Technology and Applications of metal composition of brass
Brass is an alloy primarily composed of copper and zinc, with the proportions of zinc varying from 5% to 40%. The specific composition determines its mechanical properties, making brass versatile for various applications.
Composition and Properties
– Copper: Typically 60%-80%, provides corrosion resistance, malleability, and electrical conductivity.
– Zinc: Ranges from 5%-40%, enhances strength and ductility. Higher zinc content increases strength but reduces corrosion resistance.
– Additional Elements: Sometimes includes tin, iron, aluminum, silicon, or lead to improve machinability, strength, or corrosion resistance.
Applications
1. Musical Instruments: Brass’s acoustic properties and ease of shaping make it ideal for instruments like trumpets, trombones, and tubas.
2. Plumbing and HVAC: Due to its corrosion resistance and malleability, brass is used in valves, fittings, and pipes. Its non-sparking nature makes it safe for use in explosive environments.
3. Decorative Items: Its gold-like appearance and workability make it popular for decorative hardware, jewelry, and architectural trim.
4. Electrical Components: Brass’s good conductivity and durability suit it for electrical connectors, terminals, and battery clamps.
5. Marine Hardware: The alloy’s resistance to saltwater corrosion makes it ideal for ship fittings, propellers, and marine fasteners.
Technological Advances
Modern advancements in brass technology focus on improving its properties for specific applications. Lead-free brass, developed for plumbing to meet health regulations, is one example. Additionally, metallurgical techniques like continuous casting and advanced heat treatments enhance the material’s uniformity and mechanical properties.
In summary, brass’s variable composition allows for tailored properties, making it an essential material across diverse industries due to its corrosion resistance, malleability, strength, and aesthetic appeal.
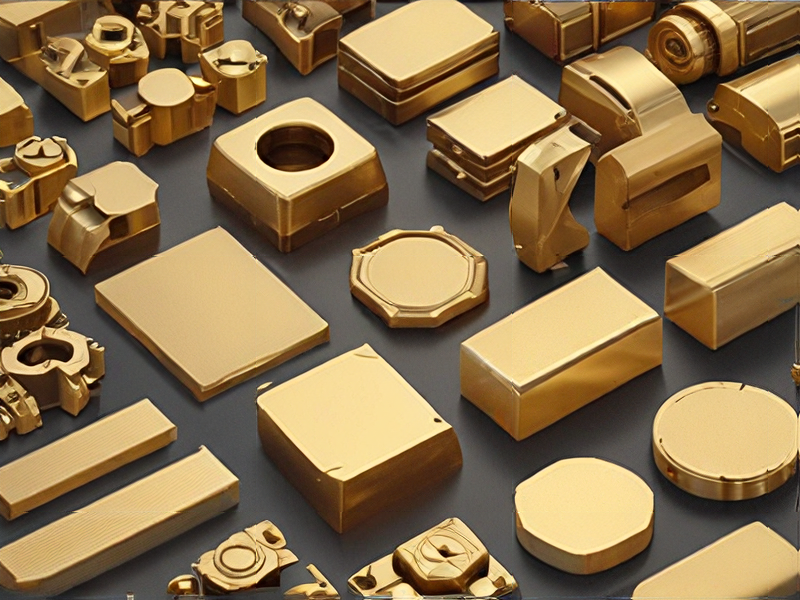
Quality Testing Methods for metal composition of brass and how to control quality
Quality testing methods for brass typically involve a combination of chemical analysis and mechanical testing. Here are some key methods:
1. Chemical Composition Analysis: Determining the exact percentages of copper, zinc, and other alloying elements in brass is crucial. This is often done using techniques like:
– X-ray Fluorescence (XRF): Provides quick and non-destructive elemental analysis.
– Optical Emission Spectroscopy (OES): Precisely measures elemental composition using sparks or arcs.
2. Mechanical Properties Testing: Ensuring brass meets required strength and durability standards involves:
– Tensile Testing: Measures the brass’s strength and ductility by pulling it until it breaks.
– Hardness Testing: Determines resistance to indentation using methods like Rockwell or Brinell tests.
– Impact Testing: Assesses toughness by striking a sample and measuring energy absorption.
3. Microstructural Examination: Evaluates grain size and structure using metallographic techniques such as:
– Metallography: Prepares samples for microscopy to observe grain boundaries and defects.
– Scanning Electron Microscopy (SEM): Provides detailed images and elemental analysis of microstructures.
Quality control involves implementing these methods at various stages of production:
– Incoming Raw Materials Inspection: Ensures alloys meet specifications before use.
– In-process Testing: Monitors production to catch deviations early.
– Final Inspection: Verifies finished product quality before shipment.
By integrating these testing methods and controls, brass manufacturers can maintain consistent quality, optimize processes, and meet customer expectations reliably.
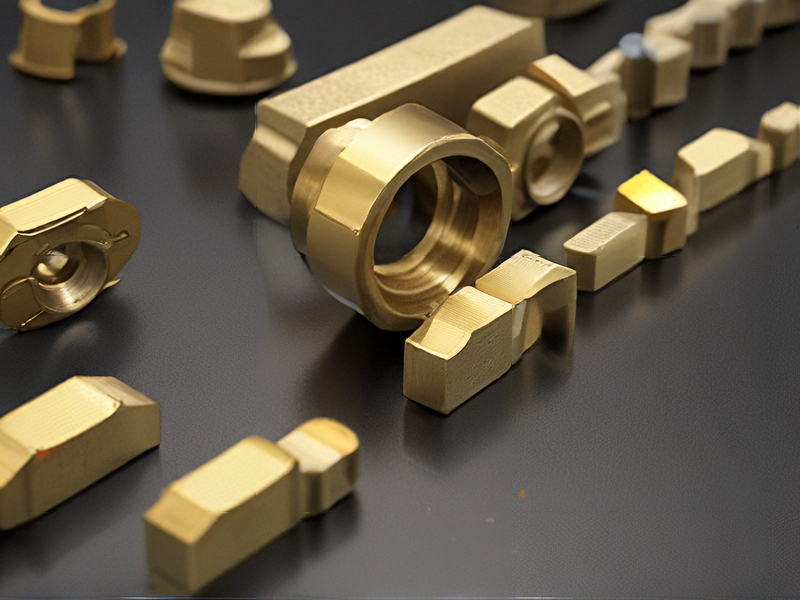
Tips for Procurement and Considerations when Purchasing from metal composition of brass
When procuring brass or items containing brass, several considerations are crucial:
1. Quality Standards: Ensure the brass meets required standards like ASTM or ISO specifications to guarantee durability and performance.
2. Supplier Reliability: Choose suppliers with a proven track record in delivering quality brass products promptly and consistently.
3. Cost Efficiency: Balance cost with quality to optimize procurement budgets without compromising on product integrity.
4. Material Specifications: Verify the alloy composition (e.g., copper-zinc ratios) to align with specific project requirements.
5. Environmental Impact: Assess suppliers’ environmental policies to support sustainability goals and compliance with regulations.
6. Testing and Certification: Request certificates of compliance or test reports to validate material properties and conformity.
7. Logistics and Transportation: Plan for safe transportation methods to prevent damage and ensure timely delivery.
8. Long-term Supplier Relationships: Foster partnerships with reliable suppliers to streamline future procurement processes and ensure continuity.
By focusing on these factors, procurement teams can effectively source brass materials that meet quality, cost, and sustainability objectives for various applications.

FAQs on Sourcing and Manufacturing from metal composition of brass in China
Certainly! Here are some FAQs on sourcing and manufacturing brass in China:
1. What is the typical composition of brass sourced from China?
Brass sourced from China typically consists of copper and zinc, with varying percentages depending on the desired properties such as strength, corrosion resistance, and color.
2. How can I ensure quality when sourcing brass from Chinese manufacturers?
Quality assurance can be ensured by conducting thorough supplier audits, requesting samples for testing, and establishing clear quality specifications in your contracts. It’s also beneficial to work with manufacturers who have certifications like ISO standards.
3. What are the common manufacturing processes used for brass in China?
Chinese manufacturers employ processes such as melting, casting, forging, and machining to produce brass components. Each process can be tailored to meet specific design requirements.
4. Are there environmental considerations when manufacturing brass in China?
Yes, manufacturers in China are increasingly adopting eco-friendly practices to minimize environmental impact. Look for suppliers who adhere to regulations and standards for waste management and emissions control.
5. What are the typical lead times and MOQs (Minimum Order Quantities) when sourcing brass from China?
Lead times and MOQs vary depending on the complexity of the order and supplier capacity. It’s advisable to discuss these details upfront with potential suppliers to align expectations.
6. What are the payment terms usually accepted by Chinese brass manufacturers?
Common payment terms include T/T (Telegraphic Transfer), L/C (Letter of Credit), and occasionally, Alibaba’s Trade Assurance for added security in transactions.
7. How can I address language and communication barriers with Chinese manufacturers?
Utilizing professional translators or working with manufacturers who have English-speaking staff can help overcome language barriers. Clear communication and documentation are essential for avoiding misunderstandings.
These FAQs should provide a solid foundation for navigating sourcing and manufacturing brass components in China effectively.
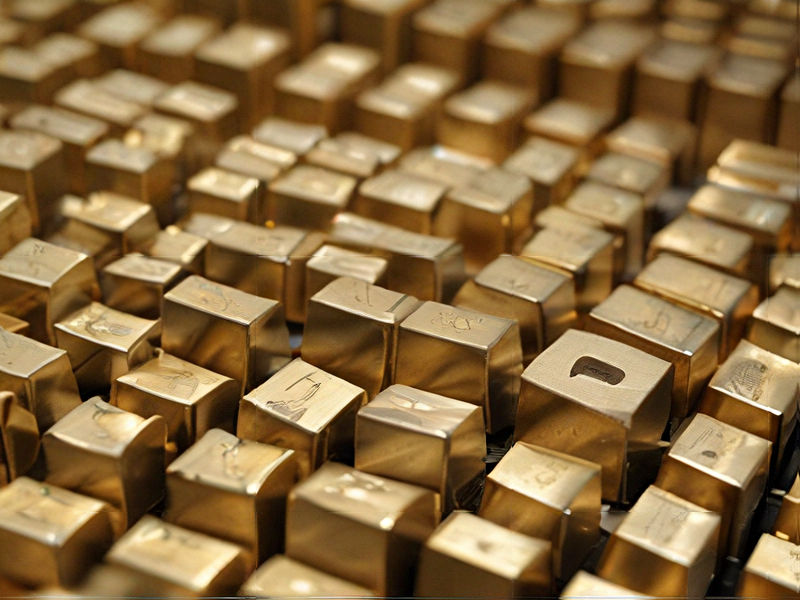