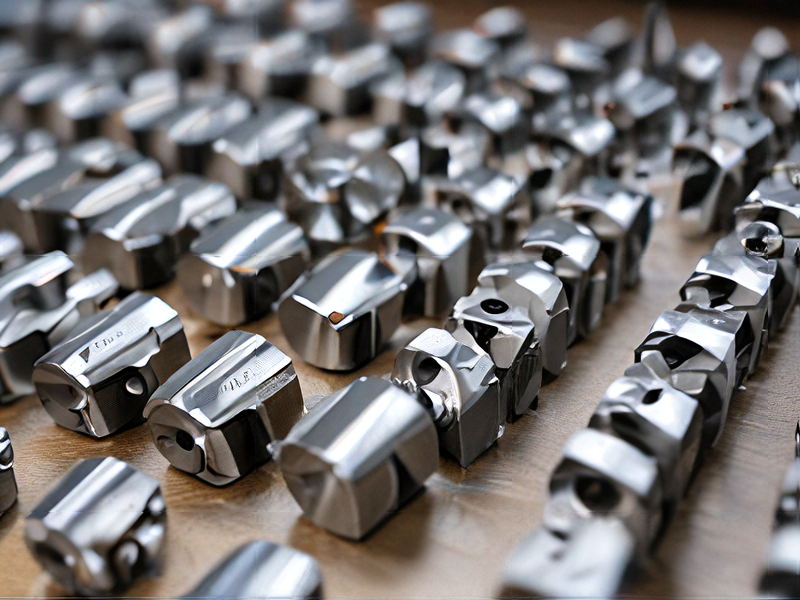
FAQs on Sourcing and Manufacturing from cnc for metal in China
Certainly! When sourcing CNC manufacturing services for metal in China, consider the following FAQs:
1. How do I find a reliable CNC manufacturer in China?
– Utilize online platforms like Alibaba or Made-in-China for initial searches. Seek recommendations from industry peers or engage sourcing agents based in China for their expertise.
2. What factors should I consider when choosing a CNC manufacturer?
– Evaluate their experience with metal CNC machining, quality certifications (ISO, AS9100, etc.), production capacity, and client references. Assess their communication proficiency in English and technical expertise.
3. What are the typical lead times for CNC manufacturing in China?
– Lead times vary based on complexity and volume but generally range from 2-8 weeks for production. Factor in additional time for shipping and customs clearance.
4. How can I ensure quality control when manufacturing in China?
– Insist on detailed quality agreements and conduct regular inspections during production. Consider hiring a third-party quality control agency or visit the manufacturer’s facilities if feasible.
5. What are the payment terms usually accepted by Chinese CNC manufacturers?
– Common terms include a deposit (30-50%) upfront with the balance paid upon completion or before shipment. Negotiate terms that align with your risk tolerance and the manufacturer’s policies.
6. How can I protect my intellectual property (IP) when outsourcing to China?
– Sign non-disclosure agreements (NDAs) and ensure your contract includes IP protection clauses. Consider registering patents or trademarks in China for additional security.
7. What are the advantages of sourcing CNC manufacturing from China?
– Cost-effectiveness due to lower labor and production costs, access to advanced CNC technology, and flexibility in production volumes.
Navigating CNC manufacturing in China requires thorough research, clear communication, and diligent oversight to ensure successful outcomes and mitigate risks associated with international sourcing.
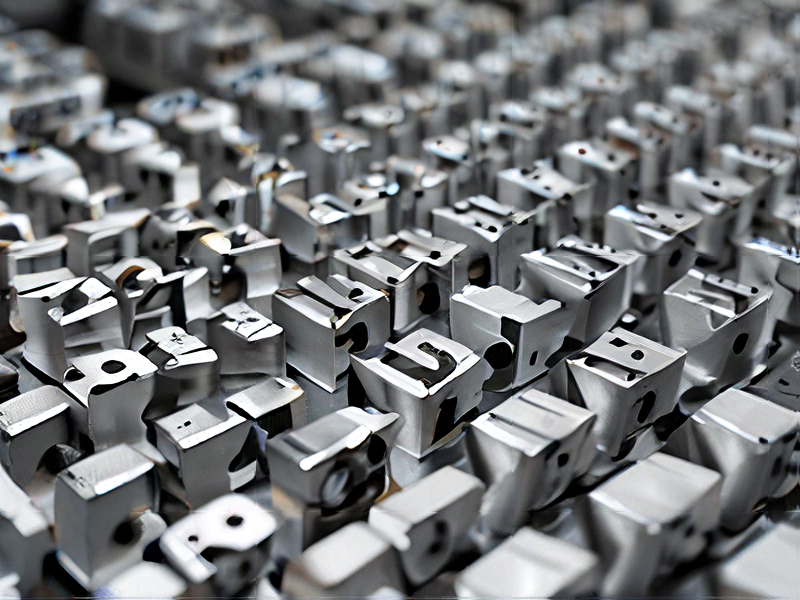