Technology and Applications of metal plating
Metal plating, also known as electroplating, involves depositing a thin layer of metal onto a conductive surface to enhance properties such as corrosion resistance, durability, conductivity, and aesthetics. This process is widely used across various industries:
1. Corrosion Protection: Metal plating provides a barrier against corrosion, extending the lifespan of components exposed to harsh environments. Commonly plated metals for corrosion resistance include zinc, nickel, and chromium.
2. Electronics: Printed circuit boards (PCBs) utilize metal plating to create conductive pathways between components. Copper is primarily used due to its excellent conductivity and adherence properties.
3. Aesthetics: Decorative plating enhances the appearance of objects, from jewelry to automotive parts. Gold, silver, and chrome are popular choices for their luster and durability.
4. Wear Resistance: Plating can improve wear resistance on components subjected to friction and abrasion, such as machine parts. Hard chromium and nickel-phosphorus alloys are frequently employed for this purpose.
5. Engineering Applications: Industries like aerospace and automotive use plating to achieve specific engineering requirements. For instance, cadmium plating provides lubricity in moving parts, while titanium nitride (TiN) enhances cutting tool performance.
6. Medical Devices: Biocompatible materials like titanium are plated onto medical implants to promote osseointegration and reduce the risk of rejection.
7. Environmental Benefits: Advances in plating technologies aim to reduce environmental impact through processes like trivalent chromium plating, which minimizes hazardous waste compared to traditional hexavalent chromium methods.
Overall, metal plating plays a crucial role in modern manufacturing, offering a versatile range of applications that enhance functionality, appearance, and longevity across diverse industries.
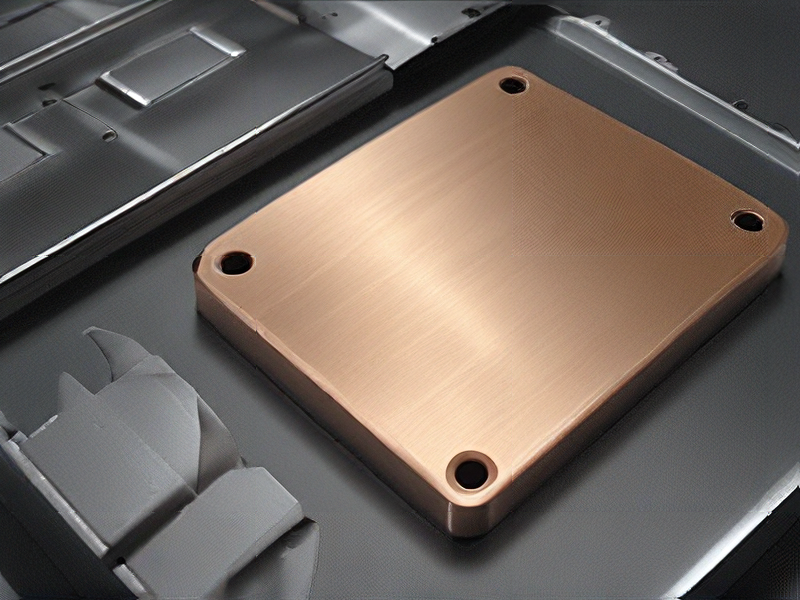
Quality Testing Methods for metal plating and how to control quality
Quality Testing Methods for Metal Plating:
1. Visual Inspection:
– Purpose: Identifies visible defects like cracks, pits, discoloration, or uneven coating.
– Procedure: Inspect plated surfaces under appropriate lighting using magnifying tools if necessary.
2. Thickness Measurement:
– Purpose: Ensures the plating thickness meets specifications.
– Procedure: Use micrometers, X-ray fluorescence (XRF), or eddy current instruments to measure coating thickness.
3. Adhesion Testing:
– Purpose: Checks the bond strength between the coating and the substrate.
– Procedure: Perform bend tests, tape tests, or thermal shock tests to evaluate adhesion quality.
4. Hardness Testing:
– Purpose: Assesses the hardness of the plated layer.
– Procedure: Use microhardness testers like Vickers or Knoop hardness tests to measure surface hardness.
5. Corrosion Resistance Testing:
– Purpose: Determines the coating’s ability to resist corrosion.
– Procedure: Conduct salt spray tests, humidity tests, or cyclic corrosion tests according to industry standards like ASTM B117.
6. Porosity Testing:
– Purpose: Detects pores or pinholes that could lead to corrosion.
– Procedure: Use ferroxyl tests, electrochemical methods, or microscopic examination to identify porosity.
Quality Control Methods:
1. Process Control:
– Maintain strict control over plating bath composition, temperature, and pH.
– Regularly calibrate and maintain equipment to ensure consistent operation.
2. Standard Operating Procedures (SOPs):
– Implement detailed SOPs for each stage of the plating process.
– Ensure all personnel are trained and adhere to these procedures.
3. Inspection and Testing:
– Establish routine inspection schedules and conduct periodic quality tests.
– Utilize statistical process control (SPC) to monitor and analyze data for trends and deviations.
4. Documentation and Traceability:
– Keep detailed records of all processes, inspections, and test results.
– Use traceability systems to track each batch from raw material to finished product.
5. Continuous Improvement:
– Implement feedback loops for ongoing process improvement.
– Regularly review and update procedures based on test results and industry advancements.
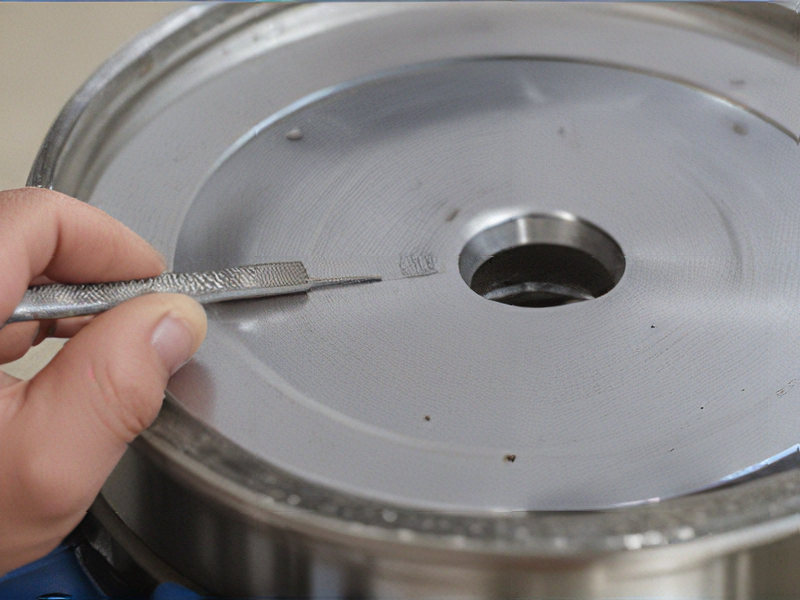
Tips for Procurement and Considerations when Purchasing from metal plating
When engaging in procurement for metal plating services, several key considerations can optimize your purchasing process:
1. Quality Standards: Ensure the plating company adheres to industry standards like ASTM (American Society for Testing and Materials) or ISO (International Organization for Standardization) to guarantee high-quality finishes.
2. Capabilities and Expertise: Evaluate the provider’s experience with your specific metal and plating requirements. Look for a track record of handling similar materials and meeting technical specifications.
3. Environmental Compliance: Verify that the plating process aligns with environmental regulations such as wastewater treatment and hazardous material disposal to mitigate environmental impact.
4. Cost and Value: Seek competitive pricing while balancing it with the quality and consistency of plating results. Consider long-term durability and performance to assess overall value.
5. Lead Times and Flexibility: Assess the plater’s ability to meet your project deadlines and their flexibility to accommodate changes in order size or specifications.
6. Communication and Support: Effective communication channels and responsive customer support are crucial for clarifying expectations, addressing concerns promptly, and ensuring smooth project execution.
7. Quality Assurance: Inquire about their quality control measures throughout the plating process to minimize defects and ensure consistent output.
8. References and Reviews: Review testimonials, case studies, or customer references to gauge satisfaction levels and reliability.
9. Location and Logistics: Consider proximity to your facility to potentially reduce shipping costs and transit times, while ensuring efficient logistics management.
10. Long-term Relationship: Look for a provider who values long-term partnerships and demonstrates a commitment to continuous improvement and customer satisfaction.
By integrating these considerations into your procurement strategy, you can enhance the likelihood of selecting a metal plating provider that meets your technical, operational, and financial requirements effectively.
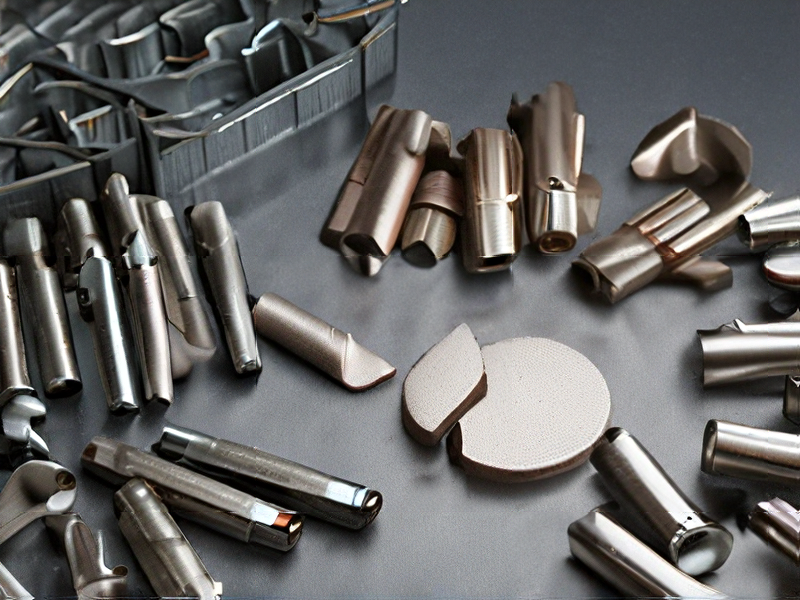
FAQs on Sourcing and Manufacturing from metal plating in China
When sourcing and manufacturing metal plating in China, consider these FAQs:
1. Why choose China for metal plating?
China offers competitive pricing, a wide range of capabilities, and extensive experience in metal plating due to its robust manufacturing infrastructure.
2. How do I find a reliable supplier?
Utilize online platforms like Alibaba or Global Sources for initial research. Conduct thorough due diligence by checking supplier reviews, requesting samples, and visiting facilities if possible.
3. What are common metal plating processes available?
China typically offers electroplating (e.g., nickel, chrome), anodizing (aluminum), and various types of coatings (e.g., zinc, tin).
4. Are there quality standards to consider?
Ensure suppliers adhere to international standards like ISO 9001. Request certifications and inspect previous work to verify quality consistency.
5. How can I manage production and logistics?
Communicate clearly with suppliers about timelines and expectations. Consider hiring a local agent or using a third-party inspection service to monitor production and ensure quality.
6. What are potential challenges?
Language barriers, cultural differences, and intellectual property protection can be challenges. Use contracts that clearly outline expectations and protect intellectual property rights.
7. What about environmental and ethical considerations?
Ensure suppliers comply with environmental regulations. Consider suppliers with certifications like ISO 14001 for environmental management and audit their ethical practices.
By addressing these FAQs, you can navigate sourcing and manufacturing metal plating in China more effectively while minimizing risks and maximizing quality control.
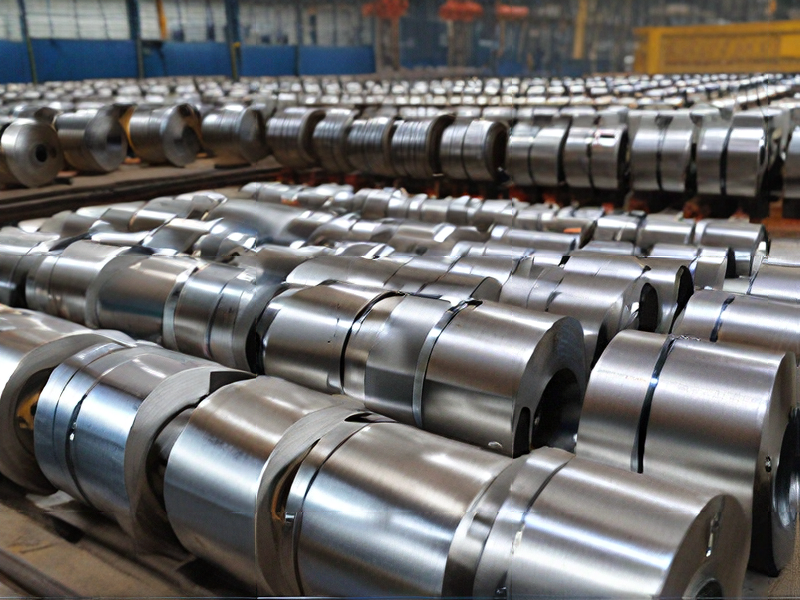