Technology and Applications of machining center
A machining center is a highly versatile manufacturing tool used in various industries for precision machining operations. It combines several machining processes into one unit, enhancing efficiency and accuracy in production.
Technology: Machining centers are equipped with computer numerical control (CNC) systems, which allow for precise control over movement and positioning of the cutting tool. Modern machining centers often feature advanced CNC capabilities, including multi-axis control (3-axis, 4-axis, 5-axis, etc.) for complex machining tasks. High-speed spindles with variable speed control enable efficient cutting of different materials, from metals to composites.
Applications: Machining centers find application in industries such as aerospace, automotive, electronics, and medical device manufacturing, among others. They are used for tasks such as milling, drilling, tapping, boring, and contouring. Key applications include:
1. Prototyping and Production: Machining centers are crucial for both prototyping new designs and mass-producing precision components with consistent quality.
2. Complex Geometries: They excel in machining complex shapes and contours that require high precision, such as turbine blades or medical implants.
3. Efficiency and Flexibility: With their ability to perform multiple operations in a single setup, machining centers reduce production time and increase efficiency compared to traditional machining methods.
4. High Accuracy and Repeatability: CNC control ensures precise machining with tight tolerances, essential for parts requiring exact dimensions and surface finishes.
5. Customization: Machining centers can be programmed to handle diverse materials and geometries, making them adaptable to changing production needs.
In summary, machining centers represent a cornerstone of modern manufacturing due to their technological sophistication, versatility, and ability to enhance productivity across various industries. Their integration of advanced CNC technology enables the efficient production of complex parts with high accuracy and repeatability, meeting the stringent demands of today’s manufacturing environment.
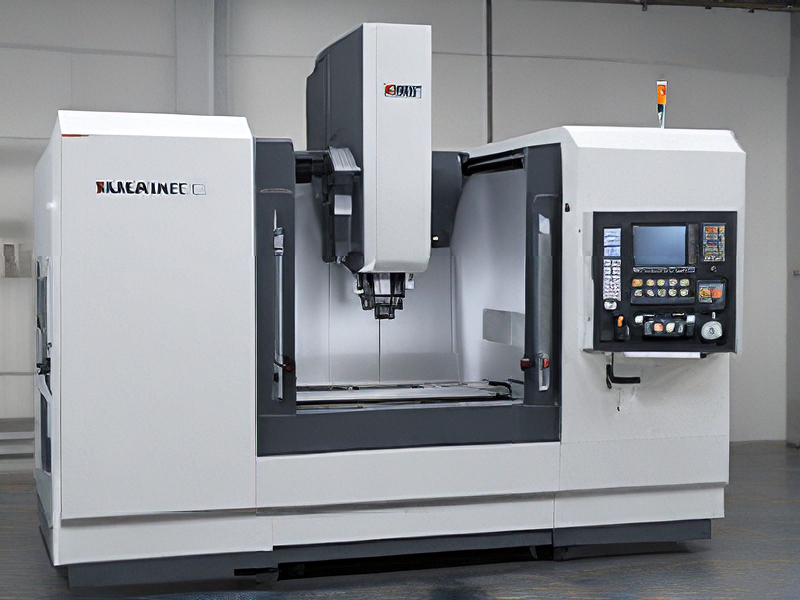
Quality Testing Methods for machining center and how to control quality
Quality testing methods for machining centers typically involve both in-process and final inspection techniques to ensure precision and adherence to specifications. Here are key methods and controls:
1. Dimensional Inspection: Utilizes precision measuring tools like calipers, micrometers, and coordinate measuring machines (CMMs) to verify critical dimensions and tolerances of machined parts.
2. Surface Finish Analysis: Measures surface roughness using profilometers to ensure parts meet specified finish requirements, crucial for functional and aesthetic purposes.
3. Geometric Accuracy: Checks geometric features such as straightness, flatness, roundness, and perpendicularity using tools like dial indicators and laser alignment systems.
4. Tool Wear Monitoring: Monitors tool wear and cutting conditions through sensors and periodic inspections to maintain consistent machining quality and prevent defects.
5. Material Analysis: Conducts material composition analysis and hardness testing to verify material integrity and suitability for intended applications.
To control quality effectively:
1. Establish Standard Operating Procedures (SOPs): Document procedures for machine setup, operation, and maintenance to ensure consistency and traceability in production.
2. Implement Statistical Process Control (SPC): Monitors key process parameters (e.g., tool wear, dimensional accuracy) using statistical techniques to detect trends or deviations early.
3. Regular Maintenance and Calibration: Schedule routine maintenance for machines and calibration of measuring instruments to uphold accuracy and reliability.
4. Employee Training: Provide ongoing training to operators and inspectors on quality standards, inspection methods, and machine operation to enhance competency and awareness.
5. Quality Management Systems (QMS): Adhere to ISO standards or industry-specific QMS frameworks to ensure systematic control and continuous improvement of processes.
By integrating these methods and controls, machining centers can consistently produce high-quality components that meet customer requirements and regulatory standards.
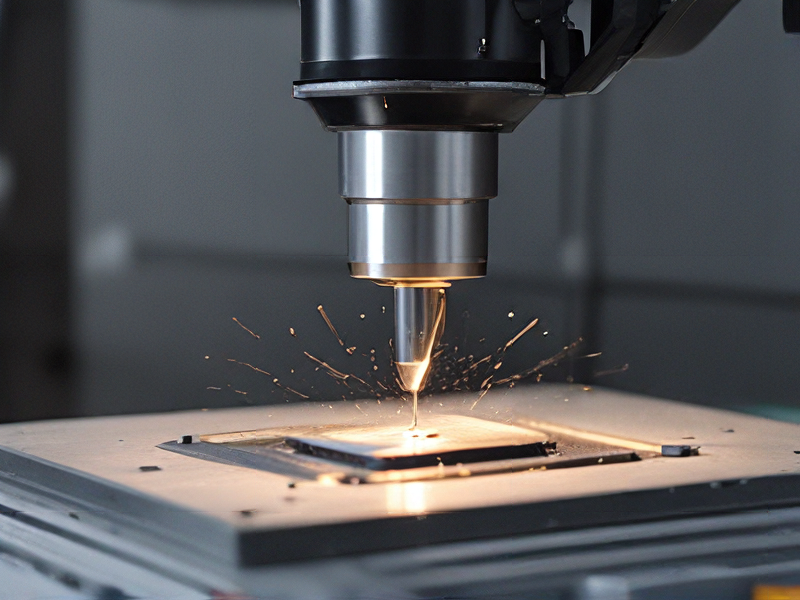
Tips for Procurement and Considerations when Purchasing from machining center
When procuring from a machining center, consider these key tips and considerations to ensure a successful purchase:
1. Define Your Requirements
– Specifications: Clearly define the technical specifications required for your parts, including dimensions, tolerances, materials, and finishes.
– Volume: Determine the quantity needed and whether it’s a one-time order or recurring demand.
2. Vendor Evaluation
– Reputation: Research the machining center’s reputation in the industry through reviews, references, and case studies.
– Certifications: Verify certifications like ISO 9001 for quality management and AS9100 for aerospace standards.
3. Technical Capabilities
– Machinery: Ensure the machining center has the necessary equipment and technology, such as CNC machines, multi-axis machining, and CAD/CAM capabilities.
– Expertise: Evaluate the skill level of the workforce and their experience with similar projects.
4. Quality Assurance
– Inspection Processes: Check the machining center’s quality control measures, including in-process inspections and final product testing.
– Documentation: Require detailed inspection reports and material certifications.
5. Lead Time and Flexibility
– Turnaround Time: Confirm the lead times and ensure they align with your project schedule.
– Scalability: Assess the machining center’s ability to handle future increases in order volume.
6. Cost Considerations
– Quotations: Obtain detailed quotes that include all costs, such as setup fees, material costs, machining costs, and shipping.
– Value: Consider the balance between cost and quality; the cheapest option may not always provide the best value.
7. Communication and Support
– Project Management: Ensure there is a dedicated project manager or point of contact.
– Customer Service: Evaluate the responsiveness and helpfulness of the support team.
8. Logistics and Supply Chain
– Location: Consider the proximity of the machining center to your facilities to reduce shipping costs and lead times.
– Supply Chain Reliability: Ensure the machining center has a reliable supply chain for raw materials.
By meticulously evaluating these aspects, you can select a machining center that meets your technical needs, quality standards, and budget constraints.
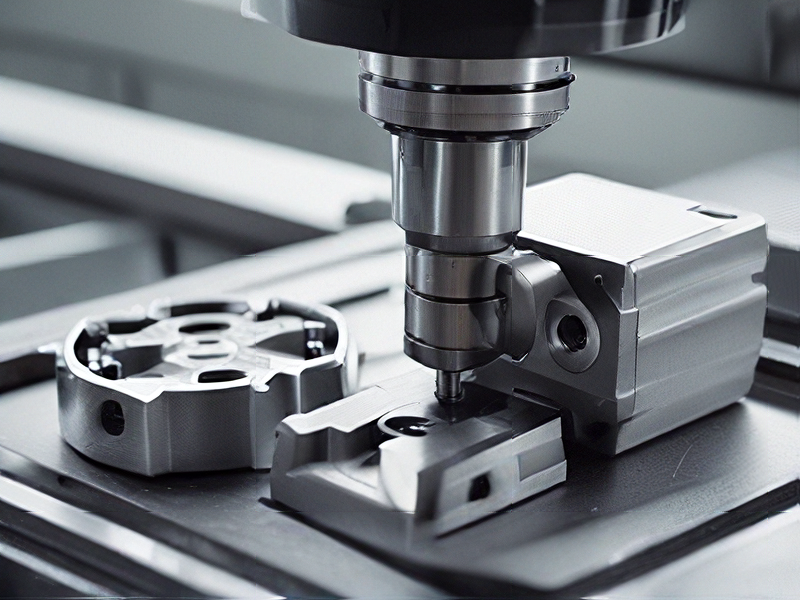
FAQs on Sourcing and Manufacturing from machining center in China
Certainly! Here are some frequently asked questions (FAQs) regarding sourcing and manufacturing from a machining center in China:
1. What are the advantages of sourcing from a machining center in China?
Sourcing from China offers cost advantages due to lower labor and production costs compared to many Western countries. Additionally, Chinese machining centers often have advanced technology and infrastructure to handle large-scale production volumes.
2. How can I ensure quality when sourcing from China?
Quality assurance can be achieved through rigorous supplier selection processes, regular inspections, and implementing quality control measures at various stages of production. It’s crucial to establish clear quality standards and communicate expectations effectively with the machining center.
3. What factors should I consider when choosing a machining center in China?
Factors to consider include the machining center’s expertise in your specific industry, their production capacity, quality certifications (such as ISO), their track record with other clients, and their ability to meet your timeline and logistics requirements.
4. What are the typical lead times when manufacturing in China?
Lead times can vary depending on factors such as the complexity of the parts, order volume, and current production schedule. Typically, lead times range from a few weeks to a few months, so it’s essential to plan accordingly and factor in shipping times.
5. How can I manage logistics and shipping from China?
Partnering with a reliable freight forwarder or logistics company experienced in shipping from China is recommended. They can handle customs clearance, shipping arrangements, and ensure your products reach their destination safely and on time.
6. What are the potential challenges of sourcing from China?
Challenges may include language barriers, cultural differences, intellectual property protection, and occasional fluctuations in quality or production delays. Mitigating these risks involves thorough research, clear contracts, and regular communication with your Chinese partners.
7. How can I stay updated on industry trends and regulations in China?
Keeping in touch with industry associations, attending trade shows, and leveraging local contacts or consultants in China can help you stay informed about market trends, regulatory changes, and emerging technologies.
Navigating sourcing and manufacturing from a machining center in China requires careful planning, clear communication, and a proactive approach to quality control and logistics management.
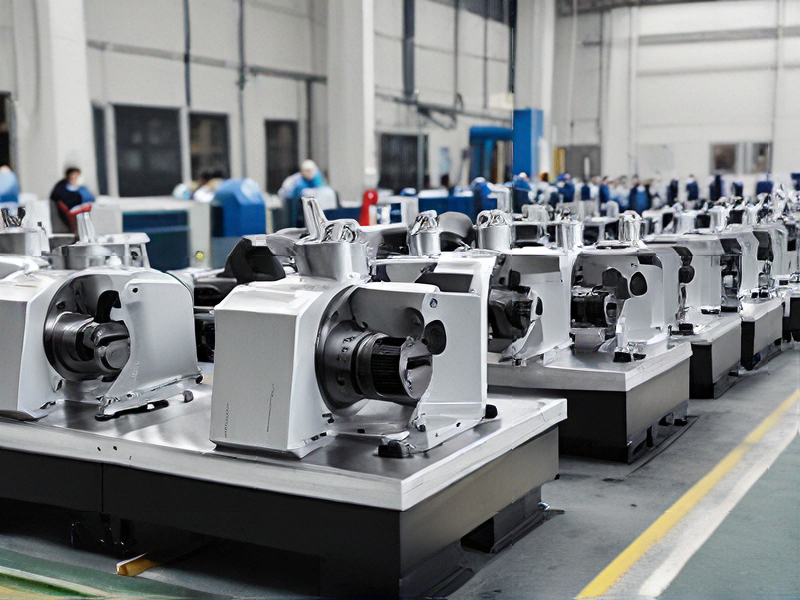