Technology and Applications of industrial machinery components
Industrial machinery components encompass a diverse array of technologies crucial to manufacturing and production processes. These components include mechanical, electrical, and electronic elements designed to enhance efficiency, precision, and reliability across various industries.
Mechanical Components:
1. Bearings and Shafts: Essential for reducing friction and supporting rotating parts, ensuring smooth operation in machines like conveyor systems and turbines.
2. Gears and Gearboxes: Transmit torque and adjust speed, vital in machines requiring precise motion control such as robotics and heavy machinery.
3. Pumps and Valves: Facilitate fluid flow and pressure control in hydraulic and pneumatic systems, integral to applications in manufacturing and energy sectors.
Electrical Components:
1. Motors and Drives: Convert electrical energy into mechanical motion, used extensively in robotics, assembly lines, and industrial automation.
2. Sensors and Actuators: Monitor parameters like temperature, pressure, and position, enabling automated feedback control and safety mechanisms in manufacturing processes.
Electronic Components:
1. Controllers and PLCs: Programmable logic controllers manage operations in complex machinery, ensuring synchronization and precise control over manufacturing processes.
2. Power Supplies and Converters: Provide stable electrical power to equipment, ensuring consistent operation and protecting sensitive components from voltage fluctuations.
Applications:
Industrial machinery components find applications in diverse sectors such as automotive manufacturing, aerospace, food processing, and pharmaceuticals. They enable high-speed production, precise quality control, and enhanced safety standards, contributing to overall operational efficiency and cost-effectiveness.
In summary, the technology and application of industrial machinery components are pivotal in driving innovation and productivity across industries, continually evolving to meet the demands of modern manufacturing processes. These components not only improve performance and reliability but also play a crucial role in advancing automation and sustainable manufacturing practices.
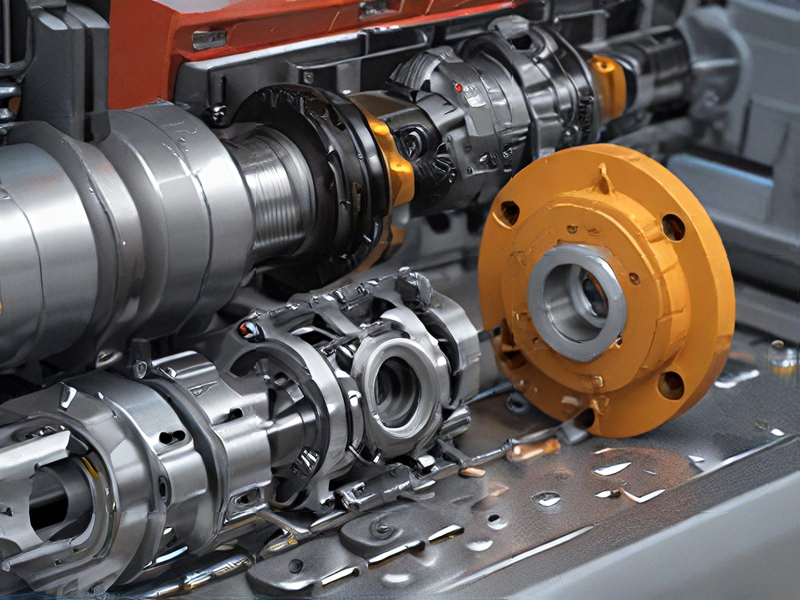
Quality Testing Methods for industrial machinery components and how to control quality
Quality testing methods for industrial machinery components typically include a combination of destructive and non-destructive techniques to ensure reliability and performance. Non-destructive methods like visual inspection, ultrasonic testing, magnetic particle inspection, and radiographic testing are used to detect surface defects, cracks, or internal flaws without compromising the integrity of the component. These methods are crucial for assessing welds, casting quality, and structural integrity.
In addition to non-destructive testing, destructive testing methods involve physically testing samples to understand material properties, such as tensile strength, hardness, and fatigue resistance. This can involve tensile testing, impact testing, hardness testing, and metallographic examination. These tests provide quantitative data on material performance under different conditions.
Controlling quality involves implementing rigorous standards and protocols throughout the manufacturing process. This includes establishing clear quality criteria, conducting regular inspections at key production stages, and employing statistical process control (SPC) methods to monitor variations and maintain consistency. Quality management systems such as ISO 9001 provide frameworks for continuous improvement and adherence to international standards.
Furthermore, ensuring skilled personnel conduct testing and inspection is vital. Training programs and certifications help maintain proficiency in testing methodologies and promote adherence to industry best practices. Documenting test results and maintaining comprehensive records enable traceability and facilitate corrective actions when necessary, ensuring that industrial machinery components meet required specifications and perform reliably in service.
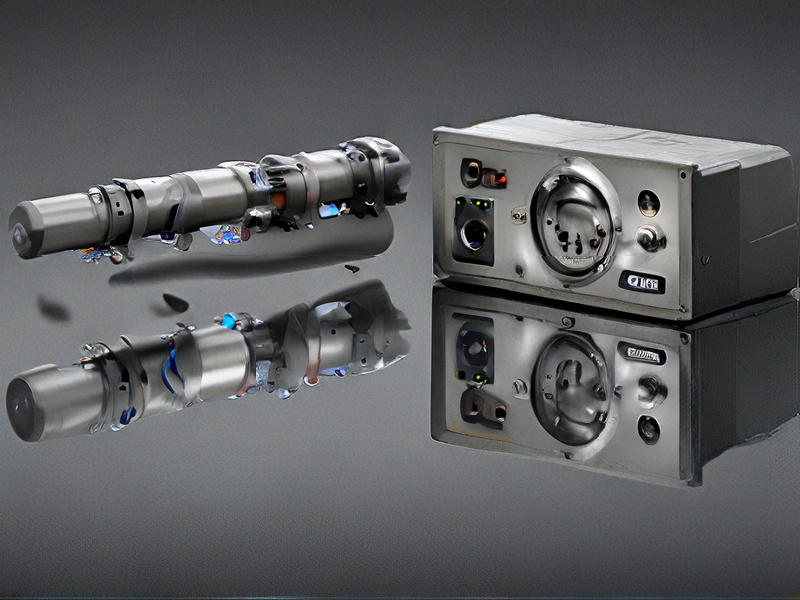
Tips for Procurement and Considerations when Purchasing from industrial machinery components
When procuring industrial machinery components, several key considerations can enhance the process and ensure optimal outcomes:
1. Specifications and Requirements: Clearly define the technical specifications and performance requirements of the machinery components. This includes dimensions, material specifications, load-bearing capacities, and operational conditions.
2. Quality and Reliability: Prioritize components from reputable manufacturers known for quality and reliability. Assess certifications, compliance with industry standards (such as ISO), and reliability metrics like Mean Time Between Failures (MTBF).
3. Supplier Assessment: Evaluate suppliers based on their track record, financial stability, delivery capabilities, and customer service. Conduct audits or request references to ensure they meet your procurement standards.
4. Cost and Value: Consider total cost of ownership rather than just initial purchase price. Evaluate factors such as maintenance requirements, energy efficiency, and potential downtime costs associated with each component.
5. Compatibility and Integration: Ensure compatibility with existing machinery and systems. Consider ease of installation and integration requirements to minimize disruption to operations.
6. Support and Service: Assess the supplier’s after-sales support, warranty terms, availability of spare parts, and technical assistance. A responsive support network can significantly impact uptime and maintenance efficiency.
7. Risk Management: Identify potential risks such as supply chain disruptions, geopolitical factors, and alternative sourcing strategies to mitigate risks and ensure continuity of supply.
8. Lifecycle Considerations: Evaluate the expected lifecycle of the machinery components and plan for future upgrades or replacements. Consider technological advancements and potential obsolescence risks.
By integrating these considerations into your procurement strategy, you can enhance decision-making, mitigate risks, and optimize the performance and reliability of industrial machinery components within your operations.
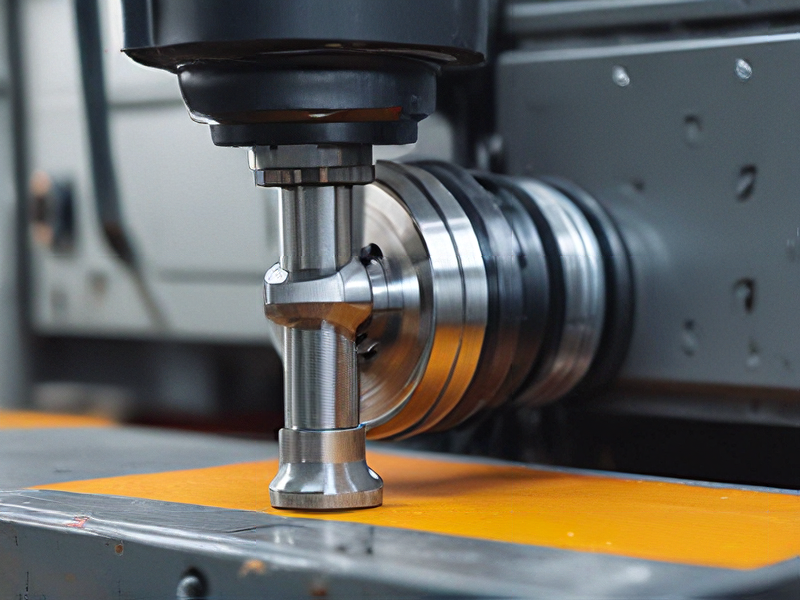
FAQs on Sourcing and Manufacturing from industrial machinery components in China
FAQs on Sourcing and Manufacturing Industrial Machinery Components in China
1. Why source industrial machinery components from China?
China offers cost-effective production, a wide variety of suppliers, and the ability to scale quickly. The country’s well-established manufacturing infrastructure and supply chain networks provide a competitive edge.
2. How to find reliable suppliers?
Utilize online platforms like Alibaba, Global Sources, and Made-in-China. Attend trade shows such as the Canton Fair. Perform due diligence by checking supplier certifications, visiting factories, and seeking customer reviews.
3. What are the key considerations for quality control?
Implement rigorous quality assurance processes, including pre-production samples, regular inspections during production, and final pre-shipment inspections. Partner with third-party quality control companies if needed.
4. How to handle intellectual property (IP) protection?
Register your IP in China before engaging with suppliers. Use Non-Disclosure Agreements (NDAs) and include clear IP clauses in contracts. Regularly monitor the market for potential infringements.
5. What are common payment methods and terms?
Common payment methods include Telegraphic Transfer (T/T), Letter of Credit (L/C), and online payment platforms. Negotiate payment terms such as a small deposit upfront (30%) and the balance after shipment or upon receiving satisfactory inspection results.
6. How to manage shipping and logistics?
Choose between air freight for speed or sea freight for cost-efficiency. Partner with reputable freight forwarders and understand Incoterms (FOB, CIF, DDP) to determine responsibilities and costs.
7. What are the potential risks and how to mitigate them?
Risks include quality issues, delays, and communication barriers. Mitigate these by conducting thorough supplier vetting, maintaining regular communication, and having contingency plans.
8. How to ensure compliance with international standards?
Ensure suppliers meet relevant international standards (ISO, CE, RoHS). Conduct regular audits and request compliance certificates.
9. What are the advantages of working with sourcing agents?
Sourcing agents offer local expertise, supplier networks, and can manage negotiations, quality control, and logistics, saving time and reducing risks.
10. How to establish long-term partnerships with suppliers?
Build trust through clear communication, fair treatment, and timely payments. Visit suppliers regularly and consider long-term contracts for mutual benefits.
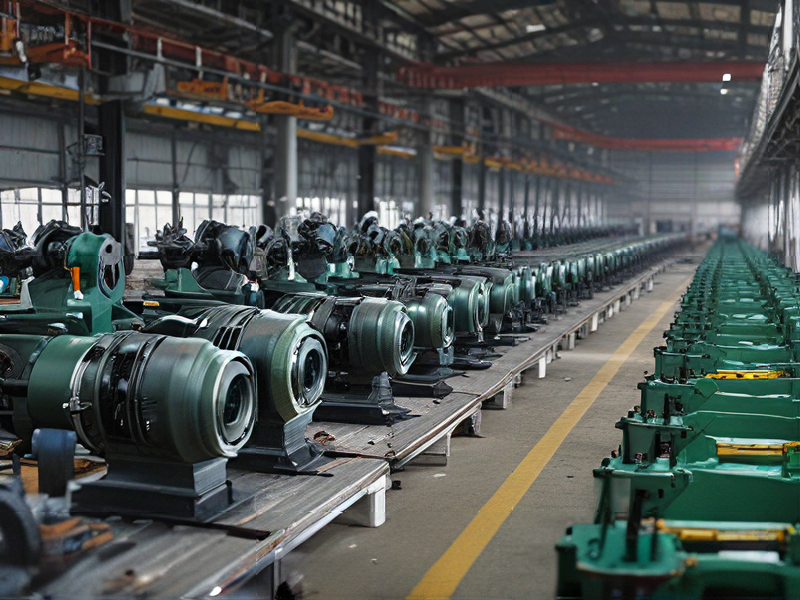