Technology and Applications of mim metal injection molding
Metal Injection Molding (MIM) is a manufacturing process that combines the versatility of plastic injection molding with the strength and properties of sintered metals. It involves four main steps: feedstock preparation, injection molding, debinding, and sintering.
Feedstock Preparation: Metal powder is mixed with a binder material to form a feedstock. This mixture is typically composed of fine metal powders (such as stainless steel, titanium, or tungsten) and a polymer binder.
Injection Molding: The feedstock is injected into a mold cavity under high pressure, much like plastic injection molding. This step shapes the material into the desired form, allowing for complex geometries and precise dimensions.
Debinding: After molding, the binder must be removed from the molded parts. This is usually done through a combination of thermal and chemical processes, leaving behind a “brown” part composed of metal powder.
Sintering: The brown part is then heated in a controlled atmosphere to a temperature below its melting point but high enough to cause the metal particles to bond together. This process eliminates pores and increases the density and strength of the part, resulting in a final sintered metal component.
Applications: MIM is valued for its ability to produce complex shapes with high precision and excellent mechanical properties. It finds applications in various industries, including automotive, aerospace, medical, and consumer electronics. Components such as surgical instruments, firearm parts, electronic connectors, and gears benefit from MIM due to its cost-effectiveness in producing small, intricate parts at scale.
In conclusion, MIM offers significant advantages in manufacturing intricate metal components that are difficult or expensive to produce using traditional methods. Its versatility, coupled with advancements in materials and process control, continues to expand its applications across industries, driving innovation and efficiency in metal part production.
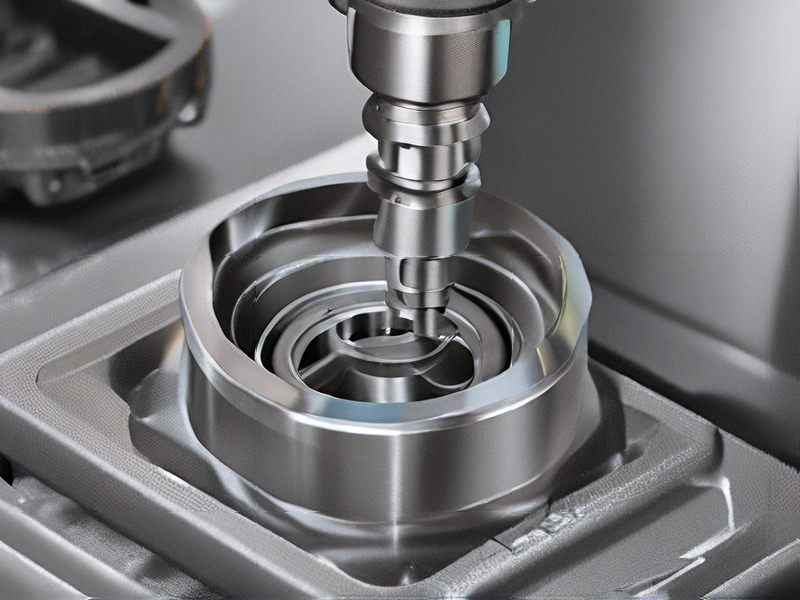
Quality Testing Methods for mim metal injection molding and how to control quality
Quality testing for Metal Injection Molding (MIM) is crucial to ensure that parts meet specifications and performance standards. Key methods and controls include:
1. Material Inspection:
– Powder Analysis: Verify particle size distribution and composition using laser diffraction and scanning electron microscopy (SEM).
– Feedstock Evaluation: Assess homogeneity and rheological properties to ensure consistent flow behavior.
2. Process Control:
– Injection Molding: Monitor temperature, pressure, and injection speed to maintain part consistency. Use automated systems for precise control.
– Debinding: Implement thermal or solvent debinding with controlled rates to prevent defects like swelling or cracking.
– Sintering: Control temperature, atmosphere, and time to achieve desired density and microstructure. Utilize thermogravimetric analysis (TGA) and differential scanning calorimetry (DSC) for process optimization.
3. Dimensional and Visual Inspection:
– Coordinate Measuring Machines (CMM): Measure critical dimensions and geometries to ensure parts meet design tolerances.
– Visual Inspection: Check for surface defects, such as cracks or pores, using optical microscopy or automated vision systems.
4. Mechanical Testing:
– Hardness Testing: Assess surface and bulk hardness using methods like Rockwell or Vickers hardness tests.
– Tensile Testing: Evaluate mechanical strength, elongation, and yield strength of parts to confirm material performance.
5. Microstructural Analysis:
– Metallography: Examine grain size, phase distribution, and porosity using optical microscopy and SEM.
– X-Ray Diffraction (XRD): Identify and quantify phases and detect any undesirable compounds.
6. Non-Destructive Testing (NDT):
– X-Ray/CT Scanning: Inspect internal structures for defects without damaging the part.
– Ultrasonic Testing: Detect internal flaws or voids in larger components.
By implementing these methods and maintaining strict process controls, manufacturers can ensure high-quality MIM parts that meet stringent industry standards.
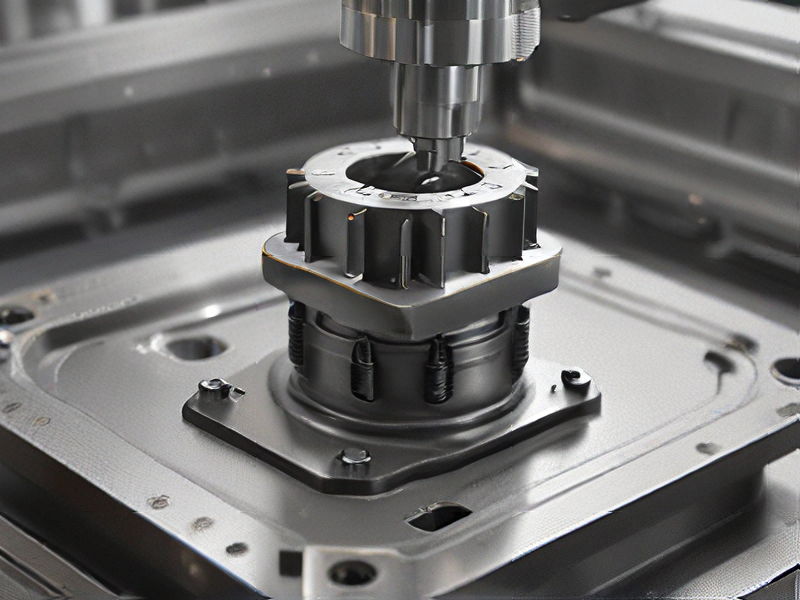
Tips for Procurement and Considerations when Purchasing from mim metal injection molding
When procuring from Metal Injection Molding (MIM) providers, it’s essential to consider several factors to ensure quality, cost-effectiveness, and efficiency. Here are key tips and considerations:
1. Supplier Evaluation:
– Experience and Reputation: Choose suppliers with a proven track record in MIM, as experience often translates to better quality and reliability.
– Certifications: Look for ISO certifications or other industry-specific standards to ensure quality control processes are in place.
2. Material Selection:
– Compatibility: Ensure the MIM process can work with your chosen material, considering factors like mechanical properties, corrosion resistance, and cost.
– Standards: Verify that the supplier adheres to material standards and specifications relevant to your application.
3. Design Considerations:
– Complexity: MIM is ideal for producing intricate shapes with tight tolerances. Ensure your design leverages these capabilities to avoid unnecessary machining.
– Volume: MIM is cost-effective for high-volume production due to lower per-unit costs but may be less so for small batches.
4. Cost Factors:
– Tooling Costs: Initial tooling for MIM can be expensive. Balance this against the long-term savings in high-volume production.
– Unit Cost: Evaluate the overall unit cost, including secondary processes like finishing, to ensure the total expense meets budgetary constraints.
5. Quality Assurance:
– Testing and Inspection: Confirm that the supplier conducts rigorous testing and inspection, including dimensional analysis and mechanical testing.
– Defect Rates: Review the supplier’s historical defect rates and their process for addressing non-conformities.
6. Lead Times and Capacity:
– Production Lead Time: Understand the supplier’s lead times for tooling and production to align with your project timelines.
– Capacity: Ensure the supplier can handle your production volume without compromising on quality or delivery schedules.
7. Communication and Support:
– Technical Support: Choose a supplier that offers robust technical support, from design consultation to troubleshooting.
– Transparency: Effective communication regarding project status, potential delays, and any issues is crucial for a smooth procurement process.
By considering these factors, you can optimize your procurement strategy for MIM components, ensuring high-quality, cost-effective outcomes.
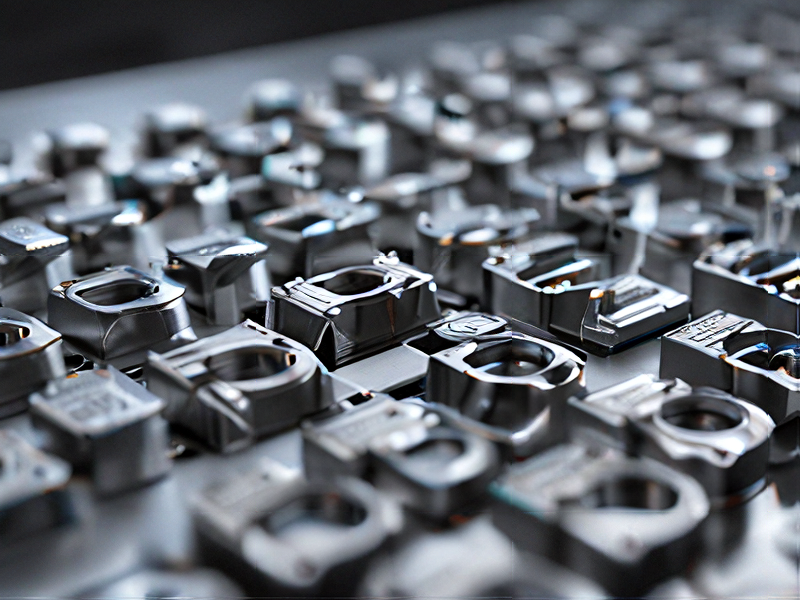
FAQs on Sourcing and Manufacturing from mim metal injection molding in China
Here are some frequently asked questions (FAQs) regarding sourcing and manufacturing from MIM (Metal Injection Molding) in China:
1. What is Metal Injection Molding (MIM)?
Metal Injection Molding (MIM) is a manufacturing process that combines the design flexibility of plastic injection molding with the strength and durability of metallic materials. It involves mixing metal powders with a binder material to create a feedstock, which is then molded into shape and sintered to achieve the final metal part.
2. Why choose MIM for manufacturing?
MIM offers cost-effective production of complex, high-precision metal parts with excellent mechanical properties. It is suitable for small to medium production runs and enables the creation of intricate geometries that are difficult or costly to produce using traditional machining methods.
3. What are the advantages of sourcing MIM parts from China?
China has a well-established MIM industry with numerous manufacturers offering competitive pricing and extensive experience in mass-producing MIM components. Chinese suppliers often provide comprehensive services from design optimization to finishing operations, making them a preferred choice for cost-effective production.
4. How to select a reliable MIM manufacturer in China?
When choosing a MIM manufacturer in China, consider factors such as their experience with MIM technology, their track record with similar projects, quality certifications (e.g., ISO 9001), and their ability to provide comprehensive support including material selection, design assistance, and post-processing capabilities.
5. What quality assurance measures should be in place?
Quality assurance in MIM manufacturing should include rigorous inspection processes at each stage, from raw material testing through to final inspection of sintered parts. Ensure the manufacturer adheres to international quality standards and can provide documentation for traceability and compliance.
6. What are the typical lead times for MIM production in China?
Lead times for MIM production in China can vary depending on part complexity, volume, and post-processing requirements. Generally, expect lead times ranging from a few weeks to a couple of months, including tooling design and fabrication.
7. How does cost compare between MIM in China vs. other manufacturing methods?
MIM in China offers competitive pricing compared to traditional machining methods for complex metal parts. While initial tooling costs can be higher, MIM’s ability to produce intricate designs in bulk can result in significant cost savings over time.
Navigating MIM sourcing and manufacturing in China requires attention to detail, thorough supplier vetting, and clear communication to ensure quality and reliability throughout the production process.
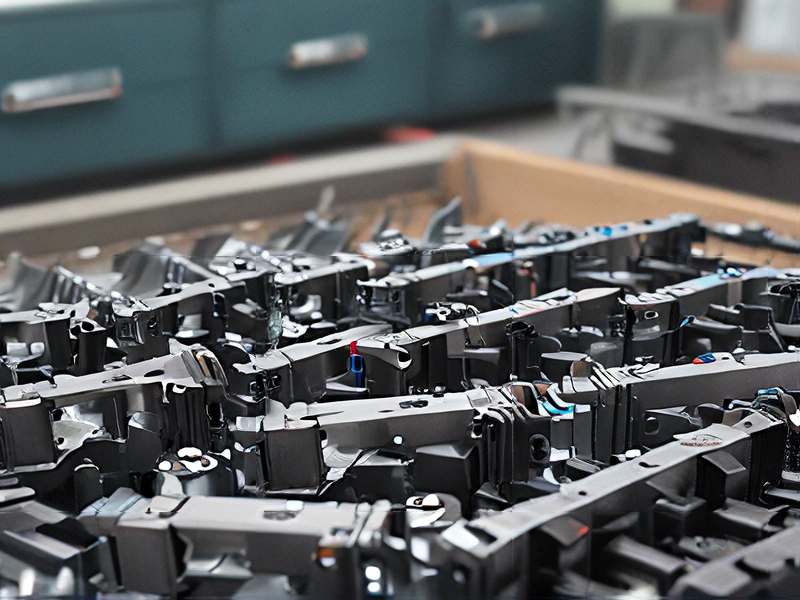