Technology and Applications of machines to cut wood
Modern technology has significantly enhanced the efficiency and precision of woodcutting through various advanced machines. Here are some key types of machines and their applications:
1. Circular Saws: These machines are widely used for cutting wood due to their high-speed rotary motion, which provides smooth and precise cuts. Circular saws come in different forms, including handheld and table-mounted, making them versatile for various woodworking tasks.
2. Band Saws: Featuring a continuous looped blade, band saws are ideal for making irregular or curved cuts. They are particularly useful in resawing, allowing the cutting of thick wood into thinner pieces.
3. Jigsaws: Known for their versatility, jigsaws are perfect for intricate and detailed cuts. Their reciprocating blade can maneuver through curves and angles, making them essential for artistic woodworking projects.
4. Table Saws: Essential for any woodworking shop, table saws provide stability and precision for straight cuts. They are equipped with a circular blade mounted on an arbor, which can be adjusted for depth and angle, enabling bevel cuts.
5. Miter Saws: Specialized for making angled cuts, miter saws are crucial for creating joints, frames, and molding. The blade pivots left or right to produce accurate crosscuts at various angles.
6. Chainsaws: Often used in logging and heavy-duty cutting, chainsaws are powerful tools for felling trees and cutting large logs into manageable pieces. They are available in both electric and gasoline-powered models.
7. CNC Routers: These computer-controlled machines bring automation and precision to woodcutting. CNC routers can execute complex designs and patterns with high accuracy, making them indispensable for modern furniture making and intricate woodwork.
8. Laser Cutters: Utilizing high-powered lasers, these machines offer precision cutting with minimal waste. They are particularly suited for intricate designs and can cut through various thicknesses of wood.
In summary, advancements in woodcutting technology have led to a diverse array of machines, each tailored to specific tasks, from large-scale logging to intricate artistry, enhancing both productivity and creativity in woodworking.
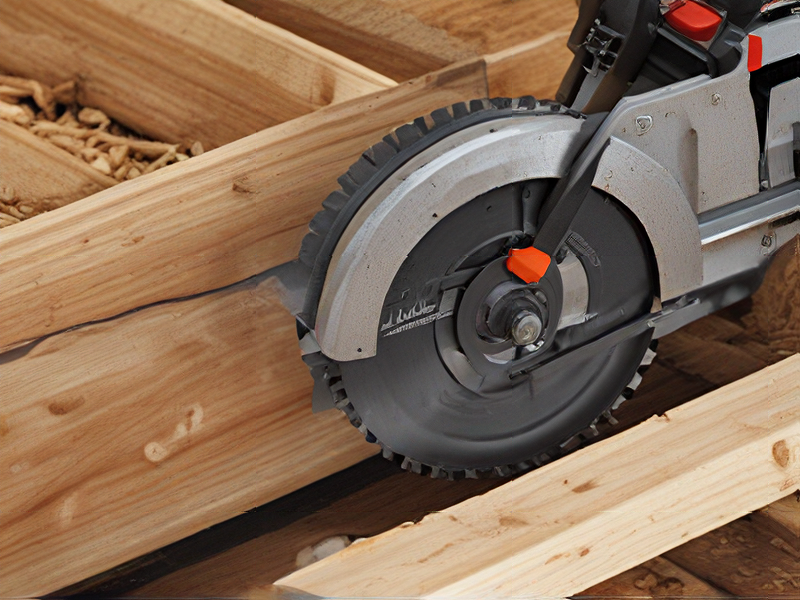
Quality Testing Methods for machines to cut wood and how to control quality
Quality testing for wood-cutting machines involves several methods to ensure precision, safety, and efficiency. Here’s an overview of key testing methods and quality control techniques:
Testing Methods
1. Dimensional Accuracy Testing:
– Method: Use calipers and micrometers to measure the dimensions of the cut pieces.
– Control: Compare measurements against design specifications to ensure precision.
2. Surface Finish Testing:
– Method: Use a surface roughness tester to measure the texture of the cut surface.
– Control: Ensure the surface roughness falls within acceptable limits for the intended application.
3. Blade Sharpness Testing:
– Method: Inspect blades using a microscope or perform a test cut and evaluate the quality.
– Control: Regularly sharpen or replace blades to maintain cutting efficiency.
4. Cutting Speed and Feed Rate Testing:
– Method: Monitor and adjust the machine’s speed and feed rate settings.
– Control: Ensure settings match the material type and desired finish to prevent defects.
5. Load and Vibration Testing:
– Method: Use sensors to monitor machine load and vibrations during operation.
– Control: Adjust machine settings or perform maintenance to reduce excessive load and vibrations.
Quality Control Techniques
1. Regular Calibration:
– Ensure all measuring instruments and machine components are regularly calibrated for accuracy.
2. Standard Operating Procedures (SOPs):
– Develop and follow SOPs for machine setup, operation, and maintenance to ensure consistent quality.
3. Operator Training:
– Train operators on proper machine use, safety protocols, and quality standards.
4. Preventive Maintenance:
– Implement a preventive maintenance schedule to address potential issues before they affect quality.
5. Inspection and Testing Protocols:
– Conduct routine inspections and tests at various stages of the production process to detect and correct any deviations.
6. Data Logging and Analysis:
– Use software to log performance data and analyze trends to identify areas for improvement.
By implementing these testing methods and quality control techniques, manufacturers can ensure their wood-cutting machines consistently produce high-quality cuts.
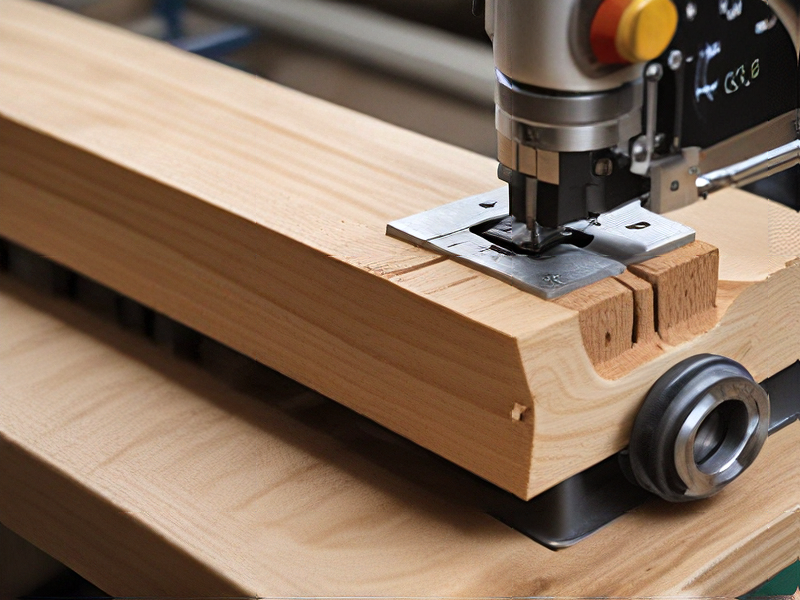
Tips for Procurement and Considerations when Purchasing from machines to cut wood
When procuring machines to cut wood, consider these tips and factors:
1. Assess Your Needs:
– Type of Cutting: Determine the types of cuts (e.g., crosscuts, rip cuts, miters) and the precision required.
– Volume: Estimate the volume of wood you will be processing to choose a machine with adequate capacity.
2. Machine Types:
– Table Saws: Versatile for various cuts, ideal for general woodworking.
– Band Saws: Excellent for curved cuts and resawing.
– Miter Saws: Best for precise angle cuts.
– Circular Saws: Portable, good for rough cuts.
– CNC Routers: Perfect for detailed and repetitive cuts.
3. Quality and Durability:
– Brand Reputation: Opt for brands known for durability and reliability.
– Build Material: Prefer machines with sturdy construction, such as cast iron or high-grade steel.
4. Safety Features:
– Look for features like blade guards, anti-kickback mechanisms, emergency stops, and dust extraction systems.
5. Power and Performance:
– Motor Power: Higher horsepower (HP) provides more cutting power. Choose according to your wood thickness and hardness.
– Cutting Capacity: Ensure the machine can handle the maximum dimensions of wood you’ll be cutting.
6. Ease of Use and Maintenance:
– Adjustability: Machines with easy-to-adjust settings improve efficiency.
– Maintenance: Check the availability of replacement parts and the ease of maintenance tasks.
7. Cost and Budget:
– Initial Cost vs. Long-term Value: Invest in quality to avoid frequent replacements or repairs.
– Warranty and Support: Prefer machines with comprehensive warranties and good customer support.
8. Environment and Space:
– Ensure you have adequate space and suitable working conditions, including ventilation and noise control.
9. Regulatory Compliance:
– Ensure the machine complies with local safety and environmental regulations.
By carefully evaluating these factors, you can make an informed decision, ensuring the procurement of efficient, safe, and reliable wood-cutting machines that meet your specific needs.
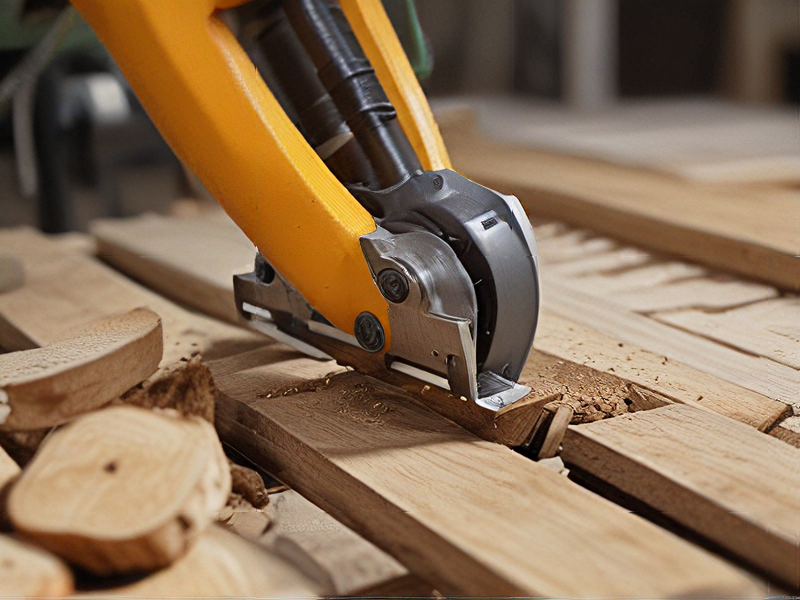
FAQs on Sourcing and Manufacturing from machines to cut wood in China
FAQs on Sourcing and Manufacturing Wood Cutting Machines in China
1. Why source wood cutting machines from China?
China offers competitive pricing, advanced technology, and a wide variety of wood cutting machines. Manufacturers here often provide customizable solutions and have a reputation for timely delivery.
2. What types of wood cutting machines are available?
China produces a range of wood cutting machines including CNC routers, laser cutting machines, band saws, circular saws, and panel saws. These machines cater to different levels of precision, efficiency, and production capacity.
3. How do I find reliable manufacturers?
Use platforms like Alibaba, Made-in-China, and Global Sources. Look for manufacturers with high ratings, good reviews, and verified certifications. Visiting trade shows and contacting trade associations can also help.
4. What certifications should I look for?
Ensure the machines have certifications such as CE, ISO9001, and other relevant quality and safety standards. These certifications indicate compliance with international regulations and standards.
5. How can I verify the quality of the machines?
Request samples, visit the manufacturer’s factory, or hire third-party inspection services. Additionally, ask for references or case studies from previous clients.
6. What is the typical lead time for manufacturing?
Lead times can vary depending on the machine complexity and order size. Generally, it ranges from 30 to 90 days. Always confirm with the manufacturer.
7. What payment terms are common?
Common payment terms include T/T (telegraphic transfer), L/C (letter of credit), and sometimes PayPal for smaller transactions. A typical arrangement might be 30% upfront and 70% before shipment.
8. How is shipping handled?
Manufacturers usually handle the logistics and can arrange shipping via sea or air. Ensure that the shipping terms (FOB, CIF, etc.) are clearly agreed upon and documented.
9. What about after-sales support?
Verify the availability of after-sales support, including installation, training, and maintenance services. Check if the manufacturer provides a warranty and spare parts.
10. Are there any import regulations to be aware of?
Yes, check your country’s import regulations regarding machinery, including tariffs, taxes, and any necessary certifications. It’s advisable to work with a customs broker to navigate these requirements.
For detailed guidance, consulting with industry experts or local trade offices can be beneficial.
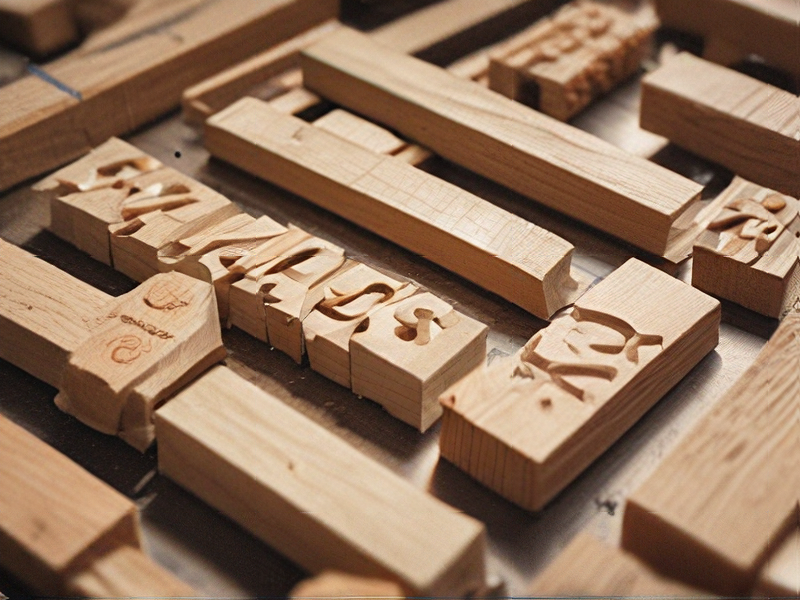