Technology and Applications of heat treatments of steel
Heat treatment of steel involves controlled heating and cooling to alter its physical and mechanical properties without changing its shape. This process is crucial in enhancing the performance, durability, and workability of steel. The primary heat treatment techniques include annealing, quenching, and tempering.
Annealing: In this process, steel is heated to a specific temperature and then cooled slowly, usually in a furnace. Annealing softens the metal, improves ductility, and relieves internal stresses, making the steel easier to machine or form.
Quenching: This involves heating the steel to a high temperature and then rapidly cooling it, typically in water, oil, or air. Quenching increases hardness and strength but can make the steel brittle. It’s often followed by tempering to achieve a balance between hardness and toughness.
Tempering: After quenching, steel is reheated to a lower temperature and then cooled. Tempering reduces the brittleness from quenching while maintaining an acceptable level of hardness and strength. This process fine-tunes the mechanical properties of the steel to meet specific requirements.
Applications:
1. Automotive Industry: Components like gears, shafts, and springs undergo heat treatment to enhance wear resistance and fatigue strength.
2. Construction: Structural steel elements such as beams and rebar are treated to ensure they can withstand heavy loads and stress without failure.
3. Tool Manufacturing: Cutting tools, dies, and drills require heat treatment to attain the necessary hardness and durability for efficient operation.
4. Aerospace: Aircraft components demand materials with exceptional strength-to-weight ratios, achieved through precise heat treatment processes.
5. Machinery: Bearings, pistons, and other machine parts are treated to improve performance and lifespan under intense operational conditions.
These heat treatment processes are vital for optimizing the properties of steel, making it suitable for a wide range of industrial applications.
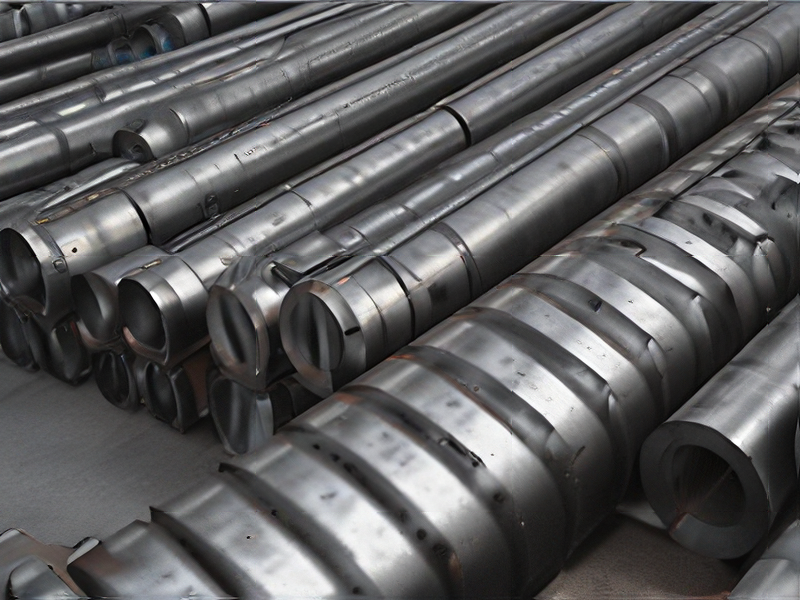
Quality Testing Methods for heat treatments of steel and how to control quality
Quality testing methods for heat treatments of steel typically involve a combination of destructive and non-destructive techniques to ensure desired properties like hardness, toughness, and microstructure. Non-destructive methods include:
1. Visual Inspection: Checking for surface irregularities and color changes after heat treatment.
2. Dimensional Checks: Measuring dimensions to ensure parts conform to specifications.
3. Hardness Testing: Using methods like Rockwell or Brinell tests to assess hardness, which correlates with strength and wear resistance.
4. Magnetic Particle Inspection: Detecting surface and near-surface flaws by applying magnetic particles and observing their alignment.
5. Ultrasonic Testing: Sending ultrasonic waves through steel to detect internal flaws or inconsistencies in material density.
To control quality:
1. Standard Operating Procedures (SOPs): Documenting precise procedures for heating, soaking, and cooling times.
2. Temperature Monitoring: Using thermocouples and pyrometers to accurately control and record heating and cooling temperatures.
3. Quenching Media Control: Ensuring the right quenching medium (water, oil, polymer) and agitation rate to achieve desired hardness without inducing cracks or distortion.
4. Process Validation: Periodically testing samples to verify that heat treatment processes meet specified standards.
5. Training and Certification: Ensuring operators are trained in proper procedures and periodically certified to maintain competency.
By integrating these methods and controls, manufacturers can consistently achieve high-quality steel components suitable for their intended applications.
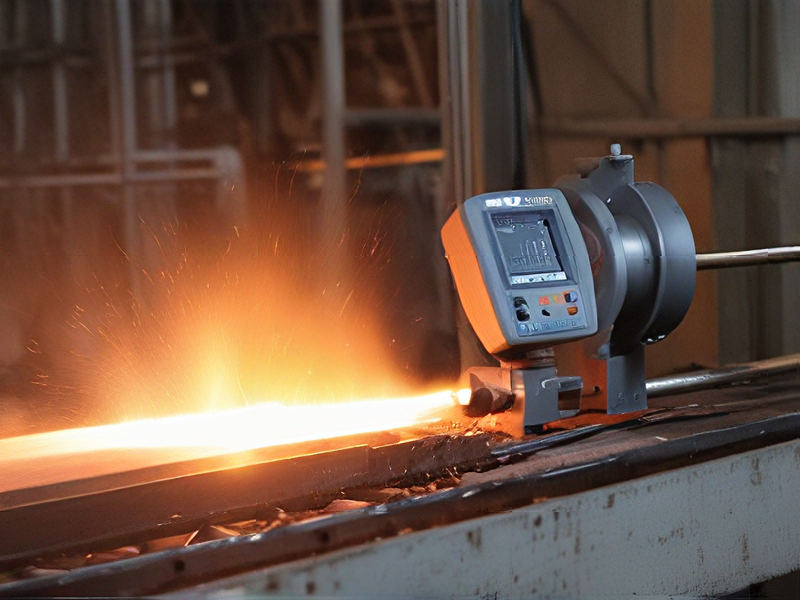
Tips for Procurement and Considerations when Purchasing from heat treatments of steel
When procuring and purchasing steel that has undergone heat treatment, consider the following tips and key considerations:
1. Understand Heat Treatment Types:
– Familiarize yourself with the different types of heat treatments such as annealing, quenching, tempering, and case hardening. Each process affects the steel’s properties differently, impacting hardness, strength, ductility, and toughness.
2. Specify Requirements Clearly:
– Clearly outline your material specifications, including the type of steel, desired mechanical properties, and intended application. This ensures you receive steel treated to meet your specific needs.
3. Check Supplier Certifications:
– Ensure that the supplier is certified and follows industry standards like ISO 9001 or AS9100. Certifications indicate adherence to quality management systems.
4. Evaluate Supplier Experience:
– Choose suppliers with extensive experience in heat treatment processes. Experienced suppliers are more likely to deliver consistent quality and understand the nuances of various treatments.
5. Request Material Test Reports (MTRs):
– Always ask for MTRs, which provide detailed information on the chemical composition and mechanical properties of the steel. This helps verify that the material meets your specifications.
6. Consider Post-Treatment Services:
– Some applications may require additional processes such as machining, grinding, or coating after heat treatment. Check if the supplier offers these services or can recommend trusted partners.
7. Assess Lead Times and Delivery:
– Discuss lead times upfront and ensure they align with your project schedule. Reliable delivery is crucial to avoid delays in production.
8. Evaluate Cost vs. Quality:
– While cost is a significant factor, prioritize quality and performance to avoid future issues. Poorly treated steel can lead to failures and higher long-term costs.
9. Inspect Samples:
– If possible, request samples before placing a large order. Inspecting samples helps verify the quality and suitability of the steel for your application.
10. Maintain Communication:
– Keep open communication with your supplier throughout the procurement process. Address any concerns promptly to ensure the final product meets your expectations.
By considering these factors, you can make informed decisions when procuring heat-treated steel, ensuring it meets your project’s technical and quality requirements.
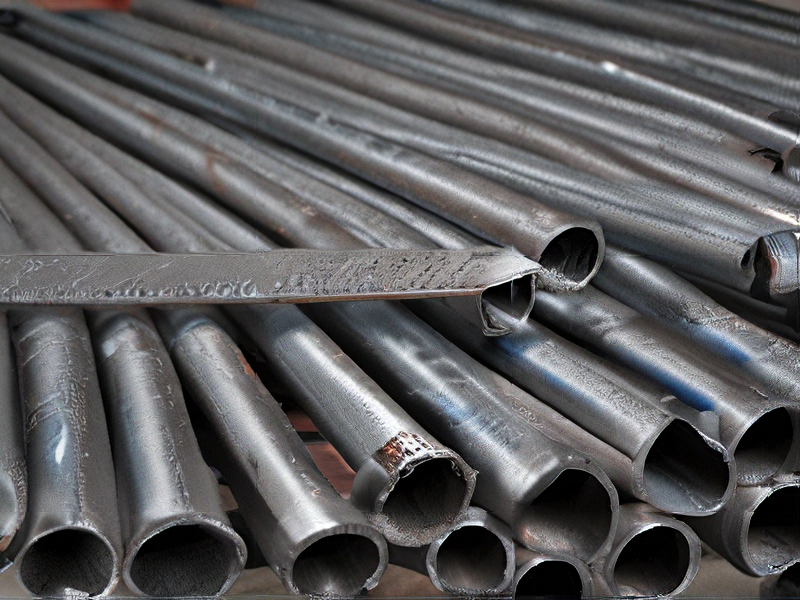
FAQs on Sourcing and Manufacturing from heat treatments of steel in China
When sourcing and manufacturing steel heat treatments in China, several key FAQs arise:
1. What types of heat treatments are commonly available?
China offers a wide range, including annealing, normalizing, quenching, and tempering, tailored to various steel grades and product requirements.
2. How can quality control be ensured?
Partnering with ISO-certified facilities and conducting on-site inspections are crucial. Establish clear quality standards and perform regular audits.
3. What are typical production lead times?
Lead times vary based on treatment complexity and order volume. Plan for 2-4 weeks for simpler treatments, and longer for intricate processes.
4. What about environmental and regulatory compliance?
Ensure facilities adhere to local and international environmental standards. Request compliance certifications to mitigate risks.
5. What are the cost considerations?
Costs are competitive due to lower labor and operational expenses in China. However, factor in shipping and potential import tariffs.
6. How to manage intellectual property (IP) concerns?
Implement robust confidentiality agreements and IP protection measures. Work with reputable partners who respect IP rights.
7. Can customization and technical support be provided?
Many Chinese suppliers offer customization and technical expertise. Clearly communicate specifications and expectations upfront.
Navigating these FAQs ensures smoother sourcing and manufacturing processes for steel heat treatments in China, balancing cost-efficiency with quality and compliance.
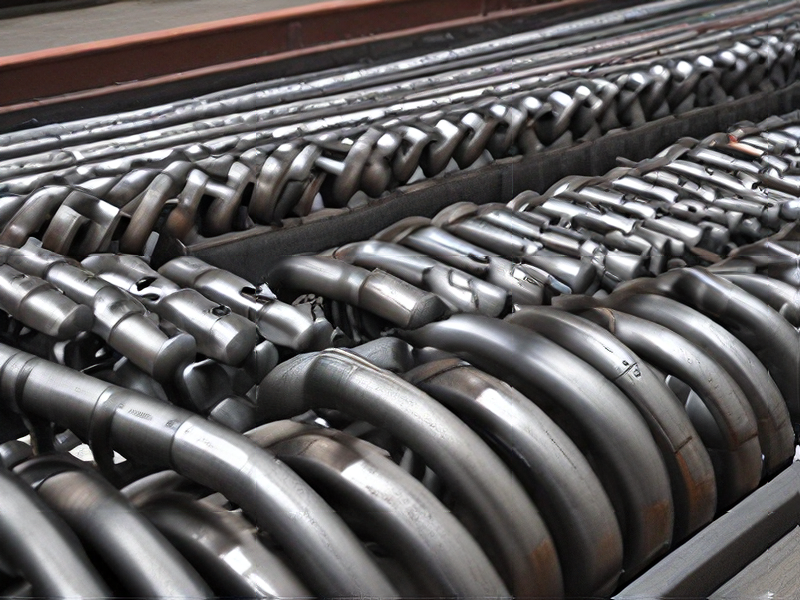