Technology and Applications of riveting metal
Riveting is a metal joining process where a rivet, typically a cylindrical shaft with a formed head at one end, is inserted through aligned holes in two or more metal pieces and deformed to secure them together. This deformation, often achieved by hammering or using specialized tools, creates a mechanical joint that is strong and resistant to vibrations. Riveting is widely used in various applications due to its reliability and suitability for joining metals that are difficult to weld or solder, such as aluminum, steel, and even plastics.
In terms of technology, there are several types of rivets including solid rivets (the traditional type), blind rivets (used when access to the rear of the joint is limited), and tubular rivets (hollow and used in applications requiring a water-tight seal). Riveting tools have evolved to include pneumatic and hydraulic riveters, which improve efficiency and accuracy in high-volume manufacturing.
Applications of riveting are diverse, ranging from aerospace and automotive industries to construction and shipbuilding. Aircraft assembly relies heavily on riveting due to the joint’s strength and ability to maintain structural integrity under stress. In automotive manufacturing, riveting is used in body assembly to join panels securely and ensure vehicle safety. Additionally, riveting is crucial in the construction of bridges, where the joints must withstand dynamic loads and weathering.
Overall, riveting remains a fundamental joining technique in metalworking, offering robust connections suitable for demanding applications where strength, reliability, and ease of maintenance are essential considerations.
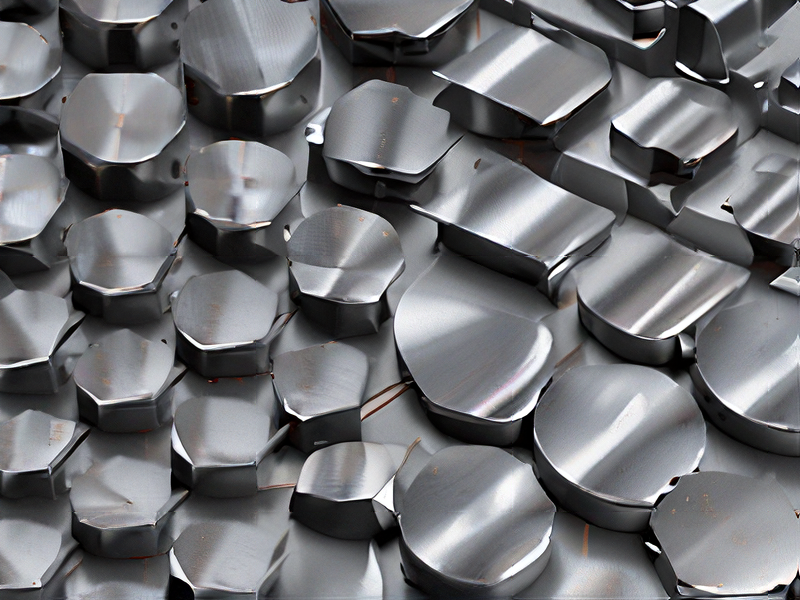
Quality Testing Methods for riveting metal and how to control quality
Quality testing methods for riveting metal are essential to ensure the integrity and performance of riveted joints. Here are the key methods and control measures:
Visual Inspection
Method: Examine rivets for proper installation, checking for defects like cracks, misalignment, or incomplete formation.
Control: Regular training for inspectors and use of visual aids or magnification tools.
Non-Destructive Testing (NDT)
1. Ultrasonic Testing:
– Method: Use high-frequency sound waves to detect internal defects.
– Control: Calibrate equipment regularly and ensure operators are certified.
2. X-ray/ Radiographic Testing:
– Method: Utilize X-rays to visualize the internal structure and detect hidden flaws.
– Control: Employ skilled radiographers and maintain stringent safety protocols.
3. Dye Penetrant Inspection:
– Method: Apply dye to the surface and inspect for cracks revealed by the dye.
– Control: Ensure thorough cleaning of parts before inspection and proper dye application.
Mechanical Testing
1. Shear and Tensile Tests:
– Method: Apply shear or tensile forces to test the strength of riveted joints.
– Control: Standardize test procedures and use calibrated testing machines.
2. Fatigue Testing:
– Method: Subject samples to cyclic loading to assess durability under repeated stress.
– Control: Use representative samples and maintain consistent test conditions.
Quality Control Measures
1. Standardized Procedures:
– Implementation: Develop and adhere to standardized riveting procedures and specifications.
– Monitoring: Regular audits and reviews of procedures.
2. Training and Certification:
– Implementation: Continuous training and certification programs for technicians and inspectors.
– Monitoring: Regular assessments and recertification.
3. Documentation and Traceability:
– Implementation: Maintain detailed records of inspections, tests, and production batches.
– Monitoring: Implement a robust traceability system to track issues back to specific batches.
By combining these methods and control measures, the quality of riveting metal can be effectively ensured and maintained.

Tips for Procurement and Considerations when Purchasing from riveting metal
When procuring riveting metal, careful planning and consideration can help ensure quality, cost-effectiveness, and timely delivery. Here are some essential tips:
1. Material Quality: Assess the material specifications and ensure they meet industry standards. Consider factors like tensile strength, corrosion resistance, and suitability for the intended application. Request material certifications and test reports from suppliers.
2. Supplier Evaluation: Choose suppliers with a proven track record. Evaluate their reputation, reliability, and production capabilities. Check for certifications like ISO 9001, which indicates adherence to quality management systems.
3. Cost Analysis: Compare prices from multiple suppliers but avoid choosing solely on cost. Consider the total cost of ownership, including shipping, handling, and potential delays. Evaluate bulk purchase discounts and long-term supply agreements.
4. Lead Time and Delivery: Confirm the supplier’s lead times and delivery schedules. Ensure they can meet your project timelines. Consider suppliers with robust logistics networks to minimize delays.
5. Customization Needs: If you require custom riveting metal parts, ensure the supplier can meet your specifications. Discuss customization capabilities, tooling costs, and lead times for custom orders.
6. Sustainability and Compliance: Ensure the supplier adheres to environmental regulations and ethical sourcing practices. Verify their compliance with relevant industry standards and regulations.
7. Technical Support: Choose suppliers who offer strong technical support. This can be crucial for addressing issues related to material selection, application, and troubleshooting.
8. Sample Testing: Request samples before making large orders. Conduct tests to verify the material’s quality and performance in your specific application.
9. Contract Terms: Clearly define contract terms, including payment terms, delivery schedules, and penalties for non-compliance. Ensure all agreements are documented to avoid disputes.
10. Risk Management: Identify potential risks, such as supply chain disruptions or quality issues. Develop contingency plans to mitigate these risks, such as maintaining a list of secondary suppliers.
By following these guidelines, you can streamline your procurement process, ensure high-quality riveting metal, and achieve better outcomes for your projects.
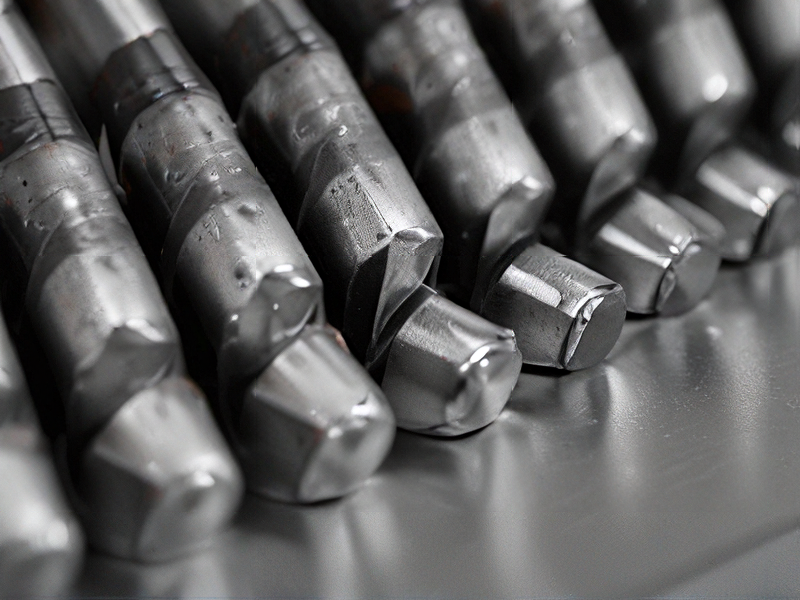
FAQs on Sourcing and Manufacturing from riveting metal in China
FAQs on Sourcing and Manufacturing Riveting Metal in China
1. Why source riveting metal from China?
China offers cost-effective manufacturing, a wide range of suppliers, and advanced production capabilities, making it a preferred choice for many businesses globally.
2. What types of riveting metal can be sourced?
Chinese manufacturers provide various types, including aluminum, steel, stainless steel, copper, and brass rivets, catering to diverse industrial needs.
3. How to find reliable manufacturers?
Use platforms like Alibaba, Global Sources, and Made-in-China. Attend trade shows like the Canton Fair or reach out to industry associations for recommendations.
4. What certifications should manufacturers have?
Look for ISO 9001, CE, and RoHS certifications to ensure quality and compliance with international standards.
5. What are the quality control measures?
Conduct factory audits, request product samples, and hire third-party inspection services to verify product quality before shipment.
6. How long does production and shipping take?
Production typically takes 2-4 weeks, depending on order complexity. Shipping can take 2-6 weeks via sea freight or 5-10 days via air freight.
7. What are the payment terms?
Common terms include T/T (bank transfer), L/C (letter of credit), and sometimes PayPal for smaller orders. A 30% deposit before production and 70% balance before shipment is standard.
8. How to handle language barriers?
Many manufacturers have English-speaking sales representatives. Using clear and simple language or hiring a local translator can also help.
9. What are the common challenges?
Challenges include communication issues, quality control, and navigating import regulations. Building strong relationships with suppliers and understanding local business practices can mitigate these risks.
10. How to ensure compliance with import regulations?
Work with a customs broker to ensure all documentation and product standards meet your country’s import regulations.
By understanding these aspects, businesses can effectively source and manufacture riveting metal from China, ensuring quality and efficiency.
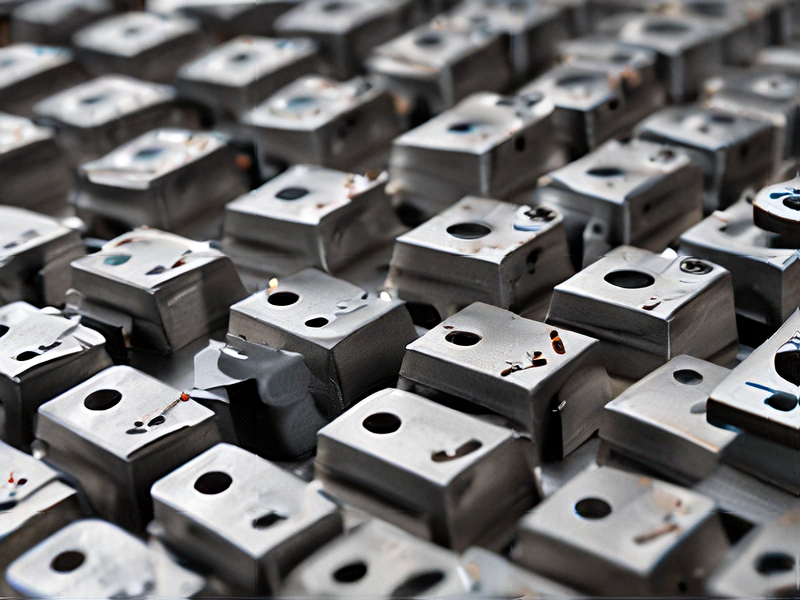