Technology and Applications of heated metal
Heated metal technology finds diverse applications across various industries, leveraging its unique properties when subjected to controlled temperature changes. One prominent use is in metallurgy, where heat treatment processes like annealing, tempering, and hardening are employed to alter the mechanical properties of metals, enhancing their strength, hardness, or ductility to meet specific industrial needs.
In manufacturing, heated metals are crucial for shaping and forming processes such as forging, casting, and welding. Forging involves heating metal to high temperatures to make it malleable, allowing for shaping into desired forms under pressure. Casting similarly utilizes heated metals to melt and pour into molds, creating complex shapes with precision. Welding joins metals by heating them to melting points, enabling fusion and structural integrity.
Heated metals also play a vital role in electronics and semiconductor industries, particularly in processes like vapor deposition and thermal evaporation. Here, metals are heated to produce vapors that condense onto surfaces as thin films, essential for manufacturing microelectronic components and coatings.
Beyond industrial applications, heated metal technology is integral to everyday consumer goods such as kitchen appliances (cooking surfaces and ovens), automotive components (engine parts and exhaust systems), and household utilities (water heaters and HVAC systems). These applications demonstrate the versatility and importance of heated metal technology across diverse sectors, continually evolving with advancements in materials science and manufacturing processes to meet increasing demands for efficiency and performance.
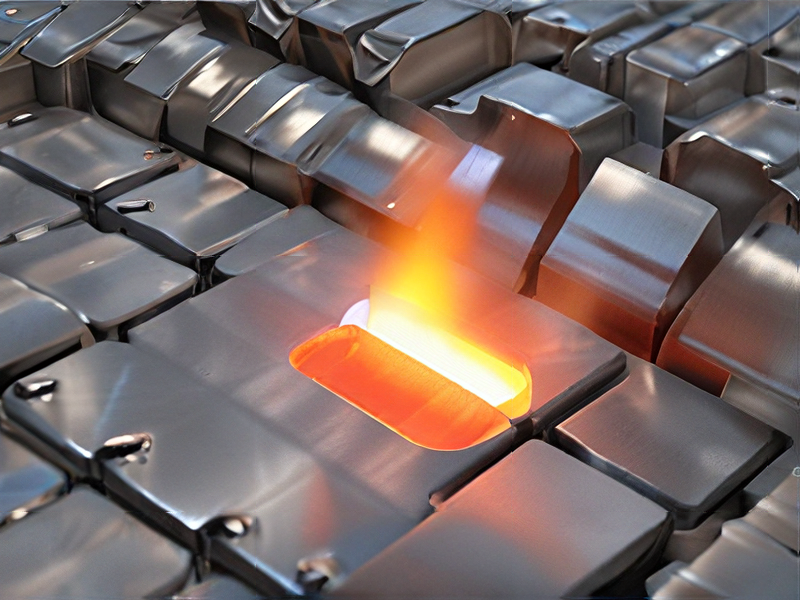
Quality Testing Methods for heated metal and how to control quality
Quality testing methods for heated metal typically involve non-destructive testing (NDT) techniques due to the critical nature of maintaining material integrity post-heating. Common methods include:
1. Ultrasonic Testing (UT): Uses high-frequency sound waves to detect internal defects or inconsistencies in the metal structure.
2. Radiographic Testing (RT): Involves passing X-rays or gamma rays through the metal to reveal internal defects or structural inconsistencies.
3. Eddy Current Testing (ECT): Detects surface and near-surface defects by inducing eddy currents in the metal and measuring changes in electrical conductivity.
4. Visual Inspection (VI): Direct observation to detect surface defects, discoloration, or irregularities that may affect quality.
5. Dye Penetrant Testing (PT): Identifies surface-breaking defects by applying a dye penetrant followed by a developer to highlight flaws.
To control quality during heating processes:
– Temperature Monitoring: Use thermocouples or infrared thermometers to ensure the metal reaches and maintains the correct temperature range.
– Heating Time Control: Monitor and control the duration of heating to prevent overheating or underheating, which can affect metal properties.
– Atmosphere Control: Maintain specific atmospheric conditions (e.g., inert gas environment) to prevent oxidation and maintain material purity.
– Cooling Rate Control: Ensure controlled cooling to prevent stress formation or structural defects.
– Process Documentation: Maintain detailed records of heating parameters and inspection results for traceability and quality assurance purposes.
Implementing these methods and controls helps ensure heated metal maintains desired properties and meets quality standards without compromising structural integrity.
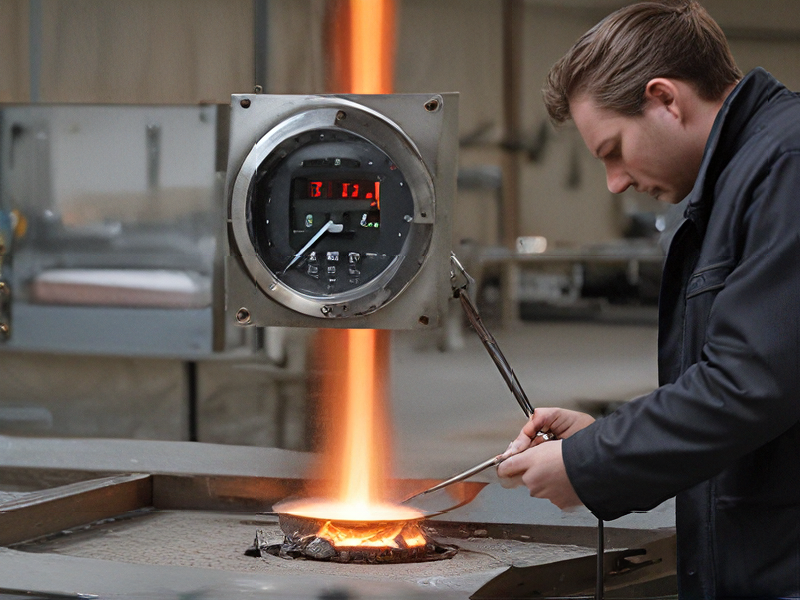
Tips for Procurement and Considerations when Purchasing from heated metal
When procuring heated metal or equipment designed to handle heated metals, several key considerations are essential:
1. Material Compatibility: Ensure the material of the equipment can withstand the temperatures and types of metals involved. Different metals have varying melting points and reactivity with materials like ceramics, metals, and polymers.
2. Temperature Range: Verify that the equipment can operate within the required temperature range for your specific heating process. Consider factors like maximum temperature, heating rate, and thermal stability.
3. Safety Features: Prioritize safety features such as temperature controls, thermal insulation, and emergency shutdown mechanisms to protect operators and prevent accidents.
4. Energy Efficiency: Evaluate the equipment’s energy consumption relative to its heating capacity. Efficient designs can reduce operational costs and environmental impact.
5. Durability and Maintenance: Choose equipment known for durability under high-temperature conditions and ensure it is easy to maintain. This includes accessibility for cleaning, part replacement, and longevity of heating elements.
6. Precision and Control: Depending on your application, consider the precision and control offered by the equipment. This may include programmable heating cycles, uniform heating distribution, and real-time monitoring capabilities.
7. Supplier Reputation: Select suppliers with a proven track record in delivering reliable equipment and providing adequate technical support. Reviews, references, and warranty terms can offer insights into supplier reliability.
8. Cost Considerations: Balance upfront costs with long-term operational savings and productivity gains. Factor in installation costs, ongoing maintenance, and potential downtime.
By addressing these considerations, you can make informed procurement decisions that align with your heating needs while prioritizing safety, efficiency, and operational reliability.
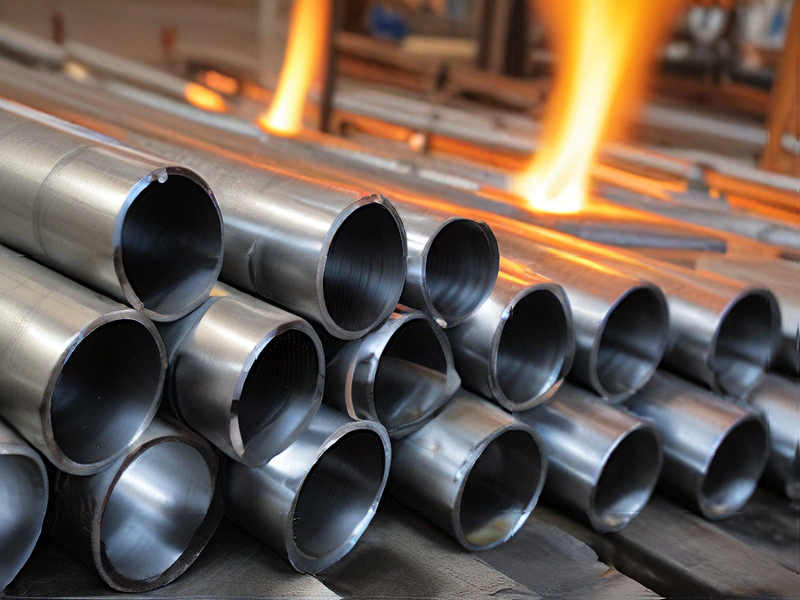
FAQs on Sourcing and Manufacturing from heated metal in China
Certainly! Here are some frequently asked questions (FAQs) regarding sourcing and manufacturing from heated metal in China:
1. What are common heating methods used in metal manufacturing in China?
– Electric resistance heating, induction heating, and gas/oxy-fuel heating are widely used methods.
2. How can I ensure quality when sourcing heated metal products from China?
– Choose suppliers with ISO certifications and conduct thorough inspections. Request samples and visit facilities if possible.
3. What are the typical lead times for heated metal manufacturing in China?
– Lead times vary based on complexity and order size but typically range from a few weeks to several months.
4. Are there environmental considerations with heated metal manufacturing in China?
– Yes, ensure suppliers comply with local environmental regulations to mitigate any impact from heating processes.
5. What are the cost implications of using heated metal manufacturing in China?
– Costs can vary based on heating method, material type, and labor costs, but China generally offers competitive pricing.
6. How do I handle intellectual property concerns when manufacturing in China?
– Use clear contracts, non-disclosure agreements (NDAs), and consider patent protections before sharing detailed designs.
7. What are common challenges faced when sourcing heated metal products from China?
– Communication barriers, quality control issues, and logistical complexities are common challenges to address.
8. Can I request specific heat treatment processes from Chinese manufacturers?
– Yes, most manufacturers can accommodate specific heat treatment requirements; specify these clearly in your orders.
By addressing these FAQs, you can better navigate sourcing and manufacturing processes involving heated metal in China efficiently and effectively.
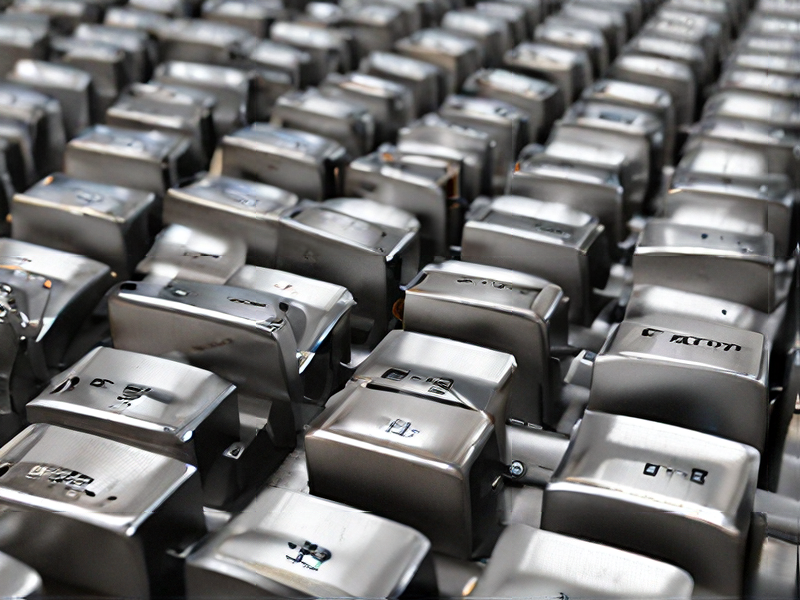