Technology and Applications of cnc metal machining
CNC (Computer Numerical Control) metal machining revolutionizes manufacturing by automating precision machining processes. Using CAD (Computer-Aided Design) software, engineers create digital models of components, which are then translated into programming code (G-code) that CNC machines understand. This technology offers unparalleled accuracy and repeatability in shaping metals such as steel, aluminum, and titanium.
Applications span various industries:
1. Automotive: CNC machining produces engine components, chassis parts, and intricate prototypes with tight tolerances critical for performance and safety.
2. Aerospace: Critical parts like turbine blades and structural components benefit from CNC’s ability to handle exotic materials and complex geometries, ensuring lightweight yet durable designs.
3. Medical: Prosthetics, surgical instruments, and implants require precise machining for biocompatibility and functional reliability.
4. Electronics: CNC fabricates housings, heatsinks, and connectors, ensuring components fit precisely within devices while optimizing heat dissipation and electrical performance.
5. Defense: From firearm components to specialized equipment, CNC machining ensures parts meet stringent military specifications for reliability and durability.
Advantages include reduced lead times, increased production flexibility, and minimized human error. CNC machines range from simple mills and lathes to multi-axis machining centers capable of simultaneous cutting in multiple directions. High-speed machining further enhances efficiency without compromising precision.
Future trends include the integration of AI for predictive maintenance and real-time process optimization, as well as advancements in additive manufacturing (3D printing) combined with CNC for hybrid manufacturing processes.
In conclusion, CNC metal machining’s versatility and precision continue to drive innovation across industries, shaping the future of manufacturing with efficiency and quality at its core.
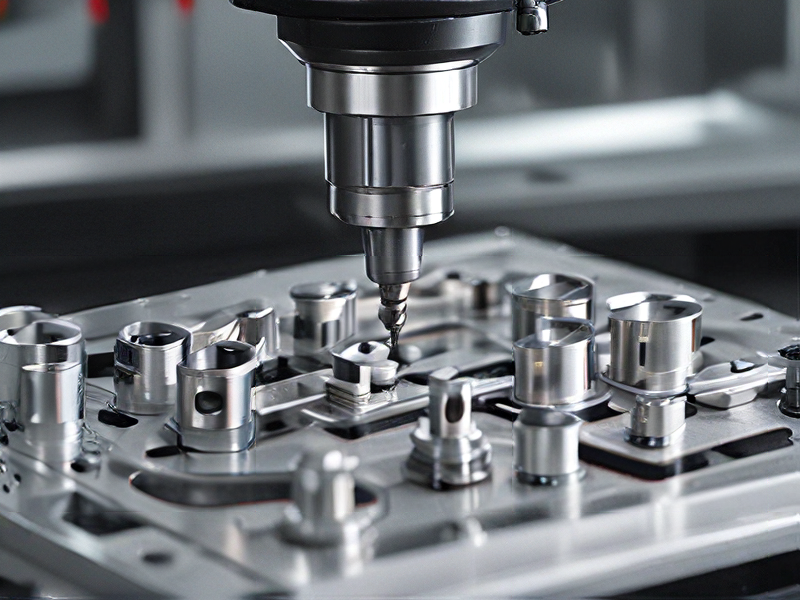
Quality Testing Methods for cnc metal machining and how to control quality
Quality testing methods for CNC metal machining typically involve a combination of in-process inspections and final product checks to ensure precision and consistency. Here are some key methods:
1. Dimensional Inspection: Using precision tools such as calipers, micrometers, and coordinate measuring machines (CMMs) to verify part dimensions against design specifications.
2. Surface Finish Analysis: Measuring surface roughness using profilometers to ensure the required smoothness or texture is achieved.
3. Visual Inspection: Examining parts visually for defects such as burrs, scratches, or irregularities that could affect functionality or aesthetics.
4. Non-Destructive Testing (NDT): Techniques like ultrasonic testing or magnetic particle inspection to detect internal flaws or defects without damaging the part.
5. Statistical Process Control (SPC): Monitoring key process parameters (e.g., cutting speed, tool wear) statistically to ensure they remain within acceptable limits, reducing variability.
6. First Article Inspection (FAI): Thorough inspection of the first manufactured part to verify all requirements are met before proceeding with full production.
To control quality effectively:
– Establish Clear Specifications: Define precise tolerances and quality standards for each part.
– Implement Regular Inspections: Conduct inspections at critical stages of production to catch issues early.
– Maintain Equipment: Calibrate measuring tools and CNC machines regularly to ensure accuracy.
– Train Personnel: Provide training on quality standards, inspection methods, and equipment operation.
– Document and Analyze Data: Keep records of inspection results and analyze trends to identify potential improvements or issues.
By integrating these methods and controls into the CNC machining process, manufacturers can consistently produce high-quality metal components that meet customer expectations and regulatory requirements.
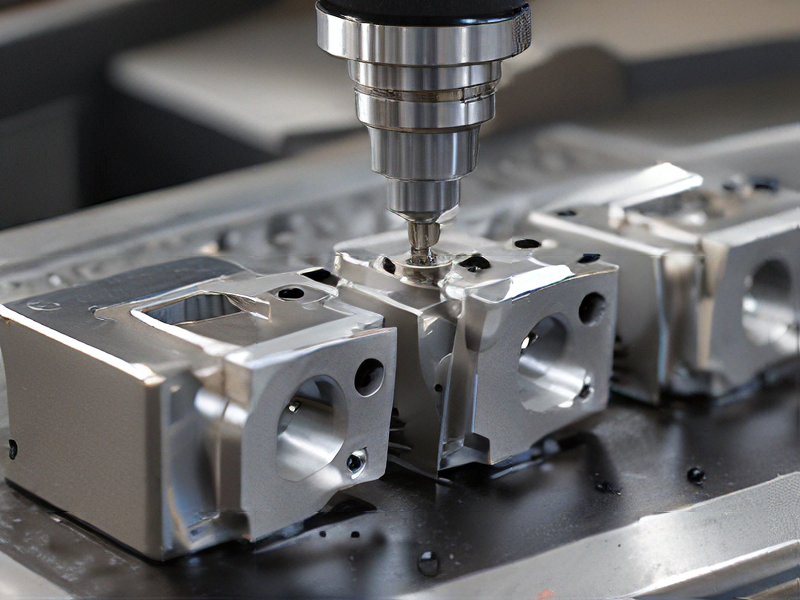
Tips for Procurement and Considerations when Purchasing from cnc metal machining
When procuring from CNC metal machining suppliers, consider the following tips and considerations to ensure quality and cost-effectiveness:
1. Define Requirements Clearly:
– Specify material type, dimensions, tolerances, surface finishes, and any other critical attributes.
– Provide detailed technical drawings and, if possible, 3D models to avoid misunderstandings.
2. Supplier Evaluation:
– Assess the supplier’s technical capabilities, equipment quality, and capacity to handle your order volume.
– Check their certifications (e.g., ISO 9001) and quality control processes.
3. Experience and Expertise:
– Choose suppliers with experience in your specific industry and project type.
– Ask for references and review their past projects.
4. Cost Considerations:
– Request detailed quotations to understand cost components like material, machining, finishing, and shipping.
– Balance cost with quality; the cheapest option might compromise the product’s durability and performance.
5. Lead Times and Delivery:
– Confirm the supplier’s ability to meet your delivery deadlines.
– Consider potential delays and plan for contingency.
6. Quality Assurance:
– Ensure the supplier performs thorough inspections and testing.
– Discuss procedures for handling defects and non-conformities.
7. Communication and Support:
– Maintain clear and open communication channels.
– Ensure the supplier is responsive and provides regular updates.
8. Intellectual Property Protection:
– Sign NDAs and ensure the supplier respects your proprietary designs and technology.
9. Logistics and Shipping:
– Consider the costs and logistics of shipping, including customs and import duties if sourcing internationally.
– Verify the packaging quality to protect parts during transit.
10. Sustainability and Compliance:
– Check the supplier’s compliance with environmental regulations and sustainability practices.
By following these tips, you can mitigate risks and ensure a smooth procurement process for CNC metal machining services.
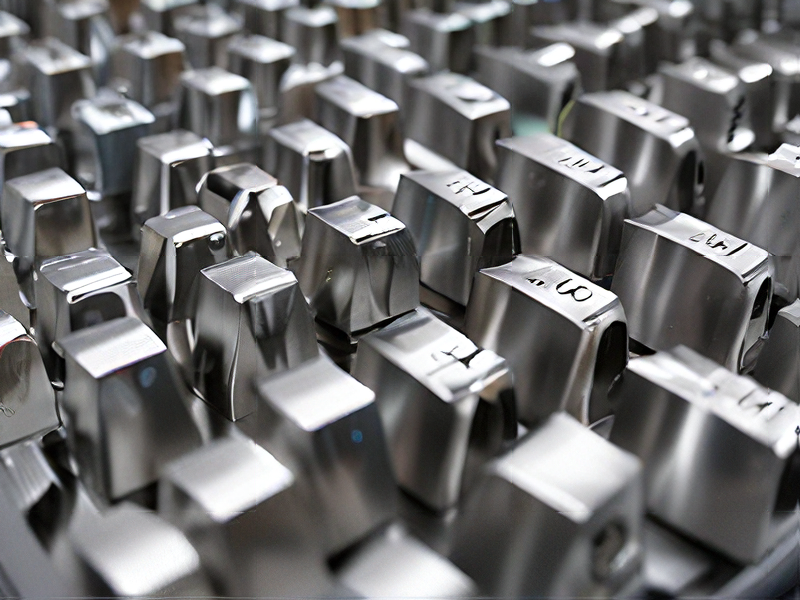
FAQs on Sourcing and Manufacturing from cnc metal machining in China
FAQs on Sourcing and Manufacturing from CNC Metal Machining in China
1. Why should I consider sourcing CNC metal machining from China?
China offers competitive pricing, high-quality manufacturing, advanced technology, and a large pool of skilled labor. Many Chinese manufacturers have ISO certifications and follow international quality standards.
2. How do I find a reliable CNC metal machining supplier in China?
Research online directories, attend trade shows, and use sourcing platforms like Alibaba and Global Sources. Look for companies with positive reviews, certifications, and experience in your specific industry.
3. What are the key factors to evaluate when choosing a supplier?
Consider their experience, quality control processes, equipment and technology, capacity, lead times, and communication skills. Visiting the factory and requesting samples can also help in the evaluation.
4. How can I ensure the quality of the machined parts?
Establish clear specifications and quality standards in your contracts. Regular inspections, third-party quality control services, and requesting detailed reports and samples can help maintain quality.
5. What are the typical lead times for CNC metal machining in China?
Lead times vary depending on the complexity of the parts and the supplier’s workload. Generally, it ranges from 2 to 6 weeks. Communicate your deadlines clearly and plan for potential delays.
6. How do I handle intellectual property (IP) concerns?
Sign non-disclosure agreements (NDAs) and include IP protection clauses in your contracts. Work with suppliers who have a good track record of respecting IP rights and consider working with a local IP attorney.
7. What are the common payment terms?
Common terms include a 30% deposit before production and the remaining 70% upon shipment. Letter of Credit (L/C) and Trade Assurance are also used to ensure secure transactions.
8. How do I manage logistics and shipping?
Work with experienced freight forwarders and clarify Incoterms with your supplier. Consider the costs and timelines of different shipping methods (air, sea, or rail).
9. What are the potential risks and how can I mitigate them?
Risks include quality issues, delays, and communication barriers. Mitigate these by thorough vetting, clear agreements, regular monitoring, and maintaining open communication.
10. Are there any cultural considerations when working with Chinese suppliers?
Building relationships is crucial. Show respect, understand local business etiquette, and be patient with negotiations and decision-making processes.
These FAQs cover essential aspects to help ensure a successful sourcing experience in CNC metal machining from China.
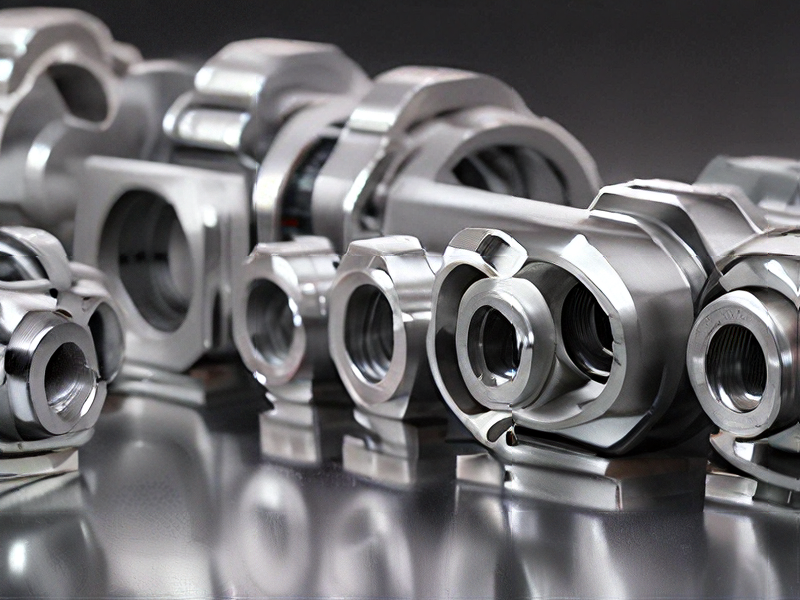