Technology and Applications of machine and machine tools
Technology and Applications of Machines and Machine Tools
Technology:
Machines and machine tools are integral to modern manufacturing, offering precision, efficiency, and the ability to handle complex tasks. Key technological advancements include:
1. Computer Numerical Control (CNC): CNC machines automate control through computers, enabling precise operations like cutting, drilling, and milling. They allow for complex designs and consistent quality.
2. Additive Manufacturing (3D Printing): This technology builds objects layer by layer, allowing for complex shapes and reduced material waste. It’s used in prototyping and producing intricate components.
3. Robotics: Robots integrated with machine tools increase productivity and accuracy. They perform repetitive tasks with high precision and are used in assembly lines, welding, and material handling.
4. IoT and Smart Manufacturing: IoT devices connect machines to monitor performance and predict maintenance needs. Smart manufacturing systems optimize production processes and enhance operational efficiency.
5. Advanced Materials: Development in materials such as composites and alloys improves machine tool performance and durability, enabling high-speed machining and better product quality.
Applications:
Machine tools are used across various industries, including:
1. Automotive: For manufacturing engine components, transmission parts, and body parts with high precision and consistency.
2. Aerospace: To produce complex and critical components like turbine blades, landing gear, and structural parts, ensuring safety and reliability.
3. Medical Devices: In the production of surgical instruments, implants, and prosthetics, where precision and quality are crucial.
4. Electronics: For making components like circuit boards and casings, requiring fine detail and accuracy.
5. Construction: Machines are used to fabricate structural elements, tools, and equipment, contributing to building infrastructure.
These technologies and applications underscore the significance of machines and machine tools in advancing industrial capabilities and driving innovation.
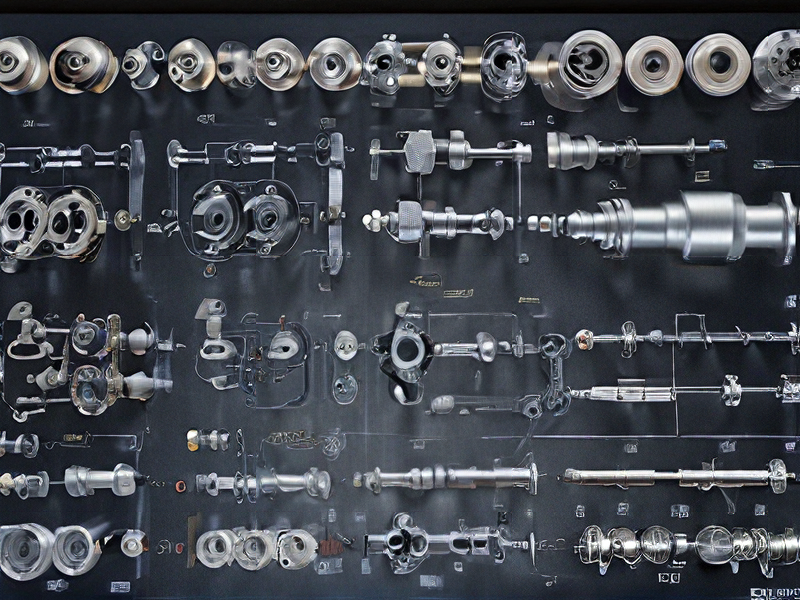
Quality Testing Methods for machine and machine tools and how to control quality
Quality testing for machines and machine tools involves various methods to ensure their performance, reliability, and precision. Here are some key methods and control practices:
Quality Testing Methods
1. Dimensional Accuracy:
– CMM (Coordinate Measuring Machine): Measures the physical geometrical characteristics of an object.
– Micrometers and Calipers: For precise measurement of small distances.
2. Performance Testing:
– Run-out Tests: Measures the deviation of rotational components.
– Load Tests: Assesses the machine’s ability to perform under different loads.
3. Surface Finish Testing:
– Profilometers: Measure surface roughness.
– Visual and Tactile Inspection: Identify surface defects.
4. Non-Destructive Testing (NDT):
– Ultrasonic Testing: Detects internal flaws using sound waves.
– Magnetic Particle Testing: Identifies surface and near-surface discontinuities in ferromagnetic materials.
5. Functional Testing:
– Trial Runs: Operate the machine under actual working conditions.
– Endurance Testing: Tests machine durability over extended periods.
Quality Control Practices
1. Standard Operating Procedures (SOPs): Establish clear guidelines for operating and testing machines.
2. Calibration:
– Regular calibration of measuring instruments ensures accuracy and consistency.
3. Statistical Process Control (SPC):
– Uses statistical methods to monitor and control the production process.
4. Inspection Plans:
– Incoming Inspection: Checks raw materials and components.
– In-process Inspection: Continuous monitoring during production.
– Final Inspection: Verifies the final product before delivery.
5. Documentation:
– Maintain detailed records of tests and inspections for traceability and accountability.
6. Training:
– Regular training for personnel to stay updated on quality standards and testing methods.
7. Continuous Improvement:
– Implementing feedback loops to constantly improve quality control processes.
By integrating these methods and practices, manufacturers can ensure that machines and machine tools meet the required standards and function reliably.
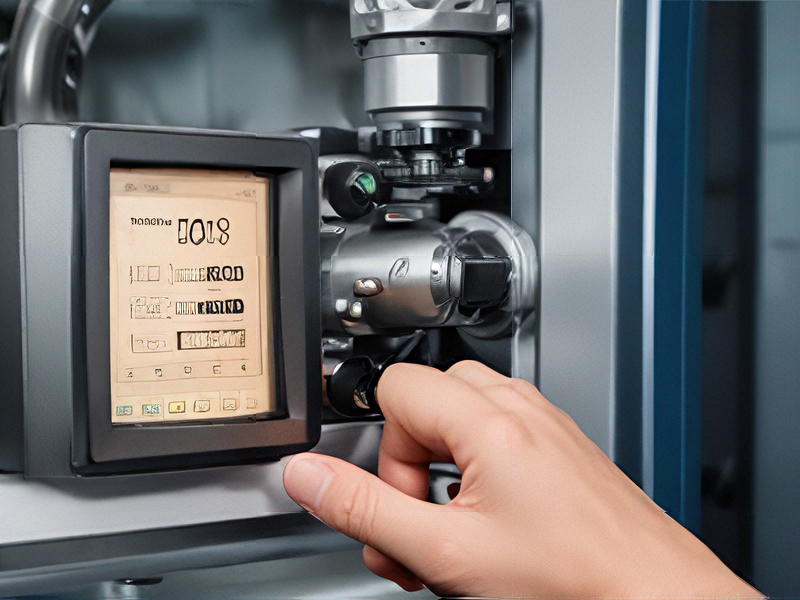
Tips for Procurement and Considerations when Purchasing from machine and machine tools
Procurement of machine tools and components requires careful consideration to ensure optimal performance, longevity, and value for money.
Here are some key tips:
1. Clearly define your needs: Precisely outline the required specifications, including dimensions, capabilities, materials to be processed, and production volume.
2. Research thoroughly: Explore reputable manufacturers, compare models, read reviews, and consider factors like brand reputation, warranty, and after-sales support.
3. Request quotes and negotiate: Obtain detailed quotes from multiple suppliers, compare pricing, delivery timelines, and payment terms.
4. Assess quality and reliability: Inspect samples, request certifications, and inquire about the manufacturer’s quality control processes.
5. Factor in total cost of ownership: Consider not just the initial purchase price, but also operating costs (energy, maintenance, repairs), and potential downtime.
6. Secure financing: Explore financing options if needed, comparing interest rates and repayment terms.
7. Ensure proper installation and training: Plan for professional installation and comprehensive operator training to maximize machine performance and minimize risks.
8. Establish clear contractual terms: Outline warranties, service agreements, and dispute resolution mechanisms in a legally binding contract.
By following these tips, you can make informed procurement decisions and acquire machine tools that meet your specific requirements and contribute to your business success.
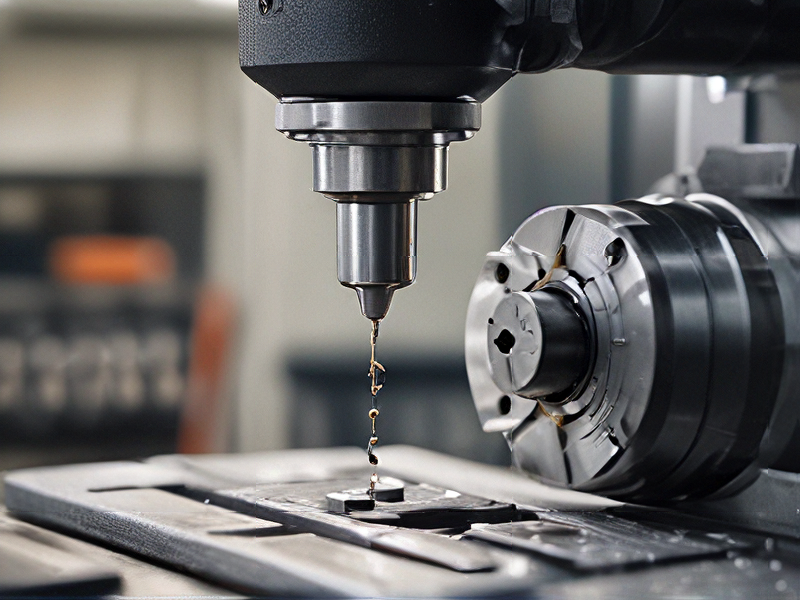
FAQs on Sourcing and Manufacturing from machine and machine tools in China
## Sourcing and Manufacturing from China: FAQs
Q: Where can I find reliable suppliers in China?
A: Online platforms like Alibaba, Global Sources, and Made-in-China connect global buyers with Chinese manufacturers. Industry-specific directories and trade shows also offer valuable sourcing opportunities.
Q: What are the key factors to consider when selecting a manufacturer?
A: Evaluate their production capacity, experience, quality control processes, certifications, and communication capabilities. Request samples and factory audits to assess their capabilities.
Q: What are the common manufacturing payment terms in China?
A: Letter of Credit (LC), T/T (Telegraphic Transfer), and PayPal are common payment methods.
Q: What are the typical lead times for manufacturing in China?
A: Lead times vary depending on product complexity, order quantity, and manufacturer capacity. Expect anywhere from 4 weeks to several months.
Q: What are the main challenges of manufacturing in China?
A: Language barriers, cultural differences, intellectual property protection, and navigating complex regulations can pose challenges. Partnering with a reputable sourcing agent can help mitigate these risks.
Q: How can I ensure quality control for my products manufactured in China?
A: Establish clear quality standards and inspection protocols with your manufacturer. Conduct regular quality checks throughout the production process and upon delivery.
Remember, thorough research and due diligence are crucial for successful sourcing and manufacturing in China.
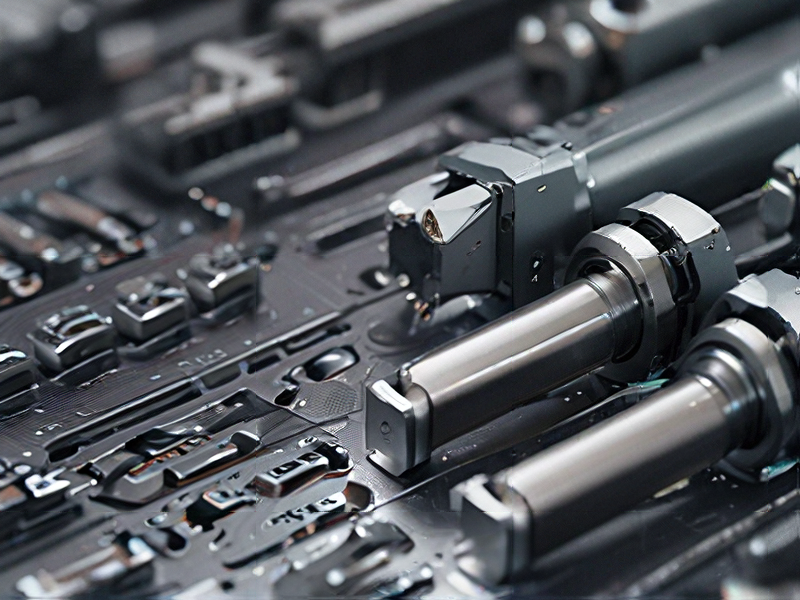