Technology and Applications of machine cnc metal
Computer Numerical Control (CNC) machines for metalworking represent a pivotal technology in modern manufacturing. These machines use computer programs to automate the operation of machine tools, enhancing precision, efficiency, and repeatability in metal fabrication processes.
CNC machines are versatile, capable of performing various tasks such as milling, turning, drilling, and grinding with high accuracy. They interpret CAD (Computer-Aided Design) files to execute complex geometries and intricate designs that would be challenging or impossible with manual methods. This capability makes them indispensable in industries like aerospace, automotive, and electronics, where tight tolerances and consistency are critical.
Applications of CNC machines in metalworking include the production of engine parts, gears, molds, and specialized components for industrial equipment. They enable rapid prototyping and mass production, reducing lead times and costs associated with traditional manufacturing techniques. CNC machines also support multi-axis machining, allowing for simultaneous cutting operations from different angles, which further enhances efficiency and flexibility.
Moreover, CNC technology continues to evolve with advancements such as integrated sensors for real-time monitoring, adaptive control systems for automatic adjustments, and connectivity features for remote operation and data analytics. These innovations improve productivity, quality control, and maintenance scheduling, contributing to overall operational efficiency.
In conclusion, CNC machines have revolutionized metalworking by combining computer technology with precision machining, enabling the creation of complex parts with high accuracy and consistency across various industries. Their ongoing development ensures they remain at the forefront of modern manufacturing, continually pushing the boundaries of what is achievable in metal fabrication.
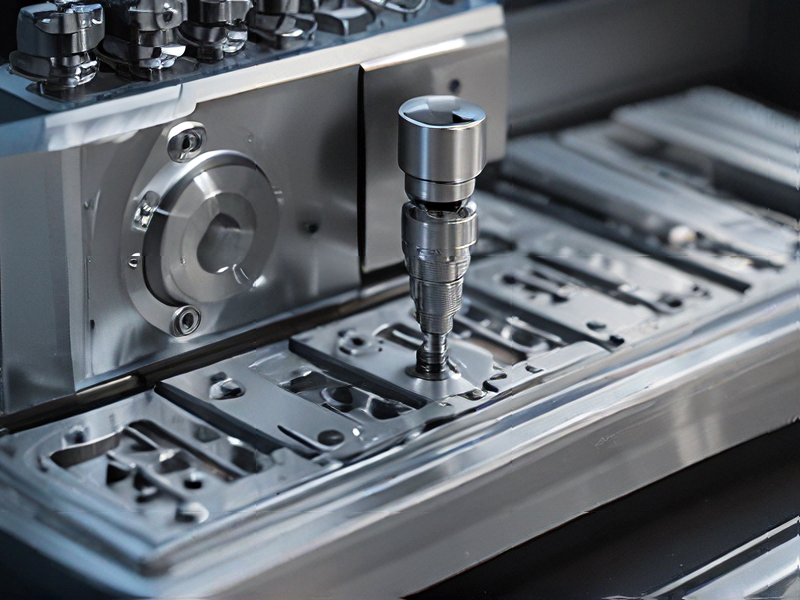
Quality Testing Methods for machine cnc metal and how to control quality
Quality testing methods for CNC metal machining typically include several key approaches:
1. Dimensional Accuracy: Utilize precision measuring tools such as calipers, micrometers, and coordinate measuring machines (CMMs) to verify dimensions against engineering drawings.
2. Surface Finish Inspection: Assess the surface roughness using profilometers or surface roughness testers to ensure it meets specified requirements.
3. Visual Inspection: Visually inspect parts for defects such as scratches, dents, burrs, or surface irregularities that may affect functionality or aesthetics.
4. Material Testing: Verify the material composition and properties using methods like spectroscopy, hardness testing (Rockwell, Vickers), or tensile testing.
5. Assembly and Fit Testing: Ensure components fit together correctly through assembly tests, verifying alignment and tolerances.
To control quality effectively:
– Establish Clear Specifications: Define precise quality standards and specifications for each part and process.
– Regular Calibration: Calibrate measuring equipment regularly to maintain accuracy in measurements.
– Process Control: Implement process controls such as machine calibration, tool maintenance, and operator training to minimize variability.
– Documentation and Traceability: Maintain detailed records of inspections, tests, and any deviations encountered during production for traceability and improvement.
– Continuous Improvement: Implement a feedback loop for continuous improvement based on quality metrics and customer feedback.
By integrating these methods and controls, manufacturers can ensure CNC machined metal parts meet required specifications reliably.
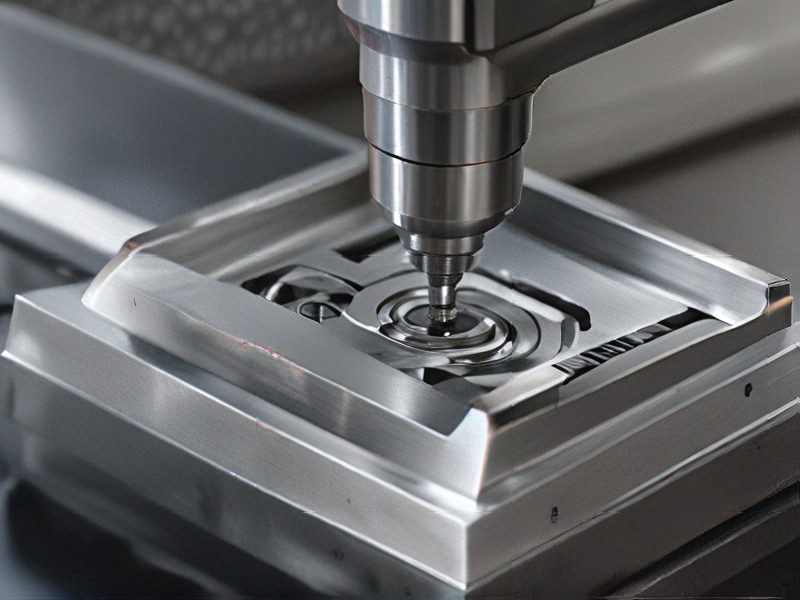
Tips for Procurement and Considerations when Purchasing from machine cnc metal
When procuring CNC machines for metalworking, consider several key factors to ensure optimal performance and value:
1. Machine Specifications: Evaluate the machine’s capabilities such as spindle speed, axis travel, and tolerance levels. Ensure they meet your production needs for precision and efficiency.
2. Manufacturer Reputation: Choose a reputable manufacturer known for quality craftsmanship and reliable customer support. Check reviews and testimonials from other users.
3. Technology and Innovation: Look for machines equipped with the latest technological advancements like automatic tool changers, probing systems for accuracy, and software compatibility for seamless integration with your existing operations.
4. Maintenance and Service: Assess the availability of maintenance support and spare parts. A responsive service network can minimize downtime and ensure long-term productivity.
5. Cost and ROI: Compare initial costs against long-term benefits and return on investment (ROI). Factor in operational costs, maintenance expenses, and potential revenue generation.
6. Training and Support: Consider the training required for operators and technicians. Manufacturers offering comprehensive training programs can help maximize machine utilization and efficiency.
7. Safety Features: Prioritize machines with robust safety features to protect operators and prevent accidents during operation.
8. Customization Options: If necessary, inquire about customization options to tailor the machine to specific production requirements or workflow constraints.
9. Future Expansion: Plan for future scalability by choosing machines that can accommodate increased production demands or technological upgrades.
10. Environmental Impact: Assess the machine’s energy efficiency and environmental footprint to align with sustainability goals.
By considering these factors, you can make informed decisions when purchasing CNC machines for metalworking, ensuring they meet your operational requirements while delivering long-term value and efficiency.
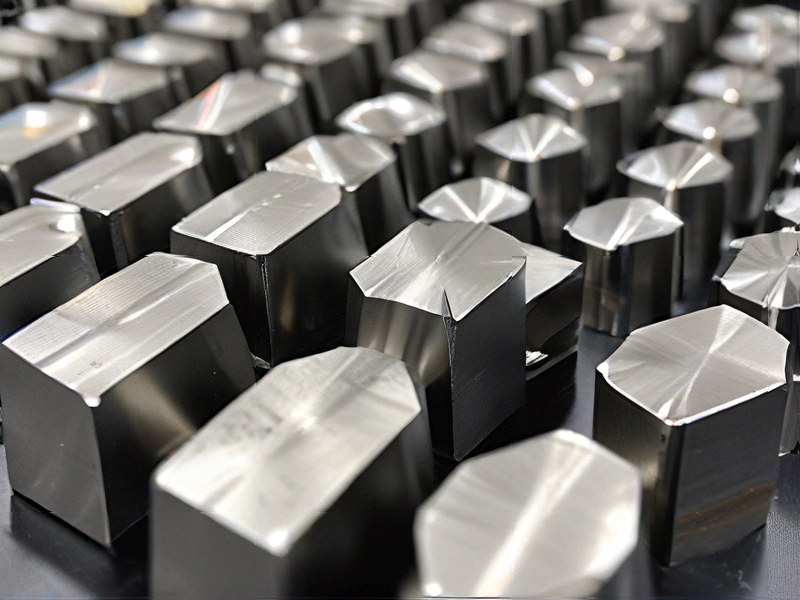
FAQs on Sourcing and Manufacturing from machine cnc metal in China
FAQs on Sourcing and Manufacturing CNC Metal Parts in China
#### Why should I consider sourcing CNC metal parts from China?
China offers competitive pricing, advanced technology, and extensive manufacturing capacity. Many Chinese suppliers have experience with international standards and can provide high-quality parts efficiently.
#### How can I find reliable CNC metal manufacturers in China?
Research online platforms like Alibaba and Global Sources, visit trade shows, or use sourcing agents. Checking references, visiting factories, and reviewing certifications (ISO, CE) can also help ensure reliability.
#### What are the common materials used in CNC metal manufacturing in China?
Manufacturers typically work with aluminum, steel, brass, and titanium. Ensure your supplier has experience with the specific material your project requires.
#### How do I ensure the quality of CNC metal parts?
Request samples before full production, conduct factory audits, and use third-party inspection services. Clear communication about specifications and tolerances is crucial.
#### What is the typical lead time for CNC metal parts from China?
Lead times can vary but generally range from 2 to 6 weeks, depending on complexity, quantity, and current workload of the manufacturer.
#### Are there any minimum order quantities (MOQs) for CNC metal parts?
MOQs vary by supplier. Some may accommodate small orders, while others prefer larger quantities. Negotiating with suppliers can sometimes adjust MOQs to fit your needs.
#### How are shipping and logistics managed for CNC metal parts from China?
Suppliers usually handle shipping via sea or air freight. Work with a freight forwarder to manage customs clearance and delivery. Ensure Incoterms (FOB, CIF, DDP) are clearly defined.
#### What are the payment terms for CNC metal parts in China?
Common payment terms include 30% deposit upfront and 70% balance before shipment. Payment methods typically include wire transfer, PayPal, or Letter of Credit for larger orders.
#### How can I address language barriers and communication issues?
Many suppliers have English-speaking staff. Using clear, simple language and visual aids (drawings, CAD files) can minimize misunderstandings. Regular video calls can also help maintain clear communication.
By addressing these FAQs, you can better navigate the process of sourcing and manufacturing CNC metal parts in China, ensuring quality, efficiency, and cost-effectiveness for your projects.
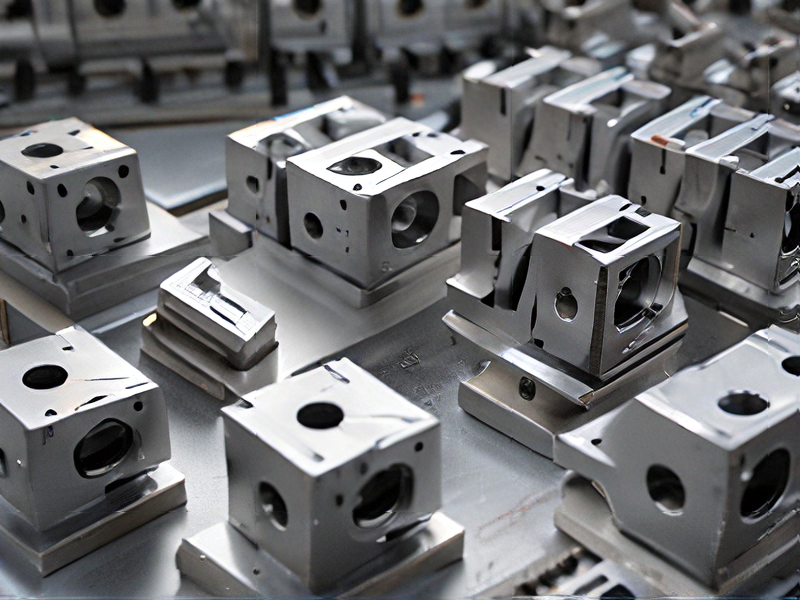