Technology and Applications of cnc resources
Computer Numerical Control (CNC) technology revolutionizes manufacturing by automating processes traditionally operated by manual control. It utilizes computerized systems to control machine tools, such as lathes, mills, routers, and grinders, with precision and repeatability. CNC finds widespread application across various industries, including aerospace, automotive, electronics, and medical devices.
Key applications include:
1. Precision Machining: CNC machines execute complex cuts and shapes with high accuracy, crucial for manufacturing components with tight tolerances.
2. Mass Production: Enables consistent production of identical parts, optimizing efficiency and reducing labor costs.
3. Prototyping: Rapid prototyping allows for quick iteration and testing of designs before full-scale production.
4. Customization: Facilitates customized manufacturing by programming machines to produce unique variations of products without retooling.
5. Automation: Reduces manual intervention, enhances safety, and allows machines to operate continuously, improving productivity.
6. Multi-axis Machining: CNC systems can control multiple axes simultaneously, enabling intricate geometries and contours that are challenging with manual methods.
7. Integration with CAD/CAM: CNC machines interface seamlessly with Computer-Aided Design (CAD) and Computer-Aided Manufacturing (CAM) software, translating digital designs into physical products efficiently.
8. Versatility: Used for cutting, drilling, grinding, and additive manufacturing processes like 3D printing, expanding its applicability across different materials and industries.
Overall, CNC technology optimizes production processes, enhances product quality, and supports innovation in manufacturing through its precision, versatility, and automation capabilities. Its continual advancement drives the evolution of modern manufacturing practices toward greater efficiency and customization.
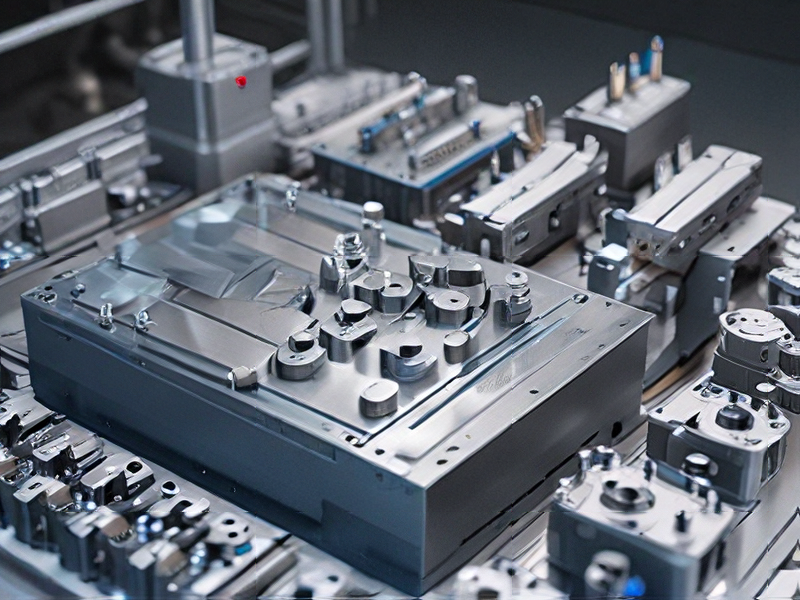
Quality Testing Methods for cnc resources and how to control quality
Quality testing for CNC (Computer Numerical Control) resources involves several methods to ensure precision and reliability in manufacturing. Here are some key methods and controls:
1. First Article Inspection (FAI):
– Method: Inspect the first piece produced against design specifications.
– Control: Verify dimensions, material, and other critical features before full-scale production.
2. In-Process Inspection:
– Method: Regular checks during the manufacturing process.
– Control: Use calibrated measuring tools like calipers, micrometers, and gauges to check dimensions and tolerances.
3. Statistical Process Control (SPC):
– Method: Apply statistical methods to monitor and control the production process.
– Control: Analyze data from production to identify trends and deviations, ensuring consistent quality.
4. Coordinate Measuring Machine (CMM):
– Method: Use CMMs for precise measurement of complex geometries.
– Control: Automate measurements and compare against CAD models to ensure accuracy.
5. Gage Repeatability and Reproducibility (R&R):
– Method: Assess the measurement system for consistency.
– Control: Perform tests to ensure that measuring instruments and personnel yield consistent results.
6. Material Testing:
– Method: Test the material properties such as hardness, tensile strength, and chemical composition.
– Control: Ensure materials meet required specifications before and during production.
7. Non-Destructive Testing (NDT):
– Method: Techniques like ultrasonic, magnetic particle, and dye penetrant testing.
– Control: Detect surface and subsurface defects without damaging the part.
8. Final Inspection:
– Method: Thorough check of the final product.
– Control: Ensure all parts meet the final specifications before delivery.
9. ISO 9001 Standards:
– Method: Implement and maintain ISO 9001 quality management system.
– Control: Regular audits and continuous improvement practices to uphold quality standards.
By integrating these methods, CNC resource quality can be meticulously controlled, ensuring high standards and reliability in manufacturing.
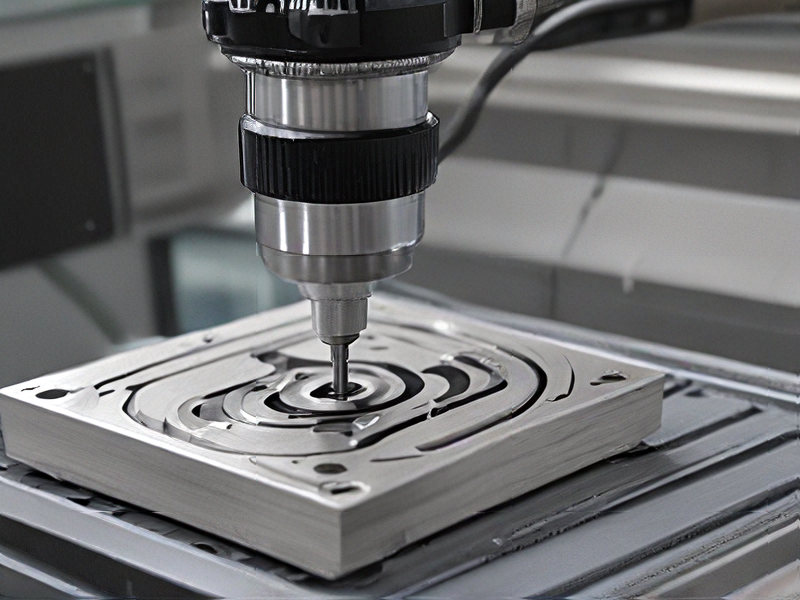
Tips for Procurement and Considerations when Purchasing from cnc resources
When procuring from CNC (Computer Numerical Control) resources, consider several key factors to ensure efficiency and quality:
1. Supplier Reliability: Choose suppliers with a proven track record in CNC machining. Check references, reviews, and industry reputation to ensure reliability.
2. Technical Capabilities: Evaluate the CNC equipment and technology offered by the supplier. Ensure they have the capability to handle your specific machining requirements.
3. Quality Assurance: Seek suppliers with robust quality control measures. Look for certifications such as ISO standards to guarantee consistent quality.
4. Cost Efficiency: Balance cost considerations with quality. Compare quotes from multiple suppliers and consider long-term value rather than just initial costs.
5. Lead Times and Flexibility: Assess the supplier’s ability to meet your delivery deadlines. Look for flexibility in production schedules to accommodate changes or urgent orders.
6. Communication and Support: Choose suppliers who communicate effectively and provide responsive customer support. Clear communication channels are crucial for addressing issues promptly.
7. Material Selection: Verify the range of materials the supplier can work with. Ensure they have expertise in machining the materials required for your project.
8. Customization and Prototyping: If needed, inquire about their ability to handle custom projects or provide prototyping services. This is crucial for testing designs before full production.
9. Sustainability Practices: Consider suppliers who adhere to sustainable manufacturing practices if environmental impact is a concern for your organization.
10. Contractual Agreements: Clarify terms and conditions related to pricing, delivery, quality standards, and intellectual property rights in a formal contract.
By prioritizing these considerations, you can enhance your procurement process when purchasing from CNC resources, ensuring optimal outcomes for your projects.
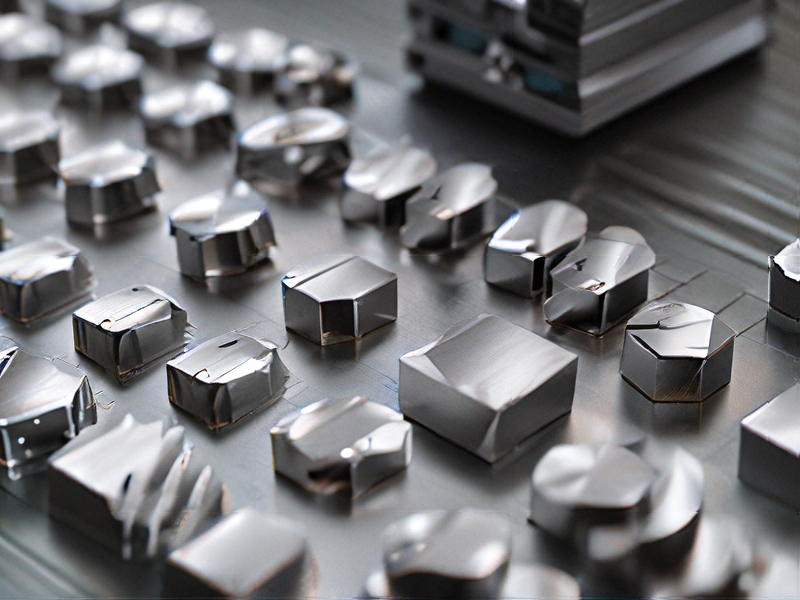
FAQs on Sourcing and Manufacturing from cnc resources in China
Certainly! When sourcing and manufacturing from CNC resources in China, here are some common FAQs:
1. How do I find a reliable CNC manufacturer in China?
– Utilize online platforms like Alibaba or Made-in-China to search for suppliers. Look for companies with verified credentials and positive customer reviews.
2. What should I consider when choosing a CNC manufacturer?
– Evaluate their experience, production capabilities, quality control measures, and communication skills. Request samples and check their adherence to international standards.
3. How can I ensure quality control during manufacturing?
– Specify detailed product requirements, conduct regular inspections during production, and consider hiring a third-party quality assurance service if necessary.
4. What are the typical lead times for CNC manufacturing in China?
– Lead times vary based on complexity and quantity. Generally, expect anywhere from a few weeks to a couple of months. Discuss timelines upfront with your manufacturer.
5. How do I handle intellectual property (IP) concerns?
– Sign non-disclosure agreements (NDAs) and clearly outline IP protection in your contracts. Work with reputable manufacturers with a history of respecting intellectual property rights.
6. What are the payment terms usually accepted by Chinese CNC manufacturers?
– Common payment terms include T/T (Telegraphic Transfer), L/C (Letter of Credit), and occasionally, PayPal for smaller transactions. Negotiate terms that align with your risk tolerance.
7. How do I manage logistics and shipping from China?
– Coordinate with your manufacturer to arrange shipping via air, sea, or courier. Factor in shipping costs, customs duties, and transportation to your final destination.
Navigating sourcing and manufacturing from CNC resources in China requires thorough research, clear communication, and diligent quality assurance practices to ensure a successful partnership.
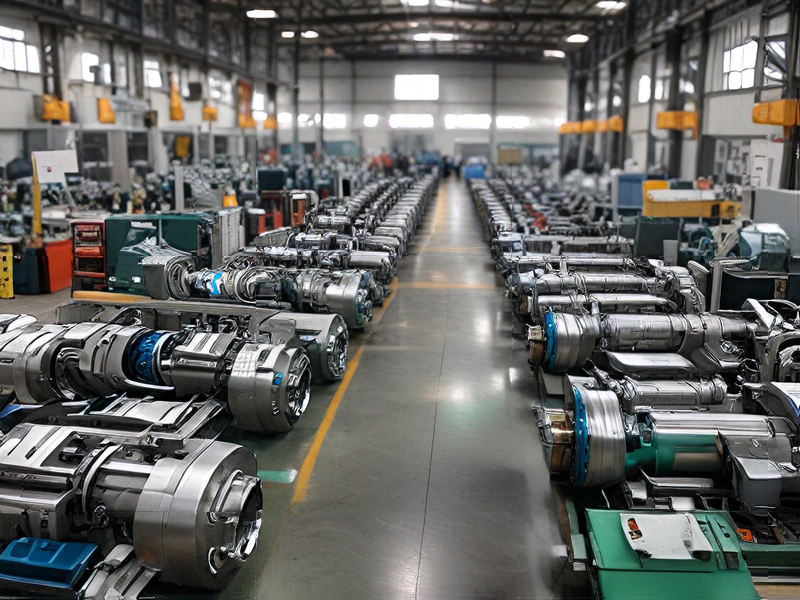