Technology and Applications of edm wire machine
Technology and Applications of EDM Wire Machines
Technology:
Electrical Discharge Machining (EDM) wire machines utilize electrical discharges to cut and shape metal workpieces. This non-traditional machining process involves a thin, electrically charged wire (usually brass or copper) that moves in a programmed path to erode material from a conductive workpiece. The machine operates in a dielectric fluid, typically deionized water, which cools and removes debris while maintaining electrical insulation.
The process relies on rapid, repetitive electrical discharges (sparks) between the wire and the workpiece. These discharges generate intense localized heat, melting and vaporizing material. The CNC system controls the wire’s path with high precision, enabling the creation of intricate and complex shapes.
Applications:
1. Tool and Die Making: EDM wire machines are essential in producing precise dies, molds, and tooling components, ensuring high accuracy and fine detail in manufacturing.
2. Aerospace Industry: The ability to machine hard materials like titanium and superalloys with tight tolerances makes EDM wire machines invaluable for aerospace parts, including turbine blades and fuel system components.
3. Medical Device Manufacturing: The precision and accuracy of EDM wire machines are critical for manufacturing intricate medical devices and implants, such as stents and orthopedic components.
4. Automotive Industry: These machines are used to create detailed parts like transmission components, gears, and fuel injectors, requiring high precision and complex geometries.
5. Electronics: EDM wire machines are employed in fabricating micro-scale components for semiconductors and electronic devices, where precision and minimal material stress are crucial.
6. Prototyping and R&D: The flexibility and precision of EDM wire machines make them suitable for developing prototypes and conducting research on new materials and designs.
In summary, EDM wire machines are vital for industries requiring high precision and intricate designs, offering unmatched capabilities in machining complex shapes and hard materials.
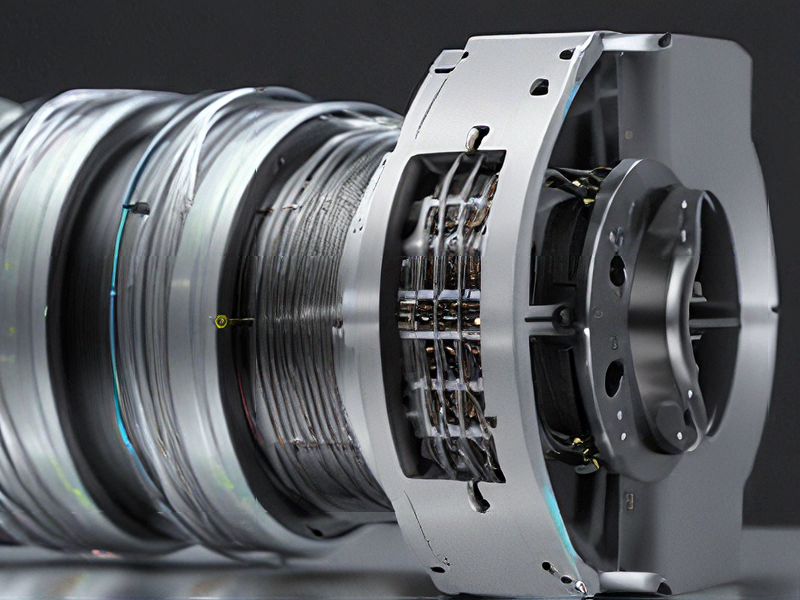
Quality Testing Methods for edm wire machine and how to control quality
Quality testing methods for EDM (Electrical Discharge Machining) wire machines involve several steps to ensure precision and reliability:
1. Dimensional Accuracy: Measure machined parts using calipers, micrometers, and CMM (Coordinate Measuring Machines) to ensure they meet specified tolerances.
2. Surface Finish: Use profilometers to assess surface roughness. The finish should meet the specified RA (roughness average) values to ensure proper performance and aesthetics.
3. Wire Tension and Alignment: Regularly check wire tension and alignment to prevent inaccuracies in cutting. This can be done using specialized tension meters and alignment tools.
4. Electrical Parameters: Monitor voltage, current, and pulse duration using built-in diagnostics and external oscilloscopes to ensure the machine operates within specified electrical parameters.
5. Machine Calibration: Regularly calibrate the machine using precision standards and test pieces to maintain accuracy over time.
6. Wear and Tear: Inspect and replace wear parts such as wire guides, power contacts, and filters to maintain consistent performance.
Quality Control Methods:
1. Preventive Maintenance: Implement a schedule for regular maintenance checks and part replacements to prevent unexpected failures and maintain machine accuracy.
2. Training: Ensure operators are well-trained in both machine operation and quality testing procedures. This reduces human error and enhances overall machine performance.
3. Process Documentation: Maintain detailed records of machine settings, test results, and maintenance activities. This helps in tracking performance trends and identifying issues promptly.
4. Statistical Process Control (SPC): Use SPC techniques to monitor the machining process in real-time. This involves collecting data on key parameters and using control charts to detect any variations that may indicate potential quality issues.
5. ISO Certification: Adhere to ISO standards (e.g., ISO 9001) to establish a robust quality management system that ensures continuous improvement and consistency in quality.
6. Customer Feedback: Regularly seek feedback from customers regarding the quality of machined parts. This helps in identifying any quality gaps and improving the process accordingly.
Implementing these methods ensures high-quality output and extends the lifespan of EDM wire machines.
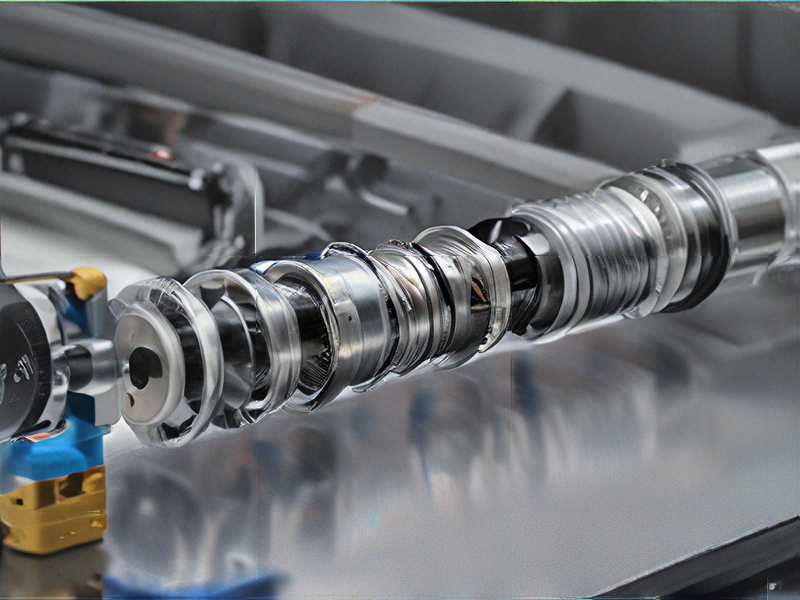
Tips for Procurement and Considerations when Purchasing from edm wire machine
When procuring an EDM wire machine, it’s crucial to ensure you’re making a well-informed decision. Here are some essential tips and considerations:
1. Purpose and Specifications:
– Define Your Needs: Understand the specific requirements of your operations. Consider the materials you’ll be cutting, the precision needed, and the production volume.
– Technical Specifications: Assess the machine’s cutting speed, accuracy, surface finish quality, and the maximum workpiece dimensions it can handle.
2. Quality and Reliability:
– Brand Reputation: Choose manufacturers with a solid reputation for reliability and quality. Read reviews and seek testimonials from other users.
– Build Quality: Inspect the build quality of the machine, including the frame, components, and overall robustness.
3. Cost Considerations:
– Budget: Establish a clear budget but also consider the total cost of ownership, which includes maintenance, consumables, and energy consumption.
– Financing Options: Explore financing options if the initial cost is prohibitive.
4. After-Sales Support:
– Service and Maintenance: Ensure the manufacturer offers comprehensive after-sales support, including maintenance services and availability of spare parts.
– Training and Technical Support: Confirm that training for operators and ongoing technical support are available.
5. Technology and Features:
– Software Compatibility: Check that the machine’s software is user-friendly and compatible with your existing systems.
– Advanced Features: Look for advanced features like automatic wire threading, collision protection, and remote monitoring capabilities.
6. Environmental and Safety Considerations:
– Compliance: Ensure the machine complies with safety regulations and environmental standards.
– Energy Efficiency: Consider the energy efficiency of the machine to reduce operational costs and environmental impact.
7. Vendor Relationships:
– Partnership: Build a strong relationship with your vendor to ensure continuous support and potential customization of the machine to meet your evolving needs.
By taking these factors into account, you can make a more informed decision and ensure the EDM wire machine you purchase aligns with your operational goals and budget constraints.
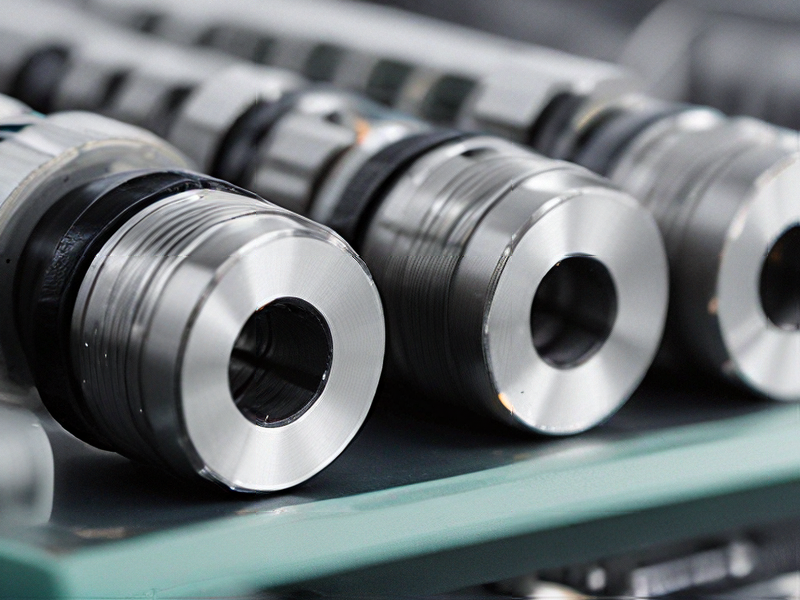
FAQs on Sourcing and Manufacturing from edm wire machine in China
Certainly! Here are some FAQs regarding sourcing and manufacturing from EDM wire machines in China:
1. What are EDM wire machines used for?
EDM (Electrical Discharge Machining) wire machines are used to cut complex shapes in metal by using electrical discharges. They are commonly used in tool and die manufacturing, aerospace, and automotive industries.
2. Why source EDM wire machines from China?
China offers competitive pricing due to lower labor costs and a developed manufacturing infrastructure. Many Chinese manufacturers also specialize in precision machining, making them ideal for EDM wire machines.
3. How do I find reliable suppliers in China?
Research online platforms like Alibaba, attend trade shows, or use sourcing agents to find reputable suppliers. Verify their certifications, request samples, and check customer reviews to ensure quality and reliability.
4. What are the key considerations for manufacturing in China?
Ensure clear communication, specify quality standards, and negotiate terms regarding production timelines, QC processes, and shipping. Consider intellectual property protections and legal agreements.
5. How can I manage quality control when manufacturing in China?
Visit factories if possible, hire third-party inspection services, or appoint a local representative to oversee production. Clearly define quality standards and conduct regular inspections throughout the manufacturing process.
6. What are the shipping and logistics considerations?
Plan for shipping costs, customs duties, and lead times. Choose reputable freight forwarders or logistics providers experienced in shipping industrial machinery to minimize delays and ensure compliance with regulations.
Navigating sourcing and manufacturing from EDM wire machines in China involves thorough research, clear communication, and diligent quality control to ensure successful outcomes.
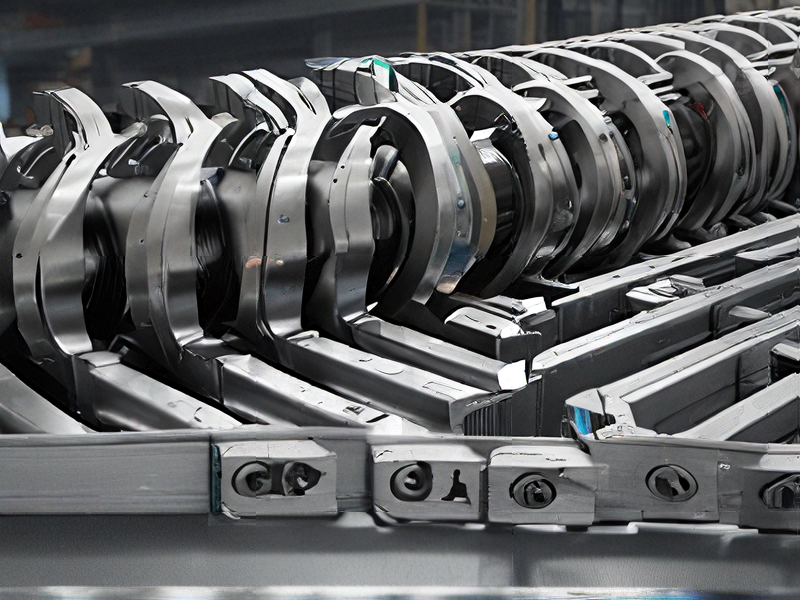