Technology and Applications of metal cutting with laser
Laser cutting technology employs a focused beam of high-intensity light to precisely cut through metals and other materials. This method is favored for its accuracy, speed, and versatility across various industries. In manufacturing, lasers are used extensively for intricate cuts in sheet metal fabrication, allowing for complex designs with minimal material waste.
Key applications include:
1. Industrial Manufacturing: Laser cutting is integral to producing components for automotive, aerospace, and electronics industries. It enables precise shaping of metals like steel, aluminum, and titanium, meeting stringent tolerances and quality standards.
2. Prototyping and Rapid Manufacturing: Its capability to quickly iterate designs makes laser cutting ideal for prototyping. Companies can swiftly produce and test parts before full-scale production, reducing time to market.
3. Micro-machining: In electronics, lasers are employed for micro-cutting and drilling of components like circuit boards and semiconductor materials. This ensures fine detail and high precision crucial for modern electronic devices.
4. Medical Devices: Laser cutting plays a pivotal role in manufacturing medical instruments and implants. It enables the production of intricate shapes and sizes from biocompatible metals, enhancing the precision and functionality of medical devices.
5. Art and Design: Artists and designers utilize laser cutting to create intricate patterns, sculptures, and jewelry from various metals. Its precision allows for detailed customization and artistic expression.
Benefits of laser cutting include minimal material wastage, high cutting speeds, and the ability to cut complex shapes without the need for tool changes. However, challenges such as initial setup costs and the need for skilled operators exist. As technology advances, laser cutting continues to evolve, offering increased efficiency and broader application possibilities in various industries.
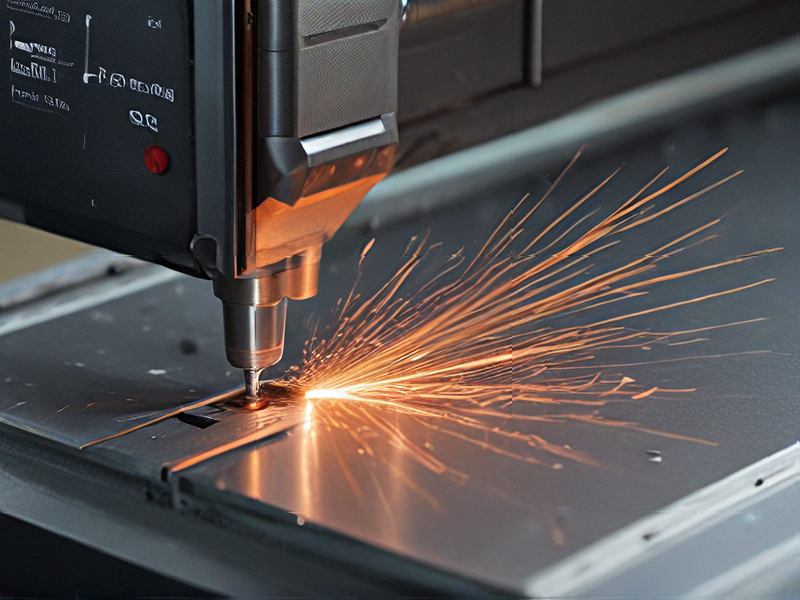
Quality Testing Methods for metal cutting with laser and how to control quality
Quality testing methods for laser metal cutting typically involve a combination of non-destructive techniques and dimensional checks. Non-destructive methods include visual inspection, where operators assess the cut edge for smoothness and consistency. Optical microscopy can be employed to examine the microstructure for any signs of heat damage or irregularities.
Dimensional checks are crucial and often conducted using coordinate measuring machines (CMM) or laser scanning systems to verify part dimensions against CAD specifications. This ensures accuracy within tight tolerances.
Controlling quality begins with precise machine calibration and maintenance to optimize cutting parameters such as power, speed, and focal length. Monitoring these parameters during operation helps maintain consistency and quality.
Additionally, real-time process monitoring using sensors can detect anomalies like deviations in cutting speed or power fluctuations. Statistical process control (SPC) methods analyze these data trends to identify potential issues before they impact quality.
Lastly, implementing a robust quality management system (QMS) that includes documentation, traceability, and regular audits ensures adherence to standards and continuous improvement.
By integrating these methods, manufacturers can achieve high-quality laser-cut metal components consistently, meeting stringent industry requirements.
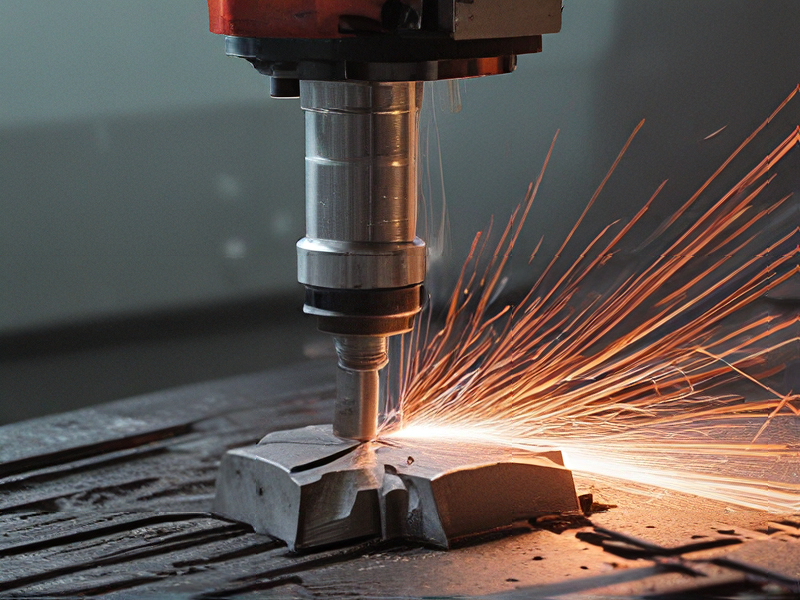
Tips for Procurement and Considerations when Purchasing from metal cutting with laser
When procuring metal cutting services using laser technology, it’s essential to consider several factors to ensure you get the best quality and value. Here are some key tips and considerations:
1. Material Compatibility: Ensure the laser cutting service is compatible with the type of metal you need. Common metals include stainless steel, aluminum, and brass. Verify that the service provider can handle the specific thickness and type of metal.
2. Precision and Accuracy: Laser cutting is known for its precision. Confirm the provider’s capability to meet the tolerances required for your project. This is crucial for parts that need to fit together or meet strict specifications.
3. Cutting Speed: Faster cutting speeds can reduce costs and lead times. However, extremely high speeds may compromise edge quality. Balance speed with the required quality to achieve optimal results.
4. Quality of Cut Edges: Check for smooth and clean cut edges, which reduce the need for secondary finishing processes. Inquire about the provider’s quality control measures to ensure consistent results.
5. Experience and Expertise: Choose a provider with a proven track record in laser cutting. Experienced providers are more likely to deliver high-quality work and offer valuable insights into design improvements and cost-saving measures.
6. Technology and Equipment: Up-to-date laser cutting machines with advanced features can enhance efficiency and precision. Ask about the type and age of the equipment used, as well as the provider’s maintenance practices.
7. Cost: Obtain detailed quotes that include setup fees, material costs, and any additional charges for design adjustments or post-processing. Compare multiple quotes to find the best balance of cost and quality.
8. Turnaround Time: Ensure the provider can meet your deadlines. Discuss lead times and any potential delays upfront to avoid disruptions to your project timeline.
9. Customization and Flexibility: Choose a provider that offers customization options and can handle varying batch sizes. Flexibility in order sizes can be crucial for both prototyping and full-scale production.
10. Customer Service: Good communication and responsive customer service are essential. A reliable provider should be easy to reach, willing to answer questions, and proactive in addressing any concerns.
By carefully considering these factors, you can select a laser cutting service that meets your needs and ensures high-quality results for your metal cutting projects.
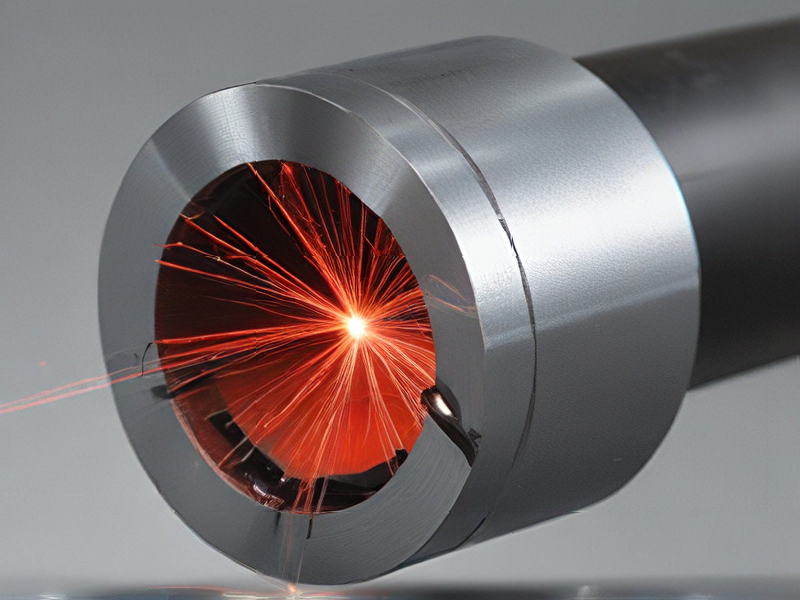
FAQs on Sourcing and Manufacturing from metal cutting with laser in China
Certainly! Here are some frequently asked questions (FAQs) regarding sourcing and manufacturing metal cutting with laser in China:
1. Why should I consider China for laser metal cutting?
China offers competitive pricing due to lower labor and operational costs. It also has a well-established industrial infrastructure supporting advanced manufacturing technologies like laser cutting.
2. What are the advantages of laser cutting for metal in China?
Laser cutting provides high precision, versatility in cutting various metals, and minimal material wastage. In China, manufacturers often use state-of-the-art laser cutting machines, ensuring quality and efficiency.
3. How do I find a reliable laser cutting manufacturer in China?
Research and verify manufacturers through online platforms, industry exhibitions, and referrals. Assess their experience, equipment capabilities, quality certifications (like ISO), and client reviews.
4. What materials can be laser cut in China?
Chinese manufacturers can laser cut a wide range of metals, including stainless steel, aluminum, carbon steel, and alloys. They cater to diverse industrial needs from automotive to electronics.
5. What are the typical lead times for laser cutting orders in China?
Lead times vary based on order complexity and quantity. Generally, Chinese manufacturers offer competitive lead times, often faster than Western counterparts due to streamlined production processes.
6. How can I ensure quality control when sourcing laser cutting services from China?
Specify quality standards in your contract, conduct factory visits or audits if feasible, and request samples or prototypes. Regular communication and clear specifications help ensure the desired quality.
7. What logistics and shipping options are available?
Chinese manufacturers often have established logistics networks for global shipping. They offer flexibility in shipping methods, from sea freight to express air delivery, based on urgency and cost considerations.
Navigating these FAQs can help businesses effectively leverage China’s capabilities in laser metal cutting, ensuring efficient sourcing and manufacturing processes.
