Technology and Applications of powder metallurgy
Powder metallurgy (PM) is a manufacturing process where various metal powders are compacted and then sintered to form a solid part. This method is renowned for producing high-precision components with minimal waste, offering significant advantages over traditional metalworking techniques.
Technology:
1. Powder Production: Metal powders are produced using atomization, reduction, electrolysis, or mechanical methods. Each method ensures the production of powders with specific properties suited to different applications.
2. Compaction: The metal powder is compressed into a desired shape using a die, typically through uniaxial pressing or isostatic pressing. This creates a “green” compact that has enough strength to be handled.
3. Sintering: The compact is heated in a controlled atmosphere below the melting point of the primary metal, causing the particles to bond at a molecular level. This enhances the strength and integrity of the final part.
4. Secondary Operations: These may include sizing, coining, machining, heat treatment, or surface treatments to achieve the final specifications and properties.
Applications:
1. Automotive: PM is extensively used in manufacturing engine components, transmission parts, and gears due to its ability to produce complex shapes with high precision and good wear resistance.
2. Aerospace: High-performance materials like titanium and superalloys are used in PM for critical components in aircraft engines and structural parts, providing a balance of strength and lightweight properties.
3. Medical: PM produces biocompatible implants and surgical instruments, benefiting from the precision and material properties achievable through this process.
4. Electronics: It is used to produce magnetic and conductive components, which are essential in various electronic devices.
5. Industrial Machinery: Gears, bearings, and filters made through PM offer high performance and durability, essential for industrial applications.
Advantages:
– Material Efficiency: Minimal waste in the process.
– Cost-Effective: Economical for large-scale production.
– Precision: High accuracy and consistency in parts.
– Customization: Ability to tailor material properties and shapes.
Powder metallurgy stands out for its efficiency, precision, and ability to create complex parts, making it indispensable in modern manufacturing across various industries.
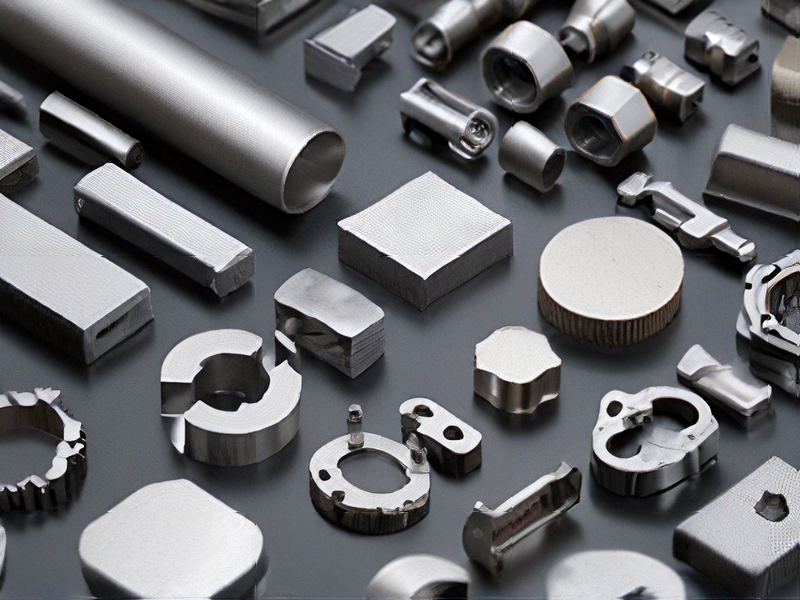
Quality Testing Methods for powder metallurgy and how to control quality
Quality testing in powder metallurgy (PM) ensures the mechanical properties and reliability of the final products. Key methods include:
1. Powder Characterization:
– Particle Size Analysis: Ensures uniformity using sieving, laser diffraction, or microscopy.
– Morphology Assessment: Scanning electron microscopy (SEM) examines particle shape.
– Flowability and Apparent Density: Measured using Hall or Carney flow meters and apparent density apparatus to ensure consistent powder behavior during compaction.
2. Chemical Analysis:
– Spectroscopy (XRF, ICP): Determines elemental composition to ensure alloy consistency.
– Carbon and Oxygen Analysis: Ensures low levels of impurities that can affect sintering.
3. Mechanical Testing:
– Hardness Testing: Evaluates the resistance of sintered parts to deformation using methods like Rockwell or Vickers hardness tests.
– Tensile and Compressive Strength: Measures the material’s ability to withstand loads, ensuring structural integrity.
– Fatigue Testing: Assesses the durability of parts under cyclic loading.
4. Microstructural Analysis:
– Metallography: Optical or electron microscopy evaluates grain structure, porosity, and phase distribution after etching.
– X-ray Diffraction (XRD): Identifies crystalline phases and detects residual stresses.
5. Density Measurement:
– Archimedes’ Principle: Determines the density and porosity of sintered components, critical for mechanical properties.
6. Non-destructive Testing (NDT):
– Ultrasonic Testing: Detects internal flaws.
– X-ray or CT Scanning: Visualizes internal structures and defects.
Quality Control:
1. Process Control:
– Consistent Powder Supply: Maintain uniform powder properties.
– Compaction Monitoring: Ensure consistent pressure and uniformity.
– Sintering Control: Accurate temperature and atmosphere control to achieve desired properties.
2. Statistical Process Control (SPC):
– Data Analysis: Monitor production data to identify trends and deviations.
– Corrective Actions: Implement improvements based on SPC findings.
3. Inspection and Testing:
– Routine Sampling: Regular testing of samples from batches to ensure ongoing quality.
– Final Product Inspection: Comprehensive testing before shipping.
Through these methods, powder metallurgy ensures high-quality, reliable components.
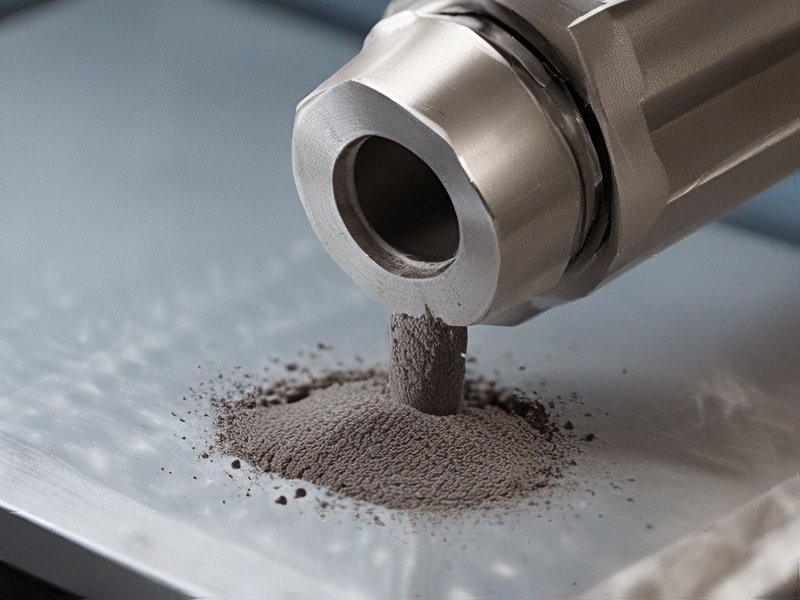
Tips for Procurement and Considerations when Purchasing from powder metallurgy
Tips for Procurement in Powder Metallurgy
1. Supplier Evaluation: Select suppliers with a strong track record in powder metallurgy. Assess their certifications, quality control processes, and past performance.
2. Material Specifications: Clearly define the material specifications required for your application. Ensure the supplier can provide consistent and high-quality powder materials.
3. Cost Analysis: Compare costs from different suppliers, considering not just the price per unit but also the total cost of ownership, including delivery, quality assurance, and potential wastage.
4. Sample Testing: Request samples before making large purchases. Conduct thorough testing to ensure the powder meets your quality and performance standards.
5. Lead Time and Delivery: Confirm lead times and ensure the supplier can meet your production schedule. Consider suppliers who offer reliable and timely delivery.
6. Technical Support: Opt for suppliers who provide robust technical support and are willing to collaborate on developing customized solutions.
Considerations when Purchasing
1. Powder Characteristics: Evaluate particle size distribution, shape, and chemical composition. These factors significantly influence the properties and performance of the final product.
2. Production Volume: Consider your production volume when selecting a supplier. Some suppliers may specialize in small batch production, while others may be more suited for large-scale operations.
3. Quality Control: Ensure the supplier has stringent quality control measures in place. Look for ISO certification or other industry-standard quality assurances.
4. Environmental and Safety Regulations: Ensure the supplier complies with environmental and safety regulations. Consider the environmental impact of the powder production process and the recyclability of the materials.
5. Logistics and Storage: Plan for proper storage and handling of the powders. Ensure your facilities are equipped to maintain the quality and safety of the powder materials.
6. Cost Implications: Beyond the initial purchase cost, consider costs related to shipping, storage, and handling. Factor in potential costs for quality control and testing.
By following these tips and considerations, you can ensure a more efficient and effective procurement process in powder metallurgy, ultimately leading to better quality and cost savings.
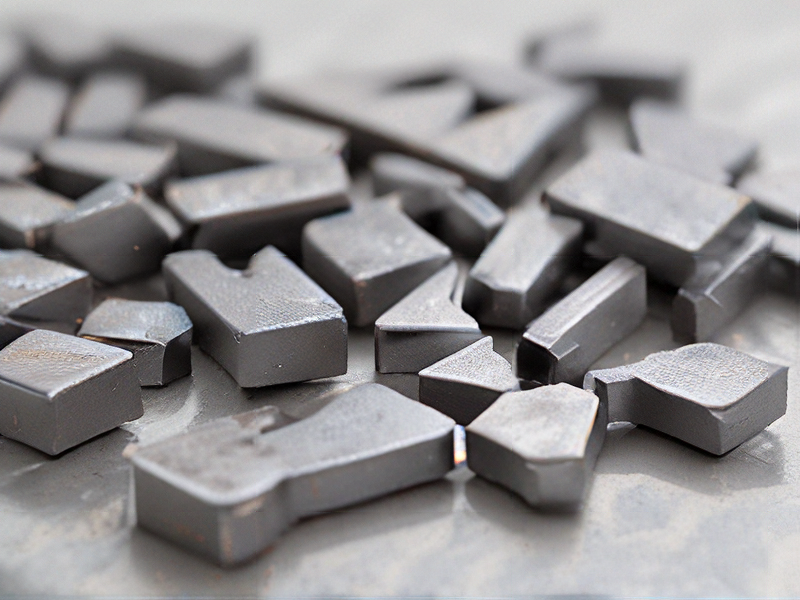
FAQs on Sourcing and Manufacturing from powder metallurgy in China
FAQs on Sourcing and Manufacturing from Powder Metallurgy in China
1. What is Powder Metallurgy (PM)?
Powder Metallurgy (PM) is a manufacturing process where metal powders are compacted into desired shapes and then heated (sintered) to form solid parts. This method is efficient for producing complex shapes with high precision and minimal waste.
2. Why source PM products from China?
China is a leading global supplier of PM products due to its advanced manufacturing capabilities, cost-effective production, and a well-established supply chain. The country offers a wide range of PM materials and products at competitive prices.
3. What materials are commonly used in PM in China?
Common materials include iron, steel, stainless steel, copper, aluminum, and various alloys. Specialized materials like tungsten carbide and titanium alloys are also available for high-performance applications.
4. What are the advantages of PM over traditional manufacturing?
PM offers several benefits:
– High material utilization, reducing waste
– Ability to produce complex shapes and fine features
– Consistent and precise tolerances
– Cost-effective for large production runs
5. How do I find reliable PM manufacturers in China?
To find reliable manufacturers:
– Attend trade shows and industry events
– Use online B2B platforms like Alibaba and Global Sources
– Seek recommendations from industry contacts
– Conduct thorough due diligence, including factory audits
6. What quality standards should I look for?
Look for manufacturers certified under ISO 9001 for quality management. Other relevant standards include ISO 14001 (environmental management) and IATF 16949 (automotive quality).
7. What are the typical lead times for PM products?
Lead times vary depending on the complexity and volume of the order but typically range from 4 to 8 weeks. Custom orders or large volumes might require longer lead times.
8. What challenges might I face when sourcing from China?
Challenges include:
– Communication barriers and time zone differences
– Ensuring consistent quality
– Intellectual property protection
– Logistics and shipping complexities
9. How can I ensure quality control?
Implementing regular quality inspections, third-party audits, and maintaining clear communication with the supplier can help ensure consistent quality.
10. What are the shipping options and costs?
Shipping options include air, sea, and rail, with costs varying based on the shipment size, weight, and urgency. It’s essential to work with experienced freight forwarders to manage logistics efficiently.
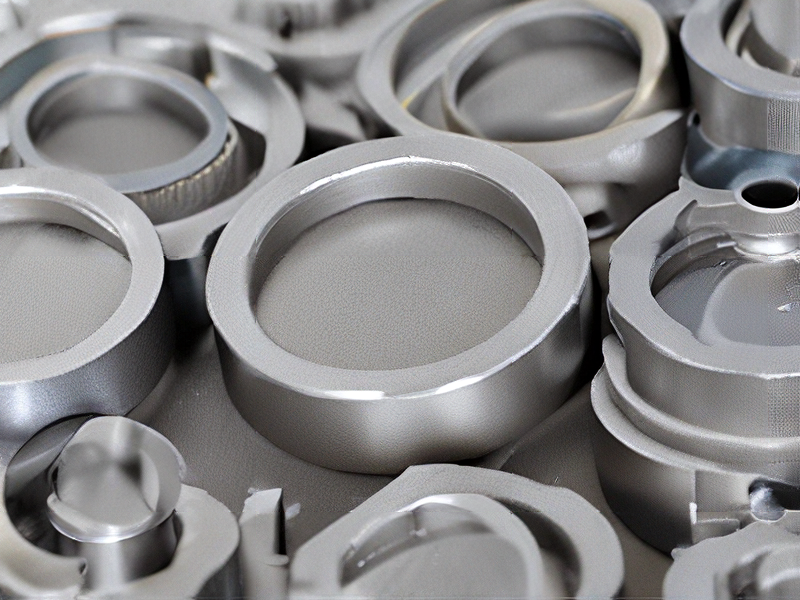