Technology and Applications of machining industry
The machining industry is pivotal in manufacturing, transforming raw materials into precise components. Technologies in this field have evolved, enhancing efficiency, precision, and versatility.
Key Technologies:
1. Computer Numerical Control (CNC)
– Description: CNC machines automate control through computers, executing pre-programmed sequences.
– Applications: Used in milling, turning, and drilling, CNC allows for high precision in automotive, aerospace, and medical device manufacturing.
2. Additive Manufacturing (3D Printing)
– Description: Builds components layer by layer from digital models.
– Applications: Ideal for prototyping and producing complex geometries, it’s widely used in aerospace, healthcare, and custom manufacturing.
3. Electrical Discharge Machining (EDM)
– Description: Uses electrical discharges to shape materials, particularly hard metals.
– Applications: Suitable for creating intricate parts and molds, primarily in the tool and die industry.
4. Laser Cutting
– Description: Employs laser beams to cut or engrave materials.
– Applications: Common in electronics, automotive, and textile industries for precision cutting and engraving.
5. Robotic Machining
– Description: Integrates robots for tasks like welding, cutting, and assembly.
– Applications: Enhances flexibility and efficiency in automotive and electronics manufacturing.
Advancements and Applications:
– Automation and IoT Integration: Smart factories use IoT to monitor and optimize machining processes, improving productivity and reducing downtime.
– Advanced Materials: Machining advanced composites and superalloys used in aerospace and medical implants.
– Sustainability: Eco-friendly machining practices, like dry machining and recycling cutting fluids, are gaining traction.
Conclusion:
The machining industry’s advancements enable high-precision manufacturing across various sectors. Continuous innovation in technologies like CNC, 3D printing, and IoT integration is driving efficiency, sustainability, and new application possibilities.
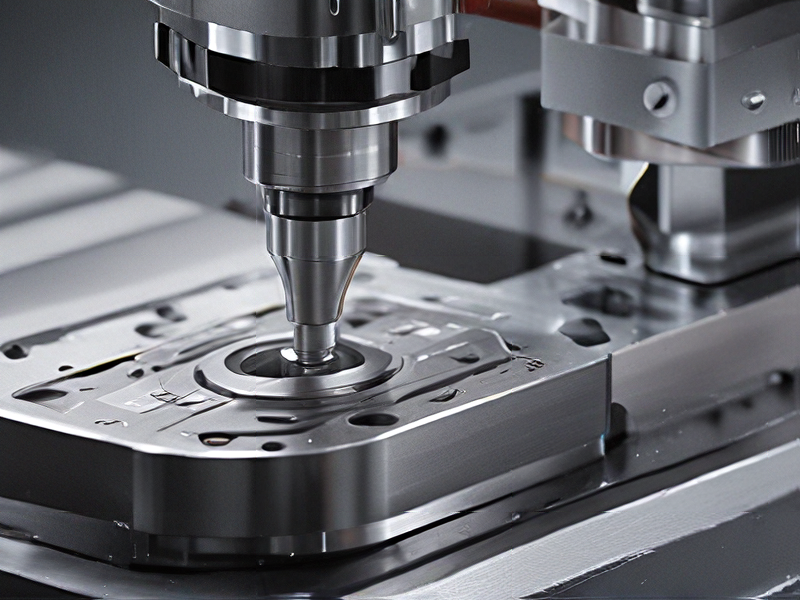
Quality Testing Methods for machining industry and how to control quality
In the machining industry, ensuring high-quality standards is crucial to meet customer requirements and maintain operational efficiency. Here are key quality testing methods and control measures:
1. Dimensional Inspection: Utilizing precision measuring tools like calipers, micrometers, and coordinate measuring machines (CMMs) to verify dimensional accuracy of machined parts.
2. Surface Roughness Measurement: Assessing the texture of machined surfaces using profilometers or surface roughness testers to ensure they meet specified standards.
3. Visual Inspection: Conducting visual checks to detect surface defects, tool marks, burrs, or other imperfections that could affect product performance or aesthetics.
4. Non-Destructive Testing (NDT): Techniques such as ultrasonic testing (UT), magnetic particle inspection (MPI), or dye penetrant testing (PT) to identify internal flaws without compromising the integrity of the part.
5. Statistical Process Control (SPC): Monitoring machining processes using control charts to detect variations and maintain process stability within predefined tolerances.
6. Quality Management Systems (QMS): Implementing standards like ISO 9001 to establish procedures for quality control, documentation, and continuous improvement.
To control quality effectively, integrate these methods into a comprehensive Quality Assurance (QA) program. This includes:
– Training: Ensuring operators are trained in inspection techniques and understand quality requirements.
– Documentation: Maintaining detailed records of inspections, tests, and process parameters.
– Feedback Loops: Using feedback from inspections to identify root causes of defects and implement corrective actions.
– Supplier Quality Management: Establishing criteria for supplier evaluation and monitoring to ensure incoming materials meet specifications.
By combining rigorous testing methods with robust quality control measures, machining companies can consistently deliver products that meet customer expectations and regulatory standards, fostering trust and reliability in their offerings.
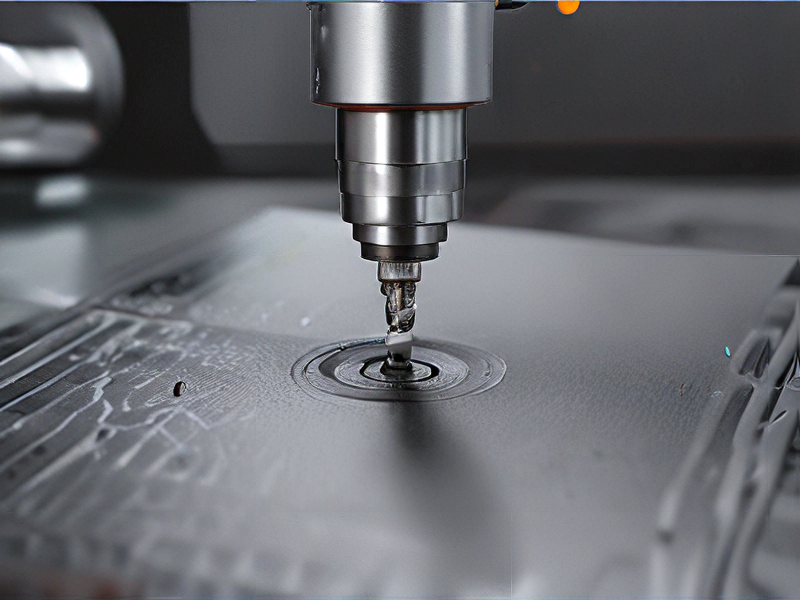
Tips for Procurement and Considerations when Purchasing from machining industry
When engaging in procurement from the machining industry, several key considerations can enhance the process:
1. Supplier Evaluation: Assess suppliers based on their experience, capabilities, certifications (like ISO standards), and track record in delivering similar components or products. Request samples or visit their facilities if possible to gauge quality firsthand.
2. Quality Standards: Ensure that suppliers adhere to stringent quality control measures. Discuss inspection protocols, certifications, and their commitment to meeting industry standards relevant to your requirements.
3. Cost and Value: While cost is crucial, consider overall value. Evaluate pricing in relation to quality, reliability, lead times, and after-sales support. Look for suppliers offering competitive rates without compromising on quality.
4. Capacity and Scalability: Verify if the supplier can handle your current and future needs. Assess their production capacity, flexibility, and ability to scale production if your demands increase.
5. Communication and Transparency: Clear communication channels are vital. Ensure suppliers are responsive and transparent about their processes, timelines, and potential challenges. Establishing good communication upfront fosters a smoother procurement process.
6. Risk Management: Identify potential risks such as supply chain disruptions, material shortages, or production delays. Discuss contingency plans and how the supplier mitigates such risks to maintain continuity.
7. Ethical and Sustainability Practices: Verify if suppliers adhere to ethical business practices and sustainability standards. This includes compliance with environmental regulations, responsible sourcing of materials, and labor practices.
8. Contractual Agreements: Formalize agreements with detailed contracts outlining specifications, pricing, delivery schedules, quality benchmarks, and dispute resolution mechanisms. Clearly define terms and conditions to avoid misunderstandings.
By prioritizing these considerations, you can optimize procurement from the machining industry, ensuring you partner with reliable suppliers capable of meeting your quality, cost, and delivery expectations.
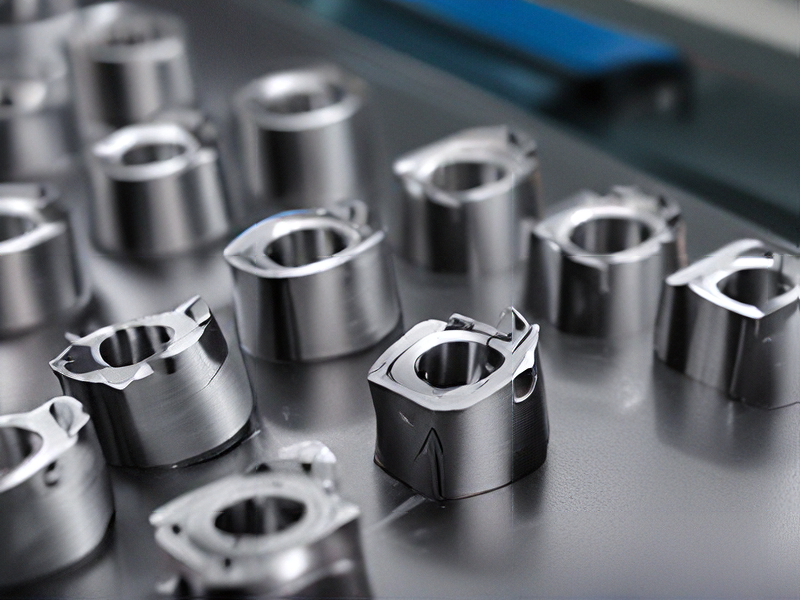
FAQs on Sourcing and Manufacturing from machining industry in China
FAQs on Sourcing and Manufacturing from the Machining Industry in China
#### 1. Why Source from China?
China offers competitive pricing, a wide range of manufacturers, and advanced technology in machining. The large production capacity and expertise in various machining processes make it an attractive sourcing destination.
#### 2. What Types of Machining Services Are Available?
Chinese manufacturers provide services including CNC machining, turning, milling, drilling, grinding, and precision machining. They can handle a variety of materials like metals, plastics, and composites.
#### 3. How to Find Reliable Manufacturers?
Use platforms like Alibaba, Made-in-China, and Global Sources. Conduct thorough due diligence, including verifying certifications, requesting references, and reviewing past work samples.
#### 4. What Quality Standards Are Followed?
Many Chinese manufacturers adhere to international standards such as ISO 9001, ISO/TS 16949, and AS9100. Ensure your supplier complies with these standards to guarantee quality.
#### 5. What Are the Common Challenges?
Challenges include language barriers, cultural differences, and potential quality issues. Mitigate these by maintaining clear communication, using a third-party inspection service, and visiting the supplier if possible.
#### 6. How Does Intellectual Property (IP) Protection Work?
While IP protection can be a concern, mitigate risks by using Non-Disclosure Agreements (NDAs), working with manufacturers who respect IP rights, and considering legal action if necessary.
#### 7. What Are the Payment Terms?
Common payment terms include a 30% upfront deposit with the balance paid before shipment. Letter of Credit (LC) and escrow services can provide additional security.
#### 8. How to Handle Logistics and Shipping?
Choose reliable freight forwarders and consider options like FOB (Free on Board) or CIF (Cost, Insurance, and Freight) terms. Understand import duties and customs regulations in your country.
#### 9. What Are the Lead Times?
Lead times vary based on complexity and order size but typically range from 4 to 12 weeks. Ensure clear agreements on timelines to avoid delays.
#### 10. How to Ensure Ongoing Quality Control?
Regular audits, quality inspections, and maintaining strong relationships with suppliers are essential. Utilize third-party quality control services for consistent standards.
By addressing these FAQs, businesses can navigate the complexities of sourcing and manufacturing in China’s machining industry more effectively.
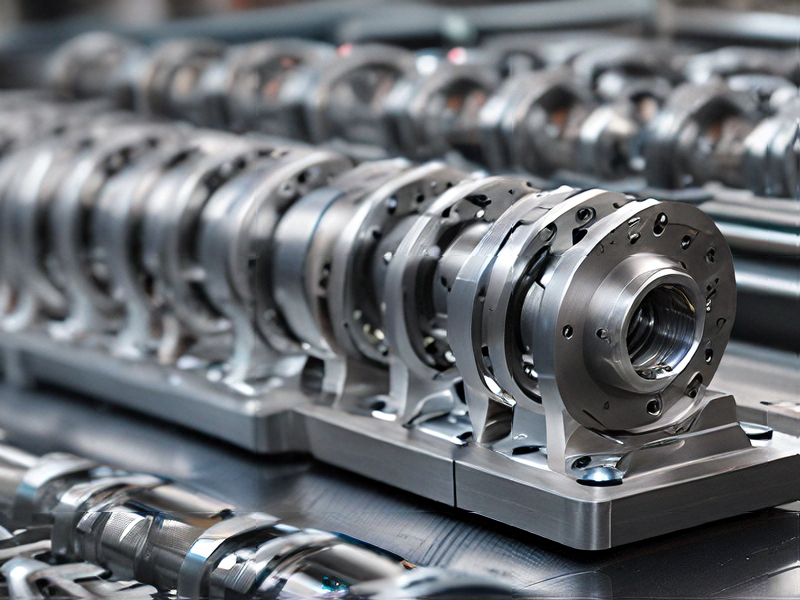