Technology and Applications of machine tooling
Machine tooling encompasses a wide range of technologies and applications essential for manufacturing and production processes. It involves the creation and use of tools to shape, cut, and form materials into desired products. Here are some key technologies and applications:
1. CNC Machining: Computer Numerical Control (CNC) machining uses computerized systems to control machine tools. This technology allows for high precision and automation in cutting, drilling, milling, and turning processes. CNC machines are widely used in automotive, aerospace, and electronics industries.
2. Additive Manufacturing: Also known as 3D printing, additive manufacturing builds objects layer by layer from digital models. It is revolutionizing prototyping and production, enabling complex designs and reducing waste. Applications range from custom medical implants to aerospace components.
3. Laser Cutting: Laser cutting employs focused laser beams to cut or engrave materials with high precision. It is used in industries such as metalworking, automotive, and electronics, offering benefits like clean cuts, minimal material waste, and the ability to cut intricate shapes.
4. Injection Molding: This process involves injecting molten material into molds to produce parts. It is highly efficient for mass production of plastic components, used extensively in consumer goods, medical devices, and automotive parts.
5. Electrical Discharge Machining (EDM): EDM uses electrical discharges (sparks) to shape hard metals and create intricate details that traditional machining methods cannot achieve. It is essential for manufacturing molds, dies, and aerospace components.
6. Grinding and Polishing: These finishing processes enhance the surface quality of components. Grinding removes excess material, while polishing creates a smooth, reflective surface. Applications include manufacturing of precision instruments, optical devices, and decorative items.
Machine tooling technologies enhance production efficiency, precision, and the ability to create complex parts. They are integral to modern manufacturing, driving innovation and enabling the production of high-quality, reliable products across various industries.
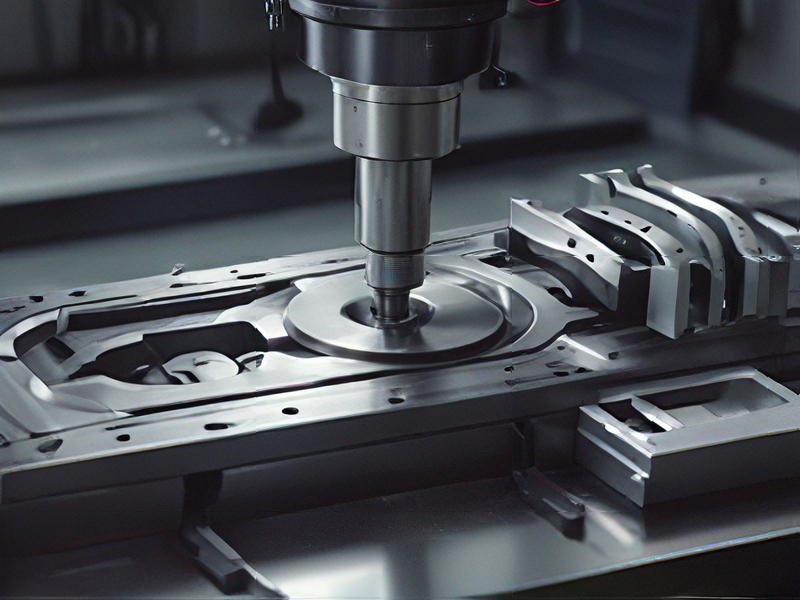
Quality Testing Methods for machine tooling and how to control quality
Quality testing for machine tooling involves several methods to ensure precision, durability, and functionality. Key methods include:
1. Dimensional Inspection: Uses tools like micrometers, calipers, and coordinate measuring machines (CMM) to check the dimensions of machined parts against specified tolerances.
2. Surface Finish Inspection: Utilizes surface profilometers and visual inspection to ensure the surface roughness meets the required standards.
3. Material Testing: Includes hardness testing (Rockwell, Brinell), tensile testing, and metallurgical analysis to confirm the material properties meet specifications.
4. Non-Destructive Testing (NDT): Techniques such as ultrasonic testing, magnetic particle inspection, and dye penetrant inspection to detect internal and surface defects without damaging the part.
5. Performance Testing: Evaluates the functionality and performance of the tool under operating conditions to ensure it performs as expected.
Quality control in machine tooling is maintained through several practices:
1. Process Control: Implementing Statistical Process Control (SPC) to monitor and control the manufacturing process, reducing variability and ensuring consistency.
2. Regular Calibration: Ensuring all measuring instruments and machines are regularly calibrated against known standards to maintain accuracy.
3. Preventive Maintenance: Regularly scheduled maintenance of machines to prevent unexpected breakdowns and ensure consistent performance.
4. Employee Training: Providing ongoing training to operators and inspectors to ensure they are skilled in the latest techniques and standards.
5. Documentation and Traceability: Keeping detailed records of the manufacturing process, inspections, and tests to trace any issues back to their source for prompt resolution.
By integrating these testing methods and control practices, machine tooling processes can achieve high levels of quality and reliability, ensuring that parts meet stringent industry standards.
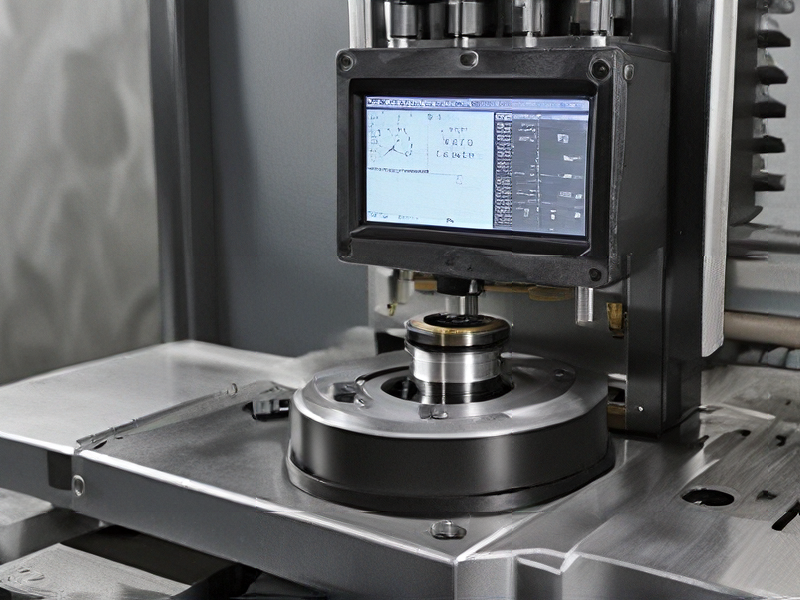
Tips for Procurement and Considerations when Purchasing from machine tooling
Tips for Procurement in Machine Tooling
1. Understand Your Requirements:
– Clearly define the specifications and tolerances needed for your project.
– Consider the materials and types of tooling required (e.g., CNC machines, lathes, milling machines).
2. Research Suppliers:
– Identify reputable suppliers with a track record of delivering high-quality tools.
– Check for certifications such as ISO 9001, which indicates quality management standards.
3. Evaluate Total Cost of Ownership:
– Assess not just the purchase price but also maintenance, spare parts, and operational costs.
– Consider the lifespan and reliability of the tooling.
4. Request Samples or Demos:
– Whenever possible, request samples or live demonstrations to ensure the tooling meets your needs.
– Engage in trial runs to validate performance.
5. Negotiate Terms:
– Negotiate not just on price but also on payment terms, delivery schedules, and warranties.
– Ensure you have a clear agreement on after-sales support and service.
6. Check Compliance:
– Ensure the tooling complies with industry standards and regulations.
– Verify safety features and ergonomics to ensure operator safety and comfort.
7. Supplier Relationship:
– Foster a strong relationship with suppliers for better terms and reliability.
– Regular communication can lead to improved service and potential cost savings.
Considerations When Purchasing Machine Tooling
1. Quality and Precision:
– High precision and quality are critical in machining. Verify the tooling’s accuracy and finish capabilities.
2. Technology and Compatibility:
– Ensure the new tooling is compatible with existing machines and technology.
– Evaluate the ease of integration and potential need for additional training.
3. Scalability:
– Consider if the tooling can handle increased production volumes and complex tasks as your business grows.
4. Maintenance and Downtime:
– Look into the maintenance requirements and the ease of obtaining replacement parts.
– Assess the downtime required for maintenance and repairs to minimize operational disruption.
5. Warranty and Support:
– A comprehensive warranty and readily available technical support can save significant time and money in the long run.
6. Environmental Impact:
– Consider the environmental impact of the tooling, including energy consumption and waste production.
– Look for energy-efficient models and those that support sustainable practices.
By focusing on these tips and considerations, you can make informed procurement decisions that enhance productivity and ensure long-term value in your machine tooling investments.
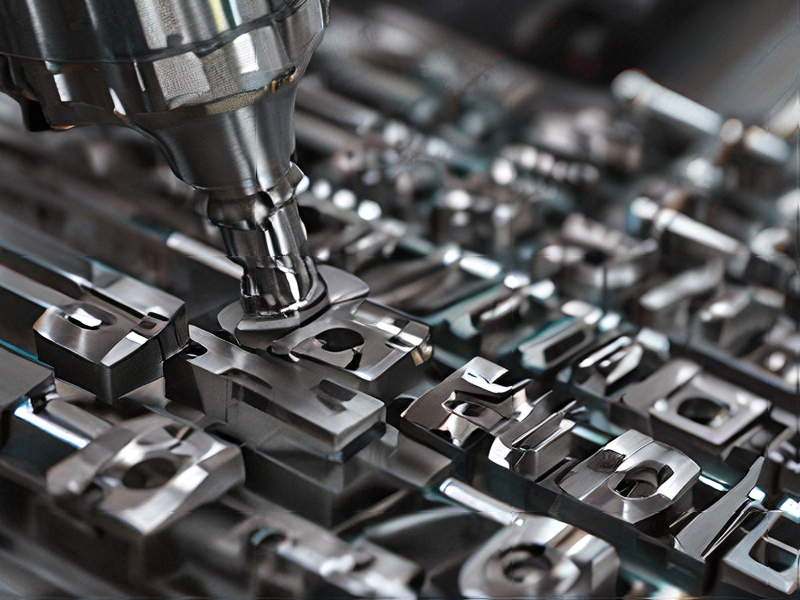
FAQs on Sourcing and Manufacturing from machine tooling in China
## FAQs on Sourcing and Manufacturing from Machine Tooling in China
Q: Where can I find quality machine tooling in China?
A: China boasts numerous reputable manufacturers and suppliers specializing in various machine tools. Online platforms like Alibaba and Global Sources connect you with a wide range of options. Participating in industry trade shows like CIMT (China International Machine Tool Show) also offers valuable opportunities for direct contact with manufacturers.
Q: What factors should I consider when choosing a supplier?
A: Prioritize experience, certifications (e.g., ISO 9001), customer testimonials, and manufacturing capabilities. Request detailed product specifications and inquire about quality control measures.
Q: How can I ensure quality control during manufacturing?
A: Clearly define quality standards in your contract. Conduct on-site inspections at the factory, and request third-party inspection services for added assurance.
Q: What are the typical lead times for machining in China?
A: Lead times vary depending on the complexity of the project and the supplier’s workload. Expect lead times ranging from several weeks to a few months.
Q: What are the payment terms commonly used?
A: Secure payment methods like L/C (Letter of Credit) or escrow services are recommended. Common terms include 30% deposit upon order confirmation and the remaining balance upon shipment.
Q: How can I manage communication with Chinese suppliers?
A: Establish clear communication channels, utilize translation services if needed, and maintain professional conduct throughout the process.
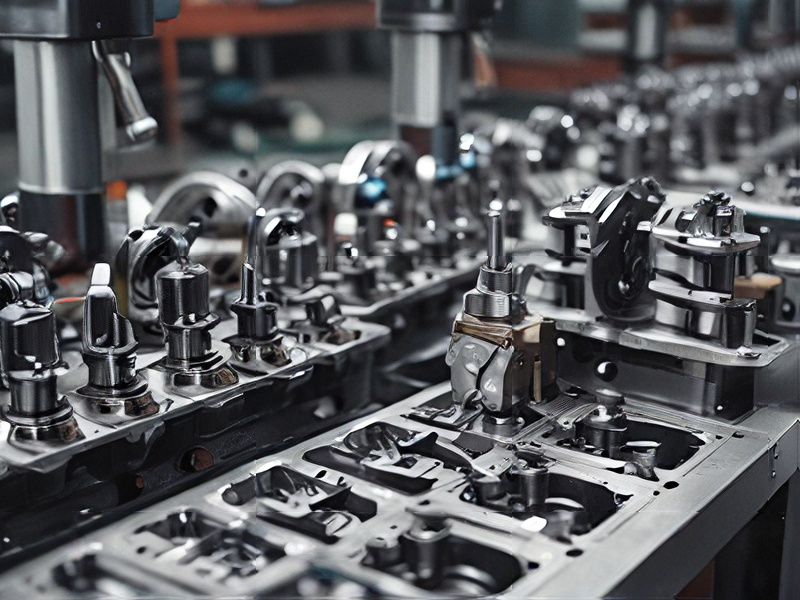