Technology and Applications of composition of steel and stainless steel
Steel is an alloy primarily composed of iron and carbon, with varying amounts of other elements like manganese, chromium, nickel, and molybdenum. The carbon content typically ranges from 0.2% to 2.1%. Steel’s composition can be adjusted to enhance properties such as strength, ductility, and resistance to corrosion and wear.
Stainless steel is a specific type of steel containing at least 10.5% chromium, which provides corrosion resistance. It may also include nickel, molybdenum, and other elements. The main types of stainless steel are:
1. Austenitic Stainless Steel: Contains high levels of chromium and nickel, making it highly corrosion-resistant and non-magnetic. Examples include 304 and 316 stainless steels.
2. Ferritic Stainless Steel: Contains chromium but little or no nickel, making it magnetic and less expensive. Common grades include 430 and 409.
3. Martensitic Stainless Steel: Contains chromium and higher carbon content, making it hardenable by heat treatment. Examples include 410 and 420 grades.
4. Duplex Stainless Steel: Combines austenitic and ferritic structures, offering high strength and corrosion resistance. Examples include 2205 and 2507 grades.
Applications:
1. Construction: Steel is used in building frameworks, bridges, and infrastructure due to its high strength and durability.
2. Automotive: Both steel and stainless steel are used in car bodies, exhaust systems, and engine components, providing strength, durability, and corrosion resistance.
3. Medical Devices: Stainless steel is used for surgical instruments, implants, and medical devices due to its biocompatibility and resistance to sterilization processes.
4. Kitchenware: Stainless steel is popular for cookware, cutlery, and appliances, offering ease of cleaning and resistance to corrosion.
5. Industrial Equipment: Used in manufacturing machinery, pipelines, and chemical processing plants for its strength and resistance to high temperatures and corrosive environments.
In summary, the specific composition of steel and stainless steel is tailored to meet the demands of various applications, optimizing properties such as strength, durability, and corrosion resistance.
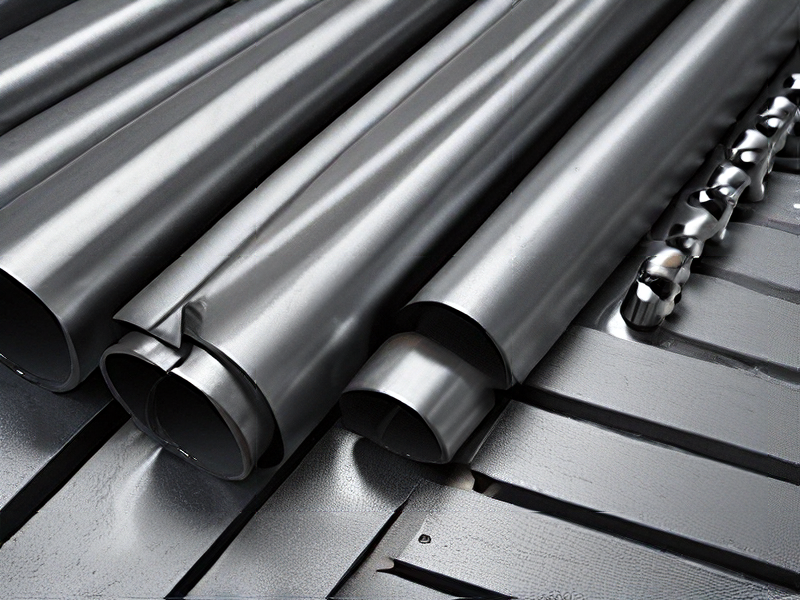
Quality Testing Methods for composition of steel and stainless steel and how to control quality
Quality testing methods for steel and stainless steel compositions typically involve several key techniques to ensure material integrity and performance:
1. Chemical Composition Analysis: Utilizing methods such as X-ray fluorescence (XRF) or optical emission spectrometry (OES) to verify the elemental composition, ensuring it meets specified standards.
2. Mechanical Properties Testing: Includes tests like tensile strength, hardness testing (Rockwell, Brinell), and impact resistance testing to assess material strength and durability.
3. Microstructure Examination: Using metallographic techniques such as microscopy to evaluate grain structure, inclusion content, and overall microstructural integrity.
4. Corrosion Resistance Testing: Particularly crucial for stainless steel, involves tests like salt spray testing (ASTM B117) to simulate environmental conditions and assess corrosion resistance.
5. Non-Destructive Testing (NDT): Techniques like ultrasonic testing (UT), magnetic particle inspection (MPI), and dye penetrant testing (PT) to detect surface and subsurface defects without damaging the material.
Quality control involves implementing these methods at various stages of production:
– Raw Material Inspection: Ensuring incoming steel meets specified chemical and mechanical properties.
– In-Process Testing: Monitoring during fabrication processes to detect any deviations early.
– Final Product Inspection: Comprehensive testing of finished products to verify compliance with customer requirements and industry standards.
Effective quality control relies on rigorous adherence to testing protocols, calibration of equipment, and skilled interpretation of results to maintain consistent material quality and performance.
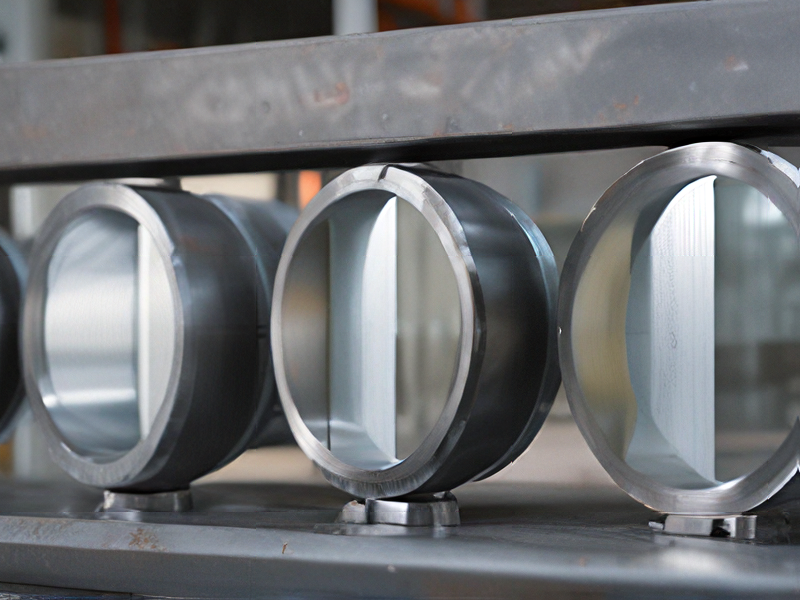
Tips for Procurement and Considerations when Purchasing from composition of steel and stainless steel
When procuring steel and stainless steel, several key considerations can ensure optimal selection and purchasing decisions:
1. Material Composition: Understand the specific composition requirements for your application. Steel alloys vary significantly in terms of carbon content, alloying elements (like chromium, nickel, and molybdenum for stainless steel), which directly impact properties such as strength, corrosion resistance, and machinability.
2. Quality Standards: Ensure materials meet recognized quality standards (e.g., ASTM for steel, ASTM A240 for stainless steel). Certification ensures materials conform to specified mechanical, chemical, and dimensional properties.
3. Application Requirements: Assess the environmental conditions (e.g., exposure to moisture, chemicals, temperature variations) the material will endure. Stainless steel, with its corrosion resistance, is ideal for harsh environments compared to carbon steel.
4. Cost Considerations: Balance material cost against performance requirements. Stainless steel typically costs more than carbon steel but offers superior longevity and resistance to corrosion, potentially reducing maintenance and replacement costs over time.
5. Supplier Reliability: Choose reputable suppliers with a track record for quality and timely delivery. Ensure they can provide material certifications and traceability.
6. Fabrication and Machining: Consider ease of fabrication and machining. Stainless steel, while corrosion-resistant, can be more challenging to work with compared to carbon steel due to its hardness and toughness.
7. Lifecycle Cost: Factor in the total lifecycle cost, including maintenance, repair, and replacement. Stainless steel’s durability often makes it cost-effective in the long term despite higher initial costs.
8. Environmental Impact: Evaluate environmental considerations such as recyclability and sustainability of the materials. Stainless steel, being fully recyclable, has a lower environmental impact compared to some other materials.
By carefully evaluating these factors, procurement professionals can make informed decisions that align with performance requirements, cost constraints, and environmental considerations when purchasing steel and stainless steel materials.
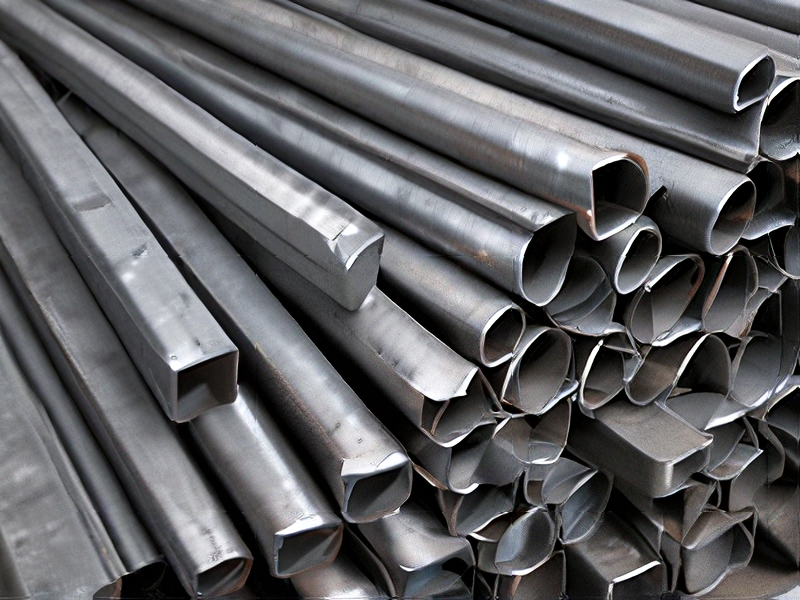
FAQs on Sourcing and Manufacturing from composition of steel and stainless steel in China
FAQs on Sourcing and Manufacturing Steel and Stainless Steel in China
1. What are the primary components of steel and stainless steel?
– Steel: Primarily composed of iron and carbon, with other elements such as manganese, phosphorus, sulfur, and silicon in smaller amounts.
– Stainless Steel: Contains iron, carbon, and at least 10.5% chromium, which provides corrosion resistance. Additional elements may include nickel, molybdenum, and manganese.
2. What are the benefits of sourcing steel from China?
– Cost Efficiency: Lower production costs compared to Western countries.
– Advanced Technology: Access to modern manufacturing techniques and technologies.
– High Production Capacity: China’s large-scale production capabilities ensure timely delivery and bulk order fulfillment.
3. Are there any quality concerns when sourcing from China?
– Quality Variability: While many Chinese manufacturers produce high-quality steel, some may not meet international standards. It’s essential to conduct thorough due diligence.
– Certifications: Ensure suppliers have relevant certifications (e.g., ISO 9001) and comply with industry standards.
4. How can I ensure the quality of steel and stainless steel from Chinese manufacturers?
– Supplier Audits: Conduct regular audits and inspections.
– Third-Party Testing: Use third-party labs to verify material composition and quality.
– Quality Control Agreements: Include specific quality control measures in contracts.
5. What are the typical lead times for steel and stainless steel manufacturing in China?
– Lead Times: Generally range from 30 to 60 days, depending on the order size and complexity. Custom orders may require longer lead times.
6. What logistical considerations should I be aware of?
– Shipping: Consider shipping times, costs, and potential delays.
– Customs: Be aware of import regulations and duties in your country.
– Incoterms: Clearly define Incoterms (e.g., FOB, CIF) to avoid misunderstandings.
7. What are the common challenges in sourcing from China?
– Communication Barriers: Language and cultural differences can lead to misunderstandings.
– Intellectual Property (IP) Risks: Protect IP through patents, trademarks, and confidentiality agreements.
– Regulatory Compliance: Ensure compliance with both Chinese regulations and international standards.
8. How can I find reliable steel and stainless steel manufacturers in China?
– Trade Shows: Attend trade shows like the Canton Fair to meet potential suppliers.
– Online Platforms: Use platforms like Alibaba and Global Sources, but verify supplier credibility.
– Industry Referrals: Seek recommendations from industry peers and associations.
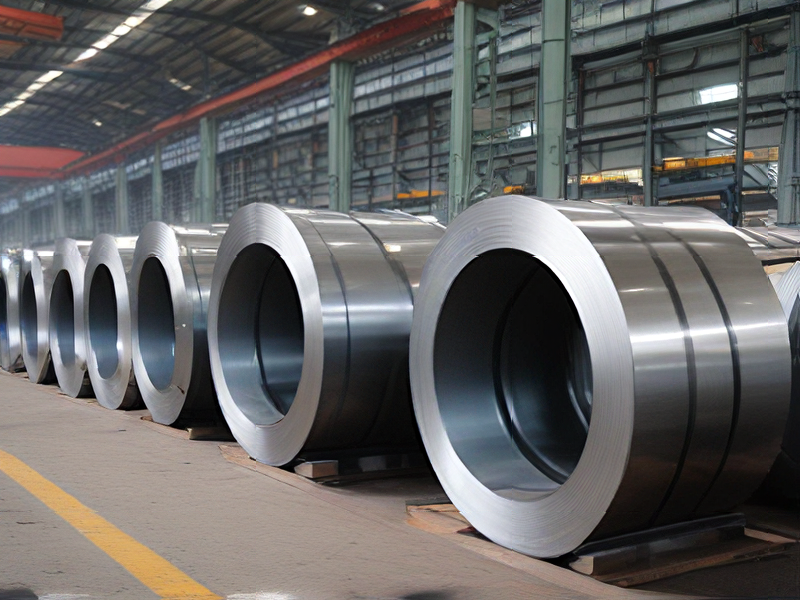