Technology and Applications of riveting metals
Technology and Applications of Riveting Metals
Riveting Technology
Riveting is a permanent mechanical fastening process that joins two or more metal sheets by deforming a rivet. There are two primary types of riveting: hot riveting and cold riveting. In hot riveting, the rivet is heated before insertion, expanding as it cools to form a tight joint. Cold riveting involves driving the rivet into place at room temperature, often with a pneumatic rivet gun.
Types of Rivets
1. Solid Rivets: Used in high-stress applications like aircraft and bridges.
2. Blind Rivets: Ideal for applications where access is only possible from one side, commonly used in construction and automotive industries.
3. Self-Piercing Rivets: Pierce and fasten in one step, often used in automotive manufacturing for joining dissimilar materials.
Applications of Riveting
1. Aerospace: High-strength solid rivets are critical in assembling aircraft structures due to their durability and reliability.
2. Automotive: Riveting is employed in car frames and body panels, providing lightweight and strong joints that can handle dynamic loads.
3. Construction: Rivets are used in steel structures, bridges, and heavy machinery, where their high shear strength and resistance to vibration are essential.
4. Consumer Goods: Riveting is used in the production of appliances, electronics, and furniture for creating sturdy joints without welding or adhesives.
Advantages of Riveting
– Strength and Durability: Riveted joints can withstand high loads and stress.
– Reliability: Provides consistent and repeatable joints, crucial in critical applications like aerospace.
– Versatility: Suitable for joining various materials, including metals and composites.
– No Heat Distortion: Cold riveting avoids the thermal distortion associated with welding.
Riveting continues to be a vital technology in modern manufacturing, offering a robust, reliable, and efficient method for assembling metal components across various industries.
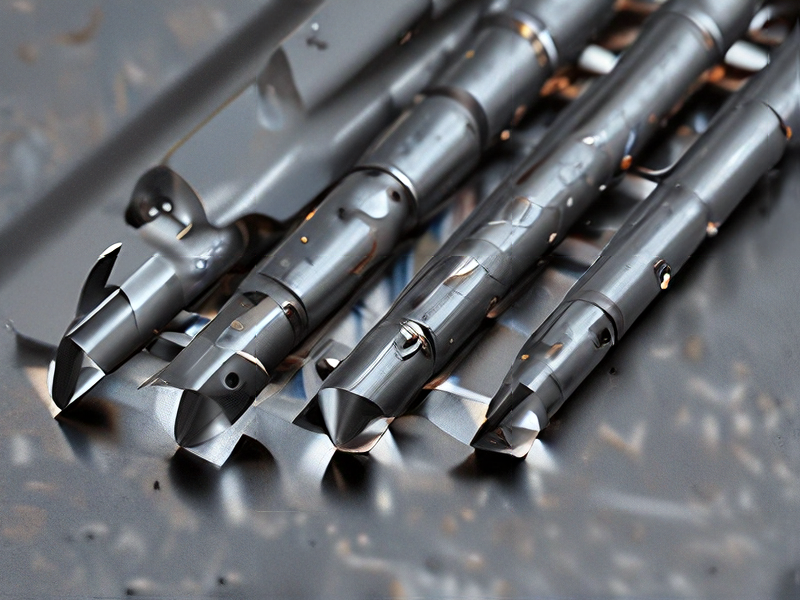
Quality Testing Methods for riveting metals and how to control quality
Quality testing methods for riveting metals are essential to ensure the integrity and strength of riveted joints. Here are key methods and quality control measures:
1. Visual Inspection: The first step involves a thorough visual examination of riveted joints. Look for misalignment, improper spacing, and any signs of wear or corrosion. Ensure that the rivets are properly flush and free from defects.
2. Dimensional Measurement: Use calipers or micrometers to measure rivet dimensions (diameter, length) and their spacing. Ensuring proper dimensions is critical for load-bearing capacity.
3. Nondestructive Testing (NDT):
– Ultrasonic Testing: This technique uses sound waves to detect internal flaws and changes in metal density.
– Magnetic Particle Inspection: Ideal for ferromagnetic materials, this method detects surface and near-surface defects by applying magnetic fields and powder inspection.
4. Tensile Testing: Samples of riveted joints can be subjected to tensile stress to assess their strength. This involves applying a load until failure occurs, providing data on the joint’s load-bearing capacity.
5. Fatigue Testing: This assesses how riveted joints perform under repeated loading scenarios, simulating real-world stress conditions.
Quality Control Measures:
– Standardized Procedures: Implement standardized riveting procedures based on industry standards (e.g., ASTM, ISO).
– Training: Regularly train employees to ensure they are knowledgeable about best practices in riveting and testing.
– Documentation and Traceability: Maintain detailed records of inspections, tests, and any corrective actions taken, ensuring traceability in quality assurance.
By employing these testing methods and control measures, manufacturers can enhance the reliability and durability of riveted metal assemblies.
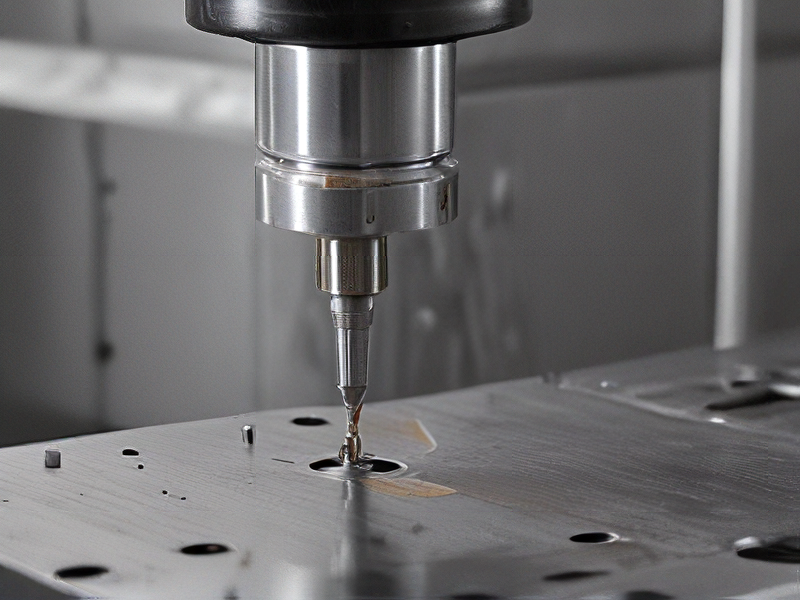
Tips for Procurement and Considerations when Purchasing from riveting metals
When procuring riveting metals, several considerations can ensure optimal purchasing decisions:
1. Material Specifications: Define the exact material requirements such as type (aluminum, steel, etc.), grade (strength), and finish (corrosion resistance).
2. Quantity and Volume: Determine the required quantity based on project needs, including any potential for bulk discounts or long-term supply agreements.
3. Supplier Reliability: Choose suppliers with a proven track record for quality, reliability, and on-time delivery to minimize production delays.
4. Cost Efficiency: Balance quality with cost-effectiveness by comparing prices from multiple suppliers and considering total acquisition costs (including shipping and handling).
5. Technical Support: Evaluate suppliers that offer technical assistance or guidance, especially if specific expertise is required for material selection or application.
6. Certifications and Standards: Ensure materials meet industry standards (e.g., ASTM, ISO) and certifications (e.g., RoHS compliance for environmental standards).
7. Packaging and Handling: Consider how materials are packaged to prevent damage during transit and storage, especially for sensitive or high-value materials.
8. Environmental Impact: Assess suppliers’ environmental policies and practices to align with corporate sustainability goals.
9. Risk Management: Develop contingency plans for supply chain disruptions or quality issues by diversifying suppliers or establishing backup sources.
10. Feedback and Reviews: Utilize feedback from industry peers or online reviews to gauge supplier reputation and performance.
By addressing these considerations, procurement professionals can make informed decisions when purchasing riveting metals, ensuring alignment with project requirements, cost-efficiency, and long-term supplier relationships.
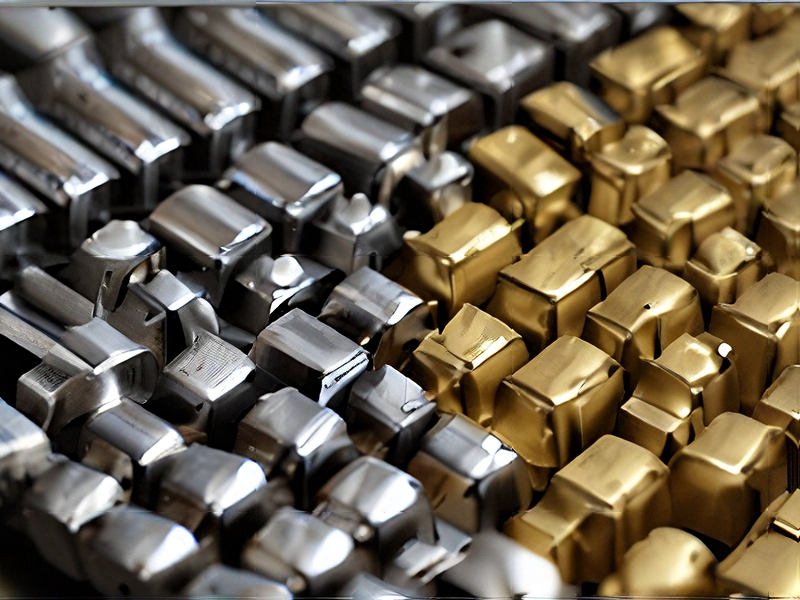
FAQs on Sourcing and Manufacturing from riveting metals in China
When sourcing and manufacturing riveted metals in China, several FAQs typically arise:
1. Why source from China?
China offers competitive pricing due to lower labor and production costs, extensive manufacturing capabilities, and a robust supply chain for raw materials.
2. How to find reliable manufacturers?
Utilize online platforms like Alibaba or attend trade shows such as Canton Fair. Verify certifications, conduct factory audits, and request samples to ensure quality.
3. What are common manufacturing processes used?
For riveting, processes like stamping, casting, and machining are common. Ensure the manufacturer has expertise in the specific methods required.
4. How to manage quality control?
Implement detailed quality agreements, conduct inspections during production, and utilize third-party inspection services to maintain consistent quality.
5. What about intellectual property protection?
Use non-disclosure agreements (NDAs), register trademarks, and consider consulting with legal experts to safeguard designs and technologies.
6. How to handle logistics and shipping?
Choose experienced freight forwarders, negotiate shipping terms (FOB, CIF), and be aware of customs regulations to avoid delays and additional costs.
7. What are the typical lead times?
Lead times can vary widely depending on product complexity and order volume. Discuss timelines upfront and factor in potential delays during peak seasons.
8. How to address language and cultural barriers?
Clear communication is key. Engage with manufacturers who have English-speaking staff or use translators to avoid misunderstandings.
By addressing these FAQs, businesses can navigate sourcing and manufacturing riveted metals in China effectively while mitigating common challenges.
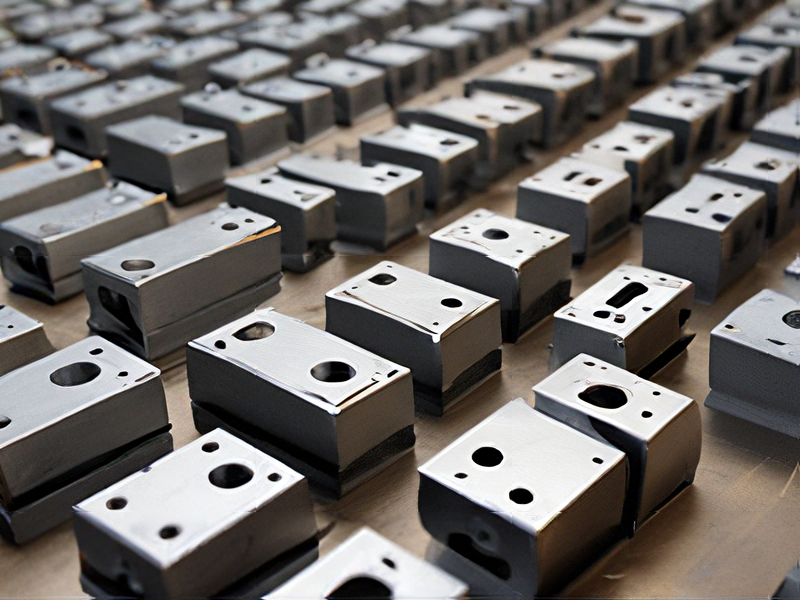