Technology and Applications of non ferrous metal
Non-ferrous metals, such as aluminum, copper, lead, zinc, and nickel, play pivotal roles across various industries due to their unique properties and applications. Aluminum, renowned for its lightweight and corrosion resistance, dominates aerospace, automotive, and packaging sectors. It’s used in aircraft frames, car bodies, and beverage cans.
Copper, valued for its conductivity and malleability, finds extensive use in electrical wiring, plumbing, and electronics. Its antimicrobial properties also make it suitable for healthcare settings. Lead, despite declining use due to environmental concerns, remains crucial in batteries, radiation shielding, and construction.
Zinc’s anti-corrosive properties make it indispensable for galvanizing steel, extending infrastructure longevity. Nickel’s resistance to corrosion and ability to withstand extreme temperatures contribute to its use in stainless steel production, aerospace components, and batteries.
Applications of these metals extend beyond traditional industries. For instance, titanium, known for its strength-to-weight ratio and resistance to corrosion, is used in aerospace, military, and medical implants. Rare earth metals like neodymium and dysprosium are vital in magnets for wind turbines, electric vehicles, and electronics.
Moreover, advancements in metallurgical processes and recycling technologies enhance sustainability and reduce environmental impact. Non-ferrous metals continue to evolve, driven by innovation and demand for sustainable solutions across global markets.
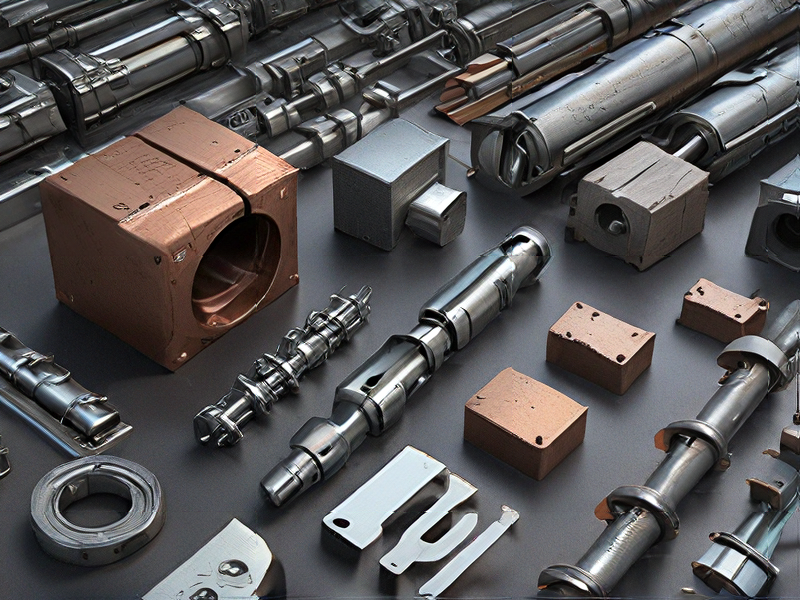
Quality Testing Methods for non ferrous metal and how to control quality
Quality testing for non-ferrous metals involves several methods to ensure their properties meet required standards. Key testing methods include:
1. Chemical Analysis:
– Spectroscopy: Techniques like X-ray fluorescence (XRF) and optical emission spectroscopy (OES) identify and quantify elements within the metal.
– Wet Chemical Analysis: Traditional methods using chemical reactions to determine composition.
2. Mechanical Testing:
– Tensile Testing: Measures strength and ductility by pulling the metal until it breaks.
– Hardness Testing: Uses methods like Brinell, Rockwell, or Vickers to determine resistance to indentation.
– Impact Testing: Charpy or Izod tests assess the metal’s toughness.
3. Non-Destructive Testing (NDT):
– Ultrasonic Testing: Uses high-frequency sound waves to detect internal flaws.
– Radiographic Testing: X-rays or gamma rays reveal internal defects.
– Magnetic Particle Inspection (MPI): Applicable to ferromagnetic metals to find surface and near-surface discontinuities.
4. Metallographic Examination:
– Microscopy: Optical and electron microscopes examine the microstructure to assess grain size, phase distribution, and possible inclusions.
5. Corrosion Testing:
– Salt Spray Test: Simulates long-term exposure to a corrosive environment.
– Electrochemical Testing: Measures the metal’s resistance to corrosion.
Quality Control
1. Raw Material Inspection: Verify the composition and properties of incoming materials.
2. Process Control: Implement strict process parameters and monitoring during manufacturing.
3. In-Process Testing: Regular sampling and testing during production to catch defects early.
4. Final Inspection: Comprehensive testing of finished products to ensure they meet specifications.
5. Documentation and Traceability: Maintain detailed records of material batches, test results, and production processes to trace any quality issues back to their source.
By combining these methods and controls, manufacturers can ensure the consistent quality and reliability of non-ferrous metals.
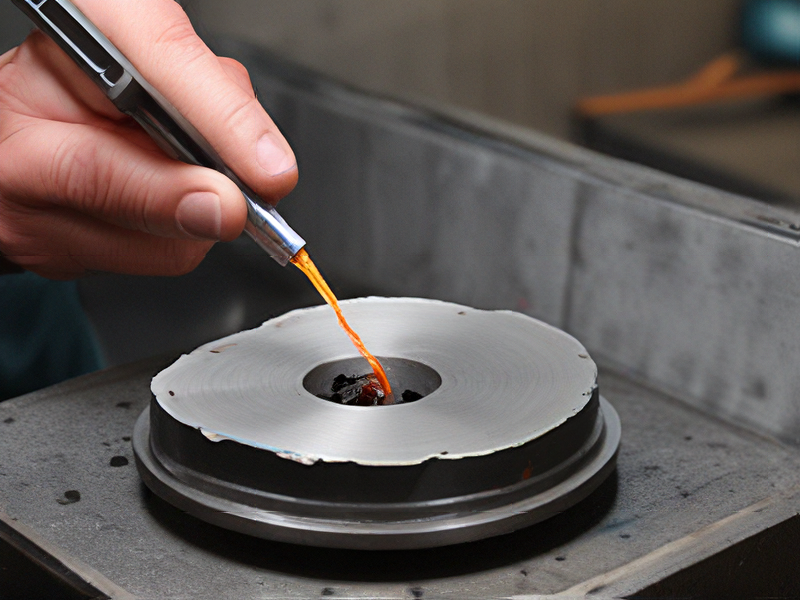
Tips for Procurement and Considerations when Purchasing from non ferrous metal
When procuring non-ferrous metals, several key considerations can ensure effective purchasing:
1. Material Specifications: Define exact material requirements (e.g., aluminum, copper, titanium) including grade, form (sheet, bar, ingot), size, and quantity needed.
2. Quality Assurance: Verify supplier certifications (ISO, ASTM) and material testing reports to ensure quality and compliance with industry standards.
3. Supplier Reliability: Evaluate supplier reputation, reliability, and track record for delivering on time and meeting specifications. Consider their financial stability and ability to handle fluctuations in demand.
4. Price and Cost: Compare quotes from multiple suppliers to get competitive pricing. Factor in shipping costs, tariffs, and potential price volatility in metals markets.
5. Supply Chain Resilience: Assess supplier’s location, proximity to your operations, and contingency plans for disruptions (e.g., natural disasters, geopolitical events).
6. Environmental Impact: Ensure suppliers adhere to environmental regulations and sustainable practices, minimizing environmental impact throughout the supply chain.
7. Payment Terms and Contracts: Negotiate favorable payment terms and establish clear contracts outlining responsibilities, delivery schedules, and dispute resolution mechanisms.
8. Risk Management: Develop strategies to mitigate risks such as price fluctuations, supply shortages, and geopolitical uncertainties that could affect non-ferrous metal supply.
By carefully considering these factors, procurement teams can effectively manage non-ferrous metal purchases, ensuring quality, reliability, and cost-effectiveness in their supply chain operations.
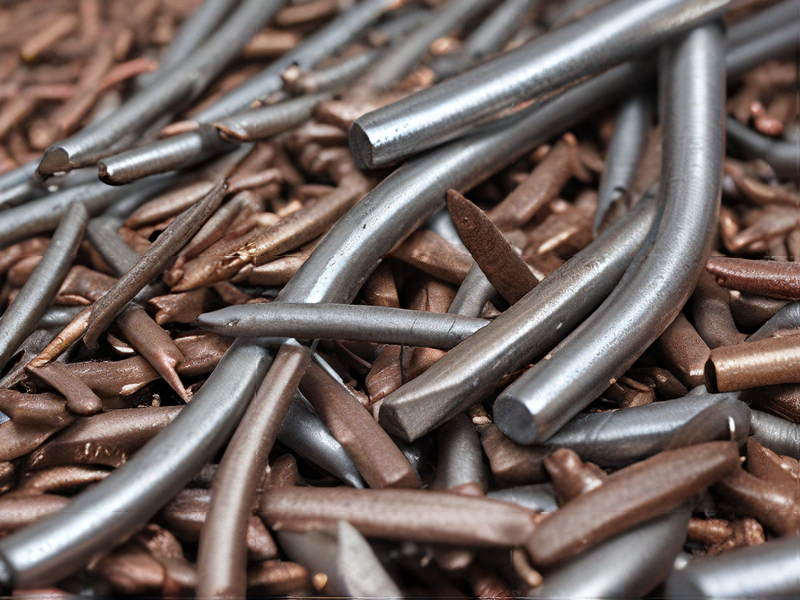
FAQs on Sourcing and Manufacturing from non ferrous metal in China
Certainly! When sourcing and manufacturing non-ferrous metals in China, several FAQs commonly arise:
1. What are common non-ferrous metals sourced from China?
China is a major producer of non-ferrous metals such as aluminum, copper, zinc, lead, and nickel. These metals are widely used in various industries including construction, electronics, and automotive.
2. How can I find reliable suppliers in China?
Utilize online platforms like Alibaba, Made-in-China, and Global Sources to find suppliers. It’s crucial to conduct thorough background checks, request samples, and verify certifications to ensure reliability.
3. What are the challenges of sourcing from China?
Challenges include quality control issues, communication barriers, intellectual property concerns, and regulatory compliance. Working with reputable agents or conducting onsite inspections can mitigate these risks.
4. What should I consider when manufacturing in China?
Factors such as production capabilities, labor costs, environmental standards, and logistics should be carefully evaluated. Engaging with manufacturers who adhere to international quality standards is essential.
5. How can I ensure product quality?
Implement rigorous quality assurance processes, including product inspections during manufacturing and before shipment. Clearly define quality requirements and standards in contracts with suppliers.
6. What are the shipping and logistics considerations?
Plan for transportation costs, lead times, customs procedures, and import/export regulations. Choosing reliable logistics partners and understanding INCO terms are crucial for smooth operations.
7. How do I manage cultural and language differences?
Establish clear communication channels, consider hiring local agents or translators, and invest time in building relationships with Chinese counterparts. Understanding cultural nuances can facilitate smoother interactions.
Navigating sourcing and manufacturing non-ferrous metals in China requires careful planning, thorough research, and proactive management to ensure successful outcomes and mitigate potential challenges.
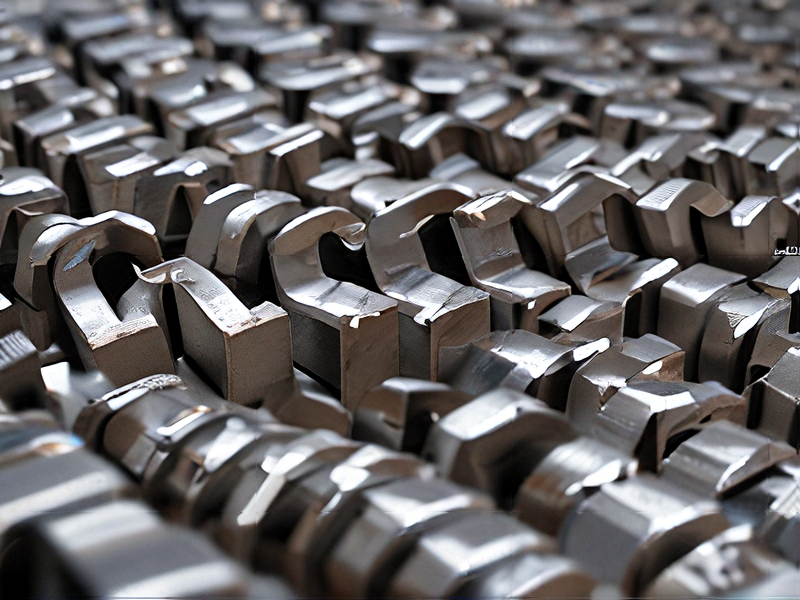