Technology and Applications of metal composition of stainless steel
Stainless steel is a versatile alloy primarily composed of iron, chromium, nickel, and small amounts of other elements like carbon and manganese. This composition provides stainless steel with its unique properties of corrosion resistance, strength, and aesthetic appeal, making it widely used across various industries.
Composition:
1. Iron (Fe): The base metal providing structural integrity and strength.
2. Chromium (Cr): The key element imparting corrosion resistance by forming a passive oxide layer on the surface.
3. Nickel (Ni): Enhances resistance to corrosion and adds toughness.
4. Carbon (C): Strengthens the alloy, but excessive amounts can reduce corrosion resistance.
5. Manganese (Mn): Aids in deoxidation and enhances mechanical properties.
Applications:
1. Construction: Used in building facades, roofing, and structural components due to its durability and aesthetic appeal.
2. Transportation: Stainless steel is crucial in automotive, aerospace, and marine industries for components requiring corrosion resistance.
3. Medical: Preferred for surgical instruments, medical devices, and implants due to its biocompatibility and ease of sterilization.
4. Food and Beverage: Hygienic surfaces for food processing equipment and storage tanks.
5. Energy: Widely used in power generation, oil and gas refining, and renewable energy applications due to its resistance to high temperatures and corrosion.
Conclusion:
Stainless steel’s composition of iron, chromium, nickel, and other elements allows for a wide range of applications where corrosion resistance, strength, and hygiene are crucial. Its versatility across industries underscores its importance in modern technology and manufacturing processes.
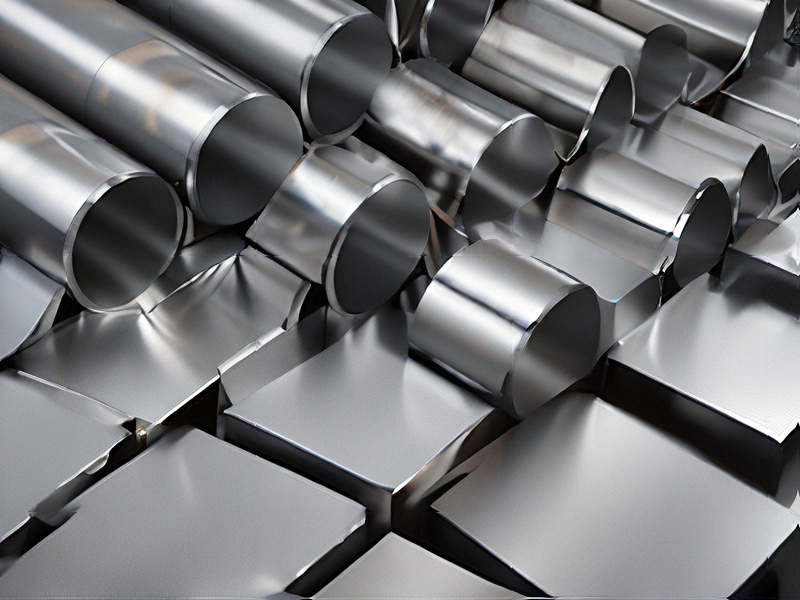
Quality Testing Methods for metal composition of stainless steel and how to control quality
Quality testing methods for the metal composition of stainless steel typically involve several key techniques to ensure consistency and adherence to specifications:
1. Chemical Composition Analysis: Utilizing methods like X-ray fluorescence (XRF) or optical emission spectrometry (OES) to determine the elemental composition of stainless steel. This ensures the correct percentages of alloying elements like chromium, nickel, and others.
2. Carbon Content Testing: Crucial for different grades of stainless steel, carbon content is often tested using combustion analysis or infrared absorption techniques.
3. Microscopic Examination: This includes metallography and scanning electron microscopy (SEM) to inspect the microstructure of stainless steel, ensuring it meets specified grain size and structure requirements.
4. Mechanical Properties Testing: Tensile testing, hardness testing (e.g., Rockwell or Vickers), and impact testing assess the mechanical strength and toughness of stainless steel.
5. Non-Destructive Testing (NDT): Techniques such as ultrasonic testing (UT) or eddy current testing (ECT) are used to detect surface and subsurface defects without damaging the material.
To control quality effectively:
– Establish Clear Specifications: Define precise requirements for chemical composition, mechanical properties, and surface quality.
– Supplier Qualification: Verify supplier capabilities and adherence to standards through audits and certifications.
– Process Control: Implement rigorous process controls to minimize variability in manufacturing, including temperature monitoring, raw material inspection, and calibration of equipment.
– Quality Assurance Testing: Conduct regular and systematic testing throughout production to ensure compliance with specifications.
– Continuous Improvement: Foster a culture of continuous improvement through feedback loops, data analysis, and corrective actions based on quality metrics.
By employing these methods and controls, manufacturers can consistently produce stainless steel with the desired composition and quality, meeting customer expectations and regulatory requirements.
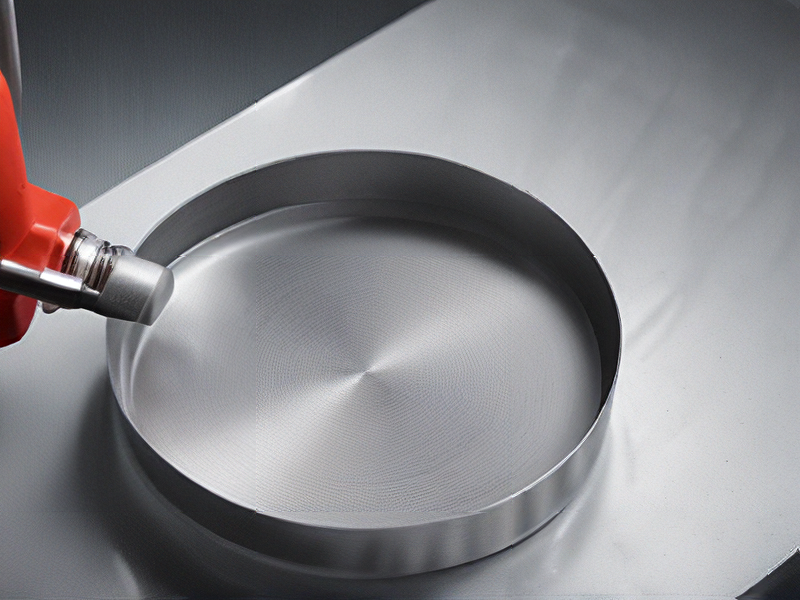
Tips for Procurement and Considerations when Purchasing from metal composition of stainless steel
When procuring stainless steel, consider the following key tips and considerations:
1. Grade Selection: Determine the appropriate grade of stainless steel based on your specific needs, such as corrosion resistance (e.g., 304 for general use, 316 for marine environments), strength requirements, and environmental factors.
2. Quality Assurance: Ensure suppliers adhere to recognized standards (ASTM, EN, etc.) and provide certification to guarantee material quality and traceability.
3. Cost vs. Performance: Balance initial costs with long-term benefits; higher grades may cost more initially but offer better durability and lower maintenance expenses.
4. Supplier Reliability: Choose reputable suppliers with a proven track record for delivering consistent quality and meeting deadlines.
5. Surface Finish: Specify the required surface finish (e.g., polished, brushed) based on aesthetic and functional requirements.
6. Compatibility: Confirm compatibility with other materials in your project to avoid galvanic corrosion or other compatibility issues.
7. Sustainability: Consider the environmental impact of production methods and recyclability of stainless steel grades.
8. Lifecycle Considerations: Assess the expected lifespan of the product and choose stainless steel grades accordingly to minimize replacements and maintenance.
By focusing on these considerations, you can effectively procure stainless steel that meets your project’s requirements for durability, performance, and cost-effectiveness.
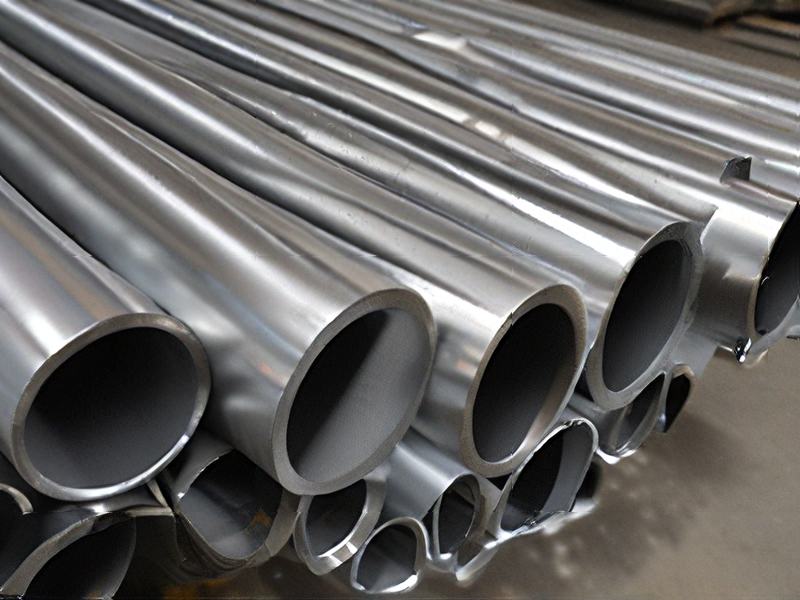
FAQs on Sourcing and Manufacturing from metal composition of stainless steel in China
Certainly! When sourcing stainless steel from China, here are key FAQs to consider:
1. What are the common grades of stainless steel available in China?
China produces a wide range of stainless steel grades, including popular ones like 304 (18-8 stainless, containing 18% chromium and 8% nickel) and 316 (known for its higher corrosion resistance with the addition of molybdenum).
2. How can I ensure the quality of stainless steel sourced from China?
Quality assurance is crucial. Work with suppliers who provide certifications like ISO 9001 and ensure compliance with international standards (ASTM, EN, etc.). Conducting factory audits and requesting samples can also help verify quality.
3. What are the typical manufacturing processes used?
Chinese manufacturers employ processes such as casting, forging, machining, and heat treatment to produce stainless steel components. Clarify with your supplier which methods they utilize and their capabilities.
4. What should I know about lead times and production capacities?
Lead times can vary based on order size, complexity, and current demand. Ensure clear communication with your supplier regarding production timelines and their capacity to meet your requirements.
5. Are there any regulatory considerations when importing stainless steel from China?
Stay informed about import regulations in your country regarding stainless steel, including tariffs, customs duties, and compliance with safety standards (e.g., REACH in the EU).
6. How do I handle logistics and shipping?
Coordinate logistics early in the process to avoid delays. Discuss shipping methods, packaging requirements, and incoterms (FOB, CIF, etc.) with your supplier to streamline the import process.
By addressing these FAQs, you can navigate sourcing stainless steel from China more effectively, ensuring quality, compliance, and smooth logistics for your business needs.
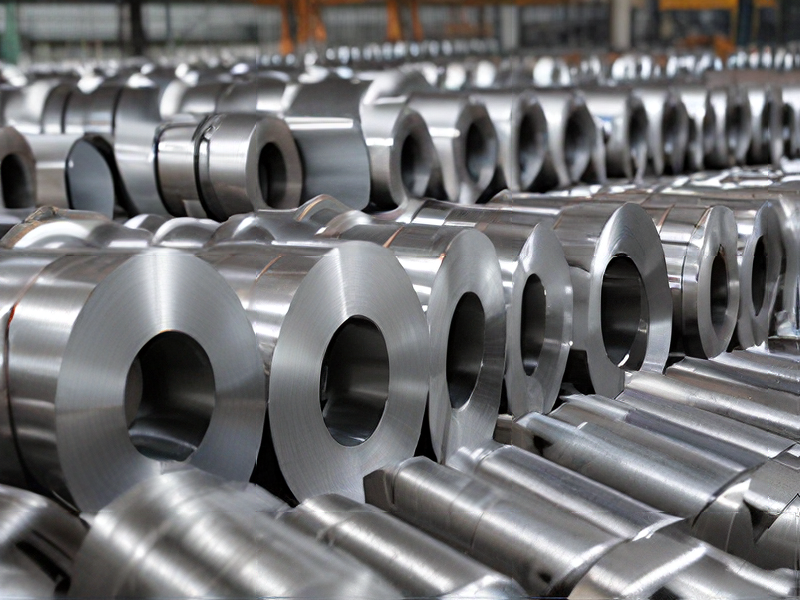