Technology and Applications of custom casting
Custom casting involves the process of creating metal components or parts that are tailored to specific designs or requirements. This manufacturing technique is widely used across various industries due to its ability to produce intricate and unique shapes that are not easily achievable through other methods.
Technology:
Custom casting typically involves several key technologies:
1. Pattern Making: The process starts with creating a pattern, which is a replica of the desired part, often made from wood, plastic, or metal. This pattern is used to create the mold into which the molten metal will be poured.
2. Mold Making: The pattern is used to make a mold, usually by packing sand, plaster, or ceramic material around it. This mold is then hardened to create a cavity that will shape the molten metal into the desired form.
3. Casting: Once the mold is prepared, the molten metal is poured into it and allowed to cool and solidify. The mold is then removed to reveal the finished casting.
4. Finishing: Post-casting processes such as grinding, machining, and surface treatment are often applied to achieve the final desired shape, dimensions, and surface finish.
Applications:
Custom casting finds applications across various industries, including:
– Automotive: Engine components, transmission parts, and decorative elements.
– Aerospace: Aircraft engine parts, structural components, and specialized tools.
– Industrial Equipment: Pump housings, valves, and machine tool components.
– Art and Sculpture: Custom sculptures, artistic pieces, and architectural elements.
– Medical: Orthopedic implants, surgical instruments, and dental prosthetics.
Advancements in materials science and casting techniques, such as investment casting and 3D printing for patterns, continue to expand the capabilities and applications of custom casting. This versatility makes it a preferred choice for manufacturers looking to create complex, high-quality metal parts tailored to specific needs.
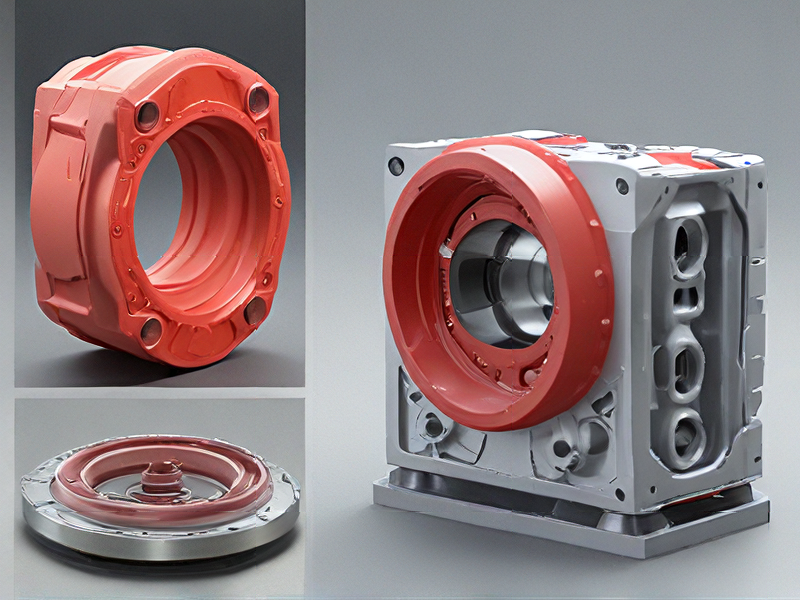
Quality Testing Methods for custom casting and how to control quality
Quality testing methods for custom casting typically include several key processes to ensure the final product meets specifications:
1. Visual Inspection: Visual examination ensures the casting’s surface finish, dimensions, and overall appearance align with requirements.
2. Dimensional Inspection: Using precision tools like calipers, micrometers, or coordinate measuring machines (CMMs) verifies critical dimensions against technical drawings.
3. Non-Destructive Testing (NDT): Techniques like ultrasonic testing (UT), radiographic testing (RT), or dye penetrant testing (PT) detect internal defects without damaging the casting.
4. Mechanical Testing: Validates material strength, hardness, and other mechanical properties through tests like tensile strength tests, hardness tests (Brinell, Rockwell), or impact tests.
5. Metallurgical Analysis: Involves metallography to examine microstructures and ensure they meet required standards for grain size, porosity, and inclusion content.
6. Pressure Testing: Ensures the casting can withstand specified internal or external pressures without failure.
To control quality effectively:
– Establish Clear Specifications: Define tolerances, surface finish requirements, material standards, and testing protocols upfront.
– Supplier Qualification: Select experienced foundries with a track record of quality and reliability.
– Process Control: Monitor and document each stage of casting, from pattern making to finishing, to identify and correct deviations promptly.
– Training and Certification: Ensure staff are trained in quality control methods and maintain certifications where applicable.
– Continuous Improvement: Regularly review processes, collect feedback, and implement corrective actions to enhance quality and efficiency.
By integrating these methods and controls, manufacturers can consistently produce high-quality custom castings that meet customer expectations and industry standards.
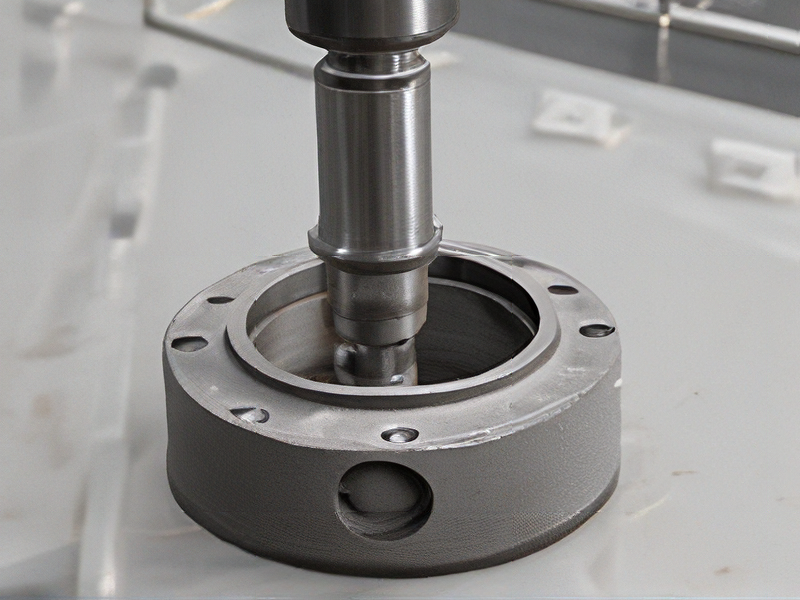
Tips for Procurement and Considerations when Purchasing from custom casting
When engaging in procurement from custom casting services, several key considerations can streamline the process and ensure successful outcomes:
1. Specifications Clarity: Clearly define your requirements in terms of materials, dimensions, tolerances, and surface finish. This clarity helps in obtaining accurate quotes and ensures the final product meets your expectations.
2. Supplier Evaluation: Assess potential suppliers based on their experience with similar projects, quality certifications (like ISO standards), and client testimonials. Request samples or visit their facilities if possible to gauge their capabilities firsthand.
3. Cost vs. Quality Balance: While cost-effectiveness is crucial, prioritize quality to avoid issues like defects or delays. Compare quotes from multiple suppliers but consider factors beyond price, such as lead times and post-delivery support.
4. Communication and Collaboration: Establish clear channels of communication and ensure the supplier understands your project timeline and milestones. Regular updates and feedback loops can prevent misunderstandings and align expectations.
5. Contract and Legal Considerations: Draft a comprehensive contract covering delivery schedules, quality standards, payment terms, and contingencies for delays or discrepancies. Legal review of terms can safeguard your interests.
6. Quality Assurance and Testing: Define acceptance criteria and specify testing protocols to validate the quality of castings before acceptance. Inspections during production stages can catch issues early, preventing costly rework.
7. Logistics and Delivery: Plan logistics for transportation and storage of castings to minimize transit risks and ensure timely delivery. Coordinate closely with the supplier to address any shipping challenges.
8. Long-term Relationship: Cultivate a partnership mindset with your supplier. Regular evaluations and feedback sessions can foster continuous improvement and reliability in future projects.
By focusing on these considerations, you can navigate procurement from custom casting services effectively, fostering successful partnerships and achieving desired project outcomes.
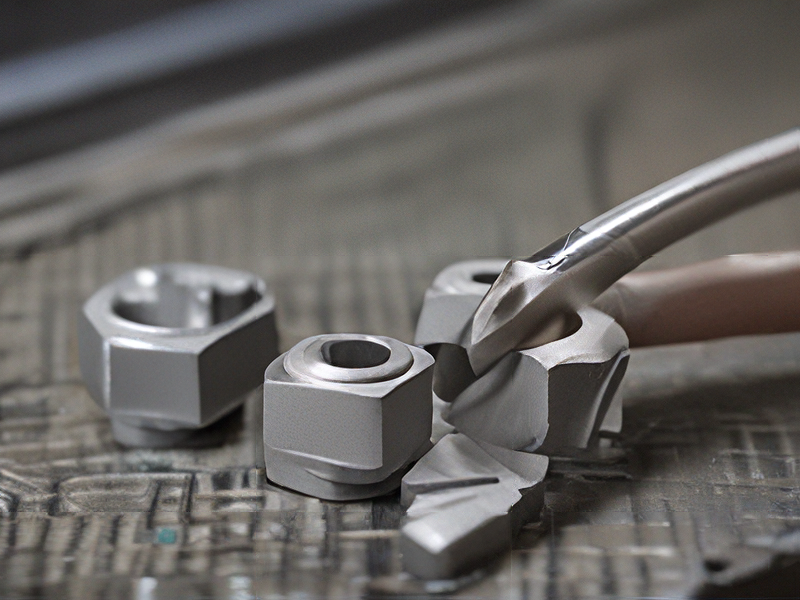
FAQs on Sourcing and Manufacturing from custom casting in China
Certainly! Here are some FAQs on sourcing and manufacturing from custom casting in China:
1. Why choose China for custom casting?
China offers competitive pricing, a wide range of material options, and expertise in manufacturing intricate designs, making it a preferred choice for custom casting.
2. How do I find a reliable manufacturer in China?
Research online directories, attend trade shows, or use sourcing platforms to find manufacturers. Verify their credentials, visit their facilities if possible, and ask for client references.
3. What materials can I use for custom casting in China?
China supports various materials such as stainless steel, aluminum, brass, and alloys like zinc and nickel. Discuss material suitability with manufacturers based on your project requirements.
4. What are the typical lead times for custom casting orders?
Lead times vary based on complexity, quantity, and manufacturer capacity. Generally, expect lead times ranging from a few weeks to several months, including design confirmation and production.
5. How can I ensure quality control in Chinese manufacturing?
Implement quality control measures like specifying tolerances, conducting inspections during production, and requesting samples before mass production. Clear communication and regular updates are crucial.
6. What are the shipping and logistics considerations?
Discuss shipping methods (air, sea, rail) with manufacturers and factor in customs procedures and tariffs. Plan for packaging requirements to ensure goods arrive safely.
7. What are the payment terms typically used in China?
Payment terms vary but often include options like T/T (Telegraphic Transfer), L/C (Letter of Credit), or Alibaba’s Trade Assurance. Negotiate terms that balance security with supplier needs.
8. How do I protect my intellectual property when sourcing from China?
Sign non-disclosure agreements (NDAs), register trademarks and patents, and work with reputable manufacturers with a proven track record of IP protection.
By addressing these FAQs, you’ll be better equipped to navigate sourcing and manufacturing from custom casting in China effectively.
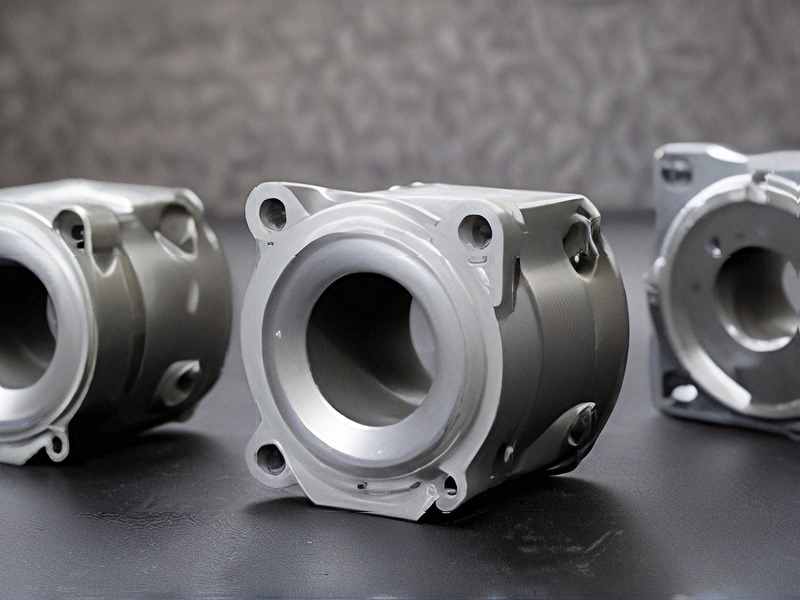