Technology and Applications of galvanized steel versus stainless steel
Galvanized steel and stainless steel are both widely used in various applications due to their distinct properties and benefits.
Galvanized steel is carbon steel that has been coated with a layer of zinc through a process called galvanization. This coating provides excellent corrosion resistance, especially in environments where the steel may be exposed to moisture or harsh conditions. Galvanized steel is commonly used in construction for roofing, siding, gutters, and fencing, as well as in automotive manufacturing and HVAC systems.
Stainless steel, on the other hand, contains chromium and often other alloying elements like nickel or molybdenum. This composition gives stainless steel its unique properties, including resistance to corrosion, heat, and staining. Stainless steel is highly durable and hygienic, making it suitable for applications such as kitchen appliances, food processing equipment, medical devices, and architectural structures where aesthetic appeal and cleanliness are critical.
In comparison, galvanized steel is generally more cost-effective and easier to work with than stainless steel. However, it may not be as durable in certain aggressive environments or under extreme temperatures. Stainless steel, while more expensive, offers superior corrosion resistance and longevity, making it ideal for applications requiring high performance and longevity.
In summary, the choice between galvanized steel and stainless steel depends largely on the specific requirements of the application, including environmental conditions, cost considerations, and desired longevity and performance. Each material has its strengths and is selected based on the balance of these factors in a particular use case.
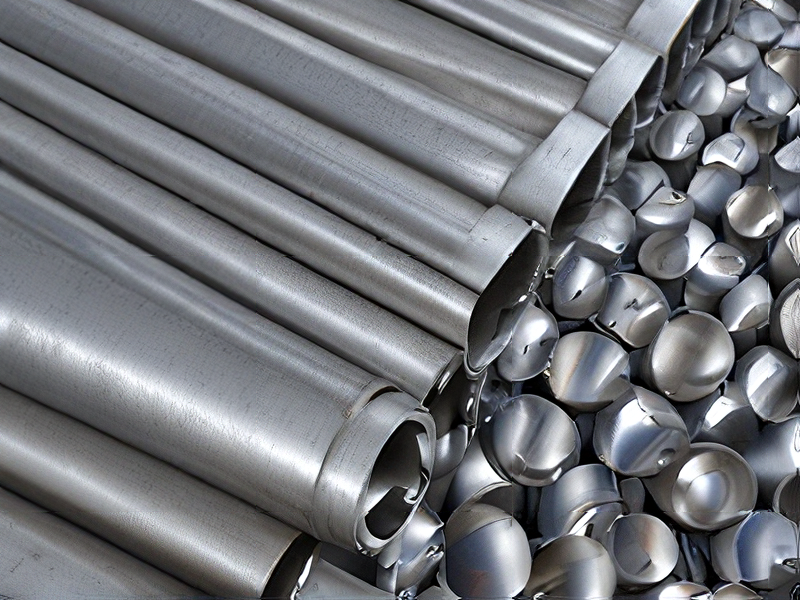
Quality Testing Methods for galvanized steel versus stainless steel and how to control quality
Quality Testing Methods:
1. Visual Inspection:
– Galvanized Steel: Look for uniform zinc coating, free from flaking, blistering, or discoloration.
– Stainless Steel: Check for surface finish quality, absence of rust, pitting, and surface defects.
2. Coating Thickness Measurement:
– Galvanized Steel: Use a coating thickness gauge to ensure zinc coating meets specifications (ASTM A123/A123M standards).
– Stainless Steel: Generally, not applicable unless a surface coating is involved.
3. Adhesion Test:
– Galvanized Steel: Perform a bend test or use a knife to scrape the coating to assess adhesion.
– Stainless Steel: Not typically required unless a coating is applied.
4. Corrosion Resistance Testing:
– Galvanized Steel: Conduct salt spray (ASTM B117) or cyclic corrosion tests to evaluate the durability of the zinc coating.
– Stainless Steel: Perform salt spray tests and other corrosion tests to ensure resistance to rust.
5. Mechanical Testing:
– Galvanized Steel: Evaluate tensile strength, impact resistance, and hardness to ensure the substrate’s integrity is not compromised by galvanizing.
– Stainless Steel: Perform tensile, impact, and hardness tests (ASTM A370) to confirm mechanical properties meet standards.
Quality Control Methods:
1. Material Certification:
– Ensure raw materials come with certification confirming compliance with relevant standards (ASTM, ISO).
2. Process Control:
– Galvanized Steel: Monitor galvanizing bath temperature, composition, and immersion time.
– Stainless Steel: Control manufacturing processes, such as welding, machining, and heat treatment, to prevent contamination and defects.
3. Inspection and Testing Plans:
– Develop and implement detailed inspection and testing plans at various production stages to catch defects early.
4. Regular Audits:
– Conduct regular audits of processes and quality management systems to ensure compliance and continuous improvement.
5. Training and Certification:
– Ensure personnel are well-trained and certified in relevant quality standards and testing procedures.
6. Documentation:
– Maintain detailed records of all inspections, tests, and corrective actions to ensure traceability and accountability.
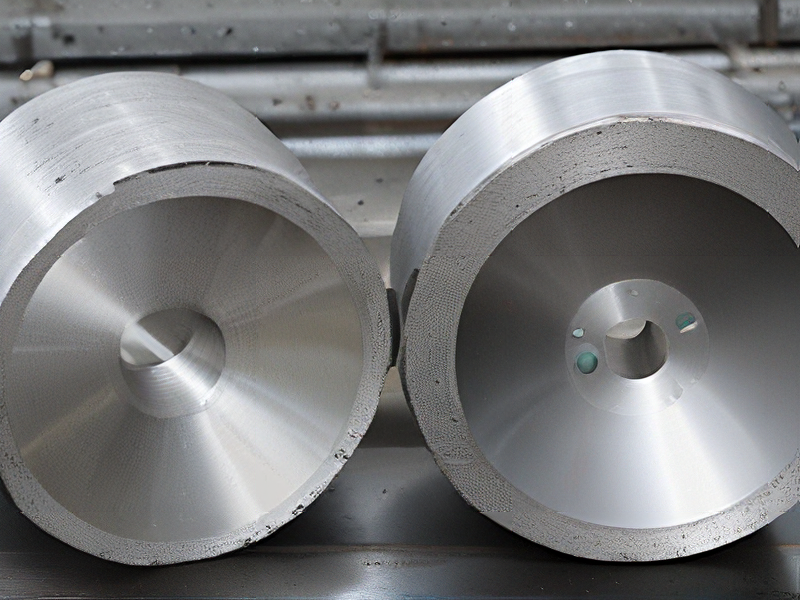
Tips for Procurement and Considerations when Purchasing from galvanized steel versus stainless steel
When procuring galvanized steel versus stainless steel, it’s essential to weigh the benefits, costs, and specific applications of each material.
Galvanized Steel
Pros:
1. Cost-Effective: Generally cheaper than stainless steel due to lower material and production costs.
2. Corrosion Resistance: Zinc coating provides decent corrosion resistance, suitable for outdoor use and wet environments.
3. Durability: The coating can withstand harsh weather conditions and physical wear.
Cons:
1. Limited Lifespan: Zinc coating can wear off over time, especially in highly corrosive environments.
2. Maintenance: Requires periodic inspection and maintenance to ensure the coating remains intact.
3. Aesthetics: The appearance may degrade over time as the coating weathers.
Applications:
– Construction (roofing, fencing)
– Outdoor structures
– Automotive parts
Stainless Steel
Pros:
1. Superior Corrosion Resistance: Contains chromium which forms a passive layer of chromium oxide, preventing rust.
2. Low Maintenance: Requires minimal maintenance, making it ideal for long-term applications.
3. Aesthetic Appeal: Maintains a shiny, polished look, and is often used where appearance is important.
Cons:
1. Higher Cost: More expensive due to material and production costs.
2. Weight: Heavier than galvanized steel, which can impact transportation and handling.
3. Workability: Harder to work with due to its strength, potentially increasing labor costs.
Applications:
– Medical equipment
– Food processing
– Marine environments
– Architectural structures
Key Considerations
1. Environment: Choose galvanized steel for moderate corrosion environments; opt for stainless steel in highly corrosive or hygienic settings.
2. Budget: Balance upfront costs with long-term maintenance and replacement costs.
3. Structural Requirements: Assess the strength, weight, and fabrication requirements of your project.
4. Aesthetic Needs: Consider the visual impact and how long the material needs to maintain its appearance.
In summary, galvanized steel is ideal for cost-sensitive projects with moderate corrosion risks, while stainless steel is preferable for applications requiring high durability, low maintenance, and superior corrosion resistance.
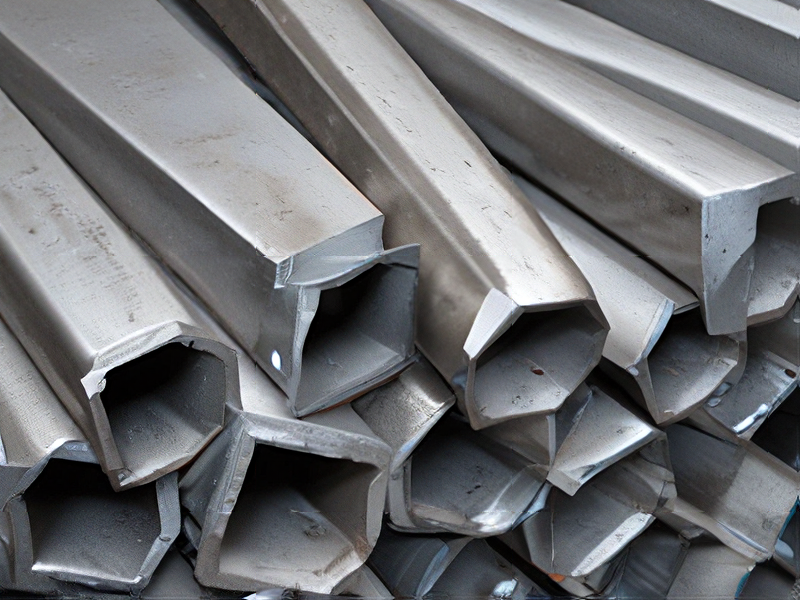
FAQs on Sourcing and Manufacturing from galvanized steel versus stainless steel in China
FAQs on Sourcing and Manufacturing from Galvanized Steel vs. Stainless Steel in China
1. What are the key differences between galvanized steel and stainless steel?
– Galvanized Steel: Coated with a layer of zinc to prevent corrosion. Cost-effective and used in outdoor and industrial applications.
– Stainless Steel: Contains chromium, which forms a passive film of chromium oxide. Known for its corrosion resistance, strength, and aesthetic appeal. Used in kitchenware, medical equipment, and construction.
2. What are the cost differences when sourcing from China?
– Galvanized Steel: Generally cheaper due to lower material and processing costs. Ideal for large-scale projects with budget constraints.
– Stainless Steel: More expensive due to the higher cost of raw materials and processing. Preferred for applications requiring durability and resistance to harsh environments.
3. Which industries prefer galvanized steel?
– Construction (e.g., roofing, wall panels)
– Automotive (e.g., body panels)
– Agriculture (e.g., fencing, silos)
4. Which industries prefer stainless steel?
– Food and Beverage (e.g., kitchen equipment)
– Healthcare (e.g., surgical instruments)
– Aerospace and Marine (e.g., components exposed to harsh environments)
5. How does the manufacturing process differ in China?
– Galvanized Steel: Involves hot-dip galvanizing or electro-galvanizing. Chinese manufacturers often excel in high-volume production at competitive prices.
– Stainless Steel: Requires precise control of alloy composition and processing. Chinese manufacturers are equipped with advanced technology for high-quality production.
6. What are the quality considerations when sourcing from China?
– Ensure suppliers comply with international standards (e.g., ISO, ASTM).
– Conduct factory audits and request material certifications.
– Establish clear specifications and quality assurance protocols.
7. How to find reliable suppliers in China?
– Use online platforms (e.g., Alibaba, Global Sources).
– Attend trade shows (e.g., Canton Fair).
– Engage local sourcing agents for on-ground support and verification.
8. What are the logistics considerations?
– Consider lead times, shipping methods, and customs regulations.
– Evaluate the supplier’s capacity to meet deadlines and handle large orders.
By understanding these aspects, businesses can make informed decisions about sourcing and manufacturing with galvanized or stainless steel in China.
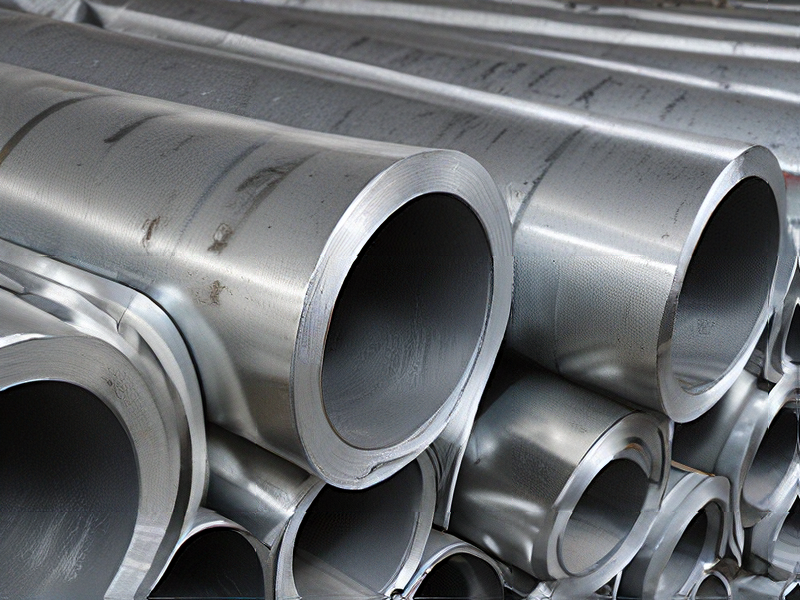