Technology and Applications of precision sheet metal
Precision sheet metal fabrication involves forming thin metal sheets into intricate shapes and components with tight tolerances. Driven by advancements in laser cutting, CNC machining, and bending technologies, this field boasts diverse applications across numerous industries.
In automotive, precision sheet metal is crucial for creating lightweight yet durable body panels, chassis components, and intricate engine parts.
Aerospace relies on it for crafting lightweight fuselage panels, intricate wing structures, and precision instrument housings.
Electronics utilizes precision sheet metal for manufacturing delicate circuit boards, casings for electronic devices, and heat sinks.
Medical applications benefit from its use in creating surgical instruments, implant components, and diagnostic equipment.
Consumer goods leverage precision sheet metal for producing stylish appliances, durable furniture, and intricate electronics enclosures.
Its versatility, precision, and cost-effectiveness make precision sheet metal an indispensable technology in modern manufacturing.
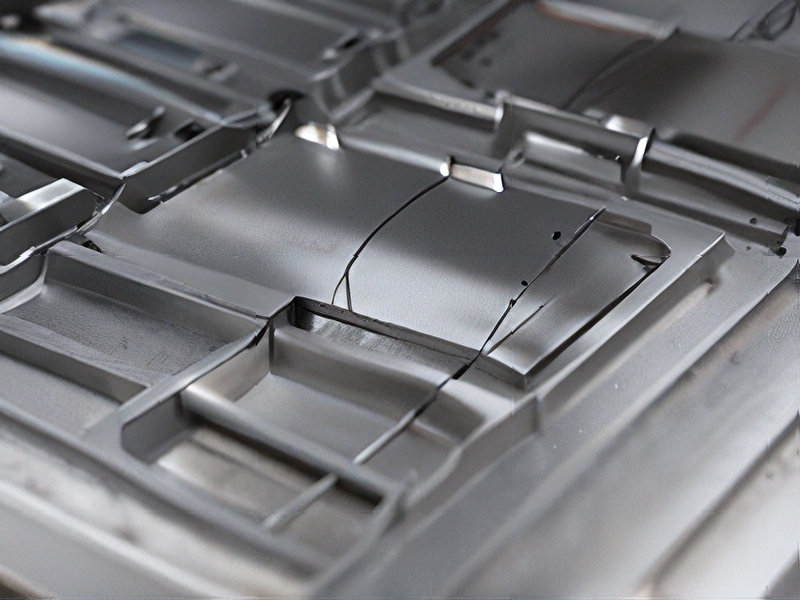
Quality Testing Methods for precision sheet metal and how to control quality
Quality testing for precision sheet metal involves various methods to ensure that the components meet the required specifications and standards. Here are some key methods and practices for controlling quality:
1. Visual Inspection
– Purpose: To identify surface defects such as scratches, dents, and color inconsistencies.
– Tools: Magnifying glasses, microscopes, or simple visual checks.
2. Dimensional Inspection
– Purpose: To verify that the sheet metal parts meet the precise dimensional specifications.
– Tools: Calipers, micrometers, height gauges, and coordinate measuring machines (CMM).
3. Material Testing
– Purpose: To ensure the sheet metal material properties meet the required standards.
– Methods: Tensile testing for strength, hardness testing, and chemical analysis.
4. Non-Destructive Testing (NDT)
– Purpose: To detect internal defects without damaging the part.
– Methods: Ultrasonic testing, radiographic testing, and dye penetrant testing.
5. Surface Finish Testing
– Purpose: To check the roughness and smoothness of the surface.
– Tools: Surface roughness testers and profilometers.
6. Functional Testing
– Purpose: To ensure the parts perform their intended functions in real-world conditions.
– Methods: Load testing, fit and alignment checks, and operational simulations.
Quality Control Practices
1. Standard Operating Procedures (SOPs):
– Detailed documentation of each step in the manufacturing and inspection process to maintain consistency.
2. Statistical Process Control (SPC):
– Use of statistical methods to monitor and control the production process, identifying and correcting deviations before they lead to defects.
3. Quality Management Systems (QMS):
– Implementation of ISO 9001 or similar frameworks to ensure a systematic approach to quality.
4. Training and Certification:
– Regular training programs for staff to stay updated on best practices and certification of skills.
5. Traceability:
– Maintaining records of material batches, production processes, and inspection results for accountability and troubleshooting.
By combining these testing methods and control practices, precision sheet metal manufacturers can ensure high quality and reliability in their products.
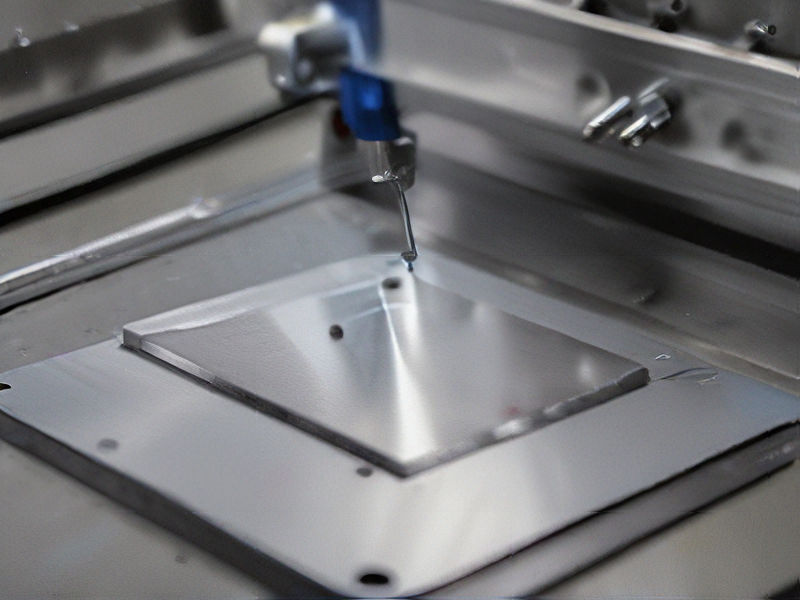
Tips for Procurement and Considerations when Purchasing from precision sheet metal
When procuring precision sheet metal, careful consideration and strategic planning are vital to ensure high-quality and cost-effective purchases. Here are some tips and considerations:
Tips for Procurement
1. Define Requirements Clearly: Specify material types, dimensions, tolerances, finishes, and any additional requirements to avoid misunderstandings.
2. Supplier Evaluation: Assess potential suppliers based on their experience, certifications (like ISO 9001), and capability to meet your specifications and volume needs.
3. Quality Assurance: Ensure the supplier has robust quality control processes. Request samples and conduct inspections before full-scale production.
4. Cost Analysis: Evaluate the total cost, including raw materials, labor, shipping, and potential tariffs. Compare multiple quotes to ensure competitive pricing.
5. Lead Time and Flexibility: Confirm the supplier’s lead time aligns with your project schedule. Opt for suppliers who can offer flexibility for urgent orders or changes.
6. Technology and Capabilities: Verify that the supplier has up-to-date equipment and technology to produce precise and consistent sheet metal parts.
7. Communication: Maintain clear and continuous communication with the supplier to promptly address any issues or changes in requirements.
Considerations When Purchasing
1. Material Selection: Choose the appropriate material (e.g., stainless steel, aluminum) based on the application, considering factors like strength, weight, and corrosion resistance.
2. Design for Manufacturability: Simplify designs to reduce complexity and cost. Consider the manufacturability of the parts to minimize production challenges.
3. Tolerance and Precision: Ensure the tolerances are realistic and necessary. Overly tight tolerances can increase costs and production time.
4. Surface Finish: Specify the required surface finish (e.g., powder coating, anodizing) based on the functional and aesthetic needs of the part.
5. Order Quantities: Determine optimal order quantities to balance between cost savings from bulk orders and the flexibility of smaller batches.
6. Sustainability: Consider the environmental impact of materials and processes. Opt for suppliers who practice sustainable manufacturing.
By following these tips and considerations, you can enhance the procurement process and secure high-quality precision sheet metal components that meet your project’s requirements.
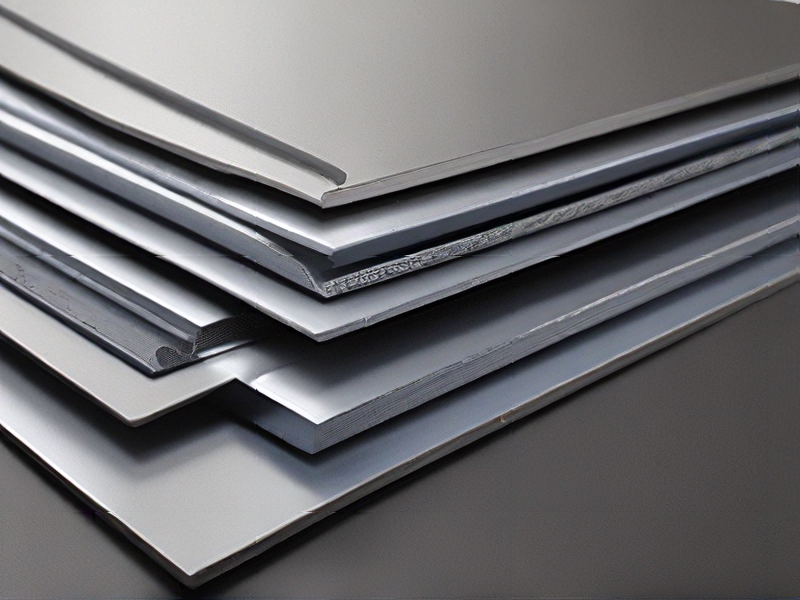
FAQs on Sourcing and Manufacturing from precision sheet metal in China
Certainly! Here are some frequently asked questions (FAQs) regarding sourcing and manufacturing precision sheet metal in China:
1. Why should I consider sourcing precision sheet metal from China?
China offers competitive pricing due to lower labor costs and a well-established manufacturing infrastructure for precision sheet metal. Many factories in China are equipped with advanced machinery and can handle large production volumes.
2. How do I find reliable suppliers in China?
Use reputable sourcing platforms or attend industry trade shows to connect with suppliers. Conduct thorough background checks, request samples, and visit facilities if possible. Partnering with a sourcing agent or consultant familiar with the industry can also provide valuable insights.
3. What are the challenges of manufacturing in China?
Quality control can be a concern, so it’s crucial to implement rigorous inspection processes and establish clear specifications. Communication barriers due to language differences and time zone disparities may also arise but can be managed through effective communication channels.
4. What should I consider when negotiating pricing?
Negotiate based on factors like order volume, material costs, and production complexity. Be aware of additional costs such as shipping, tariffs, and import duties. Building a long-term relationship with suppliers can sometimes lead to more favorable pricing terms.
5. How can I ensure intellectual property protection?
Utilize non-disclosure agreements (NDAs) and ensure contracts clearly outline ownership rights. Consider registering trademarks or patents in China if applicable. Working with reputable suppliers with a proven track record of IP protection can mitigate risks.
6. What are the advantages of outsourcing production to China?
Besides cost savings, outsourcing to China allows access to a wide range of manufacturing capabilities and technologies. This can accelerate product development and enable scalability as business needs grow.
Navigating sourcing and manufacturing in China requires careful planning and due diligence to ensure successful outcomes. Balancing cost considerations with quality assurance measures is key to establishing a reliable supply chain for precision sheet metal components.
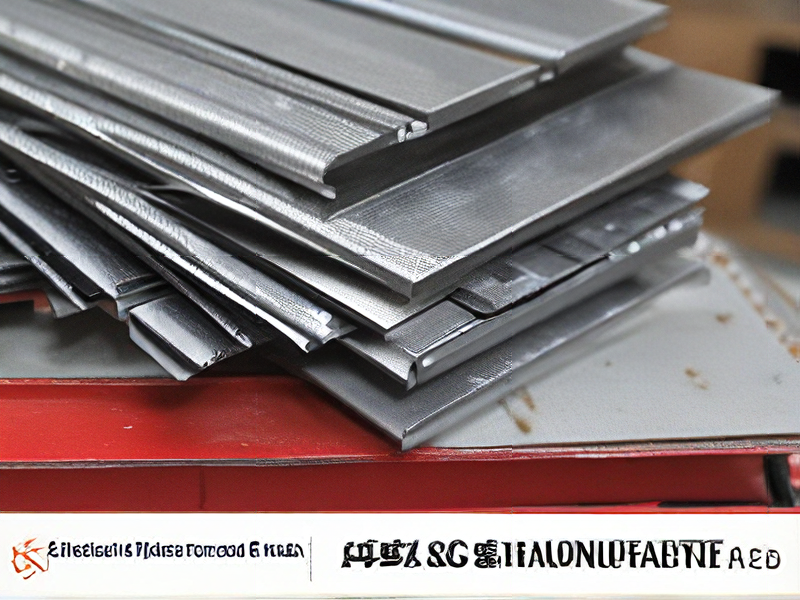