Technology and Applications of ductwork sheet metal
Ductwork sheet metal plays a critical role in HVAC (Heating, Ventilation, and Air Conditioning) systems, offering durability, efficiency, and flexibility in building infrastructure. Typically fabricated from galvanized steel, aluminum, or stainless steel, its primary function is to transport air throughout buildings, ensuring proper ventilation and climate control.
Key Applications:
1. Ventilation Systems: Ductwork distributes fresh air and removes stale air, crucial for maintaining indoor air quality in residential, commercial, and industrial settings.
2. Heating and Cooling: It facilitates the distribution of heated or cooled air from HVAC units to different rooms or zones, optimizing comfort levels.
3. Exhaust Systems: In industrial applications, ductwork removes pollutants, gases, and airborne particles from work areas, enhancing safety and compliance with environmental regulations.
4. Air Purification: It integrates with filtration systems to capture dust, allergens, and contaminants, improving overall air purity.
Technological Advancements:
1. CAD/CAM Design: Computer-aided design (CAD) and manufacturing (CAM) technologies enable precise customization of ductwork for specific building layouts and HVAC requirements.
2. Automated Fabrication: Advanced machinery automates the fabrication process, ensuring consistency in duct dimensions, fittings, and seam integrity.
3. Insulation Integration: Ducts can be insulated internally or externally to minimize thermal losses, reducing energy consumption and improving system efficiency.
4. Material Innovations: Lightweight alloys and coatings enhance corrosion resistance and longevity, suitable for diverse environmental conditions.
In conclusion, ductwork sheet metal is indispensable in modern construction, supporting environmental comfort, energy efficiency, and air quality management across various applications. Ongoing advancements in materials and manufacturing techniques continue to improve performance and sustainability in HVAC systems worldwide.
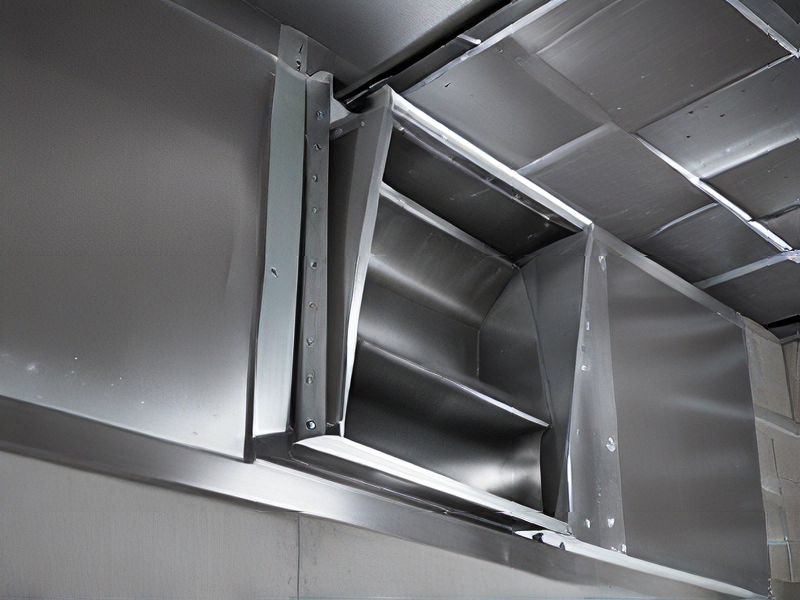
Quality Testing Methods for ductwork sheet metal and how to control quality
Quality testing methods for ductwork sheet metal typically include visual inspection, dimensional checks, and performance testing. Visual inspection ensures the surface is free from defects like dents, scratches, or corrosion. Dimensional checks verify that the ductwork conforms to specified dimensions, ensuring proper fit and alignment during installation. Performance testing involves assessing factors such as air leakage, pressure resistance, and thermal conductivity to ensure the ductwork meets performance standards.
To control quality, manufacturers can implement several measures:
1. Standard Operating Procedures (SOPs): Establish clear procedures for fabrication, assembly, and inspection to maintain consistency.
2. Quality Control Checks: Conduct regular inspections at various stages of production to detect defects early.
3. Training and Certification: Ensure workers are trained in proper fabrication techniques and quality standards. Certification programs can validate their skills.
4. Material Traceability: Track the source and specifications of materials used in fabrication to ensure compliance with standards.
5. Testing Protocols: Develop and adhere to standardized testing protocols for both in-process and final inspections.
6. Feedback Loops: Implement a system for collecting feedback from customers and field personnel to identify areas for improvement.
By integrating these methods and controls into their processes, manufacturers can consistently produce high-quality ductwork sheet metal that meets customer requirements and industry standards.
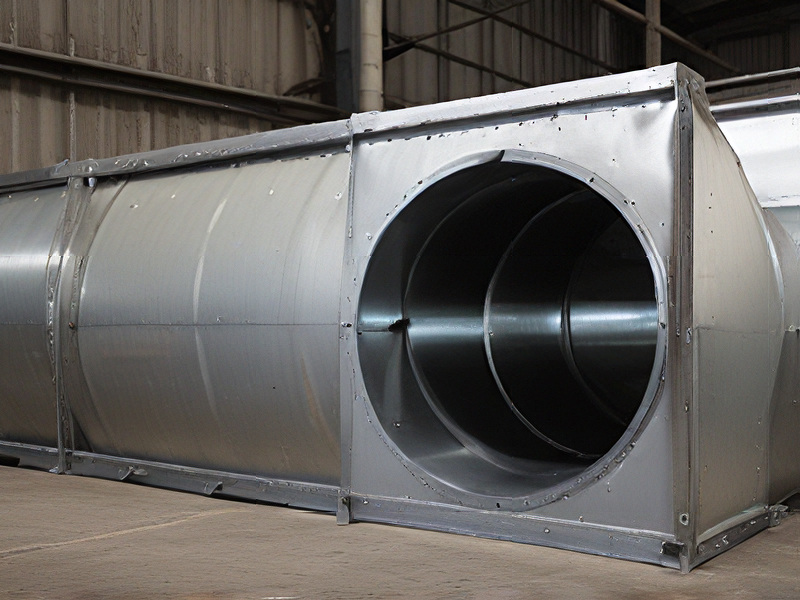
Tips for Procurement and Considerations when Purchasing from ductwork sheet metal
When procuring ductwork sheet metal, it’s crucial to balance quality, cost, and supplier reliability. Here are key tips and considerations:
1. Material Selection:
– Type: Common materials include galvanized steel, stainless steel, and aluminum. Choose based on the application and environment. For instance, galvanized steel is cost-effective and corrosion-resistant, while stainless steel is ideal for high-humidity or corrosive environments.
– Thickness: Ensure the sheet metal thickness meets industry standards and project specifications to maintain structural integrity and performance.
2. Quality Standards:
– Verify that the supplier adheres to relevant industry standards such as ASTM, ASME, or ISO certifications. Quality certifications ensure the material’s reliability and performance.
3. Supplier Reliability:
– Reputation: Choose suppliers with a proven track record of reliability and quality. Check reviews, references, and industry reputation.
– Lead Time: Ensure the supplier can meet your project timelines without compromising on quality. Delays can disrupt project schedules and increase costs.
4. Cost Management:
– Competitive Bidding: Solicit bids from multiple suppliers to ensure competitive pricing. However, avoid choosing solely on price; consider the quality and service level.
– Bulk Purchasing: Leverage economies of scale by purchasing in bulk if possible, which can lower unit costs.
5. Logistics and Delivery:
– Assess the supplier’s logistics capabilities, including their ability to deliver materials on time and in good condition. Reliable delivery services are critical to maintaining project schedules.
6. Customization and Fabrication:
– Ensure the supplier can meet specific customization needs, such as pre-fabrication or custom cutting, to streamline installation and reduce on-site labor.
7. Sustainability:
– Consider the environmental impact of your procurement choices. Opt for suppliers that offer recycled materials or sustainable manufacturing practices.
8. Post-Purchase Support:
– Evaluate the availability of technical support, warranty services, and after-sales support. Reliable post-purchase services can prevent and resolve issues efficiently.
By focusing on these factors, you can ensure a successful procurement process that balances quality, cost, and efficiency.
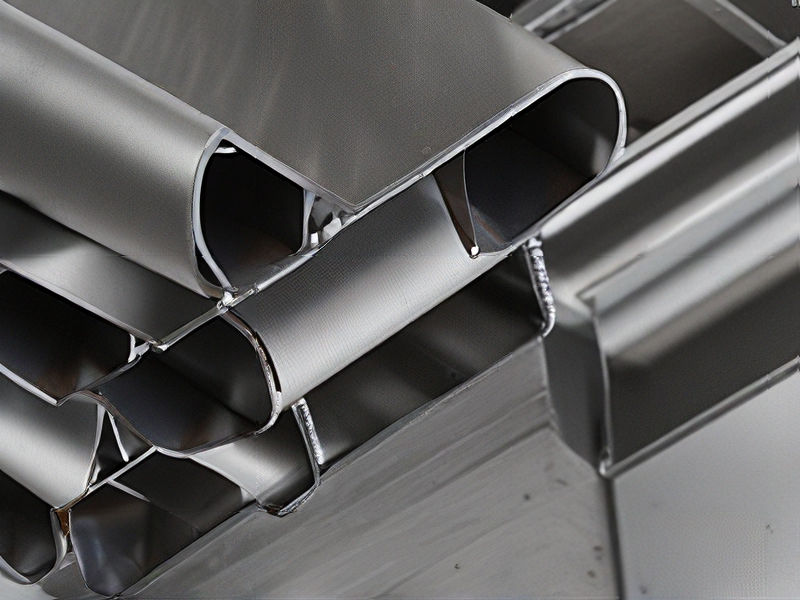
FAQs on Sourcing and Manufacturing from ductwork sheet metal in China
Certainly! When sourcing and manufacturing ductwork sheet metal from China, consider the following FAQs:
1. How do I find reliable suppliers in China?
– Utilize online sourcing platforms like Alibaba, Global Sources, or Made-in-China.com. Verify supplier credibility through reviews, certifications, and direct communication.
2. What quality standards should I expect?
– Specify your quality requirements clearly in your RFQ (Request for Quotation). Chinese suppliers can meet various international standards like ASTM, EN, or DIN, but quality can vary, so inspections and audits are advisable.
3. What are common manufacturing capabilities?
– Chinese manufacturers typically offer a range of capabilities including cutting, bending, welding, and surface treatment (e.g., galvanization). Ensure they can handle the specific thickness and dimensions you need.
4. How do I manage logistics and shipping?
– Coordinate with suppliers on shipping terms (FOB, CIF, etc.) and logistics providers for efficient transportation. Factor in lead times and potential delays.
5. What are the risks and how can they be mitigated?
– Risks include quality inconsistencies, language barriers, intellectual property protection, and regulatory compliance. Mitigate by conducting due diligence, using contracts with clear terms, and protecting designs.
6. Are there regulatory considerations?
– Understand import/export regulations, tariffs, and certifications required for your destination market. Ensure compliance with safety and environmental standards.
7. How can I ensure communication is effective?
– Clearly articulate requirements, use detailed technical drawings, and maintain regular communication through email, video calls, or local agents proficient in Chinese and English.
Navigating these FAQs will help streamline sourcing and manufacturing processes for ductwork sheet metal from China, ensuring quality, reliability, and compliance with your business needs.
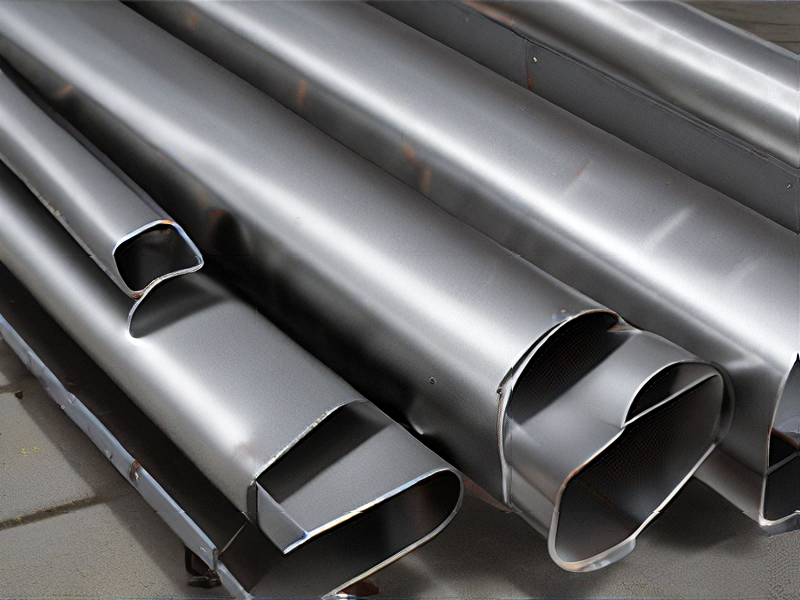