Technology and Applications of mim metal injection moulding
Metal Injection Moulding (MIM) is an advanced manufacturing technology that combines the versatility of plastic injection moulding with the strength and integrity of metal. This process involves four main steps: feedstock preparation, injection moulding, debinding, and sintering.
Feedstock Preparation: Fine metal powders are mixed with a binder to create a feedstock. The binder typically consists of polymers that make the mixture pliable for injection moulding.
Injection Moulding: The feedstock is heated and injected into a mould cavity, forming the desired shape. This step is similar to plastic injection moulding but uses metal powders.
Debinding: The binder is removed from the moulded part, usually through a thermal or solvent process. This step leaves a porous metal structure, referred to as the “brown part.”
Sintering: The brown part is heated in a controlled atmosphere to just below the melting point of the metal. This process densifies the part by bonding the metal particles, resulting in a finished product with properties close to those of wrought metal.
Applications:
1. Automotive: MIM is used to produce complex and precise components such as gears, turbocharger parts, and fuel system components.
2. Medical: This technology manufactures surgical instruments, orthodontic brackets, and components for medical devices due to its ability to produce small, intricate parts with high strength.
3. Consumer Electronics: MIM parts are found in smartphones, laptops, and other devices, including components like connectors, heat sinks, and camera modules.
4. Aerospace: It is used to create lightweight, high-strength components such as fasteners, brackets, and structural parts.
5. Industrial: MIM produces tools, hardware, and components for various machinery, offering benefits of precision and durability.
MIM is favored for its ability to produce high-volume, complex metal parts with excellent mechanical properties, making it a valuable technology in diverse industries.
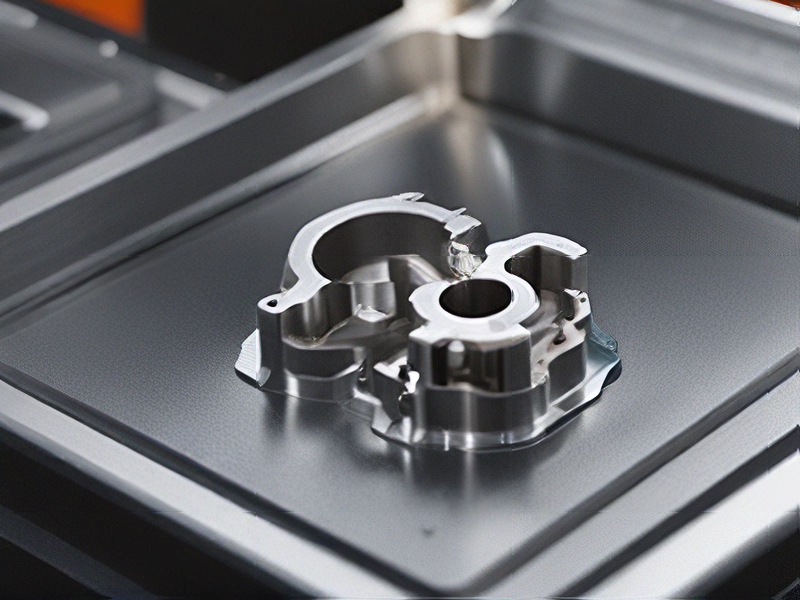
Quality Testing Methods for mim metal injection moulding and how to control quality
Metal injection molding (MIM) involves complex processes that require rigorous quality control methods to ensure high precision and consistency in the final products. Here are key quality testing methods and control measures:
1. Dimensional Inspection: Utilizing precision measuring tools such as coordinate measuring machines (CMMs) ensures parts meet exact dimensional specifications.
2. Visual Inspection: Detailed visual checks for surface defects, discolorations, or irregularities are crucial. Magnification tools aid in detecting minute imperfections.
3. Material Analysis: Verifying material composition through spectroscopy and chemical analysis ensures conformity to required standards, preventing material discrepancies.
4. Mechanical Testing: Conducting tests such as tensile, hardness, and impact tests ensures parts meet mechanical performance requirements. These tests validate material strength and durability.
5. Process Control: Implementing robust process controls throughout manufacturing minimizes variability. Parameters like temperature, pressure, and injection speed are tightly monitored and adjusted as needed.
6. Defect Analysis: Employing techniques like non-destructive testing (NDT) such as X-ray or ultrasound detects internal defects without damaging the part, ensuring integrity.
7. Statistical Process Control (SPC): Continuously monitoring production processes through SPC charts helps identify trends and deviations early, allowing timely corrective actions.
8. Quality Management Systems (QMS): Adhering to ISO 9001 or similar standards ensures systematic quality management from design to delivery, integrating feedback loops for continuous improvement.
By implementing these methods and controls, MIM manufacturers can achieve consistent quality, minimize defects, and meet stringent customer requirements effectively.
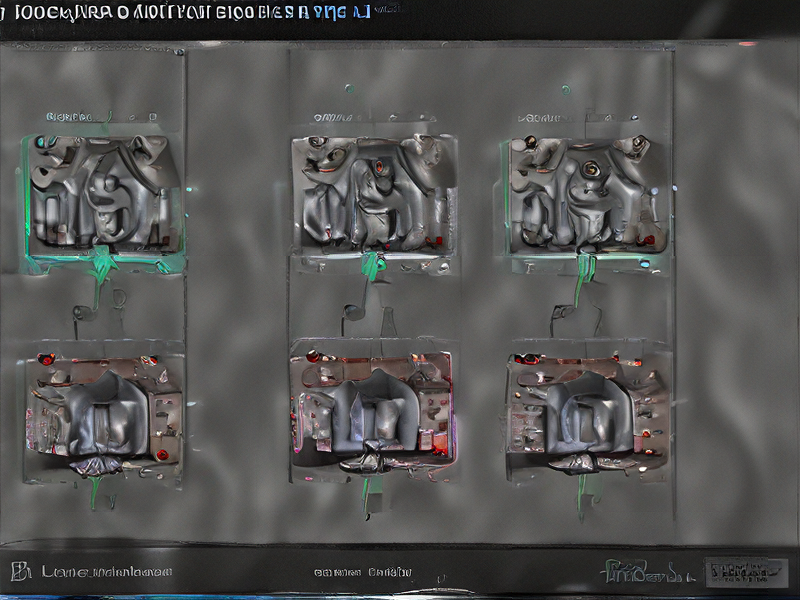
Tips for Procurement and Considerations when Purchasing from mim metal injection moulding
When considering procurement from Metal Injection Molding (MIM) suppliers, several key tips and considerations can ensure a successful purchasing process:
1. Supplier Selection: Choose MIM suppliers with proven expertise and a track record in your industry. Look for certifications (ISO 9001, ISO 13485 for medical devices, etc.) that demonstrate quality management systems.
2. Quality Assurance: Ensure the supplier has robust quality control processes throughout the MIM process, from raw material inspection to final product validation. Request samples and visit facilities if possible to assess their capabilities.
3. Material Selection: MIM can use a variety of materials (stainless steels, alloys, ceramics). Specify material requirements based on your product’s performance needs (strength, corrosion resistance, etc.) and ensure the supplier can meet these specifications.
4. Design for MIM: Optimize designs for MIM to leverage its benefits (complex geometries, reduced assembly). Work closely with the supplier during design phases to achieve cost-effective production and minimize post-processing.
5. Cost Considerations: Understand cost drivers in MIM such as material selection, part complexity, and batch size. Evaluate quotes comprehensively, considering not just unit cost but also tooling and setup fees.
6. Lead Times and Production Capacity: Clarify lead times and ensure the supplier can meet your production schedule. Evaluate their production capacity to handle your volume requirements without delays.
7. Communication and Collaboration: Establish clear communication channels and expectations regarding project updates, modifications, and quality feedback. A collaborative approach ensures alignment throughout the procurement process.
8. Post-Processing and Finishing: Discuss post-processing options (heat treatment, surface finishing) to meet aesthetic and functional requirements. Ensure these processes align with your product specifications.
9. Logistics and Delivery: Confirm logistics capabilities for shipping and delivery. Consider factors like packaging requirements and shipping regulations, especially for international procurement.
10. Contractual Agreements: Define terms and conditions in contracts regarding quality standards, delivery schedules, payment terms, and intellectual property rights to protect both parties.
By following these tips and considerations, you can navigate the procurement process effectively and establish a successful partnership with your MIM supplier.
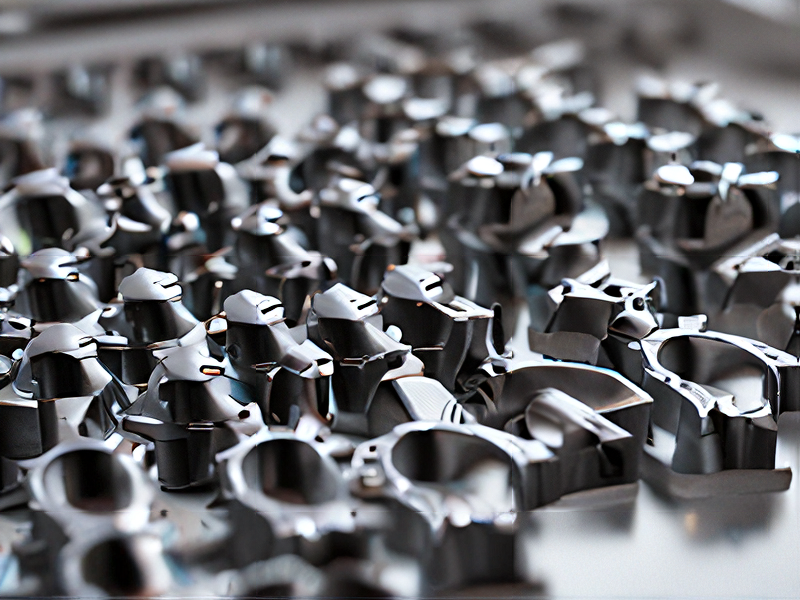
FAQs on Sourcing and Manufacturing from mim metal injection moulding in China
FAQs on Sourcing and Manufacturing from MIM Metal Injection Moulding in China
#### What is MIM Metal Injection Moulding?
MIM (Metal Injection Moulding) is a manufacturing process that combines metal powders and plastic binders to create intricate metal parts. It is ideal for producing small, complex components in high volumes.
#### Why source MIM from China?
China offers competitive pricing, advanced manufacturing capabilities, and extensive experience in MIM technology. Many Chinese manufacturers adhere to international standards, ensuring quality and reliability.
#### How to select a reliable MIM manufacturer in China?
1. Research and Vetting: Look for manufacturers with certifications like ISO 9001 and ISO/TS 16949.
2. Experience and Expertise: Choose companies with a proven track record in MIM.
3. Facility Visits: If possible, visit the facility to assess their capabilities and quality control processes.
4. References and Reviews: Seek feedback from other clients.
#### What are the cost considerations?
Costs are influenced by:
– Material: Type of metal powder used.
– Design Complexity: More intricate designs can increase costs.
– Volume: Higher production volumes typically reduce unit costs.
– Post-Processing: Additional treatments like heat treatment or surface finishing can add to costs.
#### What is the typical lead time?
Lead times vary but generally range from 6 to 12 weeks. This includes the design phase, prototyping, tool manufacturing, and production.
#### What quality control measures are in place?
Reputable Chinese MIM manufacturers implement strict quality control measures, including:
– Material Testing: Ensuring raw materials meet specifications.
– In-Process Inspection: Regular checks during production.
– Final Inspection: Comprehensive testing of finished products.
#### What are the common applications of MIM parts?
MIM parts are used in various industries, including automotive, medical devices, electronics, consumer products, and aerospace, due to their precision and durability.
#### How to handle logistics and shipping?
– Freight Forwarders: Use experienced freight forwarders familiar with Chinese exports.
– Customs Clearance: Ensure all necessary documentation is prepared to avoid delays.
– Incoterms: Clarify the terms of shipment (e.g., FOB, CIF) to understand responsibilities and costs.
#### What are the potential challenges and how to mitigate them?
– Communication Barriers: Use clear, detailed specifications and consider hiring local representatives.
– Quality Issues: Regular audits and third-party inspections can help maintain quality standards.
Sourcing MIM parts from China can be cost-effective and efficient if approached with careful planning and due diligence.
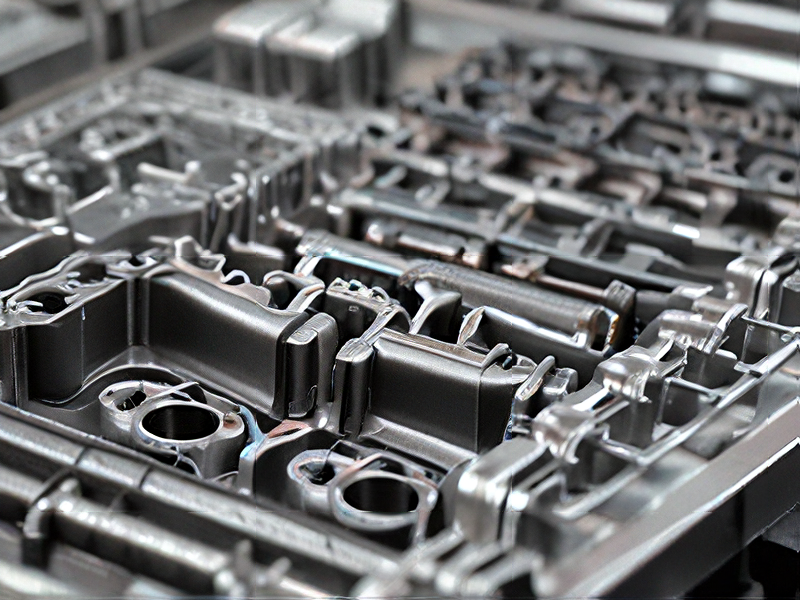