Technology and Applications of metal manufacture
Metal manufacturing technology has evolved significantly, encompassing a wide range of processes and applications across various industries. Key technologies include casting, forging, machining, welding, and additive manufacturing.
1. Casting: This involves pouring molten metal into a mold to create a specific shape. It’s widely used for producing large components and intricate parts in automotive, aerospace, and heavy machinery industries.
2. Forging: In forging, metal is shaped by compressive forces, often using a hammer or press. This process improves the metal’s strength and durability, making it ideal for critical components in aerospace, automotive, and military applications.
3. Machining: This subtractive process involves removing material from a metal workpiece using tools like lathes, mills, and drills. It’s essential for creating precise components in industries such as electronics, medical devices, and automotive.
4. Welding: Welding joins metals by melting their edges and adding filler material to form a strong bond. It’s crucial in construction, shipbuilding, and manufacturing of heavy equipment.
5. Additive Manufacturing (3D Printing): This advanced technology builds metal parts layer by layer from a digital model. It allows for complex geometries and customized solutions, finding applications in aerospace, healthcare, and automotive industries.
Applications
– Automotive: Metal manufacturing produces engine parts, transmission components, and structural frames.
– Aerospace: High-strength, lightweight metals are used for aircraft engines, fuselages, and landing gear.
– Construction: Structural steel and metal frameworks form the backbone of buildings and infrastructure.
– Medical: Precision machining and additive manufacturing produce surgical instruments, implants, and prosthetics.
– Electronics: Metal components are essential in the production of semiconductors, connectors, and housings.
In summary, metal manufacturing technologies are pivotal in producing reliable, high-quality components across diverse industries, driving innovation and efficiency.
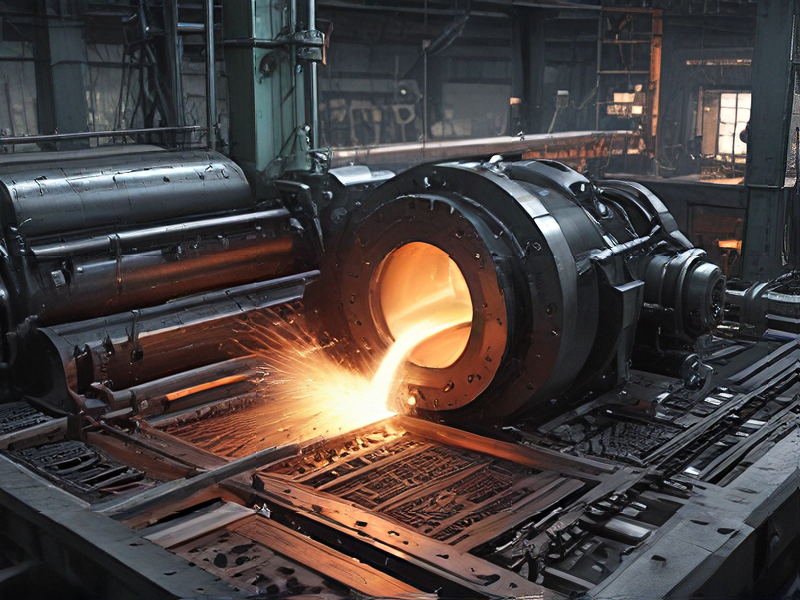
Quality Testing Methods for metal manufacture and how to control quality
Quality testing methods in metal manufacturing are crucial for ensuring product integrity and customer satisfaction. Common methods include:
1. Dimensional Inspection: Using precision tools like calipers, micrometers, and coordinate measuring machines (CMMs) to verify part dimensions against specifications.
2. Visual Inspection: Assessing surface finish, weld quality, and overall appearance to detect defects like cracks, porosity, or irregularities.
3. Mechanical Testing: Evaluating mechanical properties such as tensile strength, hardness, impact resistance, and fatigue through tests like tensile tests, hardness tests (Brinell, Rockwell, Vickers), and impact tests (Charpy, Izod).
4. Non-Destructive Testing (NDT): Methods like ultrasonic testing (UT), magnetic particle testing (MT), dye penetrant testing (PT), and radiographic testing (RT) to detect internal defects without damaging the material.
5. Chemical Analysis: Verifying material composition using techniques such as spectroscopy (XRF, OES), chemical titration, and mass spectrometry.
To control quality effectively:
– Process Control: Implementing standardized manufacturing processes and documenting procedures to minimize variability.
– Quality Management Systems (QMS): Adhering to ISO 9001 or similar standards to ensure consistency and traceability in production.
– Training and Skills Development: Ensuring operators are trained in testing methods and interpretation of results to enhance accuracy and reliability.
– Continuous Improvement: Regularly reviewing testing methods and processes to identify areas for improvement and prevent defects.
By integrating these methods and controls into manufacturing processes, companies can maintain high product quality, meet regulatory requirements, and enhance customer satisfaction.
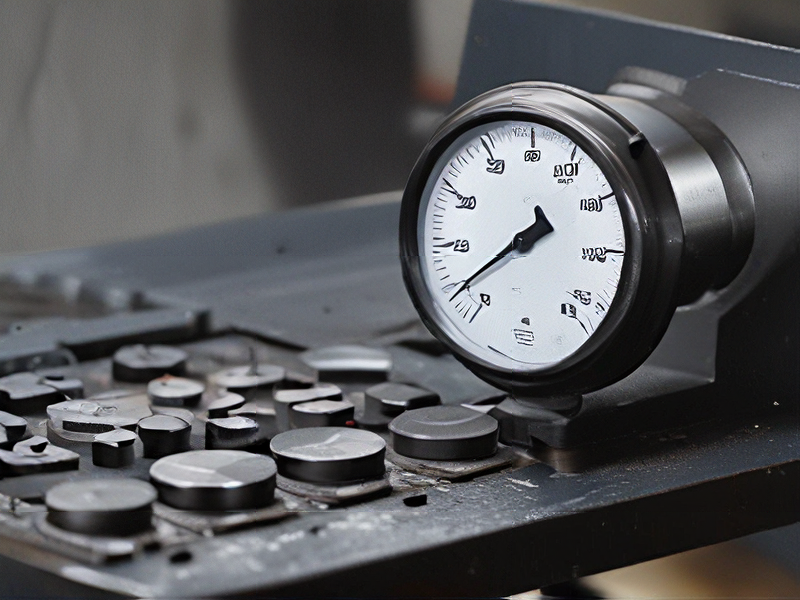
Tips for Procurement and Considerations when Purchasing from metal manufacture
Tips for Procurement and Considerations When Purchasing from Metal Manufacturers
1. Define Requirements Clearly:
– Specify the type, grade, and dimensions of the metal required.
– Clarify the application to ensure the right material is selected for performance and durability.
2. Supplier Evaluation:
– Research and vet potential suppliers for their reputation, quality standards, and reliability.
– Consider suppliers with certifications like ISO 9001 for quality management.
3. Quality Assurance:
– Request material certificates and test reports to verify the metal’s quality.
– Ensure the supplier has robust quality control processes.
4. Cost Considerations:
– Compare prices from multiple suppliers, considering factors like shipping, handling, and import duties.
– Evaluate the total cost of ownership, including maintenance and lifespan of the metal.
5. Lead Time and Delivery:
– Confirm the supplier’s lead times to ensure they align with your project schedule.
– Verify the reliability of the supplier’s logistics and their ability to meet deadlines.
6. Contract Terms:
– Negotiate clear terms regarding payment, delivery schedules, and penalties for delays.
– Include clauses for quality assurance, dispute resolution, and warranty.
7. Sustainability and Compliance:
– Ensure the supplier adheres to environmental regulations and sustainable practices.
– Verify compliance with industry standards and legal requirements.
8. After-Sales Support:
– Assess the supplier’s after-sales service, including technical support and availability of spare parts.
– Establish a communication protocol for addressing any issues that may arise post-purchase.
By following these guidelines, you can optimize your procurement process, ensuring high-quality metal supplies while mitigating risks associated with cost, quality, and delivery.
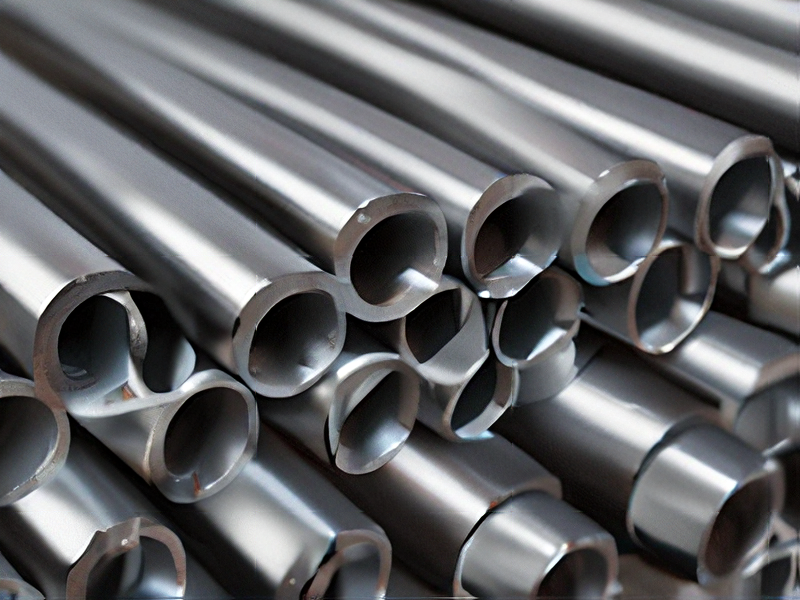
FAQs on Sourcing and Manufacturing from metal manufacture in China
Certainly! Here are some frequently asked questions (FAQs) regarding sourcing and manufacturing from metal manufacturers in China:
1. What types of metals can be sourced from manufacturers in China?
Manufacturers in China can supply a wide range of metals including steel, aluminum, copper, brass, titanium, and alloys tailored to specific needs.
2. How can I find a reliable metal manufacturer in China?
Research online directories, attend trade shows, and seek recommendations. Verify credentials, visit facilities if possible, and request samples to assess quality.
3. What are the typical lead times for manufacturing metal products in China?
Lead times vary based on complexity and volume but generally range from a few weeks to a few months. Factors like customization and order size can influence timelines.
4. What quality standards do Chinese metal manufacturers adhere to?
Many manufacturers comply with international standards such as ISO 9001 for quality management and ISO 14001 for environmental management. Specific industry standards may also apply.
5. How can I manage quality control when manufacturing overseas?
Implement detailed specifications, conduct regular inspections during production, and consider hiring third-party quality assurance services to ensure compliance.
6. What are the typical payment terms when dealing with Chinese manufacturers?
Payment terms often involve a deposit upfront (30-50%) with the balance due upon completion and inspection before shipping. Negotiate terms to align with your financial planning.
7. What are the potential challenges when sourcing from China?
Challenges may include language barriers, cultural differences, fluctuating raw material costs, intellectual property protection, and logistics management.
8. What steps can I take to ensure intellectual property protection?
Use non-disclosure agreements (NDAs), register patents or trademarks where applicable, and carefully vet manufacturers for their reputation and commitment to intellectual property rights.
9. How can I stay updated on the status of my manufacturing order?
Maintain regular communication with your manufacturer, utilize project management tools, and request updates at key production milestones.
10. What are the shipping options for products manufactured in China?
Options include sea freight, air freight, or a combination (sea-air) depending on urgency and cost considerations. Factor in logistics lead times when planning.
These FAQs provide a foundational understanding for sourcing and manufacturing metal products from China, addressing common concerns and considerations in the process.
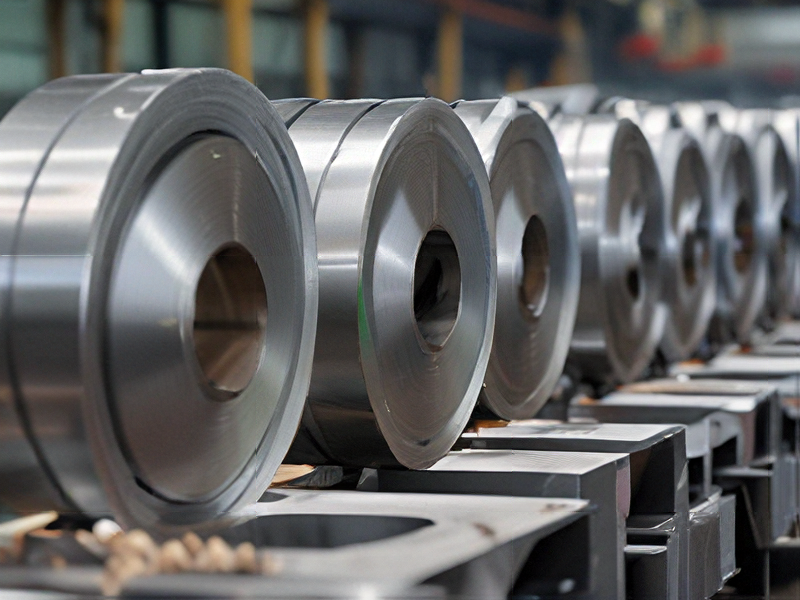