Technology and Applications of cnc lathes
CNC lathes, or Computer Numerical Control lathes, are advanced machine tools that automate the process of shaping materials, predominantly metals and plastics, by imparting rotational motion to the workpiece. The integration of computer technology allows CNC lathes to execute complex designs with high precision and repeatability, which is a significant advancement over traditional manual lathes.
Key technologies in CNC lathes include programmable logic controllers (PLC), servo motors, and advanced software for designing and simulating parts. The use of CAD/CAM systems enables engineers to create intricate designs that the CNC lathe executes with minimal human intervention. This enhances efficiency and reduces the likelihood of human error.
Applications of CNC lathes span various industries, from aerospace and automotive to medical devices and consumer electronics. In the aerospace sector, they are crucial for manufacturing components with tight tolerances and lightweight materials. In automotive production, CNC lathes efficiently produce parts like shafts, brackets, and pulleys.
Medical device manufacturing benefits from CNC lathe technology by enabling the production of custom implants and surgical instruments at precise specifications. Additionally, the versatility of CNC lathes allows for multi-tasking operations, including turning, drilling, and milling, all in a single setup.
Overall, CNC lathes play a vital role in modern manufacturing, facilitating rapid prototyping, reducing lead times, and enabling mass production of high-quality precision components. Their ability to adapt to various materials and designs continues to drive innovation across multiple sectors, making them indispensable in today’s industrial landscape.
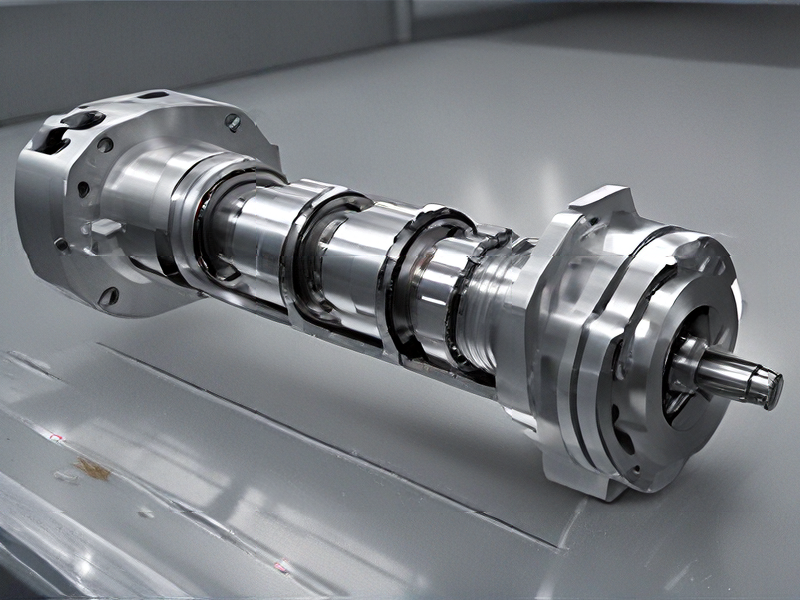
Quality Testing Methods for cnc lathes and how to control quality
Quality testing methods for CNC lathes are essential for ensuring precision, accuracy, and reliability in machined parts. Here are some effective approaches:
1. Dimensional Measurement: Utilize precision measuring tools such as calipers, micrometers, and coordinate measuring machines (CMM) to check critical dimensions against design specifications. Regularly calibrate measuring instruments to maintain accuracy.
2. Visual Inspection: Conduct visual checks to identify surface defects, tool marks, or inconsistencies. Use magnifying tools for detailed examination.
3. Tool Wear Monitoring: Regularly inspect cutting tools for wear and damage. Implement a preventive maintenance program to replace tools before they affect quality.
4. Statistical Process Control (SPC): Collect data during the machining process and analyze it to identify variations and trends. Control charts can help in monitoring process stability and capability.
5. First Article Inspection (FAI): After setting up a new job, perform a thorough inspection of the first piece produced to ensure it meets all specifications before commencing full production.
6. Machine Calibration: Regularly calibrate CNC machines to maintain their precision. Check parameters like spindle speed, tool offsets, and positional accuracy.
To control quality effectively:
– Implement Standard Operating Procedures (SOPs) for each machining process.
– Train operators on quality standards and the importance of adherence to practices.
– Maintain clear documentation of inspections and measurements to facilitate traceability and audits.
– Foster a culture of continuous improvement by encouraging feedback and regular reviews of processes and outcomes.
By combining these methods and controls, manufacturers can ensure that CNC lathe operations produce high-quality, consistent parts that meet customer expectations.

Tips for Procurement and Considerations when Purchasing from cnc lathes
When purchasing CNC lathes, there are several key considerations to ensure you make an informed decision that aligns with your production needs and budget.
1. Define Your Requirements: Identify the types of materials, part sizes, and tolerances you will be working with. Consider whether you need a CNC lathe for high-volume production or low-volume, complex parts.
2. Evaluate Precision and Accuracy: Look into the machine’s specifications regarding its precision and accuracy. Higher precision can lead to better quality parts but may also come at a higher cost.
3. Consider Machine Features: Assess essential features such as spindle speed, tool capacity, and axis configuration (e.g., 2-axis or 3-axis). Additional features like live tooling or sub-spindles may enhance productivity.
4. Brand Reputation and Support: Research the reputation of manufacturers. Consider the availability of technical support, warranty, and ease of getting spare parts.
5. Budget and Total Cost of Ownership: While initial purchase price is critical, factor in maintenance, tooling, operational costs, and energy consumption over time. A lower upfront cost might lead to higher operational expenses.
6. Floor Space and Setup: Ensure that the machine fits within your production area. Consider any additional requirements for ventilation, electrical capacity, and accessibility for setup and maintenance.
7. Demo and Trial Runs: Whenever possible, request a machine demonstration or trial run to evaluate its performance firsthand. This can reveal insights about usability and production capabilities.
8. Check User Reviews and Testimonials: Research user experiences to gauge reliability and performance in real-world applications.
By considering these factors, you can make a more informed choice that enhances your production efficiency and meets your business goals.

FAQs on Sourcing and Manufacturing from cnc lathes in China
FAQs on Sourcing and Manufacturing CNC Lathes from China
1. What types of CNC lathes can I source in China?
China offers a wide range of CNC lathes, including vertical and horizontal models, multi-axis lathes, and specialized machines for specific industries.
2. How do I find a reliable supplier?
Start by researching manufacturers through platforms like Alibaba, Made-in-China, or Global Sources. Check reviews, ratings, and request references. It’s advisable to visit factories, if possible, or consider third-party inspections.
3. What certifications should a supplier have?
Look for ISO certifications, CE markings, and product-specific certifications such as CB or UL, which ensure compliance with international standards.
4. How do I handle shipping and customs?
Negotiate Incoterms with your supplier (e.g., FOB or CIF). Consider hiring a freight forwarder for assistance with logistics, shipping, and customs clearance to avoid delays.
5. What are the payment terms?
Common payment practices include a 30% deposit with the order and the remaining 70% before shipment. Ensure you use secure payment methods and consider escrow services for higher-value transactions.
6. What is the typical lead time for CNC lathes?
Lead times can vary, typically ranging from 30 to 90 days depending on the complexity of the machine and the manufacturer’s workload.
7. Can I customize my CNC lathe design?
Many Chinese manufacturers offer customization options. Be clear about your specifications and ensure you have a detailed agreement to avoid misunderstandings.
8. What after-sales support can I expect?
Ask about warranty terms, spare parts availability, and technical support. Reliable suppliers often provide manuals and training, either on-site or online.
